Remodel-Zone 4a

I am working on a 1300sq ft remodel in zone 4a (Baltimore). The home is a ranch, on a sloped site, with a basement that walks out to grade in the rear. Original construction is 2×4 framed walls and gable roof with board sheathing. I plan to do a full gut remodel. Strategy for air sealing and insulation is my main concern.
Game plan: zip sheathing, rain screen and cladding over existing board siding for air barrier and structural reinforcement. Double stud walls on the interior, 12″ deep with dense packed cellulose. Replace undersized roof rafters with trusses and apply taped OSB sheathing to underside of trusses and integrate into zip sheathing on exterior walls, with peel and stick membrane (as seen in the “An Affordable Passivhaus” article) to create an air sealed box. Build down below OSB sheathing on ceiling level for lighting, ductwork, etc… Fill attic, above OSB, with cellulose to achieve R60 and provide baffles and roof vents. Provide 4″ xps rigid insulation under new basement slab and integrate with 4″xps on block basement walls prior to pouring new slab.
I believe this construction plan is well within my construction crews skill sets. I have been pricing and working on other methods like rigid insulation over peel and stick membrane over existing board sheathing. But with the amount of money and time being invested into this project I want to make sure we are choosing a technique that will be most likely to perform well without getting too complicated. Does the plan above seem appropriate for my zone? Flaws in my brief plan description? Any other recommendations?
GBA Detail Library
A collection of one thousand construction details organized by climate and house part
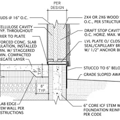
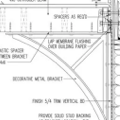
Replies
Charles,
Two reactions:
1. On a retrofit job like this, you lose a lot of interior space when you decide to build a double-stud wall by adding a row of studs on the interior. Installing exterior rigid foam or exterior mineral wool will result in less loss of floor area.
2. Removing the existing rafters and replacing them with trusses sounds like a lot of work. Is there any way you can beef up the roof framing by installing interior diagonal members (in other words, to create site-built trusses) or by sistering new rafters to the existing? Either of these approaches might be simpler (and perhaps cheaper).
Thanks for the response Martin.
1. I have already designed the interior with lost square footage from the double stud walls and I am good with it. I feel like a single layer of rigid insulation on the exterior walls still require me to build double stud walls to the interior (give existing 2x4 framing) to achieve R-40 and I am not comfortable going with multiple layers of 2" or more rigid foam because I feel like the additional long fasteners will be cost prohibitive. I have noticed that I can get 1.5" polyiso for less than zip sheathing and am contimplating using that to achieve my air barrier to exterior instead.
2. I am working with my engineer for options to bolster the existing rafters. Thanks
Do you approve of the overall plan in general for my climate? I feel like majority of the info for energy retrofits comes from colder climates. Summary: double stud walls with air barrier on the exterior and at the ceiling plan achieved through taped OSB. Attic with 18" +/- of dense packed cellulose and vented.
Charles,
Your proposed specifications will make your house one of the best-insulated homes in Baltimore.
Please use 5" of EPS instead of 4" XPS under the slab, and 3.5-4" of polyiso instead of XPS on the basement walls, to be a bit nicer to the planet. The the blowing agents used for XPS do 200x have 200x the greenhouse gas punch of those used for EPS an polyiso, and most of it leaks out over the first 50 years, at which point 4" of XPS would have a lower R value than 5" of EPS (which is already depleted of it's blowing agent in it's first year, and labled at the fully-depleted R.)
Be sure that both the interior wall foam in the basement and the exterior iso thermally break the foundation sill, but be sure that the insulation on top of the foundation sill is at least semi-permeable (EPS is good), to allow it to dry toward the exterior, and keep at least a foot of above-grade concrete exposed on the foundation to avoid moisture loading of the foundation sill from either the interior air or ground water.
The ZIP is more than an air-barrier- it's structural. If you skip the ZIP you'll have to install shear-panels or cut in some bracing to give it the necessary racking resistance.
Thanks Dana for the response, comments below:
"Be sure that both the interior wall foam in the basement and the exterior iso thermally break the foundation sill, " - they should over lap right? and look like they sandwich the sill plate if we saw it it a wall section drawing?
"but be sure that the insulation on top of the foundation sill is at least semi-permeable (EPS is good), to allow it to dry toward the exterior" ...... so if I use polyiso on the exterior I will switch over to EPS a little before reaching the foundation sill?
"and keep at least a foot of above-grade concrete exposed on the foundation to avoid moisture loading of the foundation sill from either the interior air or ground water.".....I don't have this option on the east side of the house. The sill plate is a few inches above grade. Existing grade drops 8' in elevation over a 25' span (in the east west direction) and allows the basement to walk out to grade level on the west side of the house. Ideas?
"The ZIP is more than an air-barrier- it's structural.".....I understand I was only going to delet the zip and go with foam if my structural engineer approved the existing board sheathing+foam assembly. I would actually like to not foam the exterior and just do the zip air barrier with double stud cellulose packed walls. Unless performance will suffer.
"Be sure that both the interior wall foam in the basement and the exterior iso thermally break the foundation sill, but be sure that the insulation on top of the foundation sill is at least semi-permeable (EPS is good), to allow it to dry toward the exterior..."
Uh sorry meant to say "interior" as the last word of that phrase. It's OK to go with iso all the way down to the bottom of the sheathing on the exterior, but when you do, the foundation sill would then need a drying path toward the INTERIOR. So at the sill plate level you'd have:
Siding | air gap | polyiso | ZIP | sill plate | EPS | fiber insulation.
The exterior foam delivers the performance without the hit in floor space you'd take with a double stud wall approach, and puts all of the structural wood at least partly inside the thermal envelope, where it stays warmer (=drier).
In areas where you can't get the necessary above-grade exposure for the foundation to stay dry enough to protect the foundation sill you have a few options. You can jack up that end of the house a hair while you slip-in an EPDM sill gasket as a capillary break to keep the sill dry. You could also dig down a foot on the exterior and back fill it with clean 3/4" screenings wrapped in landscaping fabric to let the concrete dry. But leaving it with only 6" of above grade exposure and insulating the interior (even with semi-permeable EPS) will leave the concrete cooler and wetter than it used to be, and wood in direct contact with that concrete will be wetter too.
I have been running the numbers for this wall/roof assembly in every which way possible from complete outside-insulation with foam to double stud walls and built down rafters filled with cellulose. I have finally found a combination that makes the most sense budget wise and interior finish wise:
Walls: cladding, 3/4" furring, 4" polyiso (2-2" layers staggered), tyvek drain wrap, original board sheathing, existing 2x4, drywall. (R-24) Not superinsulated home but the best I can do in my budget and should be appropriate for my climate zone 4a. Let me know if I am wrong.
Roof: metal roof panels, zip roof sheathing taped and integrated into wall rigid foam to create a continuous air barrier (overhanges removed to accomplish this), existing board sheathing, original rafters extended to 15" filled w/ dense packed cellulose,and drywall (R-52.5).
Question: can I have my air barrier at the roof sheathing level and roof/celing insulation at the attic floor level? There will be a gap between the insualtion and sheathing air barrier of almost 4' at the ridge location. Do you still recommend not using can lights in that ceiling where the insulation is due to air leakage? Or does that not matter here because the entire attic is inside the air barrier and I would not be losing air into an unconditioned space? Is it preferable, performance wise, to have the cellulose packed in the rafter bays tight to the air barrier? My main reason for asking is I can pack a lot more insulation on the attic floor and making the rafter bays deep enough to achieve r-5o or so will take extra materials and labor.
Thanks for everyone's help/responses.
Charles,
I'm confused. You mention "original rafters extended to 15 inches filled with dense-packed cellulose," but you also mention "roof/ceiling insulation at the attic floor level."
So which is it? Do you plan to install insulation between your roof rafters? Or do you plan to install insulation at the attic floor level?
If you want to install cellulose insulation between your rafters, you have to include a ventilation gap between the top of the cellulose insulation and the roof sheathing. That won't work if you have taped Zip sheathing. An alternative approach would be to create ventilation channels above the Zip sheathing, by installing flatways 2x4s above the Zip sheathing, to create 1.5 inch high channels from soffit to ridge. Of course, that approach means that you'll need two layers of roof sheathing.
For more information on insulating a sloped roof assembly, see How to Build an Insulated Cathedral Ceiling.
Sorry for the confusion. I am between both options. Cellulose in the rafter bays will require a little more time and materials on my side to accomplish. I can't go with an unvented hot roof assembly? (Got that detail from "High Performance Homes on a Budget", by John Abrams, JLC)
Cellulose on the attic floor is easier and will allow for more fill. But, I am not sure if can I have my air barrier at the roof sheathing level and roof/celing insulation at the attic floor level? There will be a gap between the insualtion and sheathing air barrier of almost 4' at the ridge location. Do you still recommend not using can lights in that ceiling where the insulation is due to air leakage? Or does that not matter here because the entire attic is inside the air barrier and I would not be losing air into an unconditioned space? Is it preferable, performance wise, to have the cellulose packed in the rafter bays tight to the air barrier?
Charles,
If you put your cellulose on the attic floor, then your air barrier must be at the ceiling drywall. When insulation is installed on the attic floor, building codes require that the attic be vented with soffit vents and roof vents. So the Zip sheathing on your roof won't help your air sealing efforts.
If you install cellulose between your rafters, building codes require a ventilation gap above the insulation. That requirement is explained in my article, How to Build an Insulated Cathedral Ceiling.
John Abrams has gotten away with using dense-packed cellulose in an unvented cathedral ceiling -- a code violation -- because of a local exception from an idiosyncratic code official. You can't depend on finding such a flexible code official in your area, and even if you could, I don't recommend the practice used by John Abrams. It's risky.
Martin,
If I use your detail showing rigid insulation on top of the existing roof deck,etc.... In the "how to build an insulated cathedral ceiling" link and I achieve my r-value goal with the rigid insulation on top of the existing sheathing, can I leave the rafter bays exposed to the interior and paint them?
Charles,
Yes, it's perfectly possible to install all of your insulation (usually rigid foam insulation) above the roof sheathing. Just make sure that the R-value of the rigid foam meets or exceeds minimum code requirements for your climate zone.