To crawlspace or not to crawlspace?

We are a group of four builders in Quebec breaking ground on a new construction this summer. We’ve been arguing over the niggly details for three years as we try to cobble together the most common sense, super-efficient, affordable house possible. As we seem to be proving, the discussions on how to build can go on forever…
SOGvsFPSF… We are not keen on concrete floors for a lot of reasons. Being in the renovation business makes you realize just how terrific it is to have a certain amount of future flexibility in the design. We’d like our house to last a good, long time but have pulled out enough bathrooms and kitchens to know just because we think it’s the bees knees doesn’t mean the next occupant won’t want to rip it all out for something brand new. We don’t like standing on concrete floors and even less breaking them to move plumbing. The environmental impact isn’t pretty.The thermal mass and in-floor heat are plusses but the level of insulation and detailing we’re looking for ought to provide a nice toasty floor without it.
We’re therefore looking at having a crawlspace (unvented, well-insulated, conditioned, vapour-sealed and properly drained) with a 4′ FPSF wall with vertical & skirt insulation to allow access from below. We don’t want a basement — again because we spend so much of our time seeing them go very wrong. Ideally the stem wall would continue at the very least a foot above grade but the interior floor would be as close to grade as we can. We are thinking of framing a notch into the concrete for hanging the joists and for door openings.
Is there a clever way of having a very well insulated close-to-grade floor with some rodent protection that we don’t know about?
Any input would be most welcome. We have read both GBA’s articles on the subject of crawlspaces and know they are unpopular because they fail. We’re looking for options. Thanks!
GBA Detail Library
A collection of one thousand construction details organized by climate and house part
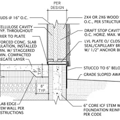
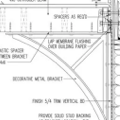
Replies
William,
- Treat the crawlspace as a short basement, insulating the walls and floor just as you would if it were taller.
- As Chris said, you can use a thinner slab, and forego the smooth power trowel finish. Up here we call it a scratch coat rather than a rat slab.
- Make sure to either provide ventilation, or sufficient vents to the floor above, so it is part of your conditioned space.
- Consider the sequence of construction. Because of the limited height you may want to do more of the insulation and framing before putting the first floor on.
- Done properly there are no inherent problems with crawlspaces. We routinely build on them here in BC.
- Think through the implications of dropping your floor to the same level as your foundation walls. It can make running plumbing and wiring from the crawlspace to the exterior walls a lot more difficult. Depending on your plans that may not matter.
William,
I'm familiar with frost-protected shallow foundations, but the ones I know about are slabs on grade. I don't know what you mean by a "4-foot FPSF wall."
If you want rodent protection, build with airtightness in mind. The lower your blower-door results, the better the likelihood that your house doesn't have a rodent-sized hole to let the critters in.
GBA has lots of information on building sealed, insulated crawl spaces. Here is a link to one of our articles on the topic: Building an Unvented Crawl Space.
Thanks! Chris, as appealing as a nice, clean slab is, we're trying to avoid using too much concrete so we may have to pass. Thank you Malcolm, love the comment about sequence of construction -- a real "D'oh!" moment in the making and the plumbing/wiring question as well. We're doing 12-16'' double stud, dense-pack cellulose walls so we should have enough room inside the envelope to bring up the mechanicals.
Sorry, Martin, I meant a 4' stem wall. Working in québécois but writing in english has its downsides. Next time I may hit you up in French!) Our 1850s house has little corners of the doors gnawed away from when the place was empty much of the time. It's a constant struggle to keep mice (and squirrels and chipmunks!) out of the pantry. I'm paranoid.
Thanks so much.
Guillaume,
Ça m'agace, les mots techniques -- plancher-dalle, vide sanitaire... Ouf! C'est difficile.
Comment dit-on «frost-protected shallow foundation» en français?
In the US we have what is called a "rat slab". It's about 3" thick layer of concrete w/o re-bar. I saw one installed under a house with a 3 ft tall crawlspace but I'm in climate zone 3A. I was jealous of how clean it was.
With a rat slab you can insulate the crawlspace walls and underneath the slab itself.
Martin,
The first frost protected shallow foundations I remember were half-buried basements built in the late 80's that didn't extend deep enough to get below the frost line, so used horizontal rigid insulation to compensate. The technique was being routinely used to protect the footings on houses with exterior stairs into their basements. I also remember using it on the sunken patio's of several large condo projects. The use as complete FPSF's on new builds might have been an extension of that.
I've seen 1" rat slabs (troweled and rough) that performed their function well for a century even in a full basement that had some foot traffic. A rat slab in a crawlspace doesn't HAVE to take very much concrete at all.
Conditioned crawl space have a great deal of utility as duct & electrical chases. Just make it deep enough that an adult human can actuall crawl on all fours rather than have to swim like a snake to install or service anything in the crawl space.
our main concern about this option is why is it almost "illegal" to have a crawl space. What is so wrong? moisture,insulation,air exchange are easy to deal with but still all we hear about is that it's a mistake to have one. Our main point to have one is that we have really hard time to beleive that insulated skirt around a slab will last hundreds years, So we will go down to frost line and might as well use the space if we don't want to have a cement slab on the first floor. Comments? thank you again!
William,
As I have often written, builders tend to stick with the foundation systems they are used to. They usually prefer to build the type of foundation they see in their neighborhoods. Certainly crawl spaces aren't illegal in the U.S. -- in many parts of the U.S., they are the most common type of foundation system built -- and I doubt if they are illegal in Quebec.
Almost all Quebec homes have basements, for valid historical reasons. That's where you kept your potatoes -- ideally in a basement that was big enough to stand up in. A basement or cellar was the only place in a Quebec home (100 years ago) that could be depended on never to freeze. A frozen potato will spoil, so you need a basement if you want your potatoes to last until spring.
Thanks again. Martin, the difficulty/charm is actually that we work in "franglais". So much of the building vocab that is used on the worksite has little if anything to do with the more formal language you need if you're looking online or in books. An FPSF is a Fondation peu profonde protégée du gel (this from the language with no word for shallow!) but around here we'd call it a dalle monolithique. We're pretty confident we can do a good job on detailing the crawlspace to make it work. I may hit you all up for opinions on inside vs. outside insulation and best membranes for the floor but maybe i'll start another thread for that.
Thanks to all. Merci à vous tous.
I have a Crawlspace that i would love to get rid of but can't afford to. Your welcome to take it from me ;)
Pros:
Lower cost
Cons:
More air leakage (blower door can pull air through the soil)
more vermin (bugs, spiders, mice)
radon (a concern everywhere in canada)
hard to insulate floor
introduces moisture often necessitating a dehumidifier in summer (can otherwise lead to mold/wood rot)
Alan - All of your "cons" would also apply to a full basement. Or are you saying that you wish you had done a slab? A crawlspace done right should have none of these cons.
My cons are for a dirt crawlspace, bugs live in dirt, but don't typically eat through concrete, according to several GBAers my high ACH is exacerbated by air being pulled thorough the soil, concrete is a physical barrier to radon, you can insulate with foam under a slab, on top of dirt it would not survive being walked on, and concrete while water permeable is far less so, and can have a poly barrier under it (and can even be treated with compounds like xypex).
Alan,
My sympathies. I hate dirt crawlspaces too - and it's a huge pain to try and pour a scratch coat after the fact.
There are a few regions in Canada where radon is not present. Luckily for me the whole of Vancouver Island is one of them.
The dirt interface is a crawlspace's biggest weakness. There may be a few examples of well built 1-2" slabs for crawls but most rely a thin sheet of plastic. Proper slab construction gives you a well drained gravel layer which can be passively vented. This type of construction is typically closer to perfect.
Use an unvented crawlspace for the right topography and situation. Only vented crawlspaces should be made illegal. I think many are building crawls in situations easily served by better performing slabs.
Crawlspaces are an antiquated form of accessibility. They usually hurt everyday access issues by adding steps. Practically all commercial jobs are slabs including most homes in the US. The only stuff that might need changing below your lowest floor is waste plumbing, which is not a big deal during those types of renovations.
Crawlspaces add volume and surface area to the building envelope. They add air leakage, moisture loads, and energy usage. These areas can hardly be considered storage as they are rarely used for that and the more they are used, they more they put that thin piece of plastic at risk.
Brian,
Just went back and added an additional kick space outlet for the built-in-vac system in the laundry room of a house I finished this summer. Try doing that with a slab.
You are still insisting that moving plumbing under the slab is no big deal during a renovation, but taking the house I just worked on, which has wood flooring extending under all the cabinetry, I could completely renovate the kitchen without touching the floor.
There are plusses and minuses with each assembly. I don't think it helps your argument to deny the real downsides slab construction has when it comes to future work.
If you do a crawl space, install the rat slab before you begin the framing. Don't try to do it after. I had many people try to convince me to do it at the end but even in our rain forest climate of North Vancouver, I had no problems. As per code, I did include a floor drain tied into the rainwater leader drains.
Thanks Malcolm, you're right. Future remodeling considerations are a benefit of crawlspaces. Even more important are topography and site considerations. We don't know the OP's situation and I thought the random opinions could use more balance, especially on a site that champions energy efficiency and the building envelope. If you are going to build a crawl space, at least make it unvented, insulated and conditioned. Be aware that this space will add to the soil gas, moisture and energy concerns.
I'm not sure about the relevance of using existing homes as examples here. If the home had been designed without a crawl space in the first place, then the conditions and situations would likely be much different. I'm sure there would be options for the outlet and I think most renovations big enough to relocate plumbing, walls or cabinets would also be replacing or refinishing the finish flooring.
While it's certainly an advantage, I think the importance of utility access is overblown. Crawlspaces are almost never used and they usually add steps, which hampers everyday flow and access to the main spaces. Commercial buildings, basements and homes on slabs are remodeled and renovated all the time. I don't think concerns of future work should result in a convoluted building envelope with increased soil gas, moisture and energy demands unless the site conditions beg for it.
I'm with you, Malcolm. As my partner says, builders deal with the house for the first year, renovators deal with it for the next 199. There is no way I'd do a slab without infloor heat in our frosty climate and chopping up a slab to run new plumbing is bad enough without also worrying about scrapping your heating system. Let's face it, Canadians have some extremes that just aren't a factor for our friends from the south. I am a bit perplexed, and would love to be enlightened, by Lstiburek's specifically NOT insulating the floor of a conditioned crawlspace (http://buildingscience.com/documents/information-sheets/crawlspace-insulation). It doesn't make sense to me. Thanks again.
@William
Since the interior walls of the crawlspace are insulated (less insulation needed vs. insulating under entire floor) and it's part of the building envelope (unvented, open floor vent via first floor, dedicated supply to provide a little conditioned air) there's no need to apply insulation to the underside of the first floor.
Basically built like a mini-basement.
Thanks Chris. That part makes obvious sense but if you look at Figure 3 of the linked page, there is no insulation under the vapor barrier. That's the perplexing bit to me.
Less insulation on crawlspace walls compared to floor depends on the crawl. Tall crawl spaces may have more surface area to insulate compared to floors. It also seems to be a bigger pain to deal with termite concerns. From a building science POV however, crawl space walls should be insulated not floors. Here is another BSC doc on crawlspaces: http://buildingscience.com/documents/insights/bsi-009-new-light-in-crawlspaces.
I think Dr Joe would stick closer to his description of a perfect wall if he were facing the decision, to crawl or not to crawl but you would have to ask him. http://buildingscience.com/documents/insights/bsi-001-the-perfect-wall
Perfect crawlspaces don't seem to be considered here. Unvented crawlspaces are more of a solution to existing home problems.
Thanks Brian. Fortunately, termites aren't really a problem for us... but with winter weather climbing yearly it's probably not a bad idea to plan for the worst. We never had ticks until a decade or so ago...
I think the lack of subslab insulation in his illustrations are just an oversight.
@ William.
I suspect it depends on climate zone as to whether or not you want to insulate the crawlspace floor.
Here's another detail showing a termite inspection strip. http://www.finehomebuilding.com/how-to/departments/energy-smart-details/creating-a-sealed-crawlspace.aspx?nterms=126503
It just seems funny to me that as more of the building assemblies, like walls and roofs, being used by energy efficient builders include conditioned service cavities, that crawlspaces aren't seen in the same light.
Does waste plumbing deserve a serviceable cavity at such major expense to the building envelope? I think other solutions exist for most everything else.
Waste plumbing, Hvac and ducts, electrical, conduit for media and controls. The same things that go in conditioned attics. Where is the extra expense? I only use them when they are the most economical way to realize a project's goals.We went through much the same arguments in the discussion of your blog. I don't particularly like crawlspaces, or favour them over other alternatives. What I do is keep an open mind and include them as an option which, depending on the site and plans, I might use. So far you haven't given me a compelling reason to preclude them.
Brian, I'd love to hear how you would handle a near grade floor without a slab. I'm really looking for options.
Malcolm, I'd be interested to hear about the other options you use. We've had to retrofit a couple of excellent renovations with air exchangers and boy were we happy to have a crappy little basement for all the ducting. Some of our reticence undoubtedly stems from doing renovating as opposed to building from scratch. The challenge is trying to find a way to build an almost passive house without marrying oneself to ALL the techniques. I personally don't see why a well-designed crawlspace can't be considered a very effective part of the building's envelope.
William, I cycle between slabs, crawlspaces and half-buried basements based on the site, budget and the house design. The last house I built was the first in several years with a crawlspace. My favoured approach is using the slab as a finished main floor. That works well with the modernist designs I generally do.
I understand Brian's reticence to use crawlspaces where he is. There are things I take right off the table as options here in the Pacific Northwest. Flat roofs, unvented roofs and decks over living spaces, designs with no overhangs, stucco and masonry. I do that for regional reasons, and I assume Brian does the same for where he is. I wouldn't suggest using my list as a general injunction against them anywhere.
The extra expenses are to the integrity of the building envelope and the ongoing, monthly costs associated with the added space conditioning loads. Lots of ways to look at the upfront expenses that are entirely site and situation dependent. My main point is that crawlspaces add building envelope costs and sloppy workmanship for questionable benefits. Everything but waste plumbing can be located topside without building a semi-controlled cave below the dwelling. The building envelope issues are compelling reasons to me and probably why crawl spaces aren't mentioned in Dr Joe's perfect wall document or seem to be allowed at all in passive house certifications.
William, to me it's mostly about the site and topography though if a client wanted a crawl space for other reasons, we would build it, but only if it were to be unvented, insulated and conditioned. I understand your concerns with concrete but challenge the idea of being inappropriate. Concrete is a natural building material with ancient origins, mostly sand, gravel and limestone and is the most used material in the world. Its weight, abundance and volume are the main reasons for its notoriety but a fine choice in the right applications.
You could look into earthen slabs as a substitute but I tend to doubt it will end up being more appropriate in the big picture. I would probably prefer an earthen slab to a low crawl space though. You could also go with pier construction, the main choice for flood prone sites and one of the safest methods for a true separation of ground and home.
In most applications I would choose an unvented crawlspace over piers. The sites that make the most sense for crawls are those that slope downhill from the driveway or entrance and have 4-7' of slope with bedrocky soil or with no room to adjust the finish grade for a walkout level basement or lower level. For slopes less than ~6', I would likely prefer filling the stemwalls with clean gravel and topping with a slab.
For sites that slope uphill from the drive or entrance, we prefer to use masonry stemwalls or pre-cast concrete panels on the back side of the home, bermed into the topography to eliminate the need to add steps or build a cave below the home. Pier or slab construction with a well vented and drained gravel layer provides better control layers for a well defined building envelope with separation from soil concerns below.
@Brian
In your climate zone is it customary for ground floor HVAC supply registers to be installed near the ceiling? I know with a slab it's basically mandatory, but curious to know if it's done that way with crawls/basements.
Even with an unvented crawl, I would prefer to keep most ducts out of there and yes, they are typically at the ceilings on the ground floor. Deep floor trusses make this easier. If we ever start using triple pane windows, we could probably avoid the need to locate supply grills near windows though it's still a challenge to avoid short circuiting with the return grills in bedrooms.
Some of the details of my current renovation of a house built in 1888, to upgrade heating to 21st century geo-thermal system may be relevant to your questions.
All of the floors were originally constructed over dirt. Besides being cold throughout the winter months here in west central Minnesota (zone 4) rodent control was a major endeavor in autumn as temperatures begin to fall. Part of my problem was deterioration of areas in the stone rubble foundation walls. After cutting several openings to examine/confirm the conditions I elected to remove all flooring including sub flooring. I was able to then examine the original 127 years old rough sawn, white oak, joists and beams. Fortunately the beams were in good condition. Many of the joists were not. I removed all suspect joists. I dug trenches for 4" diameter radon mitigation piping and placed perforated pipe wrapped with filter fabric in clean gravel.This system ultimately terminates in a sealed sump basin before venting to the outdoors. I also repaired all areas of deterioration in rubble foundation. I insulated all perimeter walls with a minimum of 2" rigid insulation and sealed all joints with closed cell foam.
Once the perimeter was insulated I raked the floors smooth and covered the floor and wrapped up the sides of the foundation with a vapor barrier mechanically fastened and sealed with polyurethane caulk to the top of foundation wall. All over lapped joints in the vapor barrier were sealed with 6" wide Grace Vycor ice and water shield tape.
Rodent control was addressed by rolling out 23 gauge galvanized hardware cloth with 1/4" grid in 36" wide rolls again overlapping the edges and where any potential gaps resulted from uneven substrate, stitched together with light gauge galvanized wire. This too was wrapped up sides of walls and fastened to the wall plate using 1" roofing nails.
New rectangular duct trunk lines were installed on top of 2" rigid insulation board and wrapped and sealed with both 2" rigid board and foam. New round ducts running perpendicular to joist direction were insulated in a similar fashion. Once this work was complete all missing joists were replaced and continuation of duct runs between joists also were insulated in fashion previously described. Rigid board insulation was then cut to fit between all joists and adhered and sealed in place and covered with perforated aluminum reflecting foil (anticipating potential future electrical radiant flooring). New 3/4" T&G fir plywood sub floor was then installed.
This construction results in a monolithic vapor barrier, a completely sealed, non-vented, crawl space, fully insulated against the ground temperatures and creating passive radon mitigation and moisture wicking to the extent dampness occurs under the vapor barrier.
Thanks for all your input. We feel pretty confident we can do it well so we're going ahead. Which leads us to our next challenge; finding a way to hang joists from the inside of our foundation wall without sacrificing thermal performance. In a perfect world we'd like the foundation wall to be a foot above grade with the interior floor close to grade. We like the ICFS but have a hard time with the exterior foam. We've seen rodent tunneling, nests and that's without mentioning the challenges of covering the foam for an aesthetic and durable finish. How does one hang a perfect ledger on the inside of a couple of inches of foam? Is there any magic bolt/screw product (that doesn't cost an arm and a leg)? Are Thanks!
William,
I'd suggest taking a small hit on efficiency, and rather than hanging the floor ledger (with all the attendant complications of supporting it through foam and then having to use hangers on all your joists) that you form a ledge into the top of your foundation to sit your floor system on. You can run the foam behind the rim joist, although you will have a bit of a bridge under the sill plate.
Malcolm, we're looking at the Simpson Connector system (essentially an octagonal plate with perforated wings that jut through the foam and get locked into the concrete. The plates on the interior finished foam give you a little wiggle room for attaching a perfect ledger and then top-chord-bearing trusses hanging off the ledger. Ever tried this system? We're also looking at the Helix microrebar for the concrete. Chairs or no chairs, expecting the mesh to stay where it's put as you walk all over it doesn't make a lot of sense to me.
William,
Our climate is so temperate that I don't worry as much as you might about thermal bridging. When i want a framed floor flush with my foundation walls I use a PT 2"x12" as a pour strip on the inside of my forms and leave it there in the finished wall. I can then set my joists on hangers attached to it and insulate as though it were a rim joist.
For slabs that will be the finished floor I don't reinforce with mesh or rebar. I saw cut them on a tight (usually 3'-0") grid and grout the lines.
Thanks again Malcolm,
Do you not worry about the sill wicking moisture out of the foundation? I suppose if you eliminate some of the temperature variables with insulation there's less of a draw.
And no kidding it's more temperate there! Sometimes I wonder why we choose to live here. Yesterday was a balmy 12 degrees and it was -32 the day before! Our poor building envelopes have to work so hard!
William,
Yes it is 12 degrees here too and I'm working in a T-shirt, but on top of that I'm wearing full rain gear - as I have been every day for the last month. The long term forecast calls for (you guessed it!) rain. There are trade offs for the mild temperatures.
Then I suppose it would be feasible to wrap the bottom and backside of the PT 2x12 in foam in the forms pre-pour? Hmmmm....
Hi William - I am really interested in how this worked out for you. Thanks, Sarah.