Unvented Low Slope Cathedral Ceiling with EPDM Roof

I’m building a new home in Vermont with a large living room that has a 1/12 pitch cathedral ceiling. The roof is constructed with 16″ LVLs spanning the entire width, Advantech roof sheathing and a layer of EPDM as the roof cover. The ceiling cover will be T&G.
I’m following the code requirements and suggestions from this blog: Insulating Low-Slope Residential Roofs – GreenBuildingAdvisor
I’m planning on spray foam of 4″ against the underside of the sheathing and then a layer of R23 Rockwool to create an R-value of ~ 51.
I have 2 questions that I haven’t seen in any other posts or explicitly in code and I’m looking for help.
1. The thickness of my insulation (4″ closed cell spray foam + R23 Rockwool 5.5″) doesn’t fill the entire cavity between the 16″ LVLs, I would have a 6″ air gap. Is this ok to leave an air gap between the T&G and the bottom side of the ROCKWOOL or do I need to completely fill the cavity which would increase both my closed cell foam and rockwool thicknesses to maintain a 51% ratio from foam to mineral wool R-value. The implication here would be cost so if there is a standard practice that allows for an air gap I prefer to follow that guidance.
2. I have an air barrier with the foam against the roof sheathing, but do I also need an air barrier above the T&G? I’ve read in other threads that T&G, as well as my puck lights (not cans) are notorious for leaking air and this will cause problems. With the thick insulation and foam I would not expect to have condensation on the bottom of the foam, but I’m also looking for guidance on this question.
GBA Detail Library
A collection of one thousand construction details organized by climate and house part
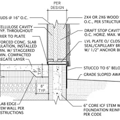
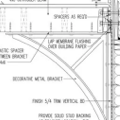
Replies
1. Make sure your Rockwool is tight up against the underside of your spray foam. There's no problem whatsoever with having a gap between the bottom of your Rockwool and your finished ceiling. In fact it will give you room for running electrical and light fixtures without disturbing your insulation.
2. You don't need 2 air barriers in your roof but you want to make sure the roof air barrier ties into the wall air barrier continuously. That requires knowing your wall air barrier strategy and focusing on the eave/overhang detail where the wall meets the roof.
A lot of people place the air barriers at the interior drywall. In your case that's a bit difficult with the T&G ceiling. But an alternate approach (usually my preferred) is to tape the exterior face of the wall and roof sheathing so that the sheathing serves as the air barrier. This works fine and avoids a lot of the interruptions inherent to the sealed drywall approach. But again, you need to resolve the wall/eave intersection.
If you have overhang details in your drawing set that you can share here that would be helpful.
Thanks for you quick reply, this is very helpful. I added another picture of the overhang on this part of the home, its pretty large as you can see and will be the same T&G un-insulated. My strategy for air barrier on the walls is to use spray foam as well. I plugged the gaps between the rafters with RIGID foam and will spray up against this fill the void. I still have access to tape the outside as well if this isn't enough.
Thanks again
I generally wouldn't rely on the spray foam to provide a complete and continuous air barrier in the walls. Your ZIP sheathing is already taped at the panel joints, which is great.
I can't quite tell from the photo if you've done this already, but a band of tape run horizontally at the bottom of the sheathing, taping it to the face of the foundation below would be necessary.
Are you in a termite zone and using a termite shield? If so, this will cause a conflict. In that case keep the termite shield and apply a good bead of caulk where the wall sheathing and the termite shield meet. Also, on the inside of your wall apply a continuous bead of caulk where the floor plate meets the floor surface.
And the key area is at the top of the wall. It might seem a bit tedious. But probably the most reliable approach would be this.
1. Run a horizontal strip of tape at the top of the Zip panels, taping them to the face of the blocking between your rafter penetrations.
2. Run a strip of tape up, across and back down each piece of blocking, so that the blocking is taped to the sides of the rafters and the underside of the roof sheathing.
3. Make sure your roof sheathing joints are taped as well, just like your wall sheathing joints.
This approach would provide you with a full wall and roof air barriers as well as continuity between them. It's a fair bit of labor but the materials are cheap. I don't know of any better way than what I've described.
Sounds like a good plan. We don't have termites up here so taping the sheathing at the bottom is no problem.
Thanks for your help and fast response!
I would not go for MW in your case. Standard insulation wires don't work with i-joists as they are not log enough for the OSB section. You would have to make them or use webbing to hold up the batts.
It is much simpler to get the cheapest faced fiberglass batts and use those. You can staple the facing to OSB webs to hold it in place. The bonus is the class II facer on the batt buys you a bit of extra margin for higher indoor humidity but still allows for drying of the cavity to the interior.
Make sure to get batts for steel studs as these are wider and will fit snug between the OSB webs.
As for air barrier continuity, at this stage your best bet is spray foam. Have the spray foam contractor spray from the roof deck down to the top plate.
nestpropertiesvt,
Nothing to add to the good advice you got from JGSG and Akos except kudos for having a plan for how you intend to insulate the roof. Most posters with low sloped roofs end up in the Q&A having worked themselves into a corner with their framing decisions before even considering the roof assembly.
Because the R-value ratios are for long-term resilience against moisture concerns, I use the long-term R-value for closed cell spray foam. When freshly installed it may be R-7/in as you calculate, but over time air displaces the refrigerant inside the cells, eventually resulting in about R-5.6/in, so that's the value I use. In your case, 4" would be R-22.4, which is probably close enough to the climate zone 6 rule of having at least 50% of the R-value in th foam layer to be safe, but you might want to increase that to 4.5 or 5" to be safe.
When going for thermal envelope code compliance, I use the higher R-value to limit embodied carbon emissions. And since this is a site about green building, for other readers I'll mention that it's a good idea to never design a house that requires a flat roof, as it can only be done safely with foam insulation, and foam is never a "green" choice due to its high levels of embodied carbon and with spray foam, the risk of curing problems resulting in poor indoor air quality and sometimes requiring full remediation.