Vapor Barrier: existing gypsum sheathing in Texas

First, thank you all for the incredible information you all share on this site; I am a big fan!
My 1978 house is in The Woodlands, TX; just north of Houston and is mostly constructed with brick veneer, a 2″ air gap, gypsum sheathing and 2×4 framing. The house does have portions of cedar/cypress board siding. I have Heating, A/C +D with an UltraAire dehumidifier ducted to the system.
We still have a humidity problem during the summer. Aside from the walls, its known the ducting is leaky too.
What I would like todo is to add insulating sheathing and an air barrier to the walls and attic (not currently conditioned space, want to keep roof ventilated). I am already going to gut the interior side of the walls to patch any holes in the sheathing.
Ideally I guess, i would go through the exterior side of the wall but that would be crazy with removing the brick veneer. So how can this be done if possible from the interior side?
Thanks in advance!
GBA Detail Library
A collection of one thousand construction details organized by climate and house part
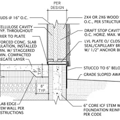
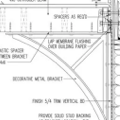
Replies
Zefrum,
First of all, the wall assembly you describe -- one with brick veneer (a so-called "reservoir" cladding) and vapor-permeable sheathing (gypsum sheathing) is at risk for problems related to inward solar vapor drive. Problems are most likely to show up on east, south, and west walls -- not north walls -- especially on walls with interior glued-on mirrors or wall cabinets. For more information on this phenomenon, see When Sunshine Drives Moisture Into Walls.
To the extent that your wall assembly has avoided moisture problems, you can credit either (1) the presence of a good air gap between the brick veneer and the WRB, and (2) the lack of interior-side vapor barriers.
If you plan to open up your walls from the interior, you might want to consider insulating using the flash-and-batt approach. Installing a layer of closed-cell spray foam against the interior side of the gypsum sheathing will reduce the risk of inward solar vapor drive. For more on this approach, see Flash-and-Batt Insulation.
Thank you Martin.
Basically this method would be to use spray foam just to minimally cover the surface so batt insulation can fill the stud bay correct?
Is there a more eco friendly method than using a foam product that can provide the same bennefit?
Would a paint of a spray sealant such as Knauf's ECOSEAL Plus work well?
Thanks!
Zefrum,
Knauf Ecoseal is a sprayable caulk. While Ecoseal can be used to seal cracks, it is not an insulation material. Nor is it a vapor barrier. For more information, see this article: Air Sealing With Sprayable Caulk.
The main reason to use closed-cell spray foam is that it is a vapor barrier in addition to being an air barrier and an insulation material. You want a vapor barrier (or at least a vapor retarder) in this location to address inward solar vapor drive.
Zefrum,
Check out Lapolla Soltice closed cell foam. It uses a new blowing agent that has much lower GWP than older products.
Thank you Martin and Steve; I appreciate your quick responses.
Is there anyother liquid applied material that can give me a a vapor barrier / retarder that is compatible with rock wool batting? Could I use Prosoco R-Guard or Poly Wall Liquid Wrap 2300, again on the interior side of the ext gypsum sheathing? I want to avoid srapy foams.
If I must use a closed cell spray foam to prevent solar driven vapor ingress, what are your thoughts on the DIY'er install using Tiger Foam? (Tiger Foam™ E-84 Fast Rise Formula)? Is there really no concern about off gasing after these products are cured (after an hour for Tiger)?
One last question: if I use closed cell spray foam as my WRB, would it still be the case that vapor can travel through the stud to the sheet rock? -I cant cover the stud's length edge with foam for a straight wall right?
Zefrum,
Q. "Could I use Prosoco R-Guard or Poly Wall Liquid Wrap 2300, again on the interior side of the ext gypsum sheathing?"
A. I don't recommend either of those products for this purpose, since both of those products are vapor-permeable.
If you really want to avoid spray foam, you might consider the cut-and-cobble approach. For more information, see Cut-and-Cobble Insulation.
Zefrum,
Q. "If I use closed-cell spray foam as my WRB, would it still be the case that vapor can travel through the stud to the sheet rock?"
A. The closed-cell spray foam wouldn't really be your WRB -- it would be an air barrier, vapor barrier, and an insulation layer. To answer your question: Yes, water vapor can travel through studs -- but the amount of water vapor that would pass through the studs wouldn't be significant enough to worry about.
The vapor permeance of framing lumber is comparable to that of closed cell foam, so with a 1" flash foam the 1" path through the studs around the foam layer isn't moving appreciably more moisture via diffusion than the foam itself. And it's only ~25% of the total wall area (typical for 16" o.c. 2x4 studwalls), so even if the species used has twice the vapor permeance of closed cell foam, it's still not going to make a practical difference.
Products like Tiger Foam will work just fine if you pay attention to the instructions, particularly the temperature of the surfaces and the temperature of the tanks. The tanks drop in temperature as the foam is released- keeping the tanks in a tub of water at the correct temperature can keep the chemical temps more uniform, for a more consistent result.
In my area by the time you've bought the extra spray tips and safety equipment it's cheaper to hire a pro than use DIY kits whenever there is more than 1000 board-feet of foam. That is sometimes true even at 600 board feet (the size of the largest kits). The pros have several advantage over DIY kits, such as electronic temperature control of the chemicals, better spraying guns, more experience, etc.
SFAIK the DIY foam kits are all still using HFC245fa as the blowing agent, and not the much more benign HFO1234ze (Honeywell Solstice ™) being used by Lapolla's Foam-LOK 2000 4G Solstice or Demilec's Heatlok XT High Lift products. But if contractors with those products are rare in your neighborhood (Demilec's US operation is based in TX, Lapolla is based in Houston, so they're probably NOT rare), it's not a major crime against the planet to install a flash-inch to gain the benefits of lower vapor permeance and better air tightness.
Thank you Dana; I was concerned bout the actual costs of these kits too. I can only do one room at a time though, and so it wouldnt be practical to have an installer come out for 15 rooms, one at a time. Its difficult to have best practices when constrained to living in the house while renovating.
Zefrum,
Q. "Should I install the rigid foam as close to the sheathing as possible... or should I leave a gap between the rigid foam and the sheathing? And should I add a vent hole to the sheathing too?"
A. Install the rigid foam as close to the sheathing as possible -- no gap, no vent holes. Seal the perimeter of each piece of rigid foam, as described in my article, Cut-and-Cobble Insulation.
Martin, Thank you for the idea!
I was actually considering this method but for one didnt know how to call it and two I am concerned about which sub-method I should use.
So, if I use this cut-and-cobble method in my area, should I install the ridgid foam as close to the sheathing as possible; maybe even glue/sprayfoam it to the sheathing (to reduce condensation potential/allow liquid water to escape)? Do I also seal the cut edges somehow before spray foaming the peice in place?
-Or-
Should I leave a gap between the ridgid foam and the sheathing? And if so, should I add a vent hole to the sheathing then too?
Thank so much! I almost have a complete plan of attack ;-)
Got it! Thank you so much!
To save money and be nicer to the planet, using reclaimed foam (any type) for the cut'n'cobble project is the way to go. A cut'n'cobble can even tolerate some really cheap beat-up stuff with broken corners, etc, since it's going to be cut down to size anyway. But even near-perfect used foam is pretty cheap. eg:
https://houston.craigslist.org/search/sss?query=rigid+foam