What insulation type and configuration for an old Victorian would work best?

I have a house, climate zone 5 (southwest PA) that is gutted to the studs. True 2×4 balloon construction. I have put on a new roof which I intend to put closed cell foam. But on the exterior walls, I’m trying to determine best course for insulation. So I have the studs, 1×8 sheathing that runs diagonally foundation to roof line. Covering that is old felt paper, then 1″ wood dutch lap siding. On top of that 1″ foam board, fairly dense, with a dense cardboard and shiny aluminum side facing outward, then vinyl siding nailed into that. The house is heated with a boiler and steam radiators. I put in new windows, bigger than old windows taken out. I have seen the wood siding and I’m guessing it has been covered up for close to 30 years. This 1″ foam board was the only insulation this house had, the cavities between the studs were empty. I want to take the vinyl siding off the house, repair the nail holes and pant it, taking it back to its former self. I was going to spray foam the exterior walls, but have been doing a lot of reading about mineral wool, which has many advantages over others. Spray foam you are dealing with some chemicals and cost. Also within the last year, 3 houses in my area have caught fire, (all early 1900 homes) and that is actually the primary reason I like the mineral wool for the fire break. So that’s the back ground,
So if I rip off the siding can I use a combination of closed cell to seal up the house and install the mineral wool, like the flash and batt system?
Is it a bad idea to take the vinyl and foam board off as that removes a barrier? I would think that having a barrier, then insulation then barrier would cause some problems.
Should just the mineral wool be installed and then place a barrier over that then the plaster board? I plan on installing plaster board and plastering the walls.
GBA Detail Library
A collection of one thousand construction details organized by climate and house part
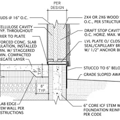
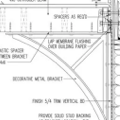
Replies
Robert,
Right now, you have no way to assess the condition of the wood siding that you describe as "Dutch lap siding." It could be in great shape, or it could be in such bad shape that you will need to install new siding.
There is nothing wrong with your plan, as long as your realize that when you remove the 1-inch rigid foam board, you will be making your walls leakier and less well insulated.
If the existing wood siding is in bad shape, you should certainly install new rigid foam before you install new siding -- the thicker, the better -- followed by housewrap, vertical furring strips, and new siding.
You definitely need to come up with a plan to flash around the windows, including (if necessary) a plan for well-flashed exterior jamb extensions.
If the existing wood siding is in good shape, and you want to keep it, you should probably insulate between your studs with dense-packed cellulose insulation. You'll still have thermal bridging through your studs, so you should consider installing interior rigid foam, or perhaps interior horizontal 2x4 furring strips to reduce thermal bridging.
It's nearly impossible to air seal plank sheathing adequately without some sort of air barrier, and while dense-packed cellulose would make it tighter, half-pound open cell polyurethane would be tighter, and probably cheaper too, assuming you're gutting the interior to make the installation (is that how you were going to apply the closed cell foam?) Closed cell foam is an extremely expensive air barrier, and the performance difference between a flash-inch of closed cell + 3" of cellulose vs. a full cavity fill of 4" of open cell foam is negligible. A full 4" of open cell foam only uses as much polymer as 1" of closed cell, and uses water instead of HFCs as the blowing agent.
Using 2 mil nylon (Certainteed MemBrain) as an interior side vapor retarder under the wallboard costs less than 15 cents per square foot (installed), compared to a buck a foot for closed cell foam, and gives the assembly HUGE drying capacity compared to an inch of closed cell foam, but comparable vapor retardency during the winter season when the sheathing is cold.
If either side of the assembly is ever hot enough to light-off the open cell foam within, it's already pretty much a total loss. The extremely high air retardency of foam relative to fiber insulation is an asset in an active fire situation, as is the fact that polyurethane foam does not melt (unlike polystyrene), and would char in place even if it did ignite.
What is your proposed stack-up for the roofing & roof insulation?
To Martin: So interior rigid foam and then the drywall? Could I put plastic sheathing or something like Tyvek and then the drywall?
To D Dorsett: the house is completely gutted now, down to the studs, so install of spray foam would be easy. You mention using the Cetainteed membrane at .15/sq ft, were you also using the open cell phone in the cavities between the studs? Foaming complete house is about 8K$, and using mineral wool is about 2K$. I had a new roof put on, and had it sealed up and I do intend to close cell spray the roof deck.
Robert,
Before we give advice on the best type of insulation to install between the studs, we need to know if you intend to leave the existing exterior 1-inch rigid form, or whether you intend to remove it.
Martin,
I'm going to take off the vinyl siding and put on hardi plank siding. That was the very first plan that I had, and after you brought up that it may not be in good condition, I'm shifting back to the original. The vinyl on there now looks irregular and out of period. I can put a style of hardiplank on there that looks a lot better. Already did the dormers that way, might as well make the rest of the house that way.
Thanks,
Robert
Robert,
In Comment #3, you mentioned adding interior rigid foam. But considering what you wrote in Comment #6, I'd advise you to add more exterior rigid foam rather than trying to add interior rigid foam.
You intend to use closed cell foam on the roof deck, understood, but what else is in the stack-up? An fiber insulation, gypsum board, etc?
Rock wool batts are not designed to fit rough full-dimension framing. Even if the studs are at standard 16" on center spacing, the extra thickness of the studs would the batts to be narrower than those designed for milled framing which makes it more difficult do to a good job. In my area 3" of open cell foam costs about as much as 1" of closed cell foam, and would air seal better than 1" of closed cell foam. Fiber insulation is fine if the sheathing of the house can be made air tight, but it's better to use blown or sprayed, not batts.
In my area a full-depth 4" of open cell foam typically comes in at about $1.20-$1.40 per square foot, whereas 1" of closed cell foam comes in at about $1.00-1.20 per square foot, which makes any "flash and fill" with 1" closed cell foam + fiber more expensive. It's often possible to air seal the plank sheathing by other methods, which could make another half-inch to inch of exterior foam, and using damp-sprayed cellulose (or blown rock wool, but that's usually more expensive) in the cavities a lower-cost/higher performance option. And, there is exactly as much plastic in 4" of half pound open cell as there is in 1" of 2lb density closed cell foam- the outgassing potential doesn't really change by going to the lower density foam- it's the same amount of "stuff".
The existing exterior inch of foam is not sufficient for dew point control on a full 4" cavity depth of other insulation. A flash inch of closed cell on the interior would be adequate dew point control at the foam/fiber interface, but would limit the drying capacity for the sheathing. Adding as little as another half-inch of rigid foam on the exterior (making it 1.5" total) would be enough to let you use fiber or open cell foam in the cavities without the expense of interior vapor retarders, and would retain ample drying capacity toward the interior for the sheathing.
To Martin: It would be easier to add exterior foam and then the hardiplank. Adding interior rigid foam would require a whole new level of demolititon and reconstruction. I like the hardiness of the hardiplank also and it is relatively not too expensive.
To D Dorsett: I plan on putting 5/8 plaster board on the roof deck after closed cell is installed and then 3/4 tongue and grove over that.. After making that decision I did read somewhere that this should be sealed somehow. I have not installed foam or plasterboard yet. There are no vent spaces in the roof, and plumbing vents or any breaks in the roof have not been determined yet. I do plan on using this room for the master suite. I see your point about different combinations of insulation and will stick with the open cell foam in the exterior walls, then the plaster board. This is a real learning experience, thanks for all.
How much closed cell foam is going under the roof deck? To hit the IRC 2015 code-minimum of R49 takes about 8", which for most products would have to be installed in four lifts of 2" each to do safely, and with high quality. That much foam is both dauntingly expensive, and environmentally damaging.
In climate zone 5 in an unvented ceiling assembly as long as 40% of the total R value is closed cell foam, the rest can be fiber insulation, as long as it is reasonably air tight toward the interior (the proposed 3/4" gypsum board would be fine, if sealed at any plumbing & electric connections, etc), and has a vapor retardency less than 10 perms (paint the gypsum board with latex primer- one coat is sufficient). A stackup of 4" of closed cell foam at the roof deck would be R20-R24, and sufficient to be moisture safe with R30-R35 of fiber insulation (at less than half the cost of the foam) between the foam & gypsum would bring it up to code at lower expense, with only half foam, for only half the environmental cost of the polymer & blowing agents.