Squeaking, creaking, crunching foam
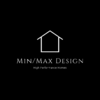
Just built a 1500 sqft home with a full basement in northern Michigan, climate zone 6A. Took the ‘exulation’ approach with guidance from here and Building Science Corp. The house gets rather squeaky and creaky. Most noticeable during sunny days, large temperature swings, and/or seasonal changes. For example this past week temperatures were bouncing between the 30’s and 60’s. However, it will likely continue throughout the summer into fall if it’s like last year.
I am thinking it’s the foam, because when I installed it last spring I remember it got pretty squeaky/creaky particularly after being in direct sunlight- really points to thermal expansion. At first the foam had a few fasteners, basically one in each corner, but then it was fully secured with 2 x 4 furring strips- didn’t seem to stop the squeakiness though. I figured once the cladding was installed, there would be no direct sunlight to provide wild temperature swings and associated thermal expansion.
The wall assembly from outside to inside:
-12″ LP Smartside (wood fiber not the osb stuff) painted dark blue
-2 x 4 furring strips providing 1.5″ rainscreen. Secured with 10″ timberlok screws 2′ OC into the wall studs.
-Taped 2″ XPS providing drainage plane initially secured with 6″ spike and washers at each corner. Seams staggered with previous layer.
-Untaped 2″ foil faced polyiso (factory seconds) secured with 4″ screws and washer at each corner. Seams staggered with previous layer.
-Untaped 1″ foil faced polyiso (factory seconds)secured with 2″ screw and washer was each corner. Seams staggered with previous layer.
-When temporarily securing the foam I specifically avoided studs so the furring strips would lay flat. Went around the inside with the great stuff foam gun and sealed all the screws/nails poking through the osb. I figured the 2 x 4 compressing the foam and each 10″ screw passing through the foam would secure it.
-7/16″ OSB. All seams taped or otherwise sealed.
– 2 x 6″ advanced framing exterior walls. Single top plates, 24″ OC. Designed and built myself so not a big deal to line up floor joist, wall studs, ceiling joist, knee wall studs, and roof trusses.
-R-11 insulation in the stud cavities (keeps at least 2/3 R-value on exterior of sheathing)
There are ceiling joists with an OSB attic floor (all seams taped) in order to keep the ceiling joist cavity within the air barrier/envelope. Additionally, no machinery was used to lift and position trusses so the attic floor was quite helpful in this regard. 22″ ‘knee’ wall with standard trusses installed on top to provide plenty of room for cellulose insulation. Exterior insulation extends from sill pate to bottom of trusses (top of the ‘knee’ wall). I believe this approach went a long way toward airtightness (0.53 ACH50).
Another important detail- the inspector wanted blocking at the top of each rainscreen cavity which would prevent venting of each cavity. (Is it still debatable over whether this needs to be open at the top and bottom?). The house has a head band and belly band of 5/4″ x 12″ trim. Each cavity is open at the bottom, however at the bottom of the headband I cut a wide and deep rabbet so the last piece of siding would tuck into it. At the top of the top row of siding I installed corrugated plastic sign board that had a bunch of channels in it. This effectively provided a vent at the top of each furring cavity, at least to some extent, and it was completely out of sight.
One more detail. Never really notice noise coming from the east side of the house. The east side is mostly shaded. Definitely notice it from the south and west side. West is completely unshaded and south is partially shaded by the detached garage, but not so much in the spring, summer, fall. The north side will get some semi direct sun in the summer but that’s during sunsets (the sun is to the northwest, but more west than north). I don’t really remember noise coming from the north side.
I did a deep energy retrofit on a different house a while ago with a very similar “exulation” approach. Key differences:
-5″ of fiber faced polyiso (I think it’s usually used for commercial roofs) was used instead of a mix of XPS and polyiso. (2) 2″ layers and (1) 1″ layer.
-House was balloon framed and studs were 16″ OC
-3/4″ furring strips used on top of the insulation and channels were open to the roof framing
-Painted cedar/wood siding (medium green) instead of smart side
-Housewrap was installed over the insulation.
-No interior insulation, but I don’t think that’s relevant here.
There were no squeaking, creaking, or crunching.
So with that novel on the background info:
-Has anybody else experienced this?
-Any suggestions on preventing this? Go to 16″ OC framing?
-Polyiso expanding at different rate than XPS…or maybe XPS has a relatively large thermal expansion rate?
-Radiative coupling between siding (dark blue increasing the impact to some extent) and XPS? I would like to think the 1.5″ channel and venting would go a long way toward counteracting this.
-Expansion of smartsiding effectively causing 2 x 4 furring to slide on XPS?
-XPS is just loud when it comes to sliding/shifting? No matter what, there’s always going to be some contraction/expansion and XPS is just loud?
-Don’t use XPS and use foil faced polyiso to prevent any radiative coupling?
-I guess another way of looking at it, is where is the relative motion? The furring and the XPS, the XPS and polyiso? I am hesitant to believe it would be the two polyiso layers against each other or against the sheathing.
I used a mix of polyiso and XPS because of what I read about polyiso r-value dropping off with cooler temperatures. However a bigger question is, which brands does this apply to and is it really worth any attention with thick layers of exulation? Thinking about the diminishing return curve…
You can see a photo of the house at the website below. The front door faces west.
https://www.minmaxdesignllc.com/ultra-efficient-ranch
GBA Detail Library
A collection of one thousand construction details organized by climate and house part
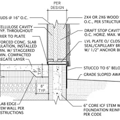
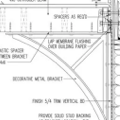
Replies
MD,
Sorry I don't have any useful isights into your main questions. A comment on the blocking in cavities though: Most codes preclude connecting uninsulated concealed spaces to stop the spread of fires. Our expressly prohibits venting the rain-screen gap into the roof space above. That doesn't mean you can't vent the cavity to the outside, you just need to do it so that the openings are 0n the face of the walls, not the top.
My guess is different rates of expansion for the two different types of rigid foam so you’re getting some sliding and fastener migration during temperature changes. The two types of rigid foam sliding against each other will give you the squeaking, and I’d guess the XPS is the one actually making the sound. The crunching is probably occurring as whichever type of rigid foam expands the most or the fastest pushes the fasteners sideways through the other type of rigid foam.
I’m not sure what can be done to prevent the sound. The only thing that comes to mind is to put a layer of housewrap between dissimilar layers of rigid foam to provide a sort of linear bearing to limit the squeaking as the two materials slide past each other.
Bill