Radiant heating in a cement slab
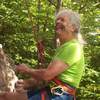
I am ready to install pex for radiant heating prior to pouring cement. I assume that it would be best if I installed the wire grillwork up three inches from the styrofoam insulation so that the pex ends up in the middle of the six inch thick slab. I bought plastic chairs to elevate the rebar in the grade beam around the perimeter but I have yet to figure out a method for keeping the grillwork with the pex up above the bottom of the slab. The grill has six inch squares and my feet are 12 inches so walking around on tippy toes in rubber boots in six inch deep wet concrete doesn’t seem possible without risking a face plant in the concrete or toppling the pastic rebar chairs. Any suggestions?
GBA Detail Library
A collection of one thousand construction details organized by climate and house part
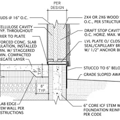
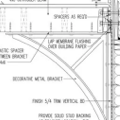
Replies
My first comment is somewhat pedantic: "cement" is the glue that binds aggregate together to form concrete. You will be placing concrete floors, not cement floors.
Practically speaking, I don't do radiant floors, but if I did, I would use a rebar grid on 12" (or larger) centers, not welded wire fabric.
Along those lines, 6" thick seems like a lot unless it's going to be seeing really high loads. Generally in residential you do a 4" slab with no reinforcement.
The slab is a thickened edge slab; no stem walls no footing other than the 12 in thick grade beam integral to the slab. Also there are two posts holding up the 32ft of beam supporting the second floor and with six inches of concrete (yes Michael it was a tad pedantic) I will skip footings for those two posts. I'll add extra renforcing though. Because I'm in a hurry to get the roof on before the snow I bought one plastic chair per square foot which I will install just prior to pouring the concrete and hope they don't sink into the styrofoam. Maybe I should not fill the forms and reduce the thickness to 5 inches. 37 tons of concrete will be difficult to heat or cool in a hurry.
My original enthusiasm for heated floors was because they don't take up floor space and they don't have noisy fans and they don't limit options for the placement of furniture and the distribution of heat is done by 5/8 inch flexible pipes. Why don't you do radiant floors Michael?
Typically piping is tied to the top layer of slab reinforcing before the concrete is placed, although there are other approaches as well.
With a full 6" slab you've got plenty of depth to work with. "Theoretically" you can have as little as 3/4" concrete cover above your hydronic piping. But from what I've read in various places, including a Q&A thread here on GBA (link below) you're better off with 1" to 2". Two inches provides for a little more even heating across the surface while with 1" you're liable to feel some slight variation in the surface temperature.
So, here's your 6" from top down -
2" top cover
1" piping (systems vary from 3/4" to 1 1/4". I'm guesstimating yours.)
3/4" welded wire mesh fabric, or #3 bars each way
2 1/4" bottom cover
This is good and keeps your reinforcing in the middle third of the slab, where you want it. A little higher is okay as well.
As far as installation, could you perhaps lay 2x12 planks down across the reinforcing and several reinforcing chairs, then work off that somewhat like a scaffold? The piping is tied to the reinforcing BEFORE the concrete is placed. So you wouldn't be working around wet concrete.
https://www.greenbuildingadvisor.com/question/radiant-tube-depth-in-slab-on-grade
A couple of things about floor heat, and in particular concrete floors with heat.
First, as you noted, a heating element with a lot of heat capacity is unresponsive. This means it tends to overshoot the thermostat. The trend now is to use low heat capacity systems like WarmBoard which respond a lot quicker.
In general, in houses that are constructed to modern standards of insulation and air-tightness the heating load per square foot is so low that the floors never need to be that warm, so you don't get that cozy warm floor feeling. The rule of thumb is that a floor puts out 2 BTU/SF for every degree of difference between the floor surface and the air. A modern house typically has a heating load in the 10 BTU/SF ballpark, which means you want floor temperature 5F above air temperature. So if your thermostat is at 72F the floors would be at 77F. That's barely perceptible -- and that's the maximum heating load, 99% of the time the floors are going to be cooler than that.
Notwithstanding the previous paragraph, toasty warm floor are great for short periods with bare feet, but if you have to stand on them in shoes for long periods they get uncomfortable.
Finally, concrete just makes for a lousy residential floor. It's hard and unforgiving. It's slippery. It's loud unless you cover it with rugs.
My recommendation would be to run floor heat only in the bathrooms, then you can crank the temperature and have some of the heat spill over to the rest of the house.
Do you need cooling in your climate? If so, size a heat pump to your cooling load and then add bathroom floor heat to make up the rest of the heat.
DC covered the thermally-related reasons I don't use radiant floors. I do use electric radiant heat in bathroom and mudroom floors where they are close to the surface and only operate for short periods of time.
I rarely fight about it anymore but I disagree with the idea that concrete floors are inherently hard to stand on because of their "hardness." The difference between a wood floor compressing 0.01" when you walk on it vs. a concrete floor that compresses 0.0001" is not a difference our bodies can feel. Unheated concrete floors do draw heat from our bodies more quickly than wood floors, which in my opinion and research is the reason why concrete floors may not feel comfortable to stand on for long periods.
I have read a number of posts on this website about radiant floors, and I have had a number of my questions answered on the topic. I must admit, yours is the first mention I have come across about electric radiant floors in the mudroom.
Our builder has wisely suggested switching from hardwood to tile in the mudroom of our upcoming VT build. As such, it occurs to ask what advantages do you see in adding electric radiant to this space?
Thanks!
Ben
Reply to boxfactory, #28: mudrooms in cold climates tend to be dirty, wet spaces. Dirt + water = mud. Despite the name, nobody wants muddy floors. Electric in-floor heat dries the water quickly which helps keep the floors clean. It's not the most environmentally friendly approach and I don't use it in that location often, but it's an affordable luxury for people who use their mudrooms hard but want clean interiors.
Mudrooms are also rooms where people tend to take their shoes off and might have cold feet from being outside. A warm floor is nicer than a cold floor in a room like that.
I have to ask a few questions.
Was the selection of the steel reinforcing selected without consulting an engineer?
Was the tubing length and layout decided without the use of mathematic?
If you chouse to burry thousands of dollars under this slab how sure are you that you will have the funds to complete the build?
You do understand radiant heat is likely to more than double your HVAC budget and every sub bidding other parts of this job will see the radiant heat in the plans and assume no expense will be spared on this job and bit with that in mind.
Walta
The steel reinforcing was arrived at with only my l;imited experienc and lots of GBA articles including pictures and and lots of Youtube videos and videos from manufafcturers and the canadian version of GBA. The tubing plan was provided by the company selling the heating system. The thickness of the concrete was not mentioned in any of the submissions I got.
As I mentioned in comment #3 the advantages are worth the extra expense. I don't think I will mind if the floors are only 20*C. I will mind if they are 10 or 11 degrees. I think I saved four times the price of the heating system by doing all the formwork myself. A thousand feet of pex is hardly thousands of dollars. At the speed I am acquiring helpers it looks like I might end up doing most of the work myself. I could have bought special styrofoam insulation made to press pex for radiant heating into the channels provided but an experienced contractor in underfloor heating told me it wasn't as good as burying the piping in the middle of the slab. As heat is conducted in every direction it made sense to me.
Michael your comment about the difference in compressibility between concrete and is something I've wondered about. My daughters idea was that kids will more likely break their teeth on a conrete floor than a wood floor. I recently went dancing on a concrete floor and it makes a world of difference. I'm sure it is not just psychological. I poured a concrete floor in my bakery 40 years ago and the long hours spent on the concrete floor were one of the reasons I decided to retire when I did. Nils
Nilst,
" I don't think I will mind if the floors are only 20*C. I will mind if they are 10 or 11 degrees."
I'm, not weighing in on whether radiant floors make sense, just this narrower point:
With a properly insulated unheated slab, the concrete will track the indoor air temperatures within a degree or so, just as the rest of the surfaces (walls, ceiling etc.) do. So the floor would never be 10 or 11 degrees, and the difference between the unheated one and that with radiant tubes will be, as Michael said, maybe 5F max.
Malcolm, when I first learned about underfloor heating my first reaction was , wow imagine all the space saved in the house, no duct work no bulky radiators no noisy fans, and warm floors to boot. I was able to put the electrical panel , the heating system and hot water in a 12 inch thick false wall eight feet long. The ventilation system will be in the conditioned space above the upstairs bathroom. The entire heating ,ventilation and hot water system will only take up 4 or 5 square feet of usable conditioned space. Also, I've lived with forced air oil heating which I 'improved' by adding a heat pump which added central air conditioning to the mix. When the oil heater was heating it blew warm air so we were comfortable with the thermostat set at 18 but with the heat pump the air felt cool so the set point often was jacked up to 20 or 21degrees C. The fan was on for much longer as well. Floors that are one or two degrees warmer than the air will be an added bonus. The floor space I saved I won't have to heat and the space I do heat can be comfortable a a lower temperature. The thirty tons of warm concrete in a well insulated space will help us weather a several day power failure without freezing. We don't need air conditioning here, just bug protection.
"The thirty tons of warm concrete in a well insulated space will help us weather a several day power failure without freezing."
I think if you were to do the math on that you'd be disappointed by what it told you.
Are you insulating under the slab? That will probably make the biggest difference.
Let me state that in a modern over code insulated house, radiant heat is not an efficient use of cash.
However, I grew up with radiant in the early 60's and love it. Installed it in my last house and set my current house up for it.
A few issues with the comments:
There are not thousands of dollars buried in the slab, barrier pex is cheap. Manifolds and mixing valves add up, but really it is the design work that costs
Systems overshoot when the water temp is too high. Not really an issue with a good system design.
You want warm floors in a super insulated house, no problem.
It is frequently a struggle to get enough tube in the floor in an old code minimum house[pre ~2000]. One must frequently up the water temp to get enough btus for peak loads, and it can be a struggle to keep floor temps low enough.
For a well insulated PGH house etc, simply lower the amount of tube in the floor, as the heat output is not defined by square foot of floor, but linear foot of tubing and the temp of the water in it. By only running tube where one is likely to have one's feet, one can raise the water temp and the floor temp in those areas will give you the effect you wish. Basically in most rooms there is no one standing or sitting with their feet within 2 feet of a wall.
I think doing a manual J for each room, determining the the peak loss and calculating for 'X' degree water, how many feet of tubing you need. Since you will never be in a situation of needing a lot of tubing, you can play with the length that makes sense.
Looking at my kitchen, a double loop running just in front of the cabinets and not filling the space in the middle would mean a person working in the kitchen would have warm toes while standing in the middle not so much. Similar thought processes in other rooms. Coil under the dining room table, etc
I don't want a bare concrete floor, I have worked on concrete floors for 40 years and would prefer wood, whatever the compression numbers show. You don't need bare concrete to do radiant, you just need to adjust the water temps for the insulating value of the floor covering.
Again, rethink your choices, why pay for a boiler install at all? Install variable heat pumps and get free AC.
I think the broader point is that the system has to be planned and engineered. Too many people figure they'll put the tubing in while pouring the floor and figure out the details later. That is a recipe for disappointment.
I do however disagree with this statement:
"Systems overshoot when the water temp is too high. Not really an issue with a good system design."
OP said he will have 37 tons of concrete in his floor. To change the temperature of that slab by 1F takes 37,000 BTU, in or out. The only way to change the amount of heat flowing into the house from the slab is to change the temperature of the slab. When the sun rises in the morning or goes down in the evening the temperature of the slab is going to have to change by several degrees to adjust to the new conditions. With a boiler sized for the house it's going to take several hours of output for the slab to respond.
Overshooting was mentioned, not lag
In your well insulated and air sealed house, how many hours does it take to notice if you shut the heat off? In my moderately insulated, moderately tight, wildly overglazed house it takes hours to notice if heat is lost on a freezing cold day.
Radiant slab heat works, works well and done will it experiences neither lag nor overshoot any worse than say, a mini split with its weird little algorithm driving room temp.
what tends to happen in an underinsulated radiant slab house, is that there is insufficient tube to provide heat, and so the water temp is raised to make up for it. In a fully tubed floor this creates overshoot.
Sun loading is more likely to create overshoot, and slab radiant has difficulty with any external heat loads, IE a friends machine shop with the doors open in the winter.
A minisplit can go from producing nothing to 100% of its rated output in a couple of minutes. And it can go back to zero even faster. So can a conventional furnace.
A radiant floor can only change its output as fast as the floor can change temperature. In order to go to zero, the floor has to cool to room temperature, because the heat flow is driven by the temperature difference between the floor and the air. In order for the floor to cool, the heat in it has to go somewhere, and that's usually into the heated space. If the heat capacity of the floor is tens of thousands of BTU it can take hours for the floor temperature to respond to changes in the heat input.
[sigh]
minisplits frequently allow 3 degrees of variance as part of their control algorithm
of course it takes hours for the floor to respond, just as it takes hours for the rest of a well built house to respond
In practice, when done right, it is of no concern
Hell, I grew up with an uninsulated slab heated with copper coils and single pane glass and we never noticed temperature swings.
Handy snow free pathway around the house though...
Solar loading is a far more important problem in radiant slab, not the delay associated with the slab itself.
Again, radiant slabs work really, really well. The can perform as well as any other heating system and as accurately as any other heating system if you put the time into design and installation, implying otherwise flies in the face of facts on the ground.
They can also perform poorly as can every other heating system.
To put a fine point on it: Overshoot and undershoot are a possibility but not a eventuality with radiant slab heating.
In a 'green' house they are almost totally a waste of money.
Response to gus #16: "just as it takes hours for the rest of a well built house to respond." Not really--while there is lag time and potential comfort issues if you're trying to bring a house quickly from say 50°F to 70°, the air temperature will change in minutes. There are advantages to heated floors, but responsiveness is not one of them, and to claim otherwise is just silly.
why would you be bringing a house from 50 to 70?
not a normal thing to do .
It would probably take a week to drop a house with a radiant slab to 50 degrees.
Most mini splits are not sized to do so either
My [oversized according to comments here] garage minisplit takes several hours to bring the garage from 50 to 60+
radiant does not do setbacks.
to argue that a radiant slab cannot do its normal job is silly
[reply to #18]
OK, here's a real-world example: as documented in this thread: https://www.greenbuildingadvisor.com/question/hows-this-for-solar-gain
last year on December 21 my house had enough solar gain that it needed no heat, even though the outside temperature was my heating design temperature of 21F. According to the Manual J I had done when the house was build the heating load at 21F is 27,600 BTU/hr. So when the sun went down the heating load went from zero to 27K BTU/hr in a few minutes. Similarly, in the morning when the sun came over the ridge the load went from 27K BTU/hr to zero in a very short period of time.
OP says he has a slab that is 6" thick and 37 tons. Concrete is about 1.5 tons per cubic yards so that's 24.6 cubic yards, at 6" thick that's 1,332 square feet. What would it look like if my house had a slab like that? To get 27K BTU/hr out of that you need 20 Btu/sf, which means the slab has to be 10F above room temperature. That slab has a heat capacity of about 37,000 BTU/degree F, so to switch from zero output to 27K output you need to pump 370,000 Btu into the slab. With a heat source sized for the house that's over 12 hours of heating. So if when the sun goes down you start heating that slab, twelve hours later the slab will be warm enough to meet the heating needs of the house.* Then a few hours later the sun comes up. Now the heating need of the house is zero, but that slab is 10F hotter than the inside of the house. The house is going to heat up, probably to the point of being uncomfortably hot. The heat that you spent all night putting into the slab didn't go to keeping you comfortable at night, and instead went toward making you uncomfortable during the say.
*(This is a simplification and it's actually somewhat worse. The slab will warm slowly, the house will cool until there is enough temperature delta between the slab and the house to match the heat loss of the house. It will probably take a lot longer and the house will get cold).
Gee, what is it I said? exterior heating loads? Solar gain?
The kind of heating loads that are actively discouraged here?
Yeah, that
IT isn't the slab, it is the exterior loads, just like I said
Your example is the example of what not to do, not a failure of all radiant slabs
But that's real life. And solar gain in the winter is actively discouraged here?
OK, let's try another example then. Here in DC, according to NWS records, on March 30 it was 37F. On March 31 it was 66F. A 29 degree swing in just a few hours. At 66F my house needs no heat, occupant activity keeps it comfortable. At 37F it needs 64% of design load, or about 17,500 BTU/hr.
Using the same hypothetical as in my earlier example, the temperature of the slab would have to change by 6.4F. That requires about 240,000 BTU, or over eight hours of output from the heating source. When the temperature rises like that it's like you're running your heat full blast for eight hours before realizing that you don't need it.
Again
radiant slabs work, and have been for many decades, your opinion notwithstanding.
They do not constantly overshoot or lag, despite your contentions.
excessive solar gain is not the real world, it is poor design
sure you can make a system perform poorly if you design poorly, but it is not endemic to the system
The key is the ratio of the heat capacity of the floor to the heating load of the house.
I remember when radiant floor heat first got big in the late eighties and early nineties. Back then, it was common for houses to have heat loads in the 100K BTU/hr range and boilers rated at twice that. I installed my first radiant floor about 25 years ago, it was in a house built around 1870 and to meet the heating load we had to have wall radiators in addition to the radiant floor. In a house like that the heat losses were so high -- and the radiators provided enough relatively quick response capacity -- that the heat capacity of the floor wasn't an issue. Similarly, those old houses used cast iron radiators, which suffer from the same lag problems as concrete floors, but it wasn't a big problem.
From an energy-efficiency perspective the way we build houses has probably changed as much in the past 20 years as in the previous 100. The HVAC industry has struggled to keep up with houses which are much tighter and much better-insulated.
DC, I appreciate you sharing multiple examples using actual numbers to illustrate your case. That's more effective than repeatedly stating an opinion without evidence.
Thanks Michael (#30). That's very kind of you.
I have a thing about people over-using concrete.
nilst,
Some redundency in comment content, but here's my input.
Based on your comments in #3 reply - I would strongly recommend appropriately engineered footings under the two post locations holding up your second floor. If you are concerned about rebar chairs sinking into the under-slab foam during the floor pour, then just think about the weight on the two posts. In my own home all the posts are set onto 2' square pads that are below the under slab foam. Simply "adding reinforcement" around the posts will not likely be enough. The posts represent thousands of pounds on a pretty small foot print.
Also based on your rebar chairs sinking into the foam comment, I am guessing that you are in a heating dominant climate zone. If so have you provided sufficient under slab insulation, a sufficiently high psi foam for under the edge of the slab, and prepared the ground and foam if frost heave is a risk for your climate zone? Low density/psi foam is fine under the slab area, but best have an engineer rate psi for the thickened edge.
Regarding the mesh and attaching the pex. I installed pex in my basement and garage slabs for future use if I felt it necessary. I haven't. My garage has a 5" slab to accommodate my still imaginary heavy truck. The basement slab pour is only 4" thick and my cement contractor warned me about setting the pex too close to the surface. 3/4" was way too risky in his view and advised me to aim for a 1" minimum with more better. Not hard to do in a 6" slab, but as others have noted, 6" seems like overkill.
The floor slab mesh is 6x6 - 10 ga welded wire for both floors. I tied the three separate length matched loops of pex to the mesh with many, many zip ties. Zip tails cut off or aimed down. The chairs hold the mesh above 3"- 25 psi reclaimed XPS. The nominal O.D. of the pex is under 3/4" so the over coat of concrete is about 1 1/2" +- since the pex does not like to stay absolutely flat. Or straight or pretty much anything you want it to do. In the garage I zip tied to the top of the wire grid.
In the basement, I zip tied the pex to the underside of the welded wire grid as the over coat depth might be scarily close to the 1" minimum if the pex moved. I also needed to allow for relief cuts to be made without cutting the pex. If you are really interested in how I managed to tie it under the mesh I will reply. Meantime, once the pex and mesh were done, the mesh was held up by a combination of chairs and broken chunks of patio pavers. I cringed, but deferred to my cement guy. During the pour, the crew used rakes to grab the mesh and lift the areas where they walked it down. An art that seems like black magic, but the floor and pex are all fine. No cracks, no problems. The chair and paver chunks were no where near 1 support per sq ft. I can check my photos some time later if you like.
As others have noted, uneven length pex loops will not give you good results. Spacing too far will result in very noticeable banding of the warmth felt. It will also make a real mess of sizing your pumps and heat outputs. If you are getting free engineering from the pex suppliers, good for you. Think hard about where you want to bring up your loop ends and prepare a buck to hold things while the concrete cures. They do sell metal braces that force the pex into a curve, but I found that 1" pvc conduit elbow preforms to be as effective and it relieves the stress risk on the pex where it surfaces. And any troweling nicks.
Reply to dc. After careful measuring for my concrete order. and I found that my slab will be 17,5 cm thick center and 35 cm thick thropugh the grade beam. At that thickness I'll need 15 cubic meters; hence the 37 tons. Almost all references I could find put concrete at 2.5 tons per cubic meter. A cubic yard is 0.76455 cubic meters. The overshoot of the heating system is my biggest concern. The plan for the tubing simply ran tubing at equal spacing everywhere in the slab with equal length runs. No allowances were made for warmer temps in the bathroom or next to the exterior doors or under the stairs. I think I will reduce the thickness from 17.5 cm to 13 cm. That will save me 3.46 cubic meters of concrete or over 8.5 tons. Still the problem remains. There are two solutions that I can think of. One is to install a minisplit. That could also cool the house in the summer if needed. Alternatively, I believe there is a company in New Brunswick that makes an ERV with an inline heat pump.
My recommendation would be to size a minisplit to your cooling load. I didn't catch what part of Canada you're in but I think unless you're in the Maritimes or BC you're going to have significant cooling needs, although I don't think any part of Canada is cooling-dominant. Then size the radiant to make up the difference between the amount of heating your minisplit is capable of providing at your winter design temperature and your calculated heating load.
I would then place the radiant heat strategically and use a two-stage thermostat so that the minisplit only comes on for heat when the radiant is unable to keep up. This solves a lot of the problems with lag.
I recommend looking at concrete-less slabs as well.
I second the recommendation to engineer the post footing, and in particular not to put foam under them.
The critical factor is the bearing capacity of the soil, which is determined by local conditions. Around here we use 1500 pounds per square foot unless there's soil testing which shows otherwise. That's slightly over ten pounds per square inch. Yes, you can get foam that is rated at over 10 psi, but that assumes an "acceptable" level of deformation. With a post like that no amount of deformation is acceptable, if it sags by even an eighth of an inch your house is going to go out of kilter.
You also need engineered footings under the exterior walls. With appropriate supports under the posts and walls I think you'd be fine with a 4" unreinforced slab -- but I'm not an engineer. You could even look at concrete-free slabs, there are a couple good designs on the GBA website.
Concrete is pretty much the least green building material, you want to minimize its use when you can.
nilst,
I haven't read the Quebec building code, but in the provinces I'm familiar with, going from stem walls to a thickened slab moves the project from the prescriptive solutions in Part 9, to Part 4 which requires the foundation to be engineered. Quebec may be different, but it's worth exploring before going ahead.
I must admit that I haven't read the quebec building code either and I am going pretty much from the Canadian wood frame buldings guide. But we arer pretty much on our own here. Our small town has been through at least 3 building inspectors and about as many environment inspectors. They are difficult to find and they jump ship as soon as a bettter paid position elsewhere opens up. I abandoned my original intention to forego concrete entirely because of the lively opposition from engineer and builder friends, but so far the scrutiny from officialdom has been zero. I will take lots of pictures and notes in case and inspector does challenge my build. I believe that I am getting a much more thorough going over on GBA than any inspectors I have seen pass through here. I think if I was beholden to a bank for the wherewithal to build my house insurance inspectors would descend in droves.
DC Contrarian the foam under the posts is gone although according to my calculations the design load for the post is about 6000 lbs. Although eight by eight through 5.25 inches of concrete gives an area of 324 square inches which is , at 20 psi 6480 lbs. That is the design load which will only reached when a bunch of people are jumping up and down at the same time. But still not outside of the realm of the possible. so the styrofoam goes and the four foot square pads will be now 9.125 inches thick with extra reinforcing.
I have put 20,000 lb point loads on footings over foam, with plans stamped by a licensed engineer. 6,000 is a small-to-moderate load. People are unreasonably afraid of foam for some reason. It's pretty easy to quantify deflection to be whatever you think is safe. Every structural material deflects; proper engineering limits that deflection to acceptable levels. What "acceptable" is depends on the situation.
nilst,
You can very easily build a house that incorporates the high performance assemblies and details we talk about on GBA, that contravenes all sorts of requirements in Canadian building codes. I would caution you to make sure what you are doing meets those applicable standards. The preamble to the various codes makes clear that the legislation enabling building codes applies to the entire provinces whether there is local enforcement or not, and the owner is responsible for meeting them.