Severely below code insulation

Hello all, i just bought a 1920 cape in zone 4a that has absolutely no insulation anywhere. The top floor has the 2 bedrooms and a bath and all have pretty low ceilings. How does one go about insulating? The rafter are 2×4 and it has a few weird bumped out dormers. Due to ceiling height we can’t exactly bring anything down and of course the roof is only a year old so over roofing is kinda out, though it wouldn’t work due to the top floor windows anyway. What do i do? what are my options if any? thank you very much!
GBA Detail Library
A collection of one thousand construction details organized by climate and house part
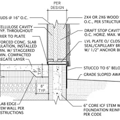
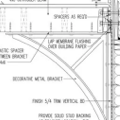
Replies
The first questions are what are your goals?
How long do you plan on keeping the home?
If you are going to be in the home for 20 years and you are going to remodel the home. It may make sense to do a deep energy retrofit.
If you will be selling in 2 years very few upgrades will save enough to pay for themselves.
Not everyone’s goals are financial. Some upgrades pay off in comfort and other will take a dollar loss to save the world.
I think once you understand your goals the first step would be an energy audit with a FLIR camera and a blower door.
Walta
Thank you for your advice. Realistically i plan on staying there as long as i can. i'm going to remodel the home for sure. I had an energy audit and they wont do a blower door test due to the age of the home. i also own a flir camera and have since swapped an exterior door and am changing 3 windows in the basement, and air sealed the other 2 doors, those are my low hanging fruit. Honestly comfort is more a priority than payback and resale value. it would be nice to live in a decent house.
Are you planning to re-side any time soon?
Is the framing full-dimension 2x4 or is it milled 1.5" x 3.5" lumber?
What sort of foundation (full basement, vented crawlspace, unvented crawlspace, other)?
No matter how you insulate, the first order if business it to make the place as air-tight as possible. Start with the big leaks, such as rim joist & foundation sill (which is usually bigger than all window & door crackage combined), flue & plumbing stack chases, balloon framing sans top plates, etc. When you're done with the bigger and more obvious stuff the FLIR and large window fan depressurizing the room/house can find the less 0bvious larger leaks more quickly, in much the same way that a blower-door can, albeit at lower pressure. It doesn't take anywhere near 50 pascals to find the bigger holes.
What is the wall construction material stackup between the interior paint and the exterior paint? (eg: horsehair plaster on lath, empty stud bays, shiplap sheathing, rosin paper, cedar clapboards.)
Any knob & tube wiring in those walls or cathedralized ceilings? Are there any kneewalled off micr0-attic spaces? Any soffit or ridge venting?
Is there any steam or hydronic heating system plumbing in exterior walls or ceilings?
Thank you Dana, i greatly appreciate your time.
i must reside and do windows soon. full dimensional 2x4 with 3/4 strapping on top then plywood for the roof.
The rim joist are already foam with closed cell. the plumbing and ventilation terminations were terrible as well.
full basement, unfinished.
Walls are vinyl siding, cedar shakes, 1x6 sheeting, 2x4s then horsehair plaster, empty stud bays. exactly how you described them.
cathedral ceilings on the second floor. the knob and tube is still in there but dead. no soffit or ridge vents. there are many knee walled micro attics.
steam system is all exterior walls as well as most of the domestic water piping.
>" must reside and do windows soon."
-------
>"Walls are vinyl siding, cedar shakes, 1x6 sheeting, 2x4s then horsehair plaster, empty stud bays."
------
>"the knob and tube is still in there but dead."
There's no tar-paper or anything between the cedar shake & 1x6 plank sheathing?
With an electrician signing off on it it's fine to leave dead knob & tube in the stud bays and blow them full of cellulose or 1.8lbs fiberglass, will be a HUGE improvement in overall air leakage & comfort levels. If the steam piping in the stud bays has asbestos insulation you may need to leave those stud bays alone. This can be done prior to re-siding, popping off some vinyl siding, drilling from the exterior, then re-installing the siding. There is usually far more surface area and higher stack effect infiltration drives in walls than in roofs/ceilings.
When re-siding, strip it down to the plank sheathing and use a fully adhered weather resistant barrier (eg Blueskin VP100 , DeltaVent SA, etc.) which will further tighten up the wall. There is probably enough depth to install 3/4-1" rigid foam board without having to buck out the window framing. With as little as 3/4" of foil faced polyiso a cellulose or fiberglass insulated full dimension 2x4 wall would meet/beat current IRC code minimums. With R5 or more on the exterior of air tight sheathing the potable plumbing is fairly well freeze protected in most zone 4A locations, even if there's 3" of cellulose between the plumbing an the plaster & lath. But for the record, got a ZIP code (for weather/climate data purposes)?
Are the foundation walls poured concrete, cinder block, quarried stone, rubble, fieldstone, or... ???
Are the micro-attics all accessible from the interior via hatches/doors? Fully air sealing the attic spaces from the outdoors can sometimes be a real PITA, but ultimately worth it. Air sealing at the kneewalls is usually a fools-errand (something I'm now convinced of, having played the starring role of "fool" in that movie a few times...)
>"full dimensional 2x4 with 3/4 strapping on top then plywood for the roof."
So you have 4.75" of depth to deal with. Is the strapping perpendicular to the rafters, or its it a rafter-edge extender?
If you're up for gutting the cathedralized ceilings, 2" of closed cell foam (preferably HFO blown goods) is more than adequate for dew point control on 2.75" of any fiber insulation filling the rest, and seals over any air leakage paths at the seams in the plywood. In zone 4A it only takes ~30% of the total-R to achieve dew point control at the foam/fiber boundary. With 2" of the lower performance climate damaging HFC blown 2lb foam (R12), and 2.75" of 1.8lbs fiberglass (~R12) it would have plenty of margin. At 2" closed cell foam runs between 0.5-1 perm, a Class-II vapor retarder which is sufficiently vapor open for seasonal drying of the roof deck toward the interior, yet not so vapor open that the roof deck loads up with moisture from the interior over the winter. Going for the full depth on the foam buys remarkably little in additional thermal performance- do the math:
https://www.finehomebuilding.com/membership/pdf/184243/021269086NRGnerd.pdf
A full cavity fill of close cell foam also comes close to fully blocking the drying path, and it comes at a substantial environmental (& financial) cost compared to fiberglass or cellulose- using the least amount necessary for dew point control is the greener way to go.:
https://materialspalette.org/wp-content/uploads/2018/08/CSMP-Insulation_090919-01.png
Taking it to the absolute minimum...
A mere inch of HFO blown closed cell foam would be ~R7, which would only be good enough for dew point control on R16 of fiber insulation. ( R7/ [R16+R7]= 30.4% ). At 3.75" 1.8lbs fiberglass is about R16, which is right up to that limit, with only some potential for moisture accumulation in the fiberglass over the winter if you're on the cold edge of zone 4A. At 3.75" cellulose would run ~R14, which would have at least some amount of margin, but would be right on the edge if it were an inch HFC blown foam ( R6/[R14 +R6]= 30% ). It's fine to take it to those limits if the ceilings are fairly air tight, and margin can be gained using something a bit more vapor tight than standard latex paint on the interior. Half-perm "vapor barrier latex" primer and air tight ceiling it would be tight enough, as would any of the broad sheet "smart" vapor retarders such as Intello Plus or Certainteed MemBrain.
Wow Dana, thank you very much!
I don't see any tar paper in the few spot that were exposed. its zip code 11516.
The windows need to be replaced as well, some are still original and rotten, the rest are terrible vinyl replacements that haven't worked in years. So With the self adhered wrb and 1 inch of foam does not seem so terrible, its alot of work but totally doable. though since i looked this up zip r starts to sound like a plan in the labor savings.
Cinder block foundation. and the strapping is perpendicular, so we have about 4.75 of depth.
I think gutting the ceilings are the way to go, they are in rough shape anyway, and to properly fix the plaster may be as much work as new drywall plus that would be an excellent opportunity to update the ancient wiring. Making the ceiling airtight doesn't seem to be so complicated as there will only by one center light and as i understand most decent drywall jobs are sufficient for air control.
Dumb question, that article is talking about walls, is it any different for the roofline? Would the perpendicular strapping and closed cell foam minimize the thermal bridging? what about just filling it up with open cell foam? it doesn't seem that we would hit code minimums in the ceiling/roof anyway? i'm sorry if i am completely misunderstanding this.
thank you so much for your time and knowledge!!