Rigid foam in Zone 5B basement

Instead of posting more questions in my earlier thread here: https://www.greenbuildingadvisor.com/question/space-and-cost-effective-basement-insulation
I decided I should update my question with the new idea so that future readers can get the proper information at the start instead of having to read through a lot of comments.
So we know fiberglass, even with a gap between it and the concrete basement is a horrible idea in my zone 5. So the idea is that I need continuous insulation on the concrete so that there will be no condensation due to dew point temps in the summer. To achieve this the key is that continuous layer, yes? Meaning all edges of the rigid foam insulation are taped and or sealed with spray foam/caulking. Meaning 0% of indoor air can contact the concrete wall. Okay, simple enough, got it.
Now in my zone, I believe it’s Zone 5b – not sure how much that differs from 5a but my understanding is we are not quite as cold or maybe wet as 5a in the winter? Okay well moving on, the dew point for my zone in the summer is what determines what R-Value my continuous layer of insulation needs to be to prevent the surface of that concrete from condensating, right? In my zone it sounds like that is anywhere from R5 to R8 – can someone confirm what that number is, and what exactly the simple science is behind it if I am misunderstanding it?
I’m a simple man on a simple budget on this current task, so I don’t want to special order mineral wool insulation (which is about 4.2 times more expensive than fiberglass in my area, mainly due to special ordering I think.) and I don’t want to use more foam to achieve my goal of R15-R20 walls due to cost, so that means I probably am going to use fiberglass *cringe*. BUT, as long as I have that rigid foam layer meeting the minimum required R-value for preventing condensation, whatever I do after that in terms of insulation should not matter, right? The threads I read here on not clear on this. It’s sort of hit and miss on the replies but the basis is this: Achieve the needed continuous rigid foam layer, whether it’s XPS, EPS, or PolyISO (prefer PolyIso), and then you can insulate with more of whatever material. In this case, fiberglass. Will this cause any issue? Specifically R-13 CertainTeed Kraft faced fiberglass insulation. My reservation to not using unfaced fiberglass is that it’s harder to get to stay in place especially if I am framing my interior portion of the wall on 24 centers. It seems 24″ o.c. framing is harder to have fiberglass fit snug in versus 16 o.c. framing since there is a larger span the insulation has to hold up against. My second question would be related to this, will the faced fiberglass cause an issue with any moisture/vapor stuck between the rigid foam and the facing of the fiberglass insulation? Theoretically if the concrete wall is insulated with the rigid foam, then the moisture will come and go between the concrete floor below and/or the floor joists at the basement ceiling level, right?
I’ll edit this post down to more simple questions if that is easier – I was trying to give my questions some background to journal my thoughts.
GBA Detail Library
A collection of one thousand construction details organized by climate and house part
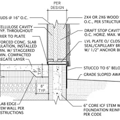
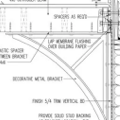
Replies
You need a layer of rigid foam thick enough that the inside facing face of the foam won’t drop below the dew point. If you have, for example, R8 foam and R11 Fiberglass in a Wall, about 42% of your total insulating value is from the foam (8 / 8+11 = 0.42). If you have 70 degrees inside and 30 degrees outside, you have a 40 degree temperature differential across the entire amount of insulation. 42% of that 40 degree difference gets added to the outdoor temperature, so (0.42% x 40) + 30 = 48 degrees on the inside facing face of the rigid foam. If 48 degrees is above the dew point for whatever your indoor humidity level is, then you’re safe.
Personally, I’d try to save money by finding some reclaimed or otherwise discounted polyiso and use that for the full R value of the wall. It’s just so much easier to install the rigid foam and be done rather than to frame out a wall to use batts.
Bill
Bill,
I am not sure what my summer dew point is. But I can find out. The fiberglass I was talking about is R13 so even worse of a ratio. I know technically with studs that wall build is probably R11 or R12 after that fact. I'm still uncertain on the amount of rigid needed but it sounds like if I have R13 fiberglass then I need to bump that rigid foam layer up more than R5.
I'm a framing machine, meaning the interior walls as I go room by room will be very easy for me to do, and I enjoy having the traditional wall build for electrical, coax, smurf tube, ethernet lines, drywall hanging, shelving, and such. I also like the cheaper value of the fiberglass. If I find polyiso like you say, then yes I would do that - so far no luck and I check craigslist (our local sale site) about once a week. The cons of living in the middle of nowhere. Regardless, I do not want to discuss this method at the time being and would like to stay focused on my original questions. I think those questions are both important for me and future readers - especially those not able to find reclaimed rigid insulation. As I said, almost every post here is very hit-and-miss on getting direct information about those questions and concerns. I do appreciate your suggestion though and will not dismiss it totally - I just don't want to rabbit trail off the primary post I have until a few more folks chime in if that makes any sense. Thanks for explaining the percentages correlation to dew point.
Just remember that the dew point inside your basement is dependent upon the air temperature and humidity of your basement air, not the outdoor air. If you measure the humdidity and temperature in your basement, you can look up the dew point easily for that info.
Bill
Nicholas,
You're under a few misapprehensions. The most dangerous time of year for condensation in this type of wall is winter, not summer. (During winter, the concrete is coldest -- and cold surfaces increase the danger of condensation.)
The easiest rules to follow on this question can be found in this article: "Calculating the Minimum Thickness of Rigid Foam Sheathing."
Assuming that your stud wall is framed with 2x4s, and you are in Zone 5, the rigid foam needs a minimum R-value of R-5, as shown in the chart in that article.
While the article discusses above-grade walls, not below-grade walls, applying the rules to situations like yours (a basement) is a safe, conservative approach.
Martin, thanks for correcting me. I figured it was since the summer is hot and humid the concrete would be warm and come in contact with the cool dry basement air causing condensation but I suppose that is opposite of what would happen.
Can you give me any information about using faced fiberglass in those 2x4 stud cavities? Must it be unfaced?
The article states "This type of wall must be able to dry inward, so it’s important to avoid low-permeance layers like polyethylene, vinyl wallpaper, or closed-cell spray foam on the interior."
However, does the paper faced fiberglass fall under that? I would assume YES but not sure, or if it applies when the foam is now on the inside of the basement wall vs outside those exterior walls.
>” I figured it was since the summer is hot and humid the concrete would be warm and come in contact with the cool dry basement air causing condensation but I suppose that is opposite of what would happen.”
That’s backwards. Condensation occurs when warm, moist air comes in contact with a cool surface, with “cool” being a temperature at or below whatever the dew point is for the “warm, moist” air. You can determine dew points for any combination of temperature and relative humidity in air with a psychrometric chart.
Basically warm, moist air and a cool surface results in condensation. Cool air with a warm surface does not.
Bill
If you do the calculations with the minimum recommended foam thickness, you will find that it will drop below the dew point. This is OK.
Jon, What do you mean by "it will drop below the dew point"? :)
According to the information, I need a minimum of R-5 on the wall before I insulate with R-13 Fiberglass.
If you have an asphalt-impregnated kraft paper face on your fiberglass batt, it's a bit of a smart vapor retarder in that it varies from about 0.5 perms (a solid Class II retarder) when it is dry to about 5 perms (a solid Class III vapor retarder) if it gets wet. So in your assembly, that is ok.
On the other hand, for a below-grade assembly that follows Martin's article on minimum thickness of sheathing, you don't need any facing at all if you are finishing off the assembly with gypsum wallboard and latex paint. This is especially true because it is really only the above-grade portion of your basement wall that is seeing the conditions driving the dewpoint calculation and resulting rigid insulation thickness.
Peter
Peter,
Thanks for the reply. The reason I like kraft (and asphalt) faced instead of unfaced is simply for the ease of installation and getting it to fit properly. I don't install fiberglass much anymore, especially on 24" centers. But from time before, I noticed that the unfaced fiberglass is not as fun to work with.
I would need the R-5 minimum for foam insulation, I am thinking R-7.5 would be better but that would throw off the foam to fiberglass ratio. This is not a concern, is it?
I will have 1/2" drywall and some latex paint covering this wall when all said and done. In one room I will be limited on space so that room will not have 2x4 framing and instead something like 2.5 inches of foam only.
If you need unfaced batts, try mineral wool. Mineral wool is generally unfaced, and is far easier to install than fiberglass since mineral wool has some structure to it — it can self-support without need for stapling.
Bill
I will not be using mineral wool here due to the cost. I have used mineral wool before in 2x6 framing and although it sucks to install it is a good product. I break out bad to the stuff - while fiberglass doesn't phase me. Funny stuff. Anyway, the point of this post is to determine how much XPS or Poly foam is needed and to learn if paper-backed or paper-faced fiberglass is kosher in this instance. I'm not getting a direct enough answer but think I will just go for R5 to R7.5 of XPS foam available locally and then install R13 paper faced fibgerglass in the stud cavities and call it a day. There are a lot of better ways to do this but I am going for cost savings versus energy saving returns in a basement that is already partially insulated due to 6' of earth all around the basement. I'm just hoping that R5 or R7.5 of foam will be compatible with R11 or R13 paper faced fibgerglass insulation.
Dana is giving you pretty detailed info in post #12, and he’s one of the more knowledgeable people on here regarding insulating assemblies like you’re trying to do. You may want to have another read of his post. If you only have XPS available, go for the R10 stuff which is 2” thick. It’s really the R value that matters, not the thickness of the material you choose.
I highly recommend wearing a tyvek suit while installing either fiberglass or mineral wool. Tyvek suits are cheap, and they have saved me a LOT of itching!
Bill
In my area RECLAIMED fiber faced polyisocyanurate roofing foam is cheaper per R than box-store pricing on batts (even "contractor roll" R11s). At 3" fiberglass faced or asphalted paper faced polyiso runs between R16.5 and R17. Strapping it to the wall with 1x4 furring through screwed to the foundation 16-14" o.c. with 4.5"-5" masonry screws provides a handy nailer for the wallboard. That stackup takes up less space than R5 foam + 2x4/R13 that it would take to hit code-min performance with a fiber insulated studwall with (minimal) dew point control. Routing out the foam for wiring and electrical boxes takes some planning but it's not a big deal. (This is how I retrofitted my own basement.)
Alternatively, 2" roofing polyiso runs R11 -R11.5. If you wanted to build a 2x4 wall and add contractor roll R11s or R13s that would deliver ~ R20 "whole-wall" performance comparable to or slightly ahead of the 3" polyiso-only solution, with considerable rather than minimal dew point control.
In my area reclaimed 3" polyiso runs ~$15-25/sheet for 4'x 8' (sometimes less), 2" runs $10-18/sheet (sometimes less.)
To find local foam recliamers try running this search every week or so on more nearby locations:
https://denver.craigslist.org/search/sss?query=rigid+insulation
https://saltlakecity.craigslist.org/search/sss?query=rigid+insulation
https://boise.craigslist.org/search/sss?query=rigid+insulation
https://reno.craigslist.org/search/sss?query=rigid+insulation
Dana,
The nearest one you listed is Denver and that is 4 hours away. They do not have individual sheets for sale, and I don't want to buy as many sheets they sell in a bundle, but then to get the stuff shipped here it would cost more than I can get XPS for unfortunately. It looks like the market has picked up on people wanting to re-use this stuff and that demands a higher price or quantity to be sold. No more "here is leftover foam from the last commercial roofing gig we had, $5 a sheet first come first serve" you use to see.
Anyways, I read what you said as basically saying do R10 and that paper faced fiberglass is okay between the studs but 3" of recycled poly-iso is a better and cheaper system if available to you. (And that is currently not so).
Thank you.
Run your own searches to find reclaimers on locations closer to you. I just threw out a random sampling that happened to be in 5B locations, not anything like an exhaustive search of even the Craigslist ads.
I have something like a half-dozen materials reclaimers selling used roofing iso within an hours drive, not all of whom advertise in Craigslist. Talk to some commercial roofers for leads on the quantities you need. 4" of EPS would work too (but that takes longer screws.) Nationwide Foam will ship to your build site from regional depots (for a price), if you need more than a few sheets. (Buy 10-15% more than needed to cover damaged sheets, etc.)
>"...I read what you said as basically saying do R10 and that paper faced fiberglass is okay between the studs..."
To meet/beat IRC code min performance with reasonable dew point control only takes 1" foil faced polyiso (R6) and contractor roll kraft faced R13s in a 2x4 16" o.c. studwall. That stackup has performance very comparable to 3" of roofing polyiso strapped to the wall with furring.
If you need/want R20 whole-wall performance (=better than code min) bump that to 1.5" of foil faced polyiso (R9-ish).
Kraft facers are fine as long as it doesn't flood.
Is it recommended to put atleast a 1" layer of EPS or reclaimed XPS directly against the concrete to keep the Polyiso from sucking up the moisture?
>"Is it recommended to put atleast a 1" layer of EPS or reclaimed XPS directly against the concrete to keep the Polyiso from sucking up the moisture?"
Nope.
It's perfectly fine to put fiber faced polyiso in contact with poured concrete or CMU foundations. The facers on roofing polyiso are Class-II vapor retarders, and resistant to liquid moisture. For the foundation to be wet enough for moisture to wick, into the polyiso through the facer you would have much bigger problems to deal with.