Still confused by plethora of information on insulation

I’m in North Dallas, zone 3, and here’s what I have so far (in progress pics attached).
2×6 framing for walls and 2×8 ceiling joists. Everything is 24” OC. It’s a skillion roof and I’ll route plumbing vents through the walls to avoid any penetrations through the roof. I have it decked with ½” OSB.
I am planning on 2 alternating, taped layers of 1” XPS on the roof deck (total of R-10). This would be covered by a layer of the high temp Grace Ice and Water Protection peel and stick. I will run 1×4 purlins on top of this for a standing seam metal roof. The only venting I have planned is from the 1×4 purlins – unless you recommend something else?
In zone 3 I’m supposed to have a min of R-38 in the roof assembly, but not sure how I’m going to get there without using more foam above (would prefer not to do this), or having a layer of closed cell foam underneath.
So here are my questions:
1. Should I install the WIP directly to the OSB deck and install foam above this? Or, I assumed the WIP would have to go above the foam to provide a cohesive seal across the above deck assembly and allow me to wrap to the fascia. Is this the right order?
2. Is the WIP even needed if I have 2 layers of XPS?
3. I’m confused by the guidance from GBA on the application of (spray) open cell vs closed cell under roof decking. My understanding is open cell has the potential of allowing the roof decking to absorb moisture from inside and cause a potential failure, so vapor barrier paint needs to be used. An expensive alternative would be to use closed cell spray foam, but not if there is above deck foam board insulation, since the decking has no way to vent if sandwiched between 2 layers of closed foam. What do you recommend?
4. For the exterior walls I’m planning to have ½” OSB sheathing (seams taped), 1” XPS foam boards, Tyvek wrap (seams taped), and 1×4 purlins for metal siding. I plan on having ‘outie’ windows, so keeping the wrap at the outer layer. Inside I’d like to use closed cell spray foam too, but have the same concerns as the roof. What do you recommend?
I appreciate any guidance you can provide. Love the GBA site – It’s like drinking from a firehose.
GBA Detail Library
A collection of one thousand construction details organized by climate and house part
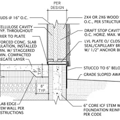
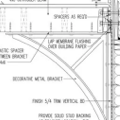
Replies
Andrew. I think this article will help to clarify things. It details how you can combine rigid foam with air permeable insulation. https://www.greenbuildingadvisor.com/articles/dept/musings/combining-exterior-rigid-foam-fluffy-insulation
I'm not sure the Grace membrane is necessary, but let's see what other members think.
Thanks for the article link Steve. I've read it before and it provided guidance for the direction I'm headed now. I'm still not completely clear on the potential for interior open cell against roof sheathing creating a moisture issue. Martin has referenced this potential problem in several articles on the GBA site, although it may be a moot point since I'm in zone 3.
I would be wary of using open-celled foam and of sandwiching the sheathing between two impermeable layers of closed-cell foam. I would install cellulose directly against the underside of the sheathing to achieve the balance of the required R-value. (You might need to go a little thicker on the exterior foam to actually hit R-38 if using 8-inch (nominal) joists, however.)
Regarding moisture issues, there are three basic approaches (with a bunch of caveats):
1. Have a thick enough layer of exterior insulation for your climate zone such that moisture never condenses inside your envelope.
2. Use vapor retarders in the correct places, such that moisture never reaches a cold surface to condense on.
3. Have a ventilated assembly (roofs only, e.g. attic with soffit and ridge vents and piles of cellulose).
Using closed cell spray-foam on the inside of an assembly is sort of a combination of (1) and (2). You can use the guidelines for how much exterior foam to use to determine how much ccSPF to use. Using ccSPF on the interior is usually instead of using exterior foam, not in addition to it. Generally it's best for renovation projects where exterior insulation is not practical, as closed-cell spray-foam is expensive and generally uses blowing agents with a high global warming potential.
If I'm understanding correctly, you should be pretty well set up to rely on option (1) for your moisture control.
For climate zone 3, the article that Steve linked indicates that your roof needs a minimum of R-5 above the sheathing to prevent moisture issues. You're planning to have 2" of XPS which is more than adequate.
2" of any rigid insulation (XPS, EPS, polyiso, mineral wool, etc.) will give you sufficient R-value above your roof sheathing. Once you have the sufficient R-value outside of the sheathing, you want to use a vapor-permeable insulation in the joist cavities (cellulose, fiberglass, mineral wool, etc.). Open-cell spray foam is also vapor permeable, but there doesn't seem to be any reason to use it here over a cheaper insulation like cellulose or fiberglass.
For your walls, 1" of exterior insulation is also more than enough for your climate zone, so you should be in the clear to use cellulose, fiberglass or mineral wool in your wall cavities as well.
You don't need to use closed-cell spray foam anywhere in your project, so it's probably best to avoid it for environmental/cost reasons. On a similar note, XPS is not so great on the blowing agent front, so EPS, polyiso, or mineral wool are better choices if you're using new insulation. If you are using recycled insulation, any kind is good.
Regarding hitting R-38 in your roof, mineral wool batts for 2x8s are R-30, so any type of exterior insulation that gets you more than R-8 will get you to R-38.
Does that help clarify things a little bit?
Brendan - clarifies quite a bit. Thank you!
In zone 3 as little as R5 (~1" of closed cell foam) on the underside of the roof deck OR R5 rigid foam provides sufficient dew point control for up to R38 total-R to allow latex paint on ceiling gypsum board to be the vapor retarder, per chapter 8 of the IRC. See Table 806.5 INSULATION FOR CONDENSATION CONTROL (near the bottom of the page):
http://codes.iccsafe.org/app/book/content/2015-I-Codes/2015%20IRC%20HTML/Chapter%208.html
At 1" closed cell foam is NOT a vapor barrier, it's about 1-perm, give or take (depending on manufacturer and installer) , the border of class-II and class-III vapor retardency, and even 2" would still have adequate drying capacity toward the interior.
With R5 or more above the roof deck you don't even need the 1" shot of closed cell to fill it up tight to the deck with cellulose or fiberglass below.
Using 2" XPS above the roof deck is more than enough, but a couple of things about XPS already covered somewhat by others:
1: It is blown with HFC blowing agents, which have a hefty greenhouse gas hit
2: In the next few decades as it loses the HFCs it's R5/inch performance drops to that of EPS, or about R4.2/inch.
EPS is blown with comparatively benign pentane, most of which is recaptured at the factory, and does not play a part in it's insulation performance, which is stable over decades. It's cheaper per labeled-R too. Polyisocynurate foam is also blown with pentane, and has a higher R/inch than EPS, but a similar cost per R. As little as 1.5" of EPS or 1" of polyisocyanurate would be sufficient for dew point control at the roof deck without interior vapor retarders, but if you wanted to set it up as two layers of 3/4" that would be just fine.
The Grace Ice & Water goes directly on the roof deck, not the foam and is sufficient to air seal the roof deck without interior side foam.
On the walls you don't need any interior side vapor retarders, but see the comments about the value proposition and environmental aspects of XPS v.s. other rigid board.
Half pound density open cell foam uses half the polymer per R of closed cell foam, 1/3 the polymer per R of EPS, and is blown with water. In many markets open cell foam is cheaper than dense packed or damp-sprayed cellulose. With all spray foams getting the mixture a bit off during installation can result in long term outgassing problems. Half pound foam needs to be installed in lifts of no more than 5.5-6" (R18-R22) per pass, with a cooling period between passes. This is both an immediate term fire hazard issue, as well as an installation quality issue. MANY installers will want to go ahead and fill a 2x8 rafter bay (7.25") in one pass to save time, and they'll usually get away with it, but it's more likely to have shrinkage gaps along the rafters when they do, assuming it doesn't catch fire and burn the place down as it cures. (This is more likely to happen with 2x12 rafters done in one shot than 2x8s.) It can be a good option, and can even be cost-competitive, but understand the risks ahead of time, and discuss it with the installers.
Andrew,
You've gotten good advice.
I'm not sure what W.I.P. means. I tried to look it up, but just came up with "work in progress."
I agree with Dana and others that you don't want to put Grace Ice & Water Shield above the rigid foam. If it belongs anywhere, it belongs on the exterior side of your OSB roof sheathing, where it will perform as an air barrier and emergency roofing in case your building gets hit by a tornado.
It's good to have an excellent air barrier at this location, and the peel-and-stick will work, although there are cheaper options (taping the OSB seams with a high-quality tape like Siga Wigluv or Zip System tape, for instance, or synthetic roofing underlayment with taped seams).
If your rafters aren't deep enough to hold enough fluffy insulation to meet your R-value goals, the usual solution is to deepen your rafter bays with strapping or some type of fur-down. (Better yet: you should have figured out your insulation details before the framing was up. For more on this topic, see Plan Ahead For Insulation.)
Some types of standing-seam metal roofing can be installed over purlins, but not all types can. Some types of standing-seam roofing require a solid roof deck like plywood or OSB. Talk to your roofer.
Finally, if you take our advice and either move the Ice & Water Shield to a new location (directly above the OSB) or if you choose a less expensive way to create an air barrier at the OSB layer, remember that building codes still require the installation of some type of roofing underlayment under your metal roofing. Either asphalt felt or synthetic roofing underlayment will work.
Note that R38 is the code-min if all the insulation is between thermally bridging rafters or joists. If you have 2" of foam on the exterior it cuts the thermal bridging of 2x8 rafters by about half. Compliance on a U-factor basis only requires only U0.030, or R33 "whole-assembly", the thermal bridging and the thermal value of the ceiling gypsum, roof deck, air films etc all factored in. So
assuming 2" EPS @ R4.2/inch you have R8.4 of foam
the OSB & gypsum add up to about R1, bringing it up to R9.4
the interior & exterior air films add up to a bit over R1 so you're at about R10.5.
The average R-value of the fluff or open cell foam between the rafters then only has to be R22.5. At a typical 7% roof framing fraction R27 fluff makes it, and even an 8% framing fraction (barely) makes it. But you used 2" of fiber faced roofing polyiso (R11-ish) or 2" foil faced polyiso (R12) instead of EPS it would make it even at a 15% framing fraction.
You don't have to go fatter on the foam to meet code, but using polyiso would buy you a bit of margin, and make it easy to convince the inspectors (R27 cavity fill + R11 foam = R38 nominal at center cavity between the rafters.)
If you used foil faced polyiso the foil facer adds another ~R1 to the assembly as long as you have at least 1x purlins.
From a structural capacity point of view you may need to use 2x purlins in order to have sufficient fastener retention for the metal roof, which is fine.
A thermal weakness of this type of roof is thermal bridging of the rafters where they extend beyond the exterior walls. That can be mitigated by extending the roof insulation out 18-24" beyond the exterior wall.
FYI, here in DFW, our ZE homes with metal roofs have the following assembly: 1/2" taped Plwd/OSB sheathing, 1.5" Polyiso (to match the 2x4 perimeter nailer) and Ice&Shield on top of the polyiso to protect it, and then 1x4s to attach metal roof. Under the roof decking we install 7.5" min open cell foam. Total R38 min.
Just in case, our wall assemblies are 2x6, 1/2" taped Plwd/OSB sheathing, 1" R5 min. rigid foam, taped with approved tape for moisture barrier, rain screen and cladding. Inside we have dense packed cellulose at 4lb/ft³. Total R25 min.
We get HERS40s with these assemblies.
Armando. Just out of curiosity, why are you using the Grace membrane to protect the foam?
Thanks all. Great info.
Martin - Water and Ice Protection (WIP). Have seen it referenced this way in several places.
D Dorsett - Very enlightening info. I've changed the above deck insulation to 2" of polyiso boards.
Armando - Thanks for the local DFW insight. Matches what I'm was thinking.
The I&S not only protects the foam from elements from the time its installed till the time roofers come to install the metal roof, as they are different crews and could be delayed by scheduling or weather, and from all the walking on top of the foam. In addition, the membrane wraps around the 2x4 perimeter nailer and down the side in front of the fascia board to provide assembly with a water tight wrap, like a latex glove.