Unvented Roof Assembly Successes or Failures?
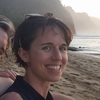
Hi!
We are reaching a point where we are going to have to replace the roof on our 1.5 story century home in the Pacific Northwest. Much like this: https://www.greenbuildingadvisor.com/article/insulating-a-cape-cod-house where the finished attic space is essentially a cathedral ceiling with knee walls.
If we are investing in a new roof, I want to do it right.
I’ve been calling and asking around about installing rigid foam over the roof sheathing and running into a lot of dead ends. I’m starting to wonder if I should keep traveling down this path or just give up?
(i.e. rip out the moldy pink fluff, replace damaged sheathing, slap on some shingles and deal with the fact that I’ll be dumping further money and materials into the underinsulated roofing system that currently exists)
THE MOST IMPORTANT QUESTION:
Whether retrofit or new construction, who here has installed rigid foam over roof sheathing? And more importantly, how do you feel about the results? Success? Failure? Mistakes? Regrets?
GBA Detail Library
A collection of one thousand construction details organized by climate and house part
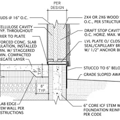
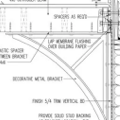
Replies
Are there no real-world examples of retrofitting a 1.5 story cape cod (or similar) with rigid foam on the exterior of the roof sheathing?
if you are retrofitting with exterior insulation I don't see why it would be any different than a standard (cathedral) roof with exterior insulation. Just take a look at how to insulate a cathedral ceiling, you are proposing bringing those half walls into the conditioned space so just forget them in terms of thermal assembly and dont insulate them and go from exterior walls to roof...
Here’s a link: https://www.greenbuildingadvisor.com/article/five-cathedral-ceilings-that-work
Thank you! I've read that article again and again and again and tried to explain the various principals when talking to remodel contractors but most give me a blank stare. There are new build contractors that are familiar but they aren't interested in retrofitting an old house. I am only considering it though because our current roof is showing signs of failure and I would really hate to reinvest in the same construction principals when I have this potential opportunity and no intention or desire to ever move.
Hollee,
Here's an example of success:
https://www.greenbuildingadvisor.com/article/solving-an-ice-dam-problem-with-exterior-rigid-foam
Thank you so much for responding and sharing!!
holleecee,
The problem with exterior foam is that although the approach yields a very well performing roof, the insulation comes with complications. The foam has to be quite thick to avoid condensation on the sheathing below - and thick foam is difficult to fasten the new Layer of roof sheathing through into the structure. It also means maintaining the continuity of the air-barrier from roof to walls, a thickened fascia, moving the gutters, and a longer period when the roof is exposed to the weather. In short it's a pretty extensive and expensive process, which I think is why you don't see it used very often.
Two summers ago I did a re-roof of a building where the roof top foam had a lot of damage from a combination of moisture and carpenter ants. We thickened the foam layer from 1" to 2", which was relatively easy as the roof deck was 2"x6" t&g, and the slope was 2/12. In those almost ideal conditions it went very smoothly. It would have been exponentially more complex with a conventionally framed roof, thicker foam, and a steeper pitch.
Thank you so very much for this real world example. I really appreciate it! As said elsewhere, our current roof is showing signs of failure -- signs of moisture in the pink fill that was stuffed between the rafters, sheetrock screws that are rusting, rain in the can lights, signs of moisture on the sheathing, and my gutters are filling with asphalt granules -- so I am very interested in figure out how to do this right for the longterm, especially, since we have no intention of ever moving as we absolutely love the house otherwise and it's in an area that would be impossible to afford relocation.
Quite a few years ago I did a foam over roof sheathing project on my garage when it was converted to an office. It's in the PNW and the shape is similar to a Cape. The ceiling was vaulted so insulation space wasn't what I'd consider adequate. Even with the foam and rafter insulation it's probably not but it's not full time conditioned living space. I'd seriously question a lot of the project details today, but since it wasn't full time living space and low moisture load inside it's worked just fine.
The mechanics of adding the foam on the outside wasn't too difficult. There are details to be found online that can go into how to address the extra thickness of the roof and how best to attach it. Roofing companies like to keep things simple and fast as it's a pretty low margin fast paced business so I don't think most of them would want to get into any complications like this. You'd probably be better off finding another contractor to do the foam and decking so that the roofers show up to what appears to them to be just another roof deck ready for shingles.
That said, what's the problem you're trying to solve here? Worn out shingles? Leaks? Cold drafty space? I think you might want to have a more direct look at the problem first before settling on a solution. There are some standard approaches to all of those problems, even with a 1.5 story Cape and its inherent issues.
Thank you for your detailed response Andy and suggestions on how novel ways to approach the build. I've actually roofed other houses I've lived in before myself but I'm not feeling as physically capable of taking on this kind of project again and the rigid foam details also gave me extra pause. I'm not a contractor just a (formerly) ambitious DIYer.
My roof/attic observations are as follows:
This is currently a 10-year old re-roof (shingles over shingles done before we bought the place) and I'm noticing that my gutters are filling with asphalt granules. It seems that the roof deck is getting unbelievable hot and maybe deteriorating the shingles at a more rapid rate? Temp readings indicate the attic space gets to be about 120 degrees sometimes in the summer if we don't have the mini-split on. I have no idea how hot the roof is getting. There are no missing or broken shingles. The granule shedding is just an observation that I am aware of.
There are can lights. (Ugh!) Sometimes the can lights rain because of condensation build up in them. Many of the screws securing those can lights to the ceiling have completely rusted out. Some of them are just brown powder.
The finish on the sheet rock is developing bubbles that are brittle and flake off. On about 25 percent of the fasteners, the drywall mud on the sheet rock screws has popped off exposing rust colored screws. I'm starting to notice cracks along the seams of the sheet rock. And in a few areas there are light brown residue droplets that you can see the path the droplets traveled. I am obsessively touching the walls and sometimes even pull out the moisture meter but I don't ever feel moisture or get a high moisture reading. However, the droplets suggest otherwise to me. The paths do not originate at the fasteners.
I know that the rafter cavities are stuffed with pink fiberglass with no vent channels other than the porosity of the fiber fill. There are soffits at the eaves and a continuous ridge vent at the peak. The pink fill that is laid on the ceiling joists in the kneewall space and up the back of the kneewalls is not moldy but I am definitely concerned about the integrity of the fill that is sandwiched between the sheet rock, rafters, and roof sheathing.
Those are my current observations. I want to address air sealing and if/when we are due for a re-roof then also increase the insulation. We are also in the PNW.
What thickness of foam & type do you have to install to meet code?
If your plan is for thick exterior foam. You might find this article interesting.
https://buildingscience.com/documents/insights/bsi-056-leiningen-versus-the-ants-redux
Walta
That was one of the articles that spurred me to ask the question about real world installs.