Polyiso install

Starting basement insulation, been reading here for nearly 3 months and finally got around to it.
I’m using 2 inches of polyiso on the walls. No signs of water over the year we have lived here, humidity stays around 50 without assistance of a dehumidifier.
When I install the polyiso can I set it against the concrete at the floor or do I need install a treated 2×4 first and then set the polyiso sheet on that to avoid direct contact with the concrete. I read the polyiso can absorb water so I got concerned about the none covered edges.
If I started with a 1 inch eps or polyiso on the floors with 2 inches of plywood this would resolve this concern on its own but I’m attempting to avoid adding anything to the floor due to not having alot of room from floor to ceiling as it is. If this is something I need to do would 1 inch plywood be acceptable.
While I am on a budget I would rather take twice as long saving money and do it right once rather than do it twice later.
Thanks in advance for any advice and input.
Zach
GBA Detail Library
A collection of one thousand construction details organized by climate and house part
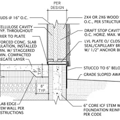
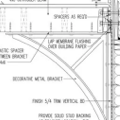
Replies
Here is a good read from Building Science Corp. about installing polyiso on basement walls. In short, you need to cover all concrete with taped and sealed sheets, providing a continuous air barrier and capillary break, to avoid winter and summer condensation.
https://buildingscience.com/documents/information-sheets/basement-insulation
Usually all you need to do is leave a 1/4”to 1/2” or so gap between the bottom of the insulation and the floor. You don’t need to do anything fancy. If you’re worried about the gaps impact on the insulating value for the wall, you can always fill it with canned foam.
Bill
It seems like you have a plan in mind, but if you haven't read it already, you may find this article helpful:
https://www.greenbuildingadvisor.com/article/how-to-insulate-a-basement-wall
I'm struggling to learn all this, thanks for the article, didnt know about fighting rising damp issues.
You said cover all concrete. So not applying any insulation to the floor would be a bad idea? My basement is 7 foot 2 at the moment with bare concrete. Plus I would need to reframe my doors as they wouldnt open with a layer of foam and plywood. I have tile on concrete right now in half the basement that is performing good. Is that because it can breat thru the grout into the space? If that would work that would be easiest option for my space. If not I'll figure out how to add insulation to the floor and make things work.
Another thing I wanted to confirm is that a non vapor permeable insulation is ok. I believe my polyiso wont allow any vapor thru. Lebowskis revised notes say its ok now tho right? Is the basic goal to prevent the warm air from reaching the now cool surface below the insulation by sealing with tape? The water wont condense on the bare concrete because it's heated with the room, but once its covered its temperature drops low enough to allow water to condense on it. Is my understanding accurate? So I'm controlling moist air from the inside plus flow thru the wall. My job outside the wall is water management. With proper exterior water management will enough moisture flow thru the concrete to cause issues between the concrete and the insulation? Water shouldnt condense between concrete and insulation because the insulation should be warmer or close to the same tempurature as the concrete and dirt outside.
My plan as of right now is the 2 inch polyiso taped with ac duct tape. Probably a 1/4 inch gap at the bottom of the sheet with tape applied over the 1/4. I'll follow the rim joist and rising damp break as illustrated in the link posted in the first post. I'll do some sort of framing with 1/2 drywall and latex paint. I think thats the summary of my insulation plan. With a breathable flooring with no insulation below the flooring unless advised other wise.
Hopefully this isnt confusing or mind numbing. I'm figuring it out but its difficult to speak clearly about things I don't clearly understand. Thanks for the advice.
Don’t use regular duct tape. The metallic stuff would be better, maybe that is what you meant by “AC duct tape”?
You get the most benefit from insulating the walls and rim joist area. You can insulate the floor too, but that adds a lot of work for less benefit (but there is still a benefit).
You need to be sure the wall is sealed and does not weep water. If there is any water coming through your wall, any insulation is going to be a problem. Fix any water issues first. You don’t need vapor permeable insulation in most cases on a basement wall. Make sure you have a capillary break under the rim joist to prevent “rising damp” from wetting the wood framing members.
Polyiso commonly has a metal foil facing which is a vapor barrier. You can get polyiso with felt facing which is vapor permeable. I would go with the regular foil-faced stuff.
Bill
Started the project and I keep reading as I go. I started reading and reviewing a pyschrometric chart which got me to wondering. I believe the concrete walls on the earthed in portions of my basement will stay above my dew points on the chart. My concern is the walk out side falling below the 45 ish degree dew point for 70 degree room at 45 % humidity. Being that the wall is concrete exposed to fresh air will the wall be able to vent thru the concrete in a way to prevent this from being a concern? My outdoor humidity for this week for example on a sunny day is around 50% at noon and around 85% at night. I know some moisture build up is acceptable as it will just dry out during the day time temperatures but I wanted to run these ideas and concerns by some people who know much more about this than me. I didnt mention my basement had a walk out portion in my original post either. Plan currently is still to use 2 inch polyiso, about 3 sheets 1 inch thick up are so far on the walk out side.
Thanks
Zach
I'm going to use a laser style thermometer today or tomorrow to acquire surface temp if the concrete. In the mean time I inserted my grill thermometer behind a portion of a mostly tape sheet. The slim air gap had a temp of 50.5 degrees f. I'll try and get an idea of surface temp tomorrow. Problem is it was only 45 last night at the lowest.
Enviroment is currently at time of test: 61 degrees in basement, furnace left off over night, 45 degree low outside.
Further reading said most condensation problems are the result of air leakage from inside rather than diffusion from outside. Would that mean proper tape and sealing of the insulation would prevent this issue?
Concrete can take the moisture- don't worry about it taking on adsorbed moisture from the room air.
As far as the rising damp issue, if you have a foot so of exposed foundation on the exterior it will almost always be sufficient for keeping a wood foundation sill from becoming too damp.
Don't put polyiso on the floor. If it ever takes on moisture it'll take forever to leave. As little as 3/4" EPS is sufficient to prevent a wood subfloor from taking on moisture from room air in most US locations. If you don't have or don't know if there's a sub-slab vapor barrier, a sheet of 6 mil polyethylene between the EPS and subfloor would protect it from ground moisture.
What is your location? At just 2" the wall polyiso won't meet code minimums in DOE climate zones 5 or higher.
An relative humidity of 50% is a meaningless number without the room temperature.
Location is little rock Arkansas. Zone 3 I believe. Basment climate is currently under heated as we havent finished insulating and dont use the space. We do have a dehumidifer running. It stays around 55 or 60 degrees at 35 to 40 percent humidity. When we occupy it it goes up to 70 degrees same humidity. That would make my wall surface dew point around 43 I believe. The insulation says at 2 inches I should have about r 13.
So basically condensation is only an issue under two conditions.
A. You use a material it will damage. Which my vapor tape polyiso is foil lined on one side and has some sort of white lining on the other side. Both it and the concrete should be able to handle the moisture as it accumulates and evaporates with out taking damage. The concrete was painted on the inside and outside with who knows what.
B. It condenses enough volume to cause pooling of water. We have never had any water issues so leaks from outside I'm not worried about. My main concern is can enough volume condense between the polyiso and the concrete to create pooling and draining of water or will it simply evaporate when the daytime sun re warms the wall?
I guess my main question boiled down is with a dew point of 43 can enough moisture condense between the concrete and polyiso to create pooling water or cause damage. Concrete is painted on both sides with something. This wall is open to the air btw.
Sorry and thanks in advance, as I learn more I'm trying to be cautious and detailed with my build.
In zone 3 a continuous R5 meets IRC code min for basements and crawlspace walls, so 2" of polyiso is substantially better than code, which is fine.
Your condensation concerns are unfounded.
Dew point is a measure of the absolute humidity in the air. Air that is 40% RH @ 60F has a dew point of 36F, the temperature at which moisture will condense. So only objects that are 36F or cooler would have condensation. Raise that same air to 70F and the RH would be 28% RH, but you're suggesting that it's still 35-40% RH @ 70F. At 70F 40% RH air has a dew point of about 45F- only objects 45F or cooler would have condensation/adsorption of moisture.
When the concrete is colder than 43F, air with a dew point of 43F that contacts the concrete will leave some moisture there, but the concrete will absorb it, and tolerates it will. If the temperature of the ground or air on the other side of the concrete is colder than 43F, the moisture will keep on going outward. But with foil faced polyiso you have a very powerful vapor barrier in place- indoor air with a dew point of 43F or higher still won't be adding measureable amounts of moisture to the concrete, even when it's colder than 43F.
As it happens, 43F is the mean outdoor temperature in Little Rock in January- the rest of the year the averages are warmer than that, as is the near-grade soil temperatures.
https://weatherspark.com/m/10887/1/Average-Weather-in-January-in-Little-Rock-Arkansas-United-States#Sections-Temperature
So even if the 43F dew point air is leaking around the polyiso, it won't be adding moisture to the concrete- instead the concrete will be adding ground moisture to the leak-air that is entering the conditioned space.
The deep subsoil temperature in Little Rock is about 65F- even if you allowed the indoor air to reach 80%RH @ 70F (dew point = 64F) the slab wouldn't be taking moisture from the room air, but if there isn't a ground vapor barrier under the slab ground water vapor diffusion could collect on the underside of vapor impermeable objects left on the floor. If you're adding a sub-floor, a vapor barrier between the slab & subfloor is a good idea.
Give a little thought to mold. If it grows between foam and concrete, it could create odor issues. Much more so than mold residing in soil - a) soil doesn't smell bad and b) air flow is much more likely from the interior side.
https://www.greenbuildingadvisor.com/question/why-is-mold-mildew-growing-behind-my-rigid-foam
So the last concern is moisture getting between the panel and raising the humidity enough to produce mold. Damage to material and pooling are ruled out.
Basically it either needs to vent to the outside or inside to control humiditiy between the wall and panels or both sides need to be vapor sealed.
The earthed in side and the exposed to air sides are a always humid enviroment correct. So they will always introduce moisture thru the concrete and should be sealed with a vapor stopping paint?
As far as the interior side I would think if it can leak in it can leak back out the way it came correct. Especially since a low humidity enviroment is being maintained inside.
Should I paint the walls with a vapor stopping paint, if so, any recommendations?
Do you feel the design would produce mold growth with or without the paint? Or is the ammount of moisture flow thrus we are talking about so miniscule that mold growth isn't a concern in the first place?
>"The earthed in side and the exposed to air sides are a always humid enviroment correct. So they will always introduce moisture thru the concrete and should be sealed with a vapor stopping paint?"
You're making this too complicated.
With an indoor dew point in the 40s F the moisture drives will always be from the exterior toward the interior, averaged over any given month.
The plane where the concrete meets the foil facer never needs to dry. Both the concrete and the facer can take it. The only issue of concern is whether it will increase the moisture content of the above-grade concrete enough to compromise the foundation sill. With a foot or more of exposure above grade for drying it usually won't be a problem, even if there is no capillary break between the concrete & foundation sill.
If mold grows on the concrete, on the other side of the foam, who cares? It's outside! There are all sorts of things growing in the soil on the other side of the concrete wall, but it's sealed off from the conditioned space. Once the foam goes up everything on the exterior side of the foam (including the concrete foundation) is sealed off from your interior, so forget about it- nothing bad happens if some mold grows on the concrete.
Below grade the foundation still needs to be nominally waterproofed (against liquid water, not necessarily watervapor), preferably on the exterior side, but the interior side works too.
For mold odor, Lstiburek recommends a fluid applied vapor barrier for a slab floor (slab floors without poly underneath and concrete basement walls are very similar).
https://buildingscience.com/documents/insights/bsi082-walking-the-plank
On the other hand, maybe mold won't grow or maybe your foam will be so well air sealed that no noticeable odor escapes.
Deleted
Didn't see Dana's post or something got mixed up. Yea something martin said in another post mentioned the same idea. Honestly I dont like the idea of mold potential within the building envelope but if it's sealed the volume of it probably will be miniscule. I'm sure it's happening in other areas of my house with out me noticing anyways.
I'm kind of at a check mate on doing it any other way also as the only options I see are strip the old paint and use a quality dry lock (not sure I wanna mess with that) or excavate and insulate from the exterior which isnt cost effective.
Using 2 coats of an oil based paint or maybe mold maybe an option that could further improve wothout an excessive cost. Just something below 1 perm. I recognize its probably unnecessary but I would rather overbuild rather than redo it later. If I have to accept mold potential I will but if there is a design to prevent it i like the idea. Any thoughts on that idea? Basically what John suggested from joes article.
Even without oil paint or mold it looks like i have a low risk, economical design for my structure. Thanks for walking me thru some of the principles of water movement in structures.
Lstiburek writes "Epoxies work well". Might work without stripping old paint.
The easy option for dryer walls (lower mold risk) is to use EPS or unfaced polyiso.
The vapor permeance of the paint is irrelevant, given the extremely low vapor permeance of the foil facer makes it moot. If the wall doesn't have a history of leaking bulk liquid water, just leave it.