Summertime condensation

We Built A addition for a customer approx 10 years ago, It is just one big room 30×30 with a hip roof and cathedral ceiling about a year ago it started leaking in hot weather, apparently from condensation. It does not leak from rain and it does not leak in the winter. If we circulate the air in the room with fans it reduces the condensation.It leaks primarily on the east side where it gets more exterior heat from the sun. The construction is 10in ceiling joist, osb deck with asphalt shingles,10 in fiberglass dense pack, un-vented, vapor barrier, wood ceiling. There is also a heavy metal bracket at the peak to attach the 4 hips together. There is also can lights. The moisture seams to come down the cavity in one path then where the ceiling meets the wall it runs down the wall. Please help Thanks
GBA Detail Library
A collection of one thousand construction details organized by climate and house part
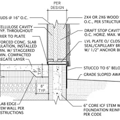
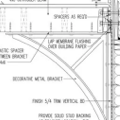
Replies
Hi user-7582894 (It would be great to get your real name).
There are a few things that could be going on here. The first thing that comes to mind is if you are running air conditioning and have an interior plastic vapor barrier, you may be creating a cool condensing surface. Also, unvented cathedral ceilings with fibrous insulation are not a great idea. You may need to remove that vapor barrier and insulate the ceiling in a more effective way. This article may be a good starting place for you: How to Build an Insulated Cathedral Ceiling.
And by the way, it will be helpful for other members who may have some insights to know where your house is located.
Brian- please shoot me an email (at the gmail address.)
My email is [email protected]
Name is Glen
>"The construction is 10in ceiling joist, osb deck with asphalt shingles,10 in fiberglass dense pack, un-vented, vapor barrier, wood ceiling. "
An unvented cathedralized ceiling with an interior side vapor barrier and air-permeable fiberglass insulation in the cavity is a moisture trap, and a code violation.
A layup of asphalt shingles & #30 felt is pretty close to 0.1 perms, which is the boundary definition of "vapor barrier". Moisture that gets in has no way to leave quickly- it can't really dry to the exterior via vapor diffusion, while gravity and capillary action are working against you, pulling moisture in. The roof deck is probably close to saturated with moisture from dew & rain wetting wicking in on nail penetrations. When the sun heats it up, the entrained air in the fiberglass takes up that moisture until it's dew point reaches the temperature of the cooler ceiling/interior vapor barrier alone.
There may also be wintertime moisture accumulation building up in the roof deck from air leaks (highly likely, with can lights.)
Potential fixes for this are highly climate dependent. Where is this house located?
Does "wood ceiling" refer to t & g planking, or something else?
Would the customer be OK with replacing the can lights with thin surface-mount LED fixtures (which are MUCH easier to air seal).
Thanks for the info, Located in central wi. Yes T&G Planking. I am concerned about this system it is what our insulation contractor recommended at the time. However we solve this problem would need to be done from the exterior. I think the customer would be ok with the surface mount LED lights. I have considered stripping the shingles and installing ventilation on top of the roof deck? Thanks Glen
Glen,
Adequately venting a hip roof is very difficult, as the ventilation for most of the area doesn't reach the ridge.
>"Located in central wi. Yes T&G Planking. I am concerned about this system it is what our insulation contractor recommended at the time."
Your contractor was/is an ignoramus. Unvented roofs in IECC climate zone 6 (=central WI) with all of the insulation on the underside of the roof deck requires more than 50% of the total-R be air-impermeable vapor retardent insulation well bonded to the underside of the roof deck. With a 10" I-joist type rafter that could be 4" of closed cell spray polyurethane (= ~R24 if HFC blown goods, ~R28 if HFO blown goods), and 6" of dense packed fiberglass (R24 - R25). If it's a 2x10 (9.25" deep) it'll still take at least 3.5" of closed cell foam. (R23-R24) and 5.75" of dense packed fiberglass (R22-R24.) What was built is a code violation, and almost guaranteed to fail eventually, since the interior side air barrier (6 mil polyethyene) isn't very reliable over the long term- it remains a vapor barrier, but would almost certainly become more air-leaky over time with a t & g ceiling. (A layer of sheet rock behind the t & g would be a better air barrier.)
>". However we solve this problem would need to be done from the exterior. I think the customer would be ok with the surface mount LED lights. I have considered stripping the shingles and installing ventilation on top of the roof deck?"
To have adequate dew point control at the roof deck with 10" of dense pack fiberglass (R48-R50) it takes a about R50 above the roof deck, which would be pretty expensive. But with the interior side vapor barrier it doesn't necessarily need it. Venting ABOVE the roof deck doesn't really cut it in your climate zone, since the OSB roof deck is a Class-II vapor retarder (almost a vapor barrier), blocking moisture from passing through quickly, but if the interior side vapor barrier is made truly air-tight it can work (or at least work better than it is right now), as long as the weather resistant barrier on the structural roof deck is something semi-permeable to water vapor.
Segmented 2x4 furring (2' sections with 1' gaps) through-screwed to the rafters with timber screws to create 1.5" deep vent channel, and a would allow cross ventilation under the nailer deck. The segmentation there would provide reasonable cross ventilation to make up for the inadequacy of the ridge ventilation.
The 10,001 nail holes trough the vapor barrier from the t & g ceiling is still a concern, but the bigger air leaks through the vapor barrier are the can-lights. It'll be a PITA to air seal those penetrations and air tight electrical boxes for the surface mount fixtures to the vapor barrier, but it really has to be made robustly air tight if only venting above the roof deck.
Dana, or others,
Would there be any sense in what I will call the half-baked approach, where one uses either rockwool or woodfiber insulation (vapor permeable) above the roof deck, but not to the prescriptive R-value for dewpoint control? (like maybe one, 2-inch layer? Vent above as described above. Vapor permeable underlayment of course.
My reasoning:
1) avoid the cost and crazy thickness of adding R-50 foam
2) if taking roofing off anyways, the timing is right
3) maintain vapor openness to the exterior (somewhat, though it wouldn't be super high with the OSB I guess).
4) cover rafters/trusses for thermal bridging reduction and possibly reduced condensation issues.
5) an added water shedding layer to further protect roof deck
6) a statistical reduction in wetting time of the sheathing (in other words, it's not 'fully adequate' dew-point control, but is improved compared to without)
Would still really rely on an air-tight interior in this case, and the interior vapor barrier would not be of issue.
I've have done over roof with similar setup as you are describing.
Peel and stick air/vapor barrier over the existing roof deck.
Purlins at 90 deg screwed to existing rafters.
Batts between purlins with synthetic underlayment on top.
Standing seam metal roof over it.
It works, relatively easy to do and the because the purlins are perpendicular to the rafters, it gives you almost as good of a thermal break as rigid insulation for much less money. It is harder to walk on though.
With any over roof, usually the fussy detail is re-doing the fascia. If you are adding a lot of insulation, you have to find a way to hide the extra height otherwise it doesn't look right on gabled/hip roofs.
User-7582894,
GBA has published a relevant article on this type of problem. Here is a link: "Summertime Condensation Near the Peak of a Cathedral Ceiling."
I have read that article.
As a bandaid you could try installing a diffusion vent. Take a look at:
https://www.buildingscience.com/documents/insights/bsi-088-venting-vapor
You can run the diffusion vent down the hips, see Fig 7. The 12" opening they show is unsightly, but something closer to the size of a standard ridge vent can move a fair bit of vapour.
If that doesn't work re-roof with enough exterior rigid insulation for condensation control in your climate:
https://www.buildingscience.com/documents/building-science-insights/bsi-100-hybrid-assemblies
You should also check the A/C vents. if they are directed towards the ceiling, they will chill it enough to cause the condensation. Redirecting the vents can change the ceiling temperature enough to stop the condensation.
Central WI is a tough climate. Very hot/humid in summer and very cold in winter. The best location for a vapor barrier is right in the middle of the thermal envelope. One fix would be to install a peel&stick vapor-proof membrane like ice& water shield over the sheathing, then rigid foam on top. In climate zone 6, you need almost as much R-value on top of the vapor barrier as below it. Your 10" of fiberglass loosely placed probably gives you R-35 or so. This means you need at least 5" of roofing polyiso on top. That's a thick sandwich, but it will be a very efficient roof and it won't drip in hot or cold weather. You might get away without the vapor barrier membrane by taping the seams in the sheathing and staggering the joints in the foam, but I prefer the waterproofing performance of the ice&water shield to protect against the inevitable roof leaks.
This still doesn't fix the fact that you've got a plastic sheet where it doesn't belong, but it won't cause as much trouble once you add insulation to the outside.
I'd overlay with permeable underlayment and a vent . Something like "Cobra Hip Vent" makes high/low vents possible.
Short-term, you would try slightly pressurizing the house (reducing infiltration of moist air).
>"built...approx 10 years ago... about a year ago it started leaking in hot weather, apparently from condensation."
Any idea what changed a year ago?
Was the interior poly detailed as an air barrier at all? That a fan minimizes the problem seems to suggest interior air-leaks.
As a crazy person who is addressing cathedral short comings from the inside, I say it is actually better to do from the inside. I am making baffles full length with 1/2" plywood, with caulking for air sealing, then using sls 2x4 perpendicular to straighten out the waves of the rafters, BIBS, then drywall with 6 mil poly under it. No holes except for limited numbers of 4 inch ceiling boxes that will be as air sealed as possible. Crazy, maybe, but I won't be adding 6+ inches above my roof, zone 7.
I agree that it's normally better to do it (either vented or unvented) from the interior side, but that's a lot cheaper to do as a retrofit if the ceiling is sheet rock rather than clear grained t & g.
With a hipped roof even vented cathedral ceilings have some risk due to the limited ridge/hip vent area & air flow, making it better to go with 4-5" of foam board above the roof deck, and 5-6" of fluff or half-pound open cell foam on the under side of the roof deck.
If scrapping the t & g and starting over with the insulation is an option, 4" of closed cell foam on the underside of the roof deck with 5.25" of rock wool batts (labeled R23, performs at R22 when compressed to 5.25") works pretty well in milled 2x10 framing in zone 6. Install a layer of gypsum board paying attention to air sealing details and give it a coat of "vapor barrier latex" prior to installing the decorative t & g.
At 4" the closed cell foam is even structural, but it comes with a substantial greenhouse gas footprint. The cheaper stuff at about a buck per square foot per inch of depth (budget $4 per square foot for 4") is blown with HFC245fa which runs about 1000 x CO2 @ 100 years. The pricier slightly higher R/inch stuff is blown with HFO1234ze, which is less than 5 x CO2 @ 100 years. But any closed cell foam has a substantial footprint from the polymer itself, due to the high polymer per R at 2lbs density. Even though the blowing agent's footprint of the HFO is less than 1% of the HFC, it only knocks about 1/3 off the total greenhouse gas footprint of the insulation per R. See:
https://materialspalette.org/wp-content/uploads/2018/08/CSMP-Insulation_090919-01.png
I agree that it's normally better to do it (either vented or unvented) from the interior side, but that's a lot cheaper to do as a retrofit if the ceiling is sheet rock rather than clear grained t & g.
With a hipped roof even vented cathedral ceilings have some risk due to the limited ridge/hip vent area & air flow, making it better to go with 4-5" of foam board above the roof deck, and 5-6" of fluff or half-pound open cell foam on the under side of the roof deck, or 2 x 12 rafters with the requisite ratios of closed cell foam/fluff all under the roof deck. Foam board above the roof deck is cheaper than sprayed closed cell foam if it's a simple gabled roof, but can be more expensive for roofs full of hips & valleys & dormers, etc.
If scrapping the t & g and starting over with the insulation is an option, 4" of closed cell foam on the underside of the roof deck with 5.25" of rock wool batts (labeled R23, performs at R22 when compressed to 5.25") works pretty well in milled 2x10 framing in zone 6. Install a layer of gypsum board paying attention to air sealing details and give it a coat of "vapor barrier latex" prior to installing the decorative t & g.
At 4" the closed cell foam is even structural, but it comes with a substantial greenhouse gas footprint. The cheaper stuff at about a buck per square foot per inch of depth (budget $4 per square foot for 4") is blown with HFC245fa which runs about 1000 x CO2 @ 100 years. The pricier (budget $5 per square foot for 4") slightly higher R/inch stuff is blown with HFO1234ze, which is less than 5 x CO2 @ 100 years. But any closed cell foam has a substantial footprint from the polymer itself, due to the high polymer per R at 2lbs density. Even though the blowing agent's footprint of the HFO is less than 1% of the HFC, it only knocks about 1/3 off the total greenhouse gas footprint of the insulation per R. See:
https://materialspalette.org/wp-content/uploads/2018/08/CSMP-Insulation_090919-01.png
I finally have time to get back at this, thanks everyone for your help, my goal at this point is what is the ideal way to correct this system from the exterior without disturbing the interior wood ceiling,and without adding to much thickness to the roof, we are willing to remove can lights, and do what is necessary from the exterior side. thanks so much for your help. Glen