To Spray foam or not?

I am trying to decide whether to spray foam my house which is currently down to the studs. I am in climate zone 2 so it is hot and humid most of the year. The house currently was built to have a vented attic. The house is about 3,000 square feet and is one story. I have a asphalt roof shingles that I had installed last summer. My HVAC equipment and water heater are in a mechanical room separated from the living space by walls and with a louvered door to the outside.
My concerns are air quality and whether the spray foam will off gas, and also whether the energy savings will be worth the extra cost. I have read the articles on Green Building Advisor on spray foam. I am considering creating a conditioned attic since my ducts are in the attic.
Spray foam contractor is telling me that I only need 5.5 inches of open cell foam sprayed to the underside of my roof decking. I know that it is common for spray foam contractors to say this despite the R value being less that what is code which code requires R38.
I read the Building America study entitled “Reducing Thermal Losses and Gains with Buried and Encapsulated Ducts in Hot-Humid Climates” from Feb. 2013 which studied spray foaming ducts and compared the energy savings to creating a conditioned attic with spray foam. According to the study, creating an unvented attic was not cost effective compared to just spraying the ducts.
My ducts would have to be reconfigured so that I could just spray the ducts. I also have a lot of recessed lighting, and although they are Halo airtight lights, I doubt that they are completely airtight.
Are the energy savings going to be enough for it to make financial sense? The answer to this seems to be no, but I am open to hearing other opinions.
Is 5.5 inches enough to spray on the roof deck? The answer to this seems to be no, but contractor claims attic will not be hot with only 5.5 inches of open cell foam.
How much do we really know about the toxicity of spray foam? If we don’t really know yet, it seems it may be better to error on the side of not using spray foam.
GBA Detail Library
A collection of one thousand construction details organized by climate and house part
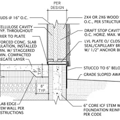
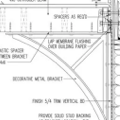
Replies
Kasey,
Here is an article on why open cell foam for attic insulation is not a good idea: https://www.greenbuildingadvisor.com/blogs/dept/musings/open-cell-spray-foam-and-damp-roof-sheathing
You could use closed cell foam, however. And some of the new products rely on much "greener" blowing agents.
Spray foam contractor advised against close cell on roof deck because if there was ever a leak, I would not be able to detect it and it could cause damage to decking and framing.
Yeah but now studies are saying open cell under roof deck can lead to moisture build up in the sheathing.
Kasey,
That is what many argue, but you should believe what is in the artifice I linked to.
The very best answer is to get the ducts out of the attic and into conditioned space and covered with a drywall soffit.
Before you insulate it is necessary to air seal the attic. The first step in that is getting rid of the pot lights.
My opinion the payback for moving the ducts or insulating the roof is too long. I would clean the outside of the ductwork and seal the joints with foil tape, remove the pot lights and air seal the ceiling then add R30 cellulose insulation.
The only real way to know it makes financial sense is with a computer program called BEopt. The program is free to use but take lots of time learn and run.
The foams seem safe when applied according to the instructions. Will your installer call off the install if it is to hot or cold or will they try it and see if it works? Will they apply it to thick so they can get home on time?
Walta
You ask about payback, so what was your HVAC costs prior to remodel?
What makes a big difference in a/c is windows. So if you have 500 sqft of west facing windows without shade, then you will have high a/c costs. Getting the ducts in conditioned space is worth 20% (WAG) and so the 20% of what is a big factor on payback. In my last house, 2000 sqft per level, foaming the roof line was about $50 in a/c costs (and similar for heat) is Zone 3/4. It was a tall roof so the payback was never.
Now - if you are redoing HVAC, then you have to factor in the downsizing in the payback.
Other factors include longevity of duct work and superiority of humidity control with a sealed attic. But getting the mechanicals out of the attic is the biggest issue in terms of longevity which you have already done.
I never lived in this house prior to remodeling it. I do not have any windows or doors facing west. I am leaning towards not spray foaming the underside of the roof deck and instead just insulating with fiberglass.
When it comes to air sealing (ducts or attic floor), be sure to actually test the results. Consider using blown in cellulose insulation.
I am assuming I would test attic floor with blower door. What result should I shoot for on attic floor?
Kasey,
You can certainly do a ventilated attic, but it is still important to air seal. Moving the ducts out of the attic would also be a plus. Some homeowners run the numbers and decide to go with a mini-split system. This allows them to abandon the ducts.
With ducts in the attic it's important to air seal both all of the ceiling/attic floor penetrations AND the ducts. Even if the house is reasonably air tight leaks in the duct work can drive air infiltration rates to very high levels whenever the air handler is running using "the great outdoors" as the pressure relief path.
In zone 2 encapsulating the ducts in vented attic with open cell foam can lead to saturated wet foam during the cooling season, but encapsulating them in an inch of HFO blown closed cell foam would be sufficient to allow burying them in a few inches of blown cellulose.
Air seal the gaps of the register boots & ceiling gypsum with can-foam & or caulk, and tape over it with housewrap foam. (Gypsum board can crumble at the edges with vibration & moisture, so without the tape the longevity of the air sealing isn't certain.) Any seams or joints in the duct boots & hard duct can be sealed with duct mastic, which works even on dirty or corroded metal. (Temperature rated foil tapes can work on shiny-new hard piping.)
Testing the room-to-room pressure differences with a cheap $100 hand held differential manometer with 0.01 water inches resolution is also worthwhile. An Energy Star home is commissioned with this type of testing, and the room to room differences have to be less than 3 pascals (0.012 water inches) under all operating conditions, doors open/closed, air handler at high/low speed, etc. With a cheap instrument operating at the limits of it's resolution it it's absolute accuracy isn't as high as it's resolution, and it needs to be tested in both directions. But any reading of 0.02" or higher is an indication that the duct balancing can be tweaked. Pressurized rooms are usually a result of inadequate return paths, but sometimes excessive supply that can be dialed back with balancing vanes.
Any flex duct needs to be stretched tight to have predictable flow characteristics. If it needs to make turns, use hard-piped ells, and make sure they are sealed well.
The actual cooling load of a 3000' single story in zone 2A is likely to be on the order of 2.5-3 tons. Having the parasitic gain of ducts in the hot attic and the parasitic infiltration losses can easily add a ton to that. But at typical "rule of thumb" HVAC sizing you probably have 5-6 tons of compressor(?).
The notion that closed cell foam on the underside of the roof deck makes it harder to find roof leaks than open cell isn't borne out in practice. Both open & closed cell foam makes it somewhat more difficult, but it's not a disaster. An inch of closed cell foam is sufficient to protect the roof deck from moisture in the attic air from being adsorbed into the cold roof deck over night, and the rest of the insulation can be fiber, as long as there is an interior-side air barrier (or the fiber is high density, such as R23 rock wool.) It's still more effective to spend the money encapsulating and burying the ducts from an energy use point of view, but from a hurricane resistance point of view, a sealed attic is better than a vented attic since it reduces the uplift pressures on the roof sheathing. At 3" or more closed cell foam is even structural, stiffening and gluing the roof deck to the rafters or trusses. (Open cell foam doesn't add anywhere near that amount of structure.) If you're in a hurricane zone it's worth considering.
In general closed cell foam isn't very green, with a high polymer per R ratio, and closed cell foam blown with (the industry standard) HFC245fa blowing agent makes it orders of magnitude worse. But there are now multiple vendors of foam blown with HFO1234ze, which has dramatically less environmental impact. At 3" it's going to be over $3 per square foot, but at 1" it should be on the order of $1.25-$1.50 per square foot- definitely not cheap R by any means, but more protective of the roof deck than 5.5" of open cell foam.
Is there a closed cell spray foam that has a blowing agent with low global warming potential and that does not need an ignition barrier? I see LaPolla's FL-2000-4G uses Solstice LBA which they claim has low global warming potential, but it appears to still require an ignition barrier. If I spray the roof deck, I will need an ignition barrier since it will not be covered with sheetrock, right?
For an attic that isn't used for storage or living space most code officials would allow intumescent paint as the ignition barrier. Most would also allow 3" (minimum) of rock wool insulation as a ignition barrier, as long as it was held in place with something that won't burn (steel wire). A fire-rated perforated aluminized fabric type radiant barrier holding the 3" rock wool in place with 1x furring might fly too. Talk to the local inspectors. (If going that route, only use the perforated radiant, which is semi-permeable to water vapor, and won't create a moisture trap the way foil or un-perforated aluminized fabric versions can.)
Solstice is Honeywell's trade name for HFO1234ze.
Demilec's Heatlok HFO High Lift is also blown with HFO1234ze. There are others, but you have to ask.
Are there any potential issues if I just spray foam the underside of the roof decking and not the walls? Or is this not recommended? I have 3 foot eaves that shade the walls.
Would 1" of closed cell with additional open cell sprayed on the underside of the roof decking prevent the issues with roof rot?
It's fine to treat the roof separately from how the walls are treated.
An skinny inch of closed cell and 4.5" of open cell would be fully protective of the roof deck in zone 2 but runs the risk of moisture pumping in/out of the open cell in summer. In some situations moisture gets pulled from the attic air into the open cell foam when the roof deck is cold overnight, then released into the attic when the roof deck heats up during the day.That risk can be mitigated with a "smart" vapor retarder such as 2-mil nylon (MemBrain) or similar &/or a small amount of supply air from the HVAC systems.
I am still trying to decide whether to use any spray foam for air sealing purposes. I am considering a flash and batt approach for the walls with 1 inch of closed cell (LaPolla FL-2000-4G) and a fiberglass batt for the rest of the stud cavity. Walls are built with 2x4s. As a reminder, I am in zone 2.
I am mainly interest in using the 1 inch of closed cell for air sealing purposes because I do not want to remove the siding on the exterior. The interior wall cavity has tar paper which was nailed on the studs from the exterior. The siding is vertical wood v-groove siding which was installed over horizontal strips of wood. There is no sheathing on the exterior. Some of the tar paper is torn in places. The walls had a lot of roach feces in them. The house is 60 years old. I plan to insulate the attic floor with fiberglass batts or blown in insulation.
Should I flash and batt in order to air seal the walls? Will this provide a good air seal long term or should I just use fiberglass batts or some other approach? Please advise.
Hi
I’ve been trying to gather information on the very subject for my house. They really haven’t done definitive enough studies to determine the expelling of vapor. One study done in some kind of micro chamber (I think that’s what they called it ) showed there was still off gassing after a year and a half. How much I don’t know? EPA’s stance is it needs more study. There is also studies going on as to why the attic can develop a lot of humidity 70 or even 95%. Not things I want in
Y attic space.