Sanity-checking a DER project
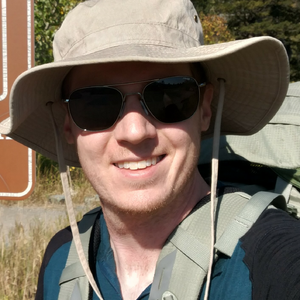
Hi all, long time listener first time caller… Looking to sanity-check / get input on my ongoing DER project — not Deep Energy Retrofit, more Dumb Everything Retrofit!
The House:
Zone 5A (Cleveland, OH area), ~2000sqft. Full basement, attached garage, basically a ranch but the back (north) side roof is low-slope so it has a full second floor a bit smaller than the first floor. Original construction 1955, has a sunroom on the north side added in the 90s with aluminum operable windows and sliding door, vinyl replacement windows around 2000, cellulose blown into vented attic and walls (from the exterior) around the same time. Siding is a stack of original lead-painted cedar lap, about 1/4″ of wishful thinking EPS, and vinyl.
The Cast & Crew:
My dad: Licensed engineer, environmentally conscious, but high-performance building knowledge a bit outdated. Built* a super-insulated house 20-30 years ago (double stud walls, fiberglass insulation, well detailed poly vapor barrier on inside) (*well, honestly it’s an ongoing project LOL). Can stamp architectural & structural drawings in this jurisdiction, and has been an immense help in the process.
Me: Electrical engineer, have a full time job, but enjoy learning & diving down rabbit holes. Very subject to analysis paralysis. Strong drive to do things “the right way” / “the best way” the first time around.
My family: My wife grew up in an apartment in a big city, and is more than somewhat mystified by American remodeling & DIY culture. Generally tolerant, but primarily wants a complete house to live in. My daughter is almost 2 and has few opinions on the matter.
…And a handful of close friends and other family members who are willing to lend a hand / provide muscle.
The Project:
Bought the house in late 2018. Kitchen was very in need of updating and second floor layout was weird. In the first 6 months of 2019, we drafted plans for an interior remodel, gutted the kitchen and most of the second floor, did some structural changes to first floor layout, removed & built new staircases, replaced most supply plumbing & electrical service, moved in, and had a baby. The “moved in” step was definitely jumping the gun, as progress has slowed to a snail’s pace with baby, COVID, etc. and we’re still operating with a temporary kitchen setup. However, all the research I’ve done over the past 2 years has led me to reevaluate the whole project, with more of an eye to the building envelope and performance rather than just interior functionality. Given that living in the space while working on it frankly isn’t working, we’re planning to move to an apartment for a bit to finish up the project, which means that if something’s going to be done, the time is now.
The Plan:
Move out. Complete the initially specified interior work, plus:
-Roof: The roof is about 20 years old, and in “just okay” shape. We’re also adding dormers to the front, as part of second floor restructuring, so it’s a perfect opportunity to re-roof, which is a perfect opportunity to convert to an unvented attic and add insulation above the sheathing. The best balance of cost, environmental impact, and weight seems to be polyiso foam — specifically about 6″ in either 2 or 3 layers with staggered seams — coupled with either fiberglass batt or netted cellulose below the sheathing. As long as the fluffy insulation is less than about R-30, 50% of the insulation will be outboard of the sheathing and air barrier, which I believe is OK in my zone. This plan also helps with the fact that in some areas, there’s only a 2×6 rafter thickness available for interior insulation (currently packed with cellulose and vented by dreams, I guess). Take this opportunity to add overhangs, and also let the insulation overhang some to tie in with future wall continuous insulation.
-Windows: What a rabbit hole! For budgetary reasons, planning to get new windows only in the worst performing areas. The existing vinyl replacements are not great, but still functional, while the existing sunroom windows are leaky, the double panes are failing, and the metal frames are uninsulated. We’ve brought the sunroom into the structure as a dining room, so it needs to be habitable. So, replace the sunroom windows with some fixed, triple pane windows and a good door. The second floor layout needs a couple new windows, and a couple are getting moved, so anything up there that gets touched also gets replaced. The others get left. The living room has a large, built in place window wall assembly — for that, we’ll need to get IGUs and either use the existing frame or field-fab a replacement.
Window manufacturer is something I’ve spent a lot of time looking at, with no firm conclusion. I’m against vinyl, and would prefer aluminum clad wood. Interested in tilt-turn operation. Zola has a 25k minimum, so they’re out. Marvin is ridiculously expensive compared to everyone else, and has comparatively not great performance. Alpen makes me nervous with the suspended film thing, plus their tilt turn is only available in the PVC line (their fiberglass line is Living Building Challenge compliant, which is cool, but I’m not a huge fan of casements). Optiwin (thru 475 high performance building supply) has some nice stuff, pricey though especially with $5k shipping and long leadtimes. Not sure who else I should be looking at / quoting here….
-Siding: While I’d love to do it all, I think budget and time constraints are going to make me leave the existing siding for the time being, and just plan other details (like the roof and windows) to allow easy integration of exterior continuous insulation and new siding at some future date when the vinyl siding is at the end of its life. I might go ahead and do the north wall now (where most of the new windows are going) — thinking tear off everything down to the sheathing, install air barrier, 4″ ish of mineral wool, rainscreen gap, wood siding.
-Interior walls: Where walls have been opened up, insulate all cavities and install something like Intello or Membrain.
-Basement: The basement is unfinished, but generally dry (with one exception corner). Leave it alone for the time being — as it’s basically compartmentalized, it can be insulated / sealed / finished later when we’re living here again.
-Budget: Squishy, but not huge. About $40k deep in this project already; a novice attempt to estimate the remaining work gets me to an additional $75k for the work I’ve outlined so far; this number is spousally approved. How the heck do people afford / justify DERs?? I’m going to be at 115K for an interior remodel and halfassed DER, and that’s without hiring any help!
-Systems: Currently 80% gas furnace, gas water heater, 30 year old AC. Put 4kW of solar on the garage roof last fall, future plan includes a pavillion structure with more solar. Would like to ditch gas entirely. Have a 2-ton ish water-source heat pump air handler sitting in my garage (industrial surplus stores are lovely). So, one option is to go ground-source heat pump — but I’d want to find someone that can do the field with directional boring. I have an acre lot but lots of trees, and trenching would likely do too much root damage. Might be very $$$. Alternately, considering mini-splits — or a combination with mini-splits upstairs for better zone control — but without doing a full DER including the walls and basement off the bat, the performance of the envelope probably won’t be high enough for that. Like the looks of the SanCO2 heat pump water heater system, but still doing research on those. Want to install an HRV, don’t know which one yet. Due to potential asbestos contamination, I’ll probably need to dismantle a lot of the ductwork for cleaning anyway, so might as well seal it well (and design it better) at the same time.
So, am I on the right track? Is it crazy to seal&insulate the roof to a high standard, and get some high performance windows, but leave other windows and walls to an unspecified future date? Thoughts or things I’m missing? Thanks!
GBA Detail Library
A collection of one thousand construction details organized by climate and house part
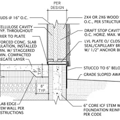
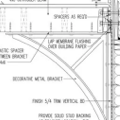
Replies
Firstly, remember that your own engineering license is only a PE exam away ;-)
Regarding DERs and economics, remember that many DERs are projects of passion, done for fun and educational value, or are done out of purely green motivations (a desire to use the absolute minimum possible amount of energy to keep the home comfy, for example). Economics aren't usually the primary driver. Taking any "insulated to code" home up to pretty good house standards is probably not going to pay for itself in energy savings alone, but you might decide the increased comfort was worth it so it's not entirely without value to do such a project.
Your plan to use exterior insulation on the roof is a good one. The other way to convert to an unvented attic is spray foam. If you're reroofing anyway, this is the time to look into exterior rigid foam and that's the route I'd take in your position. Be sure to consider reclaimed and B stock rigid foam here since you can usually save some money that way.
For windows, consider fiberglass and some of the Canadian manufacturers for more options. Many of the Canadian window manufacturers are putting out product similar to some of the fancy euro windows in terms of energy efficiency, but for better prices. I like Inline, but there are other options out there. Inline I know will custom build oddball size windows -- including very large ones (I had some very large Pella sliding glass doors I needed to replace, and Inline had no problem making them while Pella themselves said they couldn't without making 3 panel doors into 4 panel doors). Inline uses the usual Cardinal IGUs so the glass coatings will all be what you're used to.
You don't necassarily need an interior side vapor retarder, but it depends on the rest of the wall. I like exterior rigid foam, which, when thick enough, eliminates the need for an interior vapor retarder. It sounds like you're not able to reside right now, so you might need that vapor retarder if you're using something that doesn't have one like mineral wool. I personally like mineral wool batts for insulating walls, BTW, since it's an easy material to work with and it performs very well. I would do air tight drywall regardless of what else you do with the walls, since it's easy (just add a bead of sealant as you're hanging panels), and it can only help your wall's energy performance.
I would insulate your rim joist as a minimum since that's one of the low hanging fruit areas where you can usually get a pretty big gain for a relatively small investment in time and materials. Your next step would be to insulate the basement walls.
Directional boring is something I'm very familiar with since I do a lot of work in the utility industry and we use that technology all the time. While it can make turns underground, it can't make tight turns, so plan on a lot of straight shots when planning your field. The drill is going to rip up tree roots too, but probably not as bad as a trench dug by a backhoe would. The drill can go through large roots, or entire trees. To give you some perspective, my crews can drill into a precast concrete manhole with the directional drill rig and regular drill bit alone. It actually cuts a surprisingly clean hole in the concrete, but it chews up the bits so it's not the usual way to do things. Typical cost for a small (less than a mile or so) job will be $8-12 per foot for installation and material. Look for utility contractors to find a crew, or call the local engineering office for your telephone or cable TV company and ask if they can tell you some crews that they use. Most of these contractors don't really advertise because it's an all-insider word of mouth arrangement -- we all know each other so we don't need to advertise. You're not super far from me (I'm outside Detroit) in terms of telecom crew travel, so if you can't find any crews in your area post back here and I can recommend a few.
All that fun telecom industry contractor stuff aside, you'll probably find air source heat pumps to be more economical in terms of installation costs, even when factoring in operational efficiency of the system. Ground source heat pumps tend to just cost too much.
If you have any asbestos issues, or even think you might, don't do DIY abatement work -- contract that out. It's expensive work, but it uses some specialized equipment and it isn't worth the risk of doing it yourself. Once any asbestos issues are out of the way, go to town on that ductwork with a few tubs of mastic. Smear it on thick enough ("nickle thick" is the rule, many people put it on too thinly), and use the fiber reinforced type mastic for best results. I usually use some heavy rubber gloves to do this work, the "use a brush" technique has never worked for me.
It's not crazy to split the project up, many of us on GBA have done similar multi-stage DER projects with our own homes (myself included, and it's still ongoing). You do things as time and money allows. Try to do the easy stuff first, where the least time and money gets the most benefit. Rim joist areas are one of these places. If you have an oppurtunity to do DER stuff as a result of a seperate project (like needing a new roof), then that's the time to to do that work since you can combine too projects and save money. How far you go depends on what your goals are. Do you want to maximize energy efficiency? If you do, you'll be spending more money and not be focusing on economic returns of your "investment". If you want to get the best bang for your buck, you'll be optimizing things around energy cost savings and not maximizing the total R value, for example. If you want to "go green", maybe you want to shoot for Pretty Good House standards. It's not crazy to go as far as you want to go, just try to allocate your resources in such a way that you don't go so overboard on one thing that you would have had better overall benefit spending some of that money somewhere else. An R100 roof isn't very helpful when you only have R11 walls, for example. You want more of a balance.
Bill
Bill,
Thanks for the insight! Good to know that the roof plan at least seems reasonable, and I'll look into the Canadian window manufacturers you mentioned.
The directional boring stuff is good insight (one might say it's not boring at all!). Unfortunately, at that price point it may just make sense to go air-source heat pump as you suggest, and find a new home for my "effectively free" water-source unit (someone that has the space for dug trenches, or a pond for open-loop or something). Then again, thinking about it I do have a contact at an excavating company, and maybe he knows someone, I'll have to ask around. (I figured the boring would also damage roots, but only in the narrow bore rather than an entire excavated trench however deep plus the soil compaction of running a full size excavator around. Cool that they can punch thru concrete -- maybe they could start in the back of the yard and just punch straight into the basement wall!)
The asbestos thing is a whole unfortunate situation -- we (being my dad with a circular saw) tore out kitchen flooring early in the project, which I only recently learned was asbestos-containing. There's a little bit of the flooring left in one place, plus some asbestos ceiling finish in an area in the basement, plus whatever dust has been floating around the house in the 2 years that we've been living here.... not great. This is one of the main drivers of moving out for a bit, and I'll be hiring somebody to remove what's left, plus deep-cleaning everything else that was potentially contaminated. :(
I get that this type of project is unlikely to be justifiable on purely economic grounds (the solar panels are one thing where I can show a definite and reasonable payback period though). The rest is more a matter of "greenness" and performance on principal, as well as comfort. Just a bit stunned to actually run numbers on materials costs myself, when I see the scope of what some people on forums like this do, with much higher labor costs too.
Oh, and you're right, rim joists and basement walls do need to be considered -- I took some photos outside with a FLIR camera on a cold day last month, and that made the case for rim joist insulation quite handily! But, I figure basement work can be done more easily than living area work while we're living in the space.
Thanks again for taking the time to read my lengthy post!
>" Just a bit stunned to actually run numbers on materials costs myself, when I see the scope of what some people on forums like this do, with much higher labor costs too."
It's a bit of a labor of love with many on the forums. Myself, I like to be as efficient as I possibly can, and I like doing the work -- especially when I can actually measure results (reduced heatings costs, etc.). In my home office, where I'm writing this right now, my insulating and air sealing efforts resulted in the room being NOTICEABLY warmer and more comfy in the winter. It's a corner room, with a big bay window, and it used to always be one of the coldest rooms in the house. Since I spend a lot of time in that room, I appreciate the improvement in comfort that my insulating efforts made -- regardless of the cost (which wasn't really all that bad). That's one of the benefits beyond just savings in energy costs.
Try to find a good balance that works for you, just be sure to pick projects in order from biggest impact with least cost/effort towards lowest impact with highest cost/effort. Keep in mind your other projects too, so that you can coordinate things in a way to minimize overall costs and time invested. Exterior rigid foam is something you want to do around the time you replace the siding, for example, things like that.
Just try to always make "how can I better seal and/or insulate this" part of your thinking every time you do any renovation project and you'll come out ahead in the end.
Bill