Replacing exterior insulation

I live in climate zone 6 in Southeastern British Columbia. I’m recently finished re-roofing the house and am now moving on to re-siding and upgrading the windows. My question is about an exterior wall, 2×4, that was built over top of the old siding (stucco), and then insulated with fiberglass batts. The old siding (vinyl) was then nailed to the new studs (it wasn’t sheathed with OSB or plywood). I’ve had a few people look at it (mostly exterior installers) and no one has seen anything like it before. The house was built in the 1950s and had 2×4 walls with pretty minimal insulation as far as I can tell. I’m wondering if there will be any problems with moisture if we add sheathing over top of the exterior studs, house wrap that, and then add new siding. Structurally the exterior stud wall is poorly built but taking it apart is not a viable option. Also, rather than leave the old fiberglass batts in, should I look at using spray foam in between the studs – then sheathing, or use a combination of spray foam and then the batts, then sheathing. As I mentioned, I’m asking around but most people haven’t run into something like this before.
Any ideas or comments would be appreciated.
EV
GBA Detail Library
A collection of one thousand construction details organized by climate and house part
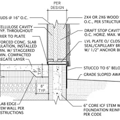
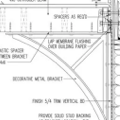
Replies
Photos would be nice. Does the old stucco look like it's in good shape - or does it have mold, flaking off, dark stains, etc? In other words do you think water has gotten to that layer and could there be significant rot below the stucco? I wonder about that because you said that the exterior stud wall was poorly built.
What you have now is unusual but not so bad. The main limitation I see is that the fiberglass performance is undermined by not having an air barrier on the outside. If you were to add sheathing, that would solve that problem, and you could retain the fiberglass that there there now, if it is installed well, filling the stud bays without gaps. But sheathing then has some moisture risk. A rainscreen assembly included a gap between the house wrap and the siding would help reduce that risk. And plywood would be a lower risk sheathing than OSB. But given that the wall isn't structural, you could also consider using just house wrap as the air barrier, and skip the sheathing. Or maybe thinner plywood, like 3/8", which would presumably high higher vapor permeability than 3/4" plywood.
How much moisture risk there is depends on, among other things,
1) What layers are inside your primary wall, and how well air sealed that assembly is.
2) How moist your climate is. I'm not sure where the boundary is between the pacific rain forest and the desert.
Spray foam would be expensive, would add significant global warming impact from the "blowing agent" it is made with, and wouldn't have much advantage over fiberglass because it is subject to the same thermal bridging effects that the studs introduce.
Derek,
You wrote, "Structurally the exterior stud wall is poorly built but taking it apart is not a viable option."
We can't provide advice unless you can clarify what this sentence means. If you exterior wall has significant structural problems, that fact would be a deal-killer. If you aren't sure, for example, whether the 2x4 studs are well secured to the old wall behind the studs, you need to talk to an engineer.
All of the materials you have described -- old stucco from the 1950s, for example, and an unsheathed wall filled with fiberglass batts -- are vapor-permeable, so I don't think that this assembly will trap moisture. As long as (a) you address structural problems and (b) you know how to flash your wall and install a WRB in a way that keeps out wind-driven rain, your plan should work. (A ventilated rainscreen gap is always a good idea, of course, so you should include one).
My guess is that your wall won't have a very high R-value. If you want to increase the R-value, spray foam would certainly be better than fiberglass batts.
Hi Martin, I'll try to clarify, the house has 2 floors. The second floor was a large addition that was done in the 1980s. It has 2x6 walls with poly vapor barrier. The 2x4 stud wall was built over the original house but only around the ground floor - it was called an energy retrofit on the blue prints. All of the windows and doors were built out to meet this new stud wall. So yes, the stud wall is now part of the structure. I'll take a few pictures in the next couple of days.
If I were to add spray foam, should I be concerned about it trapping moisture? between the layer of foam and the old stucco?
Thanks,
Derek
Here's a picture
Derek,
That doesn't look to me like old stucco behind the 2x4s, but I'll take your word for it.
If you want to install spray polyurethane foam on the exterior side of the wall, you'll need to make sure that the spray foam provides at least R-7.5. That's pretty easy, since that requires only about 1 1/4 inch of closed-cell spray foam. (I'm assuming that we are talking about installing foam insulation on the exterior side of an insulated 2x4 wall in Climate Zone 6; for more information on this issue, see Calculating the Minimum Thickness of Rigid Foam Sheathing.)
So you don't have to worry if you decide that you want to install spray foam on the exterior side of this wall assembly.
Hi Martin,
Those are the fiberglass batts, they are filthy because the vinyl put over them, attached to the studs, and lots of dirt and dust was blown in over the years. Would spray foam be the best option? Could I put rigid foam in between the studs attached to the house?
So what you're saying is if I took out the batts the closed cell spray foam would need to be R - 7.5.
Thanks,
Derek
If there is interior side poly vapor barriers in place it's going to be safer/better/cheaper to use open cell foam on the exterior rather than closed cell, and use asphalted fiberboard rather than plywood or OSB as the sheathing/nailer. That would provide the same or better air tightness, better dew point control a the structural sheathing behind the stucco layer, and about an order of magnitude higher drying capacity.
Concerns about summertime condensation on the interior side poly in this climate with such a vapor permeable exterior would be nil, since the outdoor dew point averages in SE B.C. are WAY below the room temperature of an air conditioned room.
If there are NO interior side vapor barriers on the original stucco wall a full cavity fill of open cell foam is still the better option. The difference in thermal performance between a full cavity fill of closed cell with 1/2" CDX or OSB on the exterior and a full cavity fill of open cell with 3/4" asphalted fiberboard on the exterior is less than R0.5, but the moisture resilience of the latter is much better.
The bad rap on asphalted fiberboard came from using it as a moisture resilient sheathing behind brick veneer & stucco walls before homes were air conditioned in climates with much higher summertime dew points than B.C.. When air conditioning was retrofitted the wall cavites became mold farms. In this case the stucco isn't being subjected to dew/rain wetting, and with R15 of o.c. foam + fiberboard outboard of the stucco, and R11-R13 cavity fill on the interior side, the stucco will remain super-dry, and will never be sun-blasted into releasing moisture at a high rates even if it were to become moist.
If for some reason you can't find a source of asphalted fiberboard near you, the next best choice would be exterior grade fiberglass faced gypsum board (eg GP DensGlass).
Since the exterior sheathing is not structural, you don't need to use a structural grade fiber/gypsum board or the full-on fastening spacing for structural fiberboard/gypsum, but there's no harm in making it structural.
(edited to add): This is all predicated on the notion that the new siding will either be vinyl, or built out with 10mm of rainscreen gap (as if it were in SW B.C. rather than SE B.C.) for optimal drying capacity toward the exterior.