Remodel game plan

Im several weeks away from closing on my first house. It is in Kingston, NY–climate zone 6. It is a 2-story balloon framed, brick veneer structure, built in 1952. There is a 1″ gap between interior of brick and exterior fiberboard sheathing. Framing is dimensional 2×4, and interior surface is some type of plaster, there is no lathe. There is existing fiberglass insulation in bays, but anything Ive exposed is in poor condition.
Initially I thought Id drill several hundred holes and have expanding foam injected into stud bays. Primarily due to this site, Ive come to understand that the Wall is more complex a structure than empty bays wanting insulation.
I now have two competing plans. Each plan includes removing all exterior-wall plaster, increasing bay depth via the Bonfiglioli method and insulating.
Fully DIY plan would utilize R23 mineral wool batts, carefully installed, and an air-tight drywall installation.
Less DIY, therefore more expensive, plan would utilize a vapor permeable mesh and dense pack cellulose. I would pay to have cellulose installed, but would likely perform mesh installation. This approach would likely utilize battens and bring all services inboard of vapor permeable layer. Ive been checking out Pro-Clima products, but am open to suggestions. If I go this route, Id like the structure to perform as well as it can, but I don’t want to over-do any one aspect if it doesn’t improve the structure.
There are currently no weep-holes in brick veneer. Im wondering if either approach will necessitate additional ventilation for the brick-to-sheathing area, Ive read about solar vapor drive, and don’t want to create any headaches for myself by overlooking important details. The first and second floor exterior surfaces comprise about 2300 sq.ft.
The full basement is 7-1/2′ deep, 5-1/2′ of which is below grade, I haven’t put a lot of thought into improving the basements insulation at this point, but I am interested in improving air tightness of joints between foundation and framing. The attic is also unfinished, the roof is an L-shaped hip roof (cross-hipped?) and I eventually plan to blow in loose cellulose after air sealing that area. Im not planning to demo the second floor ceiling completely– but plan to remove 6″ of ceiling plaster at all exterior walls to carry up vapor permeable mesh if going with dense packed cellulose.
Im hoping for advice on each approach, and appreciate any insight that can be shared. Also, please don’t hesitate to critique either approach If my ideas don’t mesh with proper technique, Im new to this knowledge, and ultimately want to do the best job I can for my home, at a reasonable cost.
Thanks
GBA Detail Library
A collection of one thousand construction details organized by climate and house part
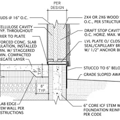
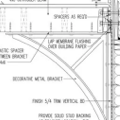
Replies
J.M.,
You mentioned that the wall has fiberboard sheathing, but you didn't mention whether there is a water-resistant barrier (WRB) like asphalt felt on the exterior side of the fiberboard. If the wall lacks a WRB, it is more vulnerable to water-entry problems.
You wrote, "anything I've exposed is in poor condition," so I'm going to assume that you have seen signs of water entry and rot. That's a problem.
Older brick-veneer homes carry lots of risks, because the flashing and WRB details may be missing. (For information on the correct way to detail a brick veneer wall, see "Flashing Brick Veneer.")
You also wrote, "There are currently no weep-holes in brick veneer." That's also a danger sign. Fortunately, it's easier to retrofit weep holes than to retrofit a WRB or flashing.
Here's the bottom line: You're worried about the wrong details. How you insulate your 2x4 walls doesn't matter very much. But how you address water-entry problems will determine whether your walls stand for decades or begin to rot.
A full assessment and the development of a retrofit plan can only be done on site. You'll need to look at the wall carefully from the interior for signs of water entry, so you can determine how to proceed. An important factor is the height of the walls and the width of the roof overhang. (Wide roof overhangs are protective.)
Thanks for for response. I will do more investigative work around the perimeter of the first floor walls, inspecting framing, plates and sheathing at the base of first floor walls.
I was referring to the existing fiberglass batts as the material in poor condition. So far, thankfully, any sheathing and framing I’ve exposed feels solid and dry.
Exterior walls measure 19’ from grade to soffit. The roof overhangs 18” around the perimeter of the house.
I recall reading some fiberboard manufactures waterproofed their products by treating the exterior side of boards with waterproofing agents. Would that be a suitable barrier 66 years later, if in fact that’s what I have?
If all framing checks out as sturdy and free of water damage, what would be a smart precaution to take from the inside, before closing up interior walls?
Ive opened several feet of 1st floor wall in each first floor room, including areas below windows, and haven't found any moisture damage. The framing on the foundation is visible from the basement, I haven't found any signs of water damage there either.
There is an existing exhaust fan in the kitchen, that penetrates straight through to the exterior. After removing the interior shroud, I could reach in about 6" on all sides of the duct, between the brick and the sheathing. I can not feel any material other than the fiberboard sheathing, so I'm presuming there is no WRB on the sheathing. Perhaps the exterior has been treated to repel water. I will attempt to get a better look at areas between brick and sheathing.
That said, and with the evidence that the building is not suffering water damage, would anyone care to comment on the two original insulating proposals?
J.M.,
The fact that you haven't seen signs of water damage is excellent news. Under those circumstances, I think you can proceed with your insulation work.
If you want to provide just a little bit more safety and redundancy to your wall system, you might want to consider one of the recommended approaches to detailing a wall with no sheathing -- even though your house has sheathing. (The problem in your case is that the wall may lack a WRB.) For more information on the details I'm talking about, see "Insulating Walls in an Old House With No Sheathing.")
Either cellulose or mineral wool batts will work fine, as long as the insulation is well installed. I wouldn't worry too much about the decision -- choose the insulation material you prefer.
Asphalted fiberboard pretty much IS a WRB- think of it as really thick #15 felt. With added weep holes and top vents It's very moisture tolerant, and not strongly wicking. But it's not stiff enough for dense pack. (1lb fiberglass would be OK, but rock wool batts are fine. ) Asphalted fiberboard is fine to even leave out in the rain, and with a 1" rainscreen gap this is just not a problem. It's not possible to make it air tight with tapes, but polyurethane caulk at all seams where it meets the framing would probably work. Horizontal seams can be taped, then troweled over with 1/8" or more of fiber reinforced duct mastic for better long term adhesion.
By "...dimensional 2x4..." do you mean rough sawn full dimension 2x4". If yes, that limits your Bonfiglioli strips to 1.5" if using R23 batts. You may want to consider 1.5" thick polyiso and long-screwing the gypsum board through the foam. While 3/4" polyiso foam + 1x Bonfiglioli strips would double the framing fraction's R value, 1.5" polyiso would more than triple it to more than R15. If it's milled 3.5" 2x4s go with the furring + foam Bonfiglioli strips.
In zone 6 using Intello or Membrain on the interior side would still be a needed to meet code if fiber insulation is used, but even skipping it would not be very risky with your assembly. In zone 5 either fiberboard sheathing or a rainscreen would be good enough to skip the interior vapor retarder, and you have both the fiberboard AND the rainscreen- it's not bad.
Thank you both for the responses, especially the note about the risk regarding dense pack cellulose and fiberboard sheathing failure.
By dimensional 2x4 I meant milled 3-1/2". I am intent on air sealing the exposed bays, attic, and basement where the foundation meets the framing. I am looking for recommendations for a polyurethane caulk for the task. Ive read through new-construction builds on this site and others, and have seen products like Prosoco Joint & Seam Filler, or Contega HF, but Im not sure if those products offer more resilience than I need for interior air sealing.
Also, I am considering leaving existing faming as-is, insulating existing cavities with R-15 mineral wool batts, and framing an additional wall with 2x3's 24" on center, 3-1/2" from the existing framing, and adding an additional layer of R-15 mineral wool. My impression is such an assembly will break the thermal bridge, and perform better than Bonfiglioli and R-23 batts.
I am wondering if such an assembly presents any risks to my exterior sheathing.
The building needs a new heating system, and I would like to install a combination on-demand domestic hot water and hydronic space heating boiler; there is natural gas in the house. I think panel radiators will work well in a relatively tight and relatively well insulated house, allowing me to achieve the rated performance of such a boiler. Ive performed heat loss calculations at varying degrees of tightness/r-value...several steps in either direction either allows a design day to operate at return water temps that allow flue gas condensation, or I'm looking at a system that performs as advertised approximately 60% of the winter.
J.M.,
I think than any brand of polyurethane caulk will work for the type of air sealing work you are talking about. Careful installation practices matter more than the brand of caulk you choose.
The wall insulation approach you describe is basically this: to create a double-stud wall by adding more framing on the exterior. That approach will certainly work. You'll get good performance. The major downside is the loss of interior floor area.
Note, as well, that you are choosing a method of wall insulation that is on the high end of most remodels. It will cost more and perform better than more typical approaches. There is nothing wrong with that, as long as your wall improvements are balanced by similar upgrades to your windows and attic insulation. Otherwise, your high-R walls won't make much sense.
Thank you for the reply, I haven't been able to determine whether any particular brand of polyurethane caulk is the one to choose, because I don't quite know what I'm looking for. I have come across several acoustical sealants that appear to fit the bill, but I don't know if that type of caulk is suitable--I can say they seem cheaper.
Im ok with loss of interior space. I find the deeper window frames appealing, in fact.
I plan to perform air sealing in the attic, and insulating as well. Probably blown cellulose. I was not planning to replace the windows. There are 22 windows in Ok condition, they deserve some attention. Most are difficult to open and close, due to layers of sloppy paint. I plan to deal with them as time permits, but expect to install exterior storm windows as part of the remodel.
A marvelous bet ideal for you! The Ugga Bugga free slot brings you into a tropical land. Back to when society had not completely evolved and people were not however lucid as they seem to be today. You are attempting to explore through the land and the clans that possess this beachy island, while likewise attempting to land some abundance and fortune. There are 3 reels and 10 paylines.You will likewise see one reward symbol, a sparkling cover. This is the wild, and it opens multipliers for punters. The free web-based Ugga Bugga slot machine https://www.slotozilla.com/free-slots/ugga-bugga doesn't have numerous extra highlights accessible beside nature. Players might view that as challenging to work with, yet the substitute without anyone else can end up being very important.
Andyadams222,
What's the question? Please elaborate or start a new discussion thread.