Tongue & Groove, Smitten by the Fates

Help me solve this sad mystery.
4/15-4/27: I installed ~1200 SF of 2×8 Select Structural Doug Fir Tongue & Groove on a timber-framed roof in Zone 2A. Kiln-dried to ~14% MC, finished with Rubio oil stain.
I used straps and a dead blow hammer to get the boards very tight — 1/16″ seams were 1/16″ too much for me. This was… not easy, to say the least. Rafters vary from 0″-40″ oc (pyramidal hip roof). (1-2) 3″ GRKs + (3) 3″ ring-shank nails at every bearing point.
4/27-5/15: We got tons of rain, often pouring through the still-tight seams.
5/16-5/20: Solitex Adhero over entire roof. Building gets sheathing + Tyvek (air-sealed). I turn on (2) 1-ton portable/floor ACs, which depressurize the building significantly (hard to open the construction door), dehumidify it decently, and cool it not-much-at-all…
~6/10: Record heat wave begins. 103+ F for ~2+ weeks.
6/19-6/28: I install polyiso + plywood + ice&water atop the Adhero. While checking for blowouts inside, I start to notice *massive* gaps everywhere in the T&G. Sometimes, I can see the entire tongue — that’s nearly half an inch. To say I am “crestfallen” or “sad” is a bit of an understatement… I’ve worked on this building for almost 3 years, and the ceiling (exposed rafters + T&G) is the defining visual trait. I cranked those flatbed-grade ratchet straps until they nearly broke.
This isn’t my first rodeo with T&G, timbers, or TX summer. I even did a similar building with No. 1 SYP T&G in this kind of heat with no issues, though we didn’t have rain. What did I do so wrong? Was it the weather, the floor AC’s? Is it gonna get worse if I don’t do X or Y? Thanks for any thoughts!
GBA Detail Library
A collection of one thousand construction details organized by climate and house part
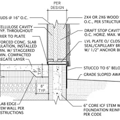
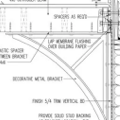
Replies
jamesboris,
The appropriate moisture level in any interior wood needs to be calculated based on the average annual interior humidity.
https://www.finehomebuilding.com/2022/05/03/how-to-acclimate-a-wood-floor-correctly
The moisture content of framing lumber should be in the 10% to 14% range. Kiln dried material is generally around 6%. Unfortunately I think it is as simple as you started with too wet wood.
To be honest, I have never seen KD lumber that dry in central TX. 12% if it's in a conditioned warehouse unless dead of winter. Only hardwood flooring comes to us that dry, and we have to let it "get wet" (i.e. acclimate) for quite a while because of it.
jamesboris,
The other factor is the size of the pieces. The wood shrinks towards the point of attachment. Wood with the same moisture content which was half as wide, would leave gaps half the size.
Jamesboris, are you saying that it rained heavily on already-installed ceiling boards? I have had similar things happen on projects and I feel your pain--it's no fun at all.
This book includes relatively easy-t0-understand formulas for determining shrinkage for various species: https://www.goodreads.com/en/book/show/156605. Not that it will help you now, but if you decide to start over, or for anyone else reading, it's a good guide.
Thanks Michael, I've consulted [online sources that've excerpted] that book for hardwood and trim stuff. I just had no way to apply that standard to this project since there was no on-site conditioned space in which to season the wood. The moisture content is now 11-13%, which still seems like a lot of shrinkage in light of what the tables say. Hence my paranoid possible delusion about the negative pressure having something to do with it ha.
In my experience all wood shrinks after installation. It doesn't matter what time of year it's installed or what the weather is like outside. The equilibrium moisture content inside a house is lower than the unconditioned space where wood is typically stored.
This is particularly true of roofs and attics. Unlike air, wood absorbs less moisture as the temperature increases.
DC,
That's what I find mystifying about advice to season wood on a construction site. It reaches an equilibrium with its surroundings, which usually doesn't represent what the RH will be in the finished home. That's why the chart I linked to makes sense. You know what moisture content you are trying to achieve independent of the condition it is being stored in.
Thank you for saying that. The more I learn about building science the more I wonder about that advice.
First, I wonder how much the moisture can change in the time frame they're talking about, typically a few days or a week. The traditional advice is that wood has to dry after cutting for one year for every inch of thickness. I realize that cut wood is a lot wetter but the point is the moisture levels don't change quickly.
Second, even in a finished house the humidity can change quickly and significantly. I measure the humidity and temperature in my house all the time, and on a spring day the RH can be 40% in the morning and 60% in the afternoon. Looking at the chart I posted earlier that would equate to an equilibrium moisture content of 7.7% in the morning and 11% in the afternoon. That's a huge swing.
I've seen humidity swings in my area (Southeast Michigan) that go from 30s %RH to 99%RH, which I take as "my humidity sensor is saturated". It's not uncommon to have swings like that in the summer, when the daytime temperature can get up in the low 90s while night time temps might be in the 60s. Rainstorms can also do it.
DC, I'd expect your area is a little more constant day-to-day, but still has big seasonal swings. When I visit out there, I like to go in the spring and fall, when it's nice. Summer is a steaming sauna. When I was consulting out there in the summer, 100+ daytime temps with very high humidity levels were common.
The difference between those two areas is that in my area, you're probably going to see the issues within a week or two, maybe days. In DC's area, you might get a lot further into your project before things change enough to see big problems. Different climatic conditions will change how long it takes to see problems arise.
Bill
I once installed a cherry floor over a radiant heat pipes (which I had also installed). I was very concerned about shrinkage so I made sure the cherry was super dry. Not long after installation, it swelled and buckled. That was fun.
Did you end up tearing it out?
I honestly can't remember what I did; it was almost 20 years ago. I probably ripped those boards out and replaced them. The owners would not have lived with buckled floors and I wouldn't have been able to face-screw them down since I couldn't have known where the radiant tubing was.
" We got tons of rain, often pouring through the still-tight seams."
There is your problem. There is nothing much that will stop wood from expanding, the old fashioned way to split boulders is to hammer in wood wedges and pour water on them. Your 3" ring shanks are nothing in this case.
My guess is after the rain the boards expanded which would not be noticeable. Once you got the place under roof and dehumidified, the broads shrank back down thus the gap.
I don't think it is every really possible to do a tight T&G install unless you season the boards inside a conditioned space such as the one where they will be installed. Even then there will be seasonal movement, for example, I built a loft out of 2x6 T&G that was in the basement for about 2 years and I'm still seeing 1/8" of gap.
I guess I just got lucky on my last install. I used 2x6 No. 1 SYP -- each piece was so warped, I had to cut it into 4' lengths, was miserable... most gaps started at least 1/16"... but there's been no movement. Perhaps because it was just a much drier year. SYP is like rock compared to DF...
If you cut the boards into many small pieces, you also have many small gaps between boards when they go up. Those "many small gaps" act as a sort of distributed expansion gap, and can absorb some of the expansion, and since the total amount of expansion/contraction is distributed over many small gaps, it's not nearly as noticeable as it would be if there was only one gap dealing with the entirety of the dimensional change of the material.
Bill
This makes sense, thanks Bill.
I had a birch floor start to swell and buckle, I installed several dehumidifiers in the basement and this cured the problem.
The wood was stored inside the house for a month before install so the moisture content of the wood was not a problem. The moisture coming up from the basement was. I ended up spray foaming the basement walls and this stopped all moisture issues.