Questions about the building assembly details and insulation strategy for a Colorado house

I live and build in Durango, CO (Zone 5a), and am currently building a custom home for some folks. My insulation contractor is proposing a few things that make me go “hmm.”
He wants to use a flash approach to the walls and spray a thin coat (about 1″) of open-cell foam against the sheathing to seal the cavities and then fill the rest with loose fill fiberglass netted. In the room above the garage we have a cathedral ceiling which he wants to spray 4″ of closed cell foam and fill the rest with fiberglass batts.
The house has a crawl space with 2″ rigid foam applied to the exterior and will be conditioned with supply air from duct and a 120 cfm exhaust fan to expel stagnant air, Stego wrap sealed to walls etc.
The walls are framed with 2×6, 16″ o.c. Sheathing is ZIP system with taped seams as the WRB, Delta Dry rainscreen applied over ZIP and a mix of stucco with 1″ foam (EIFS system) and real thin stone veneer.
The roof system is a mix of 12″ raised heel trusses over the main house, and 11 7/8″ TJI with about 9 1/2″ heels on the cathedral roof. All of the roof has Ice and Water type membrane at eaves and valleys with Delta Vent S above that. Exposed 3×8 rafter tails with soffit installed on top (no dropped soffit),
We will be venting the roof system at the top of the raised heel where the top of wall and soffit meet and running baffles continuous in the cathedral system. The main house will be loose fill fiberglass at ceiling level.
We do have HVAC ducting which will be sealed and wrapped in R-8 and mounded over with loose fill to be continuous R-60.
Since I haven’t asked a question yet here goes. First is, what are your thoughts on the insulation contractor’s proposed system in walls and cathedral ceiling? Second is, what are your overall thoughts on the building assembly for next time? Third is, is it necessary to insulate the floor joists with fiberglass batts?
GBA Detail Library
A collection of one thousand construction details organized by climate and house part
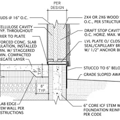
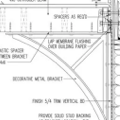
Replies
Greg,
Answer to question 1: The insulation contractor is apparently proposing a flash-and-fiberglass system for your walls. However, only closed-cell foam can be used for flash-and-fiberglass. Either you misunderstood when you reported that he plans to use open-cell foam, or the contractor is making a big mistake. If the contractor is planning to use the Owens Corning Energy Complete system, that's okay -- Energy Complete uses a latex product for air sealing, so the system is different from flash-and-fiberglass.
The proposed 120-cfm exhaust fan for the crawl space is nuts -- a real energy waster. Make it a sealed crawl space, and the homeowners will save a tremendous amount of energy.
It's not clear how the contractor intends to insulate the cathedral ceiling -- I hope there is enough room for adequate R-value there.
Answer to question 2: This is a vague question. Can you be more specific? Here's a quick answer: the house could be insulated better (higher R-values). And I'm not a fan of stucco or stone veneer -- although the Delta Dry will go a long way towards preventing moisture problems behind these problematic siding choices.
Answer to question 3: No, it isn't necessary to insulate floor joists over a crawl space. It's better to insulate the crawl space walls and seal up the crawl space. If you want to improve the thermal performance of the floor and crawl space, install thicker wall insulation on the crawl space walls, or consider insulating the crawl space floor with XPS under a thin rat slab.
My understanding for the cathedral ceiling is he plans to spray 4" of closed cell against our baffles achieving R28 and taking up 5 1/2" including baffle space the rest he wants to put a 6" batt R19 getting only R47 and taking up a total of 11 1/2". Should he just spray another inch and get us to R51.5? Outsulation isn't an option at this point although that would be preferable. The contractor was proposing open cell so he would be making a big mistake which is why it made me question his approach. Unfortunately in my area there are a very limited amount of insulators let alone knowledgable insulators. I would like to use the Ownes Corning system but nobody does it around here. The crawl space fan is a Panasonic WhisperCeiling Energy Star rated fan. The vague question was trying to get thoughts on the current assembly and suggestions to improve the assembly, or problems with the current plan. Thanks
Greg,
Typical R-value for closed-cell spray urethane is 6 per inch. With the thermal bridging through the TJIs, you will have a cathedral ceiling assembly at about R-40 with 4" foam and R-19 batts. If your contractor is claiming R-47, then he's selling you a line.
And, if you're exhausting 120 cfm continuous from a conditioned crawlspace, then you're throwing away more than 200 therms of fuel per year.
You are in an area with high radon (not even counting the local uranium mine groundwater contamination). I would not use a closed crawlspace in your area unless you have tested the home and measured very low radon levels or else have an active radon mitigation system and have tested that it is effective. The exhaust in the crawlspace seems like overkill at 120 CFM but I would first focus on making sure you don';t have a radon problem. Mitigation would most likely involve subslab depressurization and would eliminate the need for the exhaust.
Walls - if you are using 2x6 - I would go 24" OC. As Martin said, flash and batt will not work with 1" of open cell. First of all, impossible to only install 1" of open cell - it expans too quickly and open cell is not considered an air barrier until it is 2" thick. I would just stick with a blown in cellulose or fiberglass product.
Crawl - if you are conditioning your crawl with a supply duct - no need to install an exhaust fan. Do one or the other - a closed crawl can be done either with a supply only or an exhaust only (1 CFM for every 50 SF of crawl space for exhaust only).
Robert-The insulation contractor didn't actually specify what it would be but he knows we are trying to reach at least a R49 so I believe yes (not surprisingly) he is selling me a line. Which is why I was second guessing his approach. The house is going to be an Energy Star and NAHB Gold level and will be third party tested so it is very important to me that what we state is in fact what is installed, not only because of these certifications but because we try very hard to come up with the best system within a budget. That said..what would you recommend? Vent Space, 4" spray foam, 6" blown insulation, 2" rigid foam on underside of TJI taped and sealed then drywall?
The exhaust fan will be downsized to a 80 cfm although the Panasonic FV10NLFI which we were going to use consumes 36 watts of power. We used the guidelines from Lstiburek's building science.com report and are going to supply 50 cfm of supply air and 80 cfm of exhaust per the ASHRAE 62.2 whole house flow rates.
Michael- We did have the site tested and it tested fairly high so we have already installed a radon mitigation system per the EPA Building Radon Out book. It will have a in line fan installed in the attic and the crawl space will be covered with Stego vapor barrier and use mastic and be mechanically fastened to the walls and footers.
Thank you to all for the input and advice. This website and forum has been a great resource and learning tool. Thanks again
Greg,
You could hit your R-49 target with vent, 3" of closed-cell spray foam, 7" dense-pack cellulose or JM Spider, and 1" foil-faced polyiso, but I wouldn't recommend sandwiching any fibrous insulation between two impermeable layers.
A better option would be vent, 10" dense-pack cellulose, 2" foil-faced polyiso, strapping and DW.
Greg,
You said you "tested the site" for radon. Could you explain the test you used? As far as I know there isn't a cost effective way of testing a building site for potential radon exposure. You can test the soil but the results won't indicate whether the home itself will have radon problems.
And about your proposed wall and roof assemblies--
The flash and batt system in your wall insulates only the cavities. You should think about thicker exterior insulated sheathings, or better yet, double walls (my preference), or a Larson Truss. Closed cell spray foam is expensive. Plus, in a "green" home you really should avoid petrochemical foams in above grade applications anyways.
Think about using a scissor truss (less of a thermal bridge) in your vaulted ceilings with raised heels to allow for proper insulation thickness above the top plate.
I should also mention EVERY foam contractor will try to sell you on the "superior" insulating qualities of spray foam. You should know many closed cell spray foams use ozone-depleting blowing agents, and open cell spray foam has basically the same R-value of blown fiberglass and cellulose. Sure spray foams have air-sealing qualities, but build an air tight wall and you can use less expensive and less environmentally destructive cellulose insulation.
Your insulation contractor will most likely try to convince you that cellulose will settle. Tell your contractor to follow the manufacturer's specifications and blow the cellulose in at the right density, or find another contractor.
Robert-How skeptical are you about the first system, I also don't like trapping a fibrous insulation but this seems to be a decent option. I like the second option also but first need to find a cellulose installer. The current contractor did the normal "ohh yeah we don't do cellulose we use to but..." and trail off. They are the largest insulation and drywall contractor in our area and am guessing they use to install it but probably were involved in a law suit and are scared to use it now. I also don't want to be the new guinea pig while they get the densities and moisture level down. I will keep looking.
Brett- Your right the "site" was not tested rather the soils were tested by a environmental testing firm. During excavation we had them perform the test which involved setting a raised screen on top of the soil placing a canister on top of the screen, covering and sealing this with a series of tarps and plastic, leaving it undisturbed for over 24 hours, sending the canister to Colorado Springs for analysis and receiving the results. Like you said there is not a real accurate way of seeing if a home is going to have radon problems, you can test the soils at the site but until you actually place a house over this soil.. We would have put the radon mitigation system in without the test but the client is from out of the state and was skeptical about the whole thing, so we had the soils tested. Agreed about thicker exterior insulation but this house we are tapped out on the budget. Also agree on the "ungreenness" of spray foam and will probably steer away from the flash and batt and try to just use a blown in product (hopefully cellulose but again have to find an installer first). The house is well sealed between the Zip system, caulking the bottom plates etc etc. We will still use the spray foam in certain applications but sparingly.
Greg,
As an instructor of Hygro-Thermal Engineering (from a non-engineer's perspective), I'm skeptical of any building material or assembly or system that does not breathe (is not vapor-open). Not only do I believe that, unless perfection is guaranteed forever, the potential for problems is too great, I also believe that hermetically-sealed boxes are no place for living creatures (at least on Earth).
The more petrochemical products used in a home, the less healthy the space - both for the occupants and for the environment and the rest of the biosphere. The current trends in "green" construction are going in the wrong direction and I predict that we will someday soon realize that it is as much a mistake as the intensive use of petrochemical fertilizers, pesticides and herbicides. Not only are such materials rapidly being depleted and just as rapidly altering our global environment, in every case there have been dramatic unintended consequences.
It's a fool's errand to continue to do - in new and "improved" ways - what has always created problems before. We are far too clever for our own good, and we're taking much of the web of life down with us.
I build with real wood and cellulose insulation and gypsum. Straw bale with earthen plaster is even better. These are the materials that we evolved with and to which we are adapted. Our bodies cannot cope with plastics and remain healthy.