Retrofit exterior foam wall assembly: Sanity check
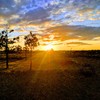
First a quick thank you to all that contribute and answer here. I have been reading GBA for some time and you all have helped and inspired me greatly.
I am located in Central Oregon, Zone 5. My existing house is about 30 years old, uninsulated slab on grade, 2×6 framing, OSB sheathing, perforated house wrap, fiberglass insulation, horrible air sealing, vinyl dual pane windows and a decked unfinished second floor/attic (so limited insulation depth and air sealing access.)
The building footprint is about 2200 SF with 1150 SF of living space, attached garage space and an unfinished full second story attic.
I plan to install Tyvek Drainwrap (Mind the Gap, Eh!), 3″ R-Tech Faced Type I EPS on the exterior, new windows and doors with innie details and a 3/4″ thick rain screen to attach the metal standing seam cladding along with LP or wood lap siding.
On the interior, I originally planned to flash and batt primarily for air sealing. Now I would like to install dense pack cellulose even though I have been unable to rent equipment or locate a contractor to do this in my area. Fiberglass, blown and batts seem to rule here. I may have to purchase equipment to do this which isn’t ideal but I feel comfortable performing the work.
My questions:
Does this sound like a reasonable wall assembly, are there more economical or effective ways to achieve a similar higher-performance envelope?
Given the situation, is cellulose worth the extra effort and cost over fiberglass? I favor the “green” value, gapless blown installation, fire and pest resistant properties, and near air barrier performance. However, batts would be cheap and easy to self perform.
Exterior foam, foil face in or out? I feel like the solar gain in winter is worth more than keeping it out in the summer. With this much insulation is it even going to matter?
The second story space is fully decked with 3/4″ T&G plywood except for about three feet that is open along most of the eaves. The decking makes air sealing the ceiling fixtures and wall top plates challenging as well as limiting insulation depth to the 2×12 floor joist depth. The open insulation along the eaves has accumulated much dirt and attracted mice over the years. I plan to replace the decking in these areas to protect the insulation and reduce air flow through the ceiling assembly. The eave vents are still open to the attic space. Any issues or opportunities I am missing here?
Is properly detailed Tyvek Drainwrap an adequate air barrier or should I “belt and suspenders” with taped foam or sheathing seams, airtight drywall, and/or spray foam flash the interior cavities? I considered a self-adhered membrane wrap, which would be much easier to install working solo, but went the drainwrap route for a cost-effective WRB and drying gap combo (Mind the Gap, Eh!) between the exterior foam and sheathing. I like things that serve multiple functions.
Are there other options or strategy to consider for slab insulation? The slab is uninsulated but with termites, existing damage in the house, I am very hesitant to install perimeter foundation insulation and create a hidden pathway into the house. Interior ceilings are already too low for my preferences at 8′ nominal so I wouldn’t want to change that much.
Thanks in advance!
GBA Detail Library
A collection of one thousand construction details organized by climate and house part
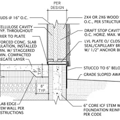
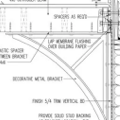
Replies
I can only speak to your desired self installation of dense pack cellulose because that is what I have experience with. It would truly be a shame if you had to purchase a blower for a one time installation. Most of the big box stores have a type of blower that is suitable for DIY dense pack. The big box store I rented from had a policy that if you bought the cellulose from them they allowed you to use their blower for up to a week free of charge. As long as you have a pickup and do some advance research it seems like you might be able to locate a store that has similar policies. It just takes some long distance telephone work and possibly some long distance driving to accomplish it. In my book the money saved would be well worth it and you will have a superior insulation job. Also, one really can't put a price on the satisfaction of doing a job most everyone considers impossible for a DIYer.
Just make sure you use the net method and make sure the blower has a way to dial back the cellulose to air ratio so the machine doesn't bog down. Many of the stores have a variety of machines, some of which do not have that ability and only are meant for loose blows in attics.
I can't speak to other aspects of the question. Hopefully others here can help.
Eric thank you for the encouragement. I have not looked closely into options in areas further away and probably have a few more locally to try before I can say I have fully exhausted my options. The next closest stores and rental centers are a couple hundreds miles round trip. I rarely see the little green blowers at my local big box stores and the ones I do see are usually tagged out for mechanical issues and look like they have been rode hard upside down and put away wet for a decade. My understanding is those machines will hit 3.2 lbs/ft^3 if setup properly and in good working condition. My ceiling is 11.5" deep and I think that depth requires min. 3.5lbs/ft^3 to reduce the chances of settling. I will keep after it until I find a good solution!
M.W.,
Q. "Does this sound like a reasonable wall assembly?"
A. Metal standing-seam cladding seems like a difficult siding choice. Make sure you have flashing details worked out for your window rough openings.
Q. "Is cellulose worth the extra effort and cost over fiberglass?"
A. Fiberglass batts, properly installed, will give you the R-value stated on the insulation packaging. The problem with fiberglass batts isn't really the material -- it's sloppy installation details. Be aware, however, that careful installation of fiberglass batts takes a lot of time. You'll also need a very robust air barrier. More information here: "Installing Fiberglass Right."
Q. "Exterior foam: foil face in or out?"
A. Most foil-faced foam has foil on both sides. If your brand of foil-faced EPS has foil on one side only, then the foil should face the direction with an air space. In your case, that means facing out, toward the rainscreen gap.
Q. "Is properly detailed Tyvek Drainwrap an adequate air barrier?"
A. No. Tape the foam, and verify airtightness with a blower-door test.
Q. "Are there other options or strategy to consider for slab insulation?"
A. Vertical insulation at the slab perimeter is definitely the way to go. Termite issues are very local, so I advise you to consult with an experienced pest consultant in your area. It's possible that exterior rigid foam will work, as long as you treat the soil.
> Exterior foam, foil face in or out?
There is no requirement for your sheathing to dry outward, but that doesn't mean it isn't beneficial. The ~1.7 perms you would get with unfaced EPS is worth something (eg, in the case of some bulk water wetting).
At 3" of Type-I EPS you have about R11.5 which has HUGE dew point margin over the code-minimum R7.5- setting it up to dry toward the interior would be fine. Installing foil faced EPS with the foil facer next to the rainscreen gap gives it another R1 in whole wall-performance (and even more dew point margin.) The solar gain through walls in winter is negligible- the solar gain is really all about windows, not insulated walls. The low-E facer reflects heat in summer, but also radiates far less heat out to the siding in winter when facing an air gap.
Key to getting performance out of batts is meticulously air-sealing the sheathing layer to the framing (and any seams in the sheathing with appropriate tapes), and fitting them carefully, as Martin suggests. That includes sculpting around electrical boxes and framing elements for a perfect fit, tucking in the corners and edges to guarantee there is no air gap where the framing meets the sheathing, splitting the batts around wiring & plumbing, then tugging them gently out to where the fiberglass is just proud of the stud edge plane for a compression fit when the wallboard goes up.
Make the sheathing the primary air barrier, but pay attention to air sealing details on both the foam and wallboard layers.
Standing seam does raise some challenges but they are similar to corrugated or other profiled metal cladding. Most solutions end in j-channel or similar.
Sold on the foil facing out towards the rainscreen gap. R-tech is faced with white on one side and shiny foil on the other side.
After reading feedback on the air barrier above, I fell back down the GBA rabbit hole.
https://www.greenbuildingadvisor.com/article/airtight-wall-and-roof-sheathing
https://www.greenbuildingadvisor.com/article/is-osb-airtight
Considering:
a) this is a retrofit and the sheathing is already full of nail holes from horizontal lap siding
b) my exterior insulation thickness allows an assembly with drying to the interior so a gap, aka Drainwrap, between the exterior foam and sheathing is not required
c) the combined expense and labor to tape sheathing seams and attempt to seal framing to the sheathing from interior stud cavities in addition to installing Tyvek Drainwrap may equal or exceed other methods, e.g. adhered membrane wrap
...it appears I might be better off moving to a self-adhered product like Delta Vent SA or similar to accomplish an all in one air barrier and water barrier to detail to.
Does it make more sense in this situation to use a membrane type self-adhered WRB?
Does it need to be a good quality vapor permeable product like Delta SA or considering the exterior foam and drying to the interior can I look to a more affordable product?
Should I still tape the foam if I am using an adhered membrane WRB at the sheathing?
With that said creating an air barrier in the ceiling assembly may be challenging since the ceiling joists are already decked with glued and nailed 3/4" T&G plywood.
Do I have to seal all the 2x12 floor joists to the underside of the T&G decking and tape seams from underneath to create an air barrier or apply some type of membrane seal on top of the decking? There is some dormer framing on top of the deck to work around as well and this is used as storage space so a membrane applied on top of the deck and then additional decking or other protection is less ideal.
Am I wasting money on high-performance membrane house wrap products that the rest of the envelope may not live up to?
I will also look more closely at blown in fiberglass. It seems more accessible locally from an equipment standpoint and solves some of the installation sensitive concerns with batts.
I am trying to get it "right" for the constraints of this situation without doing or spending more than I need to.