Garage-Meets-House Wall Assembly

Hi I’m remodeling my 1989 house and took the walls down to the studs. I have a garage that shares walls with the living room and one of the bedrooms is above.
What is the best way to rebuild that wall assembly to provide and air right separation between living space and garage that meets code (e.g. fire resistance)
I thought about using 1/2 plywood or zip sheathing and tape it and then install drywall on top of it. Don’t just want to rely on drywall. Are there better materials to build a robust air barrier?
thank you
niko
GBA Detail Library
A collection of one thousand construction details organized by climate and house part
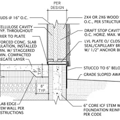
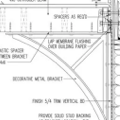
Replies
niko,
Don't fear drywall, it's essentially the go to for listed fire walls. Check out USG's 'wall builder' that shows many different assemblies, and their fire ratings.
https://www.usg.com/content/usgcom/en/design-studio/wall-assemblies.html?facets={%22k%22:%22FramingType_facet_pim%22,%22v%22:[%22Wood%20Stud%20(Load-Bearing)%22]}&facets={%22k%22:%22WallType_facet_pim%22,%22v%22:[%22Interior%20Partition%22]}&facets={%22k%22:%22assemblyProductType_facet_pim%22,%22v%22:[%22Fire-Resistant%20Drywall%20Panels%22]}
Otherwise, your idea about zip/tape and drywall is good. Perhaps even easier is two layers of fire rated drywall offset so that seams don't align, with a good job on mudding and taping. Another option you have is to put an air barrier between the studs and drywall (tyvek) for that continuity, and then you can care a little less about the quality of the drywall.
Thank you for the quick reply.
I like the double drywall idea or even the tyvek approach. However every time I install something on theses walls I’ll worry about breaking the air barrier. I liked the plywood idea since it probably would not contribute too much for air leakage if I have a screw that’s driven into the plywood. Or am I overthinking this?
Niko
I wouldn't worry too much about it. A hole is only a hole if somethings not in there, right? If you screw something into it, air wont get around it. Not a ton anyways. If you move things around on the wall, it's easy enough to repair with a pre-mixed drywall compound.
You mentioned having it down to the studs too, right? Install an air barrier on both sides, so that if one is punctured, you have backup?
LOL - I get it. My air barrier is also the gyp layer, and I worry about the same thing.
That said, the wall between the garage and house is notoriously difficult to seal. What is the top of the stud wall separating them? The trusses as in a one story ranch, or is it a 2 story house? You may consider sheathing one side then spray foaming the cavity and especially the area above the wall which is usually a joist, and usually has a few penetrations.
Not sure where you are at, but in BC we would consider the garage to be unconditioned space, and a vapour barrier would be required on the warm (house) side of the wall. This vapour barrier would typically be detailed as the primary air barrier. As for the living space above, this is a good use of closed cell spray foam in the joists to insulate and air seal. Or, you could seal the floor sheathing as your primary air barrier.
Dont forget to add a CO detector as part of the renovation.
Great thank you. I am in florida so the garage is mostly hot and humid year round.
Regarding spray foam - I am trying to do the remodel without using spray foam due to indoor air quality concerns if it’s not installed correctly.
Niko
While not completely related, you may be a good candidate for a heat pump water heater, if you planned on putting the WH in the garage.
I have thought about it. However I decided to go with Stiebel Eltron tankless electric water heaters. One dedicated for the kitchen faucets and one for the rest of the house. They require a lot of amps (3x40Amp) but work very well.
Back to the ZIP sheathing idea. Are there any concerns with off gassing with ZIP sheathing. From the OSB, the applied coating or even the tapes? The only info I could find was a research paper that was paid for by HUBER, so not sure how objective that is.
Thanks again for all the responses.
Niko
i haven't noticed or heard off any long term off gassing from either zip or zip tape. It has an adhesive smell as soon as its unrolled, but it doesn't last any real amount of time.
You may want to do some research on those tankless water heaters - they often produce a cold water sandwich. There is also a significant problem pairing tankless water heaters with very low flow devices as a 1.2gpm lav sink (which is plenty for a lav sink - I've had 0.5 gpm work fine) will only pull about half of that water from the hot water, and a flow rate of 0.6 gpm is insufficient to cause the tankless water heater to turn on.
Also, at this point you can get significant tax credits for the heat pump WH and people with incomes at or below the $80k range may be eligible to get them for free...
On the zip sheathing, I did not notice any smell from either the zip or the zip tape.
You may also want to head over to Matt Risinger's you tube channel to see the challenges he faced in his own house trying to get an airtight seal between the garage and living space. I think it is in the Real Rebuild series video on the first blower door test...
If all the offgassing is occuring from materials you used on the exterior, anything that comes off is going to dissipate outdoors, and shouldn't have much impact on the air quality inside your home. Some flashing tapes can be pretty stinky, but I don't think the Zip tape is particularly bad in that regard.
If you go with a tankless water heater, a natural gas fired one is really a better choice than an electric one. The electric ones tend to require BIG electrical supplies, which often require service upgrades with older homes, and they aren't very good in terms of overall fuel use, either (i.e. they burn more 'stuff' than using the natural gas directly), unless you happen to be in an area primarily served by hydroelectric generation.
Bill
Tankless water heaters are defined tricky.
First I upgraded my service to 300AMP to accommodate the electric water heaters. Second I picked one that has an activation flor of 0.7 GPM. My smallest fixture is the lavatory at 1.2 GPM. My thinking is if I just open the faucet in the middle it would draw 0.6 GPM from both hot and cold. So it would not activate the water heater. But I think that’s actually what I want. The default is to open the faucet in the middle and that usually for a quick had rinse. No point in calling for hot water here. If I need hot water I turn the handle which then increases the hot water draw to 0.7 GPM im and more and that’s when the water heater kicks in. This is the first time I am installing one so I’m not sure if my thinking is right. But after a few conversations with Stiebel Eltron technical service this is the system I came up with.
Would love to here you thoughts.
Niko
Your thoughts on fixture flow vs tankless activation seem correct.
You may wish to google Tankless cold water sandwich.
Consider also that 30 years ago low flow fixtures were 3.5 gmp; 20 years ago they were 2.5 gpm; 10 years ago they were 1.5 gpm. Now days the engineering of aerators has improved so much that 0.5 gpm is common, and the default of most store bought fixtures is 1.2. In 5 years you may have a difficult time getting a 1.2 gpm fixture.
Also consider that when taking a shower the temperature of the water you want may not be >50% from the hot side. The incoming water temperature in Florida is so high, especially in the summer, that you may want only 10-25% hot water mixed. The Steibel wont activate.
ETA: a. - since this is really off the title topic it should really get its own thread;
b. for those who may just turn down the temp on the tankless to solve for the above issues, to prevent Legionnaire's you need your hot water temp at min 131-135 or you introduce a safety risk.
Yes 100% agree. I have another Thread for hot water distribution where we can continue that conversation
https://www.greenbuildingadvisor.com/question/efficient-hot-water-distribution-system