Vapor barrier location / need in unit above unconditioned garage

Hi all,
Building an unconditioned garage + ADU above in Nova Scotia. The ADU will have double stud walls with intello (vapor barrier) on the interior of the service wall. That’s straightforward enough. We’re I’ve gotten myself confused is the two following assemblies:
– Insulated floor. I was planning on putting intello on the underside of the floor trusses, and blowing in cellulose. However, I’m now realizing that order puts the vapor barrier on the very cold side of the floor. Perhaps this is not an issue as the plywood subfloor will limit vapor drive into the floor?
– Unconditioned garage exterior walls. They are standard 2×6. I was planning on using batts with intello stapled to the inside of the studs. However, intello isn’t cheap, and perhaps there isn’t much value in having a vapor / air barrier in that location given that the conditioned spaces will be wrapped nicely with intello?
Thanks in advance for any insight you can provide. I’ve clearly reached the limits of my vapor barrier knowledge.
GBA Detail Library
A collection of one thousand construction details organized by climate and house part
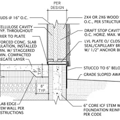
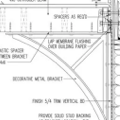
Replies
In cold climates the simplest way to do insulated assemblies is to have a vapor barrier or retarder on the interior side of the assembly and allow them to dry to the exterior. If they're not capable of drying to the exterior you have a "Wrong Side Vapor Barrier" or WSVB and on the cold side you have to have enough continuous, impermeable insulation to prevent condensation.
The question is whether an unconditioned garage creates a WSVB. I don't know. The rule of thumb for unconditioned crawl spaces is that unless at least 50% of the wall space is open it should be considered incapable of drying. A garage is a little different because you have that big garage door which can open, but if you're parking cars in there they bring in a lot of moisture.
The safest assembly would be to assume it's a WSVB and put continuous foam board on the cold side. Since it will stay warmer in the garage than outside you don't have to make it as thick as on an exterior wall. If you think your garage is going to be able to adequately dry then you can use fluffy insulation with a vapor block on the warm side. You can use faced batts with the facing pointing up. With unfaced or blown insulation it's tricky if the floor is already built, what I've done is 1/2" faced polyiso against the underside of the subfloor.
For the walls, I'm not sure. My inclination would be unfaced to aid the drying of the garage.
Thanks, DCcontrarian. Fortunately, the floor system is not yet installed so I can shift my approach. Perhaps as you recommend faced batts (face up) would be a safer assembly, even if I have to tradeoff a little r value going fiberglass instead of densepack cellulose.
Ry_Buc,
I don't think this floor is any different than any other raised one. This article deals with those situations: https://www.greenbuildingadvisor.com/article/insulating-a-wood-framed-floor-assembly
The assembly typically suggested is is a well sealed sub-floor, with batts or cellulose in the joist bays, and a layer of foam on the bottom to reduce thermal bridging.
Malcolm, I think we arrive at the same place but get there by different paths. I'm in favor of continuous insulation as the bottommost layer of raised floors because almost always they end up being wrong side vapor barriers and you need the continuous to prevent condensation.
I don't find the thermal bridging argument compelling. A 2x12 has an r-value of 14, which isn't nothing. The 2018 code only requires R30 in zones 5 and 6 , R38 in zone 7. If you figure on an air layer of R0.5, if it's 72F in the house and 30F below you get a surface temperature of 70.6F for the joists and 71.3 for the bays, I don't think that's a noticeable difference.
Generally floors that are cold are poorly air sealed, and the continuous insulation also helps with that.
Since R-30 is only 7-1/4" thick, Joe Lstiburek recommends installing it at the bottom of the bay, so there is a layer of air between it and the subfloor. He claims that tends to equalize the temperature of the floor across the subfloor, I haven't had a chance to evaluate his claim.
DC,
You may well be right.
Martin addresses Joe L's suggestion to leave a space in the article I linked to under the heading "Counterintuitive advice on air gaps".
Thanks, Malcolm. Good overview in that document. The drumbeat of continuous insulation on the bottom of the trusses is getting louder. Going to see how I can make that happen.
I like running 1x3 strapping perpendicular to the joists between the continuous insulation and the drywall. You can pin the strapping at each end and use them to hold the foam overhead while you get it positioned, the foam is so light it doesn't take much to hold them up. Then when you're doing the drywall you have a nice meaty 1x3 to sink the screws into rather than trying to hit a piece of 2x through the foam.
It also allows you to put thin junction boxes between the foam and drywall without penetrating the foam. The wire can be run in that space as well which means the wiring doesn't interfere with the insulation.
Ry_Buc,
I'm retrofitting a garage/shop to have living space above (Zone 6, Montana) - similar to your situation, but I'm stuck with some existing constraints. My assembly will look like this, starting from the lower (garage) side:
* 3/4" plywood (I want to be able to screw things to the ceiling anywhere I want), then
* Double layer 5/8" Gyp, fire-taped (for some fire protection and for soundproofing), then
* 2x4 strapping, 16 o.c., perpendicular to framing, with rigid foam (I have NGX on-hand, I know that's not ideal environmentally) pushed into the space in between 2x4s, then
* 2x8 framing (existing, 24" o.c. but somewhat irregularly spaced, hence the strapping)
** In the 2x8 joist bays, I'll have a couple layers of NGX, seams staggered, Great Stuff around the edges (so, basically cut-n-cobble in the floorpack), with the remainder of the space filled with cellulose, then
* 2x6 T&G plank, which is both the subfloor & finish floor of the living space above.
The living space above (and sharing one wall with the garage) will be conditioned, the garage will only be conditioned intermittently with a Hot Dawg Heater or something.
For the exterior garage walls, I was thinking I'd cut-n-cobble the stud bays, then a layer of 1.5" rigid continuous, then 1x strapping, then double 5/8" Gyp., then 3/4" ply for a finished surface.
The exterior wall framing is all over the place, hence the strapping, to make the gyp/ply easier to install.
For the interior garage wall, which will be shared with living space, I was thinking a similar thing. From the conditioned side to the garage side:
* 1/2" Gyp, then
* 2x4 framing w/ batt insulation (not sure if it matters if they're faced or not), then
* 1.5" rigid, continuous (again, I have a buncha NGX on hand), then
* 1x strapping, horizontal, maybe with 3/4" EPS or something between strapping?, then
* Double layer 5/8" Gyp, fire-taped, then
* 3/4" ply (again, so I can attach anything anywhere to the walls
That sounds like a bomb proof assembly, paulmagnuscalabro! I may try to incorporate some rigid on the bottom of the trusses like you're doing.