Poly or Intello interior vapour barrier?
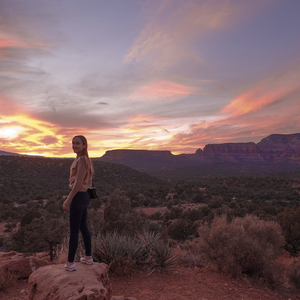
We just started installing 6 mil pol as our interior vapour control layer in a new build project. Originally it was to be Intello as per architect. Builder switched to poly for cost savings. They put Intello in some areas during framing so I thought they had switched back, I was surprised to see poly going up now.
We have black steel siding, with a ventilated rain screen cavity, and 4 inches of EPS exterior insulation. OSB sheathing. 2×6 framing with mineral wool batts. The question is whether 6 mil poly behind the drywall will create issues, since I read about inward solar vapour drive I got concerned that the black steel siding is going to drive vapour inward and the poly will lead to the OSB/framing rotting or getting moldy.
Should we stop what we are doing, rip out the poly and replace with Intello? With 4” of EPS, is it even possible moisture will be getting into the wall assembly?!
Appreciate your advice!
GBA Detail Library
A collection of one thousand construction details organized by climate and house part
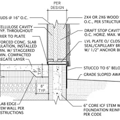
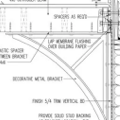
Replies
Izzza,
Inward solar vapour drive only affects reservoir claddings - that is those which absorb moisture, like brick, not metal panels.
Poly works well and is ubiquitous in Ontario. The downside is that in cooling dominated climates it can end up being a wrong-side vap0ur barrier. However (so far) our climate is still heating dominated for most of the year, so it isn't an issue.
Thank you for the quick response Malcolm! I will have to read about solar vapour drive more because I totally misunderstood but it makes sense, I recall seeing brick in visuals but I thought the steel might still create a hot cavity that could drive vapour inward.
My GC did a quick price calc and they came up with something crazy like +$7,800 to switch to Intello. Which is probably why I should have trusted their judgement in the first place. It seems, as with everything else, it always comes down to a value judgement. While Intello is technically a superior material and it would give more peace of mind, the economics don’t make sense.
I suppose the smart membrane makes more sense in applications where there is a greater risk of condensation in the wall. Perhaps I’ve gotten a bad impression of poly in examples very different than our assembly. I see how it would not be good without the exterior insulation even here in Ontario.
Izzza,
The vapour-drive in your climate is to the exterior, and with your stack up you have excellent drying potential. Poly can cause a lot of problems, but I don't think it's an issue in your situation.
Stepping back a bit a bit. Right now it's one thing after another, but relatively quickly it ends. You then go though a short period when all you see are small mistakes - and then you get to enjoy your accomplishment in having created a place where all the significant events in your life will occur. That's something to look forward to.
He has 4" EPS on the exterior. Is this not the prime example of when you should be using a smart vapor retarder on the inside? The assembly can't dry to the exterior (due to the EPS) so needs to dry to the interior.
Putting poly on the interior means any moisture that gets into the assembly can't escape.
Andy,
First off: I somehow missed the exterior foam in her description. That's bad, I need to be more careful. My advice that the wall has good drying potential to the outside was flat out wrong.
However I'm not sure it's really a problem. These walls with exterior insulation and interior poly are very common in Ontario and function well. They don't experience the problems we thought they would due to having two impermeable sides. In colder climates the vapour-drive is to the outside. Interior vapour-permeable membranes don't help much.
https://www.greenbuildingadvisor.com/article/rethinking-the-rules-on-minimum-foam-thickness
I'll be interested to hear what others think.
Yes, this is what I thought. I’m still new to all of this so just curious to learn more.
I think it’s too late now, they continued with the rockwool and poly.
Nobody seemed concerned about moisture getting past the EPS. I would generally assume a tiny bit will get in… I don’t know what happens but I know that OSB rots :)
Interestingly, my builder has done passive houses where they did not use any vapour control layer because of the amount of exterior insulation. Apparently it was challenging to deal with the building inspector but it seems to have turned out fine. My concern was mainly because this is only 4” so far from passive standard, but they all seemed fairly confident this would be fine 🤷♀️
Also, thanks for the encouragement Malcolm! Definitely cannot wait to be done, but so many decisions ahead still. I will be hemming and hawing about finishes until the last possible second 😂 I fear when this is all over I will miss it, I think this would be a total blast if I was working on someone else’s home rather than my own.
Izzza,
" I fear when this is all over I will miss it, I think this would be a total blast if I was working on someone else’s home rather than my own."
Which was why for much of my career I opted to spec build - the best of both worlds. You decide what to build and how, but don't have to live with the results.
Malcolm, I am certainly already tempted to build something again! Spec building seems risky but a fun challenge. I wonder if there is much of a market for ‘pretty good houses’? Ultimately we felt we had no choice but to build because everything for sale is objectively pretty bad. It seems extremely rare to see anything on the market remotely well built by current building science standards. So much work to make this happen as I’ve learned, these houses are rare. I’m sure it appeals to many people, plus the rarity factor, but it’s hard to know if one could buy land with the intention of earning some profit while also building a PGH… are you saying it can be done?
Izzza,
The are people associated with GBA - like Mike Maines, Ben Bogie, the rest of the authors of the Pretty Good House, and regulars on the BS & Beer show, who have successful careers designing and building high performance houses. They do that by building a practice that attracts like-minded clients. I don't know any who have done it by spec building, although maybe it's possible.
I wouldn't consider any of the projects I've done as high performance. If they had any particular merit, they were fairly well built, regionally appropriate houses for their sites.