Retrofit basement insulated floor

Home in zone 5A built in 1999 with CMU foundation walls. No evidence of insulation or vapor barrier under the concrete floor in the basement.
The basement is partially finished and will be removing finishes to retrofit, but do not want to break and repour the entire floor. Desire is for a porcelain tiled floor.
There is no standing, pooling. or running water in the 2 years I have owned the home. The floor has three covered sections: glued tile carpet, glued tile bathroom(?), and painted. The painted floor is bubbling under some taped saran wrap. This was first noticed after moving some plastic storage bins on the floor that smeared paint underneath when moved.
I don’t have any slab moisture readings. This summer/fall, the basement at 4′ height has read between 67-69 degrees F with RH between 48-55%.
Two main questions:
1. In addition to 2″ of EPS foam, is a poly or liquid vapor barrier recommended underneath the foam when using an impermeable finished floor (e.g. porcelain tile). The slab does not have either underneath.
2. If the rigid is not under the framing, how is the insulation and vapor barrier properly connected/sealed to the framing?
My plan is currently:
1. Interior drain tile system with poly vapor barrier up the wall.
2. Metal stud framing
3. 2.5″ Spray foam rim joists and walls
4. 2″ insulated + vapor barrier + floor?
Some options I’ve read:
1. Dimple mat (vapor equalization) + floating rigid + floating plywood
2. Liquid or poly vapor barrier + rigid + secured plywood
3. Liquid or poly vapor barrier + sleepers (foam in between) + plywood
The tile installers I’ve talked to don’t like these options and would prefer to tile directly to the concrete. Not having plywood or organic materials at all is an interesting option.
A possible foam + tile option is using Kerdi-board (https://www.schluter.com/schluter-us/en_US/Building-Panels/KERDI-BOARD-Panels/Schluter%C2%AE-KERDI-BOARD/p/KERDI_BOARD) or Wedi-board (https://www.wedi.net/en/products/building-systems/building-board/). Kerdi is ‘reinforced’ EPS tile substrate and Wedi is XPS. I am unsure of the order in which these are properly installed, and with or without a liquid or poly vapor barrier underneath.
I’ve read mixed thoughts on whether a liquid or poly vapor barrier should be used in addition to rigid foam, which should be a vapor barrier at 2″ thicknesses.
e.g. https://basc.pnnl.gov/resource-guides/rigid-foam-insulation-installed-over-existing-foundation-slabs#edit-group-description
e.g. https://www.finehomebuilding.com/2010/03/11/finishing-a-basement-floor
A tile installer may be hesitant to install a foam board on a ‘sealed’ slab (adhesion issues?), so is the rigid foam itself really good enough as a vapor barrier (when properly installed, etc)?
With foam being only semi-impermeable, does using an impermeable porcelain tile (or impermeable decoupling layer) necessitate a liquid/poly vapor barrier under the foam?
I really want to get insulation on the wall and know the floor will add quite a bit of thickness.
Questions I can’t wrap my head around:
1. Is the proper order of installation:
a. 2″ panel of rigid under the framing, pushed against the wall, and foamed with the wall insulation
b. When the floor is ready to be laid, additional panels are connected to it and tapped/sealed?
2. If the framing is done first with a break on the bottom plate, how is the raised edge of the insulated floor properly barriered and sealed against an open stud cavity or gypsum?
Probably overthinking this quite a bit but I think it is important to nail all details as much as possible when designing a plan.
GBA Detail Library
A collection of one thousand construction details organized by climate and house part
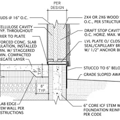
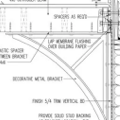
Replies
Hello Curious
https://www.greenbuildingadvisor.com/article/whats-the-best-basement-flooring-system
This article talks about the risk of water getting to the slab. It correctly explains that the most common insurance claim is water damage. If you put down foam, and many people do, you would need to rip it up if ever you get a flood, like a laundry washer leak, bathtub overflow, furnace a/c drip line clogging. The list goes on .
If you put tile, I would skip the foam. I would “paint” on a product like red guard (there are other brands that maybe better). Check first with the manufacturer to confirm they endorse this application. Then tile over it. It is the same approach taken with showers. Of course no insulation means colder floors.
Not sure why you need tile, maybe a preference. I love hardwood personally. I never wanted anything to do with laminated floors. I installed Soltice brand vinyl plank flooring against my will and now I love it.
https://www.inhaussurfaces.com/products/tobacco-oak
> Not sure why you need tile, maybe a preference.
Preference for now. We have hardwood and LVT in the main floor. While I am not 100% satisfied with LVT, it is an option if there is no 'great' way forward with ceramic tile.
> https://www.greenbuildingadvisor.com/article/whats-the-best-basement-flooring-system deciding between Delta FL and Ditra Heat.
Kind of the same place I'm in actually. My goal is ultimately to see if I can have electric radiant heated tile floors. I understand these are not "green", but insulation underneath at least drastically reduces the energy lost to the slab.
For reference, I've attached the Ditra-Heat with Kerdi-board document I found. (Layering as follows: Concrete -> unmodified thin-set mortar -> Kerdi-Board -> unmodified thin-set mortar -> Ditra-Heat -> unmodified thin-set mortar -> stone/tile). I don't know how much the heating provided would aid in drying the foam when it gets wet, how far, or to what degree.
It's not nearly as good as foam insulation, but Ditra-Heat DUO would probably be a 'safer' but much more costly to run option, then. It incorporates a thin fleece thermal break. (product: https://www.schluter.com/schluter-us/en_US/Floor-Warming/Schluter%C2%AE-DITRA-HEAT-DUO/p/DITRA_HEAT-DUO). Energy lost to the slab, but warming the slab and floor itself can aid in drying and preventing mold growth in the floor.
If foam is chosen, how to seal it to the framing? or does it need to go underneath the framing?
> https://www.greenbuildingadvisor.com/article/whats-the-best-basement-flooring-system
I think the first question has been answered due to reading the article/comments in depth.
https://www.greenbuildingadvisor.com/article/whats-the-best-basement-flooring-system#comment-10886 -> not that tile 'can't' be done [on plywood], but it's 'easier' on concrete
https://www.greenbuildingadvisor.com/article/whats-the-best-basement-flooring-system#comment-10888 -> poly above the slab. rigid is 'almost as good', but not quite as
https://www.greenbuildingadvisor.com/article/whats-the-best-basement-flooring-system#comment-10891 -> poly -> rigid -> subfloor
https://www.greenbuildingadvisor.com/article/whats-the-best-basement-flooring-system#comment-10907 -> as much foam as possible and cement board/plywood. Fine to install poly on top.
https://www.greenbuildingadvisor.com/article/whats-the-best-basement-flooring-system#comment-138910 -> [poly] won't do harm. may help. might as well install it.
Liquid coatings always have a chance to come up/bubble/etc. Poly would be cheaper.
So now I have to see if I can find someone to tile on a backer on poly.
Edit. After thinking about this, I don't think anyone would ever do this since the poly isn't adhered to the ground. I'll look into RedGuard or other liquid-based sealants that work with tile systems.
The second question still remaining in regards to the foam connection to the framing or if the foam goes under the framing.
The second question still remaining in regards to the foam connection to the framing or if the foam goes under the framing. There are no rules.
If you do insulate with a foam insulation (generic term) product:
... and you decided to put the wall framing on the concrete floor, just put a quality sealant at the edge of the foam insulation, between the foam and the concrete, where the foam insulation meets the framing. I would put a foam gasket under the steele framing to avoid potential corrosion from humidity in the slab.
It might be eaiser and faster to just put the foam down to cover the entire floor before framing walls. If you put the walls on top of insulation you just need to be sure that the foam insulation has the correct compression strength. Regular Type 1 XPS may be fine but I don't know myself. You could just call the company of the brand of foam you are buying if no one on GBA is able to anser that question.
This is awesome, thank you!
> It might be easier and faster to just put the foam down to cover the entire floor before framing walls.
This is what I was thinking initially. Due to time/money the foam could be exposed for a long time, and I'm not sure how much damage is a concern while walking on it/framing/etc. The foam gasket is something I hadn't stumbled upon yet, so thank you for the suggestion!
> If you put the walls on top of insulation you just need to be sure that the foam insulation has the correct compression strength.
A great point. I re-found this thread regarding compression. https://www.greenbuildingadvisor.com/question/xps-or-pvc-under-base-plate. Essentially, as long as the wall is non-load bearing, it should be ok, but good to keep in mind and err on the side of caution if this is the decided route.
I am faced with a similar situation in an old house. My basement is unfinished at the moment. When completed, it will have a mechanical room, storage room and large playroom/entertainment room. We have plenty of ceiling height.
I have decided to go with a dimpled floor product like Delta FL or similar with T&G OSB on top. DriCor is double the price. We will roll out the dimpled floor and tape all the seams. I envision a 4" lip riding up the foundation bottom and taping the corners. This should provide a uniform vapor barrier.
Next we will frame 2x4 walls 2" from the foundation walls, providing plenty of space for electrical etc. after we spray 2-3" of CC Spray Foam on the foundation, locking the 2x4's in place.
Since my air handler, HWHP, ERV and ducting will be in the mechanical room, it'll be easy to condition the basement.
As for flooring, we're going with a luxury vinyl plank product. I suppose you could use a concrete board over the dimple mat and then install tile. Not sure about that. But I like the vinyl plank idea. Easy to remove if need be, unlike tile.
BTW we had tile floors on a slab in our house in Florida, no less. The floors were always cold.
Good luck with your project.
We did a 4500 square foot commercial project which involved doing an insulated over-pour. 2" of EPS, then about 2" of concrete over the existing slab to contain the radiant heat tubes. A pallet jack (so high point loads) was used pretty much daily on that slab to move heavy pallets around. So if you want tile, and have 4" of height to spare, I would consider that option, particularly if your floor is not very level currently, and you really want tile.
Dow (among others) has their HI-40 and HI-60 products which are a lot more resistive to compression, however you don't need them unless you are planning to use very heavy equipment on the floor.
LVT is a lot warmer on the feet over tile. My basement is currently a water proof (or so they claim) LVT over ceramic tile and the heat conductivity factor makes for a floor that feels a lot warmer for sure.