options for vapor barrier over old existing high-humidity slab?

I have an old slab, 4′ below grade, which is high humidity (up to 98%), but never any bulk water issues (have a perimeter foundation drain and sump pit that stays dry). Before we lay down 1+” of EPS foam, radiant tubing, and do a concrete overpour, need to install a vapor barrier. 2-part epoxy sounds like the best option, but requires I bring in a crew for shot blasting or grinding, which I’d like to avoid.
What alternate vapor barrier products could I use?
I’m not sure it is a practical concern, but I am concerned using a poly sheet barrier could up bulk water on the underside, which could lead to water near the sole plate of pre-existing partition walls and longer term issues. Maybe there are some self-adhered vapor barrier products that would manage the wet layer concerns.
Thanks in advance.
GBA Detail Library
A collection of one thousand construction details organized by climate and house part
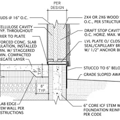
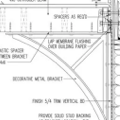
Replies
rossm,
If there are no bulk water issues, the moisture in your slab will be diffusing through the slab into the basement air. Poly will stop that. You can get moisture accumulating both below and on top of the poly due to the difference in temperature of the air and the concrete, but your layer of foam will eliminate that problem.
You may find this article useful: https://www.greenbuildingadvisor.com/article/installing-rigid-foam-concrete-slab
Thanks for the speedy response, Malcolm. Correct - no bulk water issues today. However, I would anticipate the top of the slab (today) is lower humidity than the center, and after the build-up, would expect the top of the slab to be at a higher humidity. See reference pic from Lingomat moisture meter manual, attached (I think this is why the ASTM test says the humidity must be measured 40% of the way through the slab).
To repeat back what I'm hearing, to ensure I understand correctly... with the insulation layer over the poly, you do not foresee any water accumulation between the poly and slab?
rossn1,
Yes - but I missed that you are pouring another slab on top. In that situation the place for the poly is over the foam. Otherwise the bleed water from the pour will accumulate below the foam and can take months to dry. https://www.greenbuildingadvisor.com/article/polyethylene-under-concrete-slabs
From the perspective of moisture accumulation on top of the existing concrete, it makes no difference where the foam or poly is. There won't be any.
Thanks for clarifying I don't need to worry about water forming beneath the poly/concrete. And thanks to you and @maine_tyler for calling out the topic of the vapor barrier location.
Understood the concerns with the moisture leaching into the EPS, and then needing an extended drying period.
A couple (might be bogus) concerns I would have with putting the VB on top of the foam are:
- There are probably going to be thousands of staples going into the foam, to anchor the pex in-place, and with traffic during install, these holes could get enlarged. I don't know concrete, so I don't know if these holes would allow water to go beneath the VP and possibly cause some more challenging drying situations.
- Similarly, if there is ever a flood or broken pipe event, I would think it could be challenging to dry the space between the VB and concrete
- There is a good chance I will have some 'stepping' of different foam heights, as the current slab is relatively flat, but in order to keep a relatively thin assembly, most foam may be 1-1/4", with one room at 1" and bathrooms at 3/4" to accomodate tile build-up. I would think VB over those steps could possibly be problematic, though maybe the solution is as simple as cutting the VB at that point.
If the VB was to go beneath the foam, I do have months that are available for drying. I don't know if the pour being only 1-1/4"-1-1/2" helps, either.
Is my thinking off on this?
rossn1,
In that case I would put the poly down first and tape the foam to limit the amount of bleed water that got through.
I don't know much about over-pouring concrete top coats. Can you really pour a slab only 1 1/2" thick over foam?
Ok, that makes good sense. Likely will have some foam tape around the outer edges as well, to separate concrete from lumber and to also allow for expansion and a caulked joint.
Yeah, from the various radiant guys I've spoken with in-person and contractor consensus over on heatinghelp, 1-1/4" (3/8" or smaller aggregate and 5000 psi) is typical minimum pour for an overpour with at least 25psi foam. Some folks call for for glass fiber additions, to minimize cracking. Local concrete guy confirmed the same with his plant. I was going to go with some 40psi foam, but have some areas not entirely flat and think the higher PSI foam may not conform as well.
" I would anticipate the top of the slab (today) is lower humidity than the center, and after the build-up, would expect the top of the slab to be at a higher humidity."
95% RH seems quite high and it could only ever get to 100%. If you are measuring 95 at the top, i wouldn't be surprised if it's the interior humidity adsorbing onto the concrete that is causing the high RH. Are those readings during humid summer months? What is the temp of the concrete compared to the dewpoint of the air in the basement?
I think the 40% of depth measurment is for slabs that are still curing (which would be dryer on the top drying side).
It sounds like you have exposed plates and studs on your partition walls. I assume rebuilding them to be on top of the new pour is too much work? Because that seems ideal.
My gut says what applies to new slab may also apply to old slab sitting on damp dirt... that is, the top surface releases some of it's humidity, so it is lower humidity on the surface (when open).
My measurements were with a purpose-made meter, bored hole and sleeve in the concrete. I had not tested it in 2 years, and tested again this morning... the preliminary numbers are around 92%, though have seen it at 98-99% on a couple occasions.... I have not tried through the year, but have tried during our wet season. Yes, it is very high, but when I talked to a mfg rep for a moisture products mfg, he cited several other facilities in my area with similar relative humidity slabs... so I guess that is just the case in some places around here.
I dug the sump pit, and the sandy soil is just damp, damp, but no water per-se. Here in Colorado, things are quite arid (this year a bit of an exception), so I am confident it is not an issue of moisture moving from air to concrete. Despite a cool temp on the slab, have never seen any condensation, fwiw.
Originally, the radiant was going to go on the ceiling, due to stair challenges if going on the floor... but later, the remodel exploded in size, and the stairs came into scope for replacement. So, all the downstairs framing that was not original, is already in place and it's not practical at this point to re-frame (there is a secondary wall inside the exterior wall all around the lower level to be able to meet energy code. How to keep that framing sustainable, however, is a concern, and hence the reason for digging deep and getting this right. If I could only go back, I'd probably pull out the slab, dig deeper, insulate, install heated slab... but, no chance at this point!
The usual reason to go with an adhered VB vs poly is to eliminate the air film (and subsequent air 'communication' threat) when doing a floating floor or the like above.
Because you are pouring more concrete, this is not an issue.
Note the poly should go above the foam, in contact with the concrete.
As far as sole plates: will you be sealing the vapor barrier to the edges of these existing plates? Are the plates PT at least? If worried, you could run a bead of sealant along the perimeter of the plates or tape the poly to the floor and not the plates.
I have seen redguard mentioned as an option for adhered VB, but I don't think one layer is as low perm as poly.
Thanks, maine_tyler.
In my build, there are some original walls... likely from the 60', and to be honest, I am not clear if they would have been pressure treated. Partition walls added a few years back definitely have pressure treated sole plates. My thought was to brush on a borate based wood preservative, such as boracare (which claims to migrate throughout the wood), to the bottom 8-12" of the stud walls, though I am still needing to dig into the SDS to understand if Boracare is as friendly as a simple application of borate.
Yes, I was planning on using a high quality sealant along the base of the sole plates. One I've had really good luck with is Titebond weathermaster ultimate MP. I'm not sure if I should just run a bead, or basically liquid flash it with an L-shape to the top of the sole plates. On concern there is if there is ever a water event from a flood or broken pipe... how the sole plates dry out if sealing the sides.
Thanks for the heads-up on the vapor barrier location. I'll have a look at redguard, as well.
Redgard is kind of a vapor barrier, a 30 mil dry layer has a perm rating of 0.36 perm. To get a 30 mil layer you have to apply it at a rate of 30 square feet per gallon, that's really thick.
Thanks. I think I would need something in more of a Class I vapor retarder.