Floor Registers in Raised Floor Assembly

Should I Connect a Raised Interior Floor System to the Interior Room Environment Via Air Registers?
I’m designing a small cabin that’s being built 3 feet off the ground on piers. There are beams on top of the piers and 12.25” thick SIP panels on top of those. All the seams between the SIP floor panels fail over a beam. The exterior walls are built directly on top of the SIP panels and within the exterior walls there’s a raised floor (2×6’s with plywood subfloor on top and then finished flooring). The raised floor system is there so plumbing and electrical wiring can be run throughout the cabin without having to cut into the SIP panels.
Question: Should the space within the raised floor be connected to the interior airspace via metal floor grates so that warm air can circulate inside the raised floor cavity? My reasoning for saying “Yes” is to prevent the cavity from being cooler than the room above it, contributing to possible condensation within the cavity and eventual mold issues. Also if there are air registers, any condensation that does get into the raised floor cavity can get out.
On the other hand, connecting the raised floor cavity to the main space via air registers could increase the possibility of dust and dirt getting down there and causing issues (like you might get with really dirty HVAC ductwork) unless you added screened filters below the registers.
Any thoughts or practical experience with this issue?
GBA Detail Library
A collection of one thousand construction details organized by climate and house part
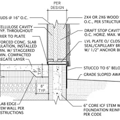
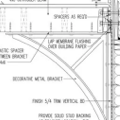
Replies
You don't need to ventilate that space. It should stay close to room temperature without ventilation.
Sounds like an interesting design. How does the plumbing get from the ground to the interior without freezing?
DC: Ah, for that I looked to the far north and read some articles from the Alaska Cold Climate Housing Research Center. I figured if anyone knew how to keep pipes from freezing it's them.
http://cchrc.org/
Basically, the standard options are an insulated pipe chase between the ground and the underside of the floor system but unless you either connect the pipe chase to the building's interior so warm air can circulate through it or add electric pipe tape the interior of the chase can still get cold enough to freeze water.
Instead of the chase, I reasoned that since water pipes from the well and waste pipes to the septic field had to eventually go underground, why not bring them up into a utility shed that sits on the ground (on a concrete slab) and then run the pipes through an attached side wall and under the raised floor? The utility shed is fully insulated and has a small direct vent propane heater that is set to come on when the temp drops below 40 degrees inside. The pipes are never exposed to the outdoor air temperatures, and the shed also gives me a space to put water purification and storage equipment as well as any other HVAC equipment.
rockies63,
Don't the lines still need heat and insulation below the slab until you hit the frost line, or is the utility shed slab detailed as a FPSF?
This puts me in mind of a cool detail the folks at South Mountain Company did on a house in Massachusetts. Matt Coffey explains it this way: "To get water into the house, we wanted to maintain above-freezing temperatures in the water supply line without electric resistance heat tape, so we decided to build a custom conduit. The town-supplied water comes up from 4 ft. below grade, and right where it turns to enter the building, we built a custom-insulated double-wall PVC conduit. The ground temperature and the ambient indoor-air temperature thermally regulate the conduit, which is essentially borrowing 55°F from the ground plus warmth from inside the house." You can see an illustration here.
Kiley,
I finally got a chance to use that utility chase on a small recording studio this summer. I also used their floor system, with 2"x4" joists below the main ones. Both details worked great.
The slab has insulation extending beyond the sides and foam underneath, similar to this.
http://www.legalett.ca/floating-slab-forms-garage-shed-outbuildings-geo-pad-footing-foundation-eps-foam.html
rockies63,
You look all set.
Malcolm, can you go into a bit more detail on the chase you built? Did you seal the bottom or the top in any way? From the drawing in the article it appears they used some kind of a PVC cap on the bottom with a smaller collar that fits around the pipes. Did you have to use any sealant at the bottom to prevent water wicking up into the insulation foam (and how did you fill the space between the inner and outer pipes)?
rockies63,
We are lucky here as the frost depth is around 12", so the stakes are a lot lower than most places.
The lower 2"x4" framing of the recording studio starts 6" above finished grade, so the chase penetrates the 1 1/2" rigid insulation at about the 10" mark. I used a leftover piece of 8" galvanized culvert, and ran a 3" piece of PVC sewer pipe through the center. I wedged pieces of foam board around the smaller pipe to keep it centered before filling the space in between with canned foam.
Where it enters the upper (2"x8") joist space I bent down four tabs on the culvert and screwed it to the lower sub-floor. The top is covered by the continuous layer of 1 1/2" foam, except for the 3" inner-pipe. I left the bottom open. I can't see it being any more of a problem if it gets wet than the other exterior insulation used on foundations.
If I was using a similar detail in a colder climate, I would increase the diameter of the inner pipe and leave the top open to the heated space above.