What would you do? Keep steam, convert to hot water, or go straight HVAC?

Hi all,
Good morning. I purchased a historic home recently that needs mechanical upgrades and a large renovation. The property is 4 units and I would like to keep it that way. It totals 5700SF with a large amount of historical details remaining which I am looking to keep in tact. The house had a fire (prior to me purchasing it) on the ground floor unit, which spread a bit to the 1st floor. Knob and tube wiring throughout. I just hired a electrician to upgrade the service as well as the entire house. We spent a lot of time together on this to be sure to keep the damage minimal. My dilemma is the heat.
The house currently has a huge boiler and a steam system. I have all but two of the radiators, the rest are there.
There are hot water heaters on every floor which I would like to remove and have them in the mechanical room. Majority of them are located in the kitchen of each unit. Ideally I would like to separate all of the utilities to be on the tenants expense. I have narrowed down a few of my options and open to further suggestions and input.
1. I keep the steam system and forget about separating it and zones. I either get the system working as best as it can or upgrade the boiler. I guess this would be my cheapest option but still leaves the house without air conditioning, and I still have all of the huge steam pipes in the bottom floor apartment I am looking to rebuild and finish. I also don’t know what kind of shape the chimney is in and may need a liner which would be a large added expense.
2. I switch over to a hot water system with a condensing boiler. Since this is a historic home, I really do not want to put baseboards around the entire house. It would completely ruin the look. I would have to purchase all new radiators. I could either run them off of one large boiler or 4 separate but maintaining 4 boilers is certainly more expensive then one. I would look to run the new system in the exact spot as the steam was previously. This still leaves me without any air conditioning throughout the entire house but I believe I can get the ceiling height I need back on the ground floor.
3. Go straight HVAC with wall mounted hyper heat units in the ground floor apartments (they can’t be on the floor) and install floor units everywhere else in the exact spots where the cast iron radiators are now. I have these hyper heat type of units on my own home and have no complaints but this house is much larger, much older, and it is much colder in that location. This would be a primary heat source and the most expensive I would imagine but it also gets me AC in every apartment and full ceiling height in the basement apartment.
Thoughts? Thank you!
https://forum.heatinghelp.com/discussion/167919/what-would-you-do-keep-steam-covert-to-hot-water-or-go-straight-hvac/p1
GBA Detail Library
A collection of one thousand construction details organized by climate and house part
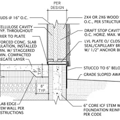
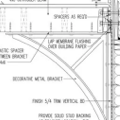
Replies
>The house currently has a huge boiler and a steam system. I have all but two of the radiators, the rest are there.
I don't know what that means?!
If you insulate the house and the windows all at least have storm windows on them you may be able to use the antique radiators for a hot water (even a condensing hot water) heating system. Most steam boiler systems were CRAZY oversized for the heat load even prior to insulating and other thermal upgrades of the house, designed to be able to heat the house even with the single pane windows cracked a bit open for ventilation. It may be possible to run them off water heaters or combi-boilers. Many steam boiler radiators were painted silver or gold to reduce their output (by 15% or more!), or covered over with something to reduce convection. Painting them any non-metallic color and removing any covers would restore their full output, and they can emit enough heat at some temperature much lower than 215F steam.
The only way to narrow down on the credible options is to run a room by room, zone by zone heat load calculation on the "after" picture of any intended building envelope up grades. Without it you're shooting in the dark, and likely to end up spending too much on oversized or inappropriate equipment.
A pretty good upper bound on the heating & cooling capacity requirements can be had using online Manual-J tools such as loadcalc.net or coolcalc.com. When using those tools be fairly aggressive on air tightness & insulation assumptions or they'll oversize it by 50% or more.
With the load numbers in hand you can then estimate the water temperature at which the radiators would actually meet the load requirements based on their "equivalent direct radiation" square feet (EDR') which can be estimated using this guide:
http://www.columbiaheatingsupply.com/page_images/Sizing%20Cast%20Iron%20Radiator%20Heating%20Capacity%20Guide.pdf
With the ratio of the calculated load to the EDR', use the nomograph on page 2 to come up with the water temperature needed to heat the zone with those radiators.
If re-using the rads is too big a PITA, you'll still need the load calculations to appropriately size a ductless heat pump solution well enough to deliver it's nameplate efficiency numbers. If running the load numbers is too big a PITA, hire a qualified third party who is NOT an HVAC installer to run them for you using a professional tool. Use an engineer or RESNET rater, someone who make a living & reputation on the accuracy of their numbers for that service rather than making it installing & maintaining equipment. Only 19 out of 20 HVAC installers know how to run a load tool, and many of them still have thumb on the scale, not quite trusting the tool to get it right when using aggressive rather than conservative assumptions, thus oversizing the equipment (often woefully so.)
Hi Dana,
Thank you very much for the reply. Greatly appreciated and helpful. Can you recommend a good 3rd party engineer who would be willing to go to the lower Hudson Valley near Beacon NY in Newburgh?
The house has a 450,000+ BTU boiler. It needs to be thrown out. Switching the radiators over has lots of mixed reviews. Many people say they would leak. I have all of the cast iron radiators but 5 or so were stolen out of the house prior to me purchasing it.
I have gotten estimates for full HVAC and running 4 separate boilers with homeruns and the cost are very close to one another with the HVAC being 7k more but I would have AC for the entire house.
The maintenance on those units, 16 heads in total, would be costly and I would have to worry about tenants taking care of them. The steam pipes would all need to be rerouted and reinstalled if I went that route.
I am trying to figure out the envelope now but its tricky if you see some of my previous post.
Id ideally like to hire a professional for this.
Be absolutely sure you get ALL of the K&T wiring replaced. It seems to have a habit of getting randomly spliced into other things where you’d least expect it. You don’t want to have any surprises down the road.
I’d switch to a hot water system, such a system will likely be much easier to zone. You’ll likely get the best efficiency for the building overall with a single boiler, although you might (might) be big enough to size things as two boilers, one sized for 1/3 and the other for 2/3 capacity System capacity. Doing it this way gives you three levels (1/3, 2/3, and both together for full power), so you can keep a boiler running in its most efficient operating range for the maximum range of load conditions. I frequently size commerical systems this way. You also have a little bit of redundancy in case of a problem with either of the boilers.
I suspect you’ll be able to reuse the existing radiators with hot water. Temperatures and pressures for the hot water system are both lower than for steam. Just be sure you have the “two pipe” radiators and aren’t using a single-pipe steam system where the supply and return use the same pipe.
If you centralize all the water heaters, you’ll almost surely want to install a recirculating loop so that your tenants don’t have to wait forever for hot water. You may be able to do this using a thermosiphon but I’m not sure of your layout so be careful. A pump will always work. You’ll have efficiency gains using a single large unit over multiple smaller ones, but you would not be able to cost effectively bill each unit for hot water consumption that way.
You can setup an AC system and still use hot water heat. You might want to stay with hot water heat for two reasons: some people really like radiant/hydronic heat, and it’ll keep your historic look.
Bill
Justin,
The common way around here for smaller rental units is a hydronic air handler with standard ac unit. The heat comes from a high capacity tank water heater (standard power went units, nothing fancy except the higher BTU) which also supplies your hot water. Tenant pays for gas. All the equipment is inside the unit (laundry room is a good spot) making plumbing runs and ducting short. The setup is pretty compact, roughly the size of a stacked washer/dryer. Relatively low maintenance, the thing that occasionally goes is the power vent fan on the tank.
I would just stick with whatever is the cheapest to install and allows individual metering. Getting a non functioning steam system back up and running or converting to water is a lot of cost for very little benefit in this case.
@Zephyr7 - The house is being completely rewired. No live knob and tube will remain.
2 boilers is an option but will be costly and I have the one pipe radiators. The cost for 4 boilers with everyone paying their own heat is only 7k less without the cost of all new radiators then going full HVAC. Doesn't seem to make much sense to do this financially although I agree, radiators would look correct in the house.
@Akos- The house is 100+ years old in excellent condition other than one floor which happens to be the basement. Plaster throughout in excellent condition. It wouldn't make any sense to destroy a gorgeous old home to put in forced air and ductwork. This is not an option for me.
Cheapest heat to install would be new steam and reroute some piping.
My guess is 15-20k for steam. Everyone would be on my dime and no zoning. No AC
Hot water with 4 separate boilers- 30k without radiators. Still no AC
HVAC- 37k- Everyone on their own zone, own meter, and both Hyper heat and AC
Justin,
I can understand not wanting to destroy a century home. In a similar century home (no insulation, double brick walls, new windows) with roughly 900 sqft apartment I put in a single centrally mounted wall mini-split system for ac and kept the existing rads. The rads were already there and working, just swapped out the low efficiency boiler to a condensing tankless hotwater heater.
With the single minisplit, in the summer, there is a fair bit of temperature variation inside the units but nobody complains, plus it takes the humidity out, which is what is the key for comfort.
The rads are not zoned, it took a fair bit of time to get the heat even. The tenants use the mini split for heat during the shoulder season when the house heat is off.
Hotwater is electric tanks in the basement, tenants pay electricity. The long runs meant a fair bit of wasted water, ended up adding in a mixing valve to the toilet water feed, if somebody flushes the toilet, it will first pull the cold water from the hotwater lines.
Best of luck.
If the heat load of the individual apartments is within the output of a 76,000BTU/hr burner water heater it can be cheaper to install 4 water heaters than a couple of high end boilers with all the zone controls. The small hydronic air handler option Akos mentioned can work that way, but if AC isn't a priority it's cheaper to install enough fin-tube baseboard capable of delivering the full heat load at domestic hot water temperatures.
Are you going to insulate after getting rid of the k & t wiring?
If a bunch of the rads have already gone to the scrap yard it's probably not worth reworking the steam system. This is doubly true if any of the steam distribution pipes are in exterior wall cavities. Steam boilers have to be sized for the radiation rather than the heat load, and a 450 KBTU/hr boiler is more than 2x oversized for the likely heat load even prior to any building upgrades, probably more than 3x oversized after tightening up.
It's unlikely that you would be able to heat the individual apartments with reasonable heat distribution with a single cold climate mini-split per unit. Room by room load calculations are critical for figuring this out.
It sounds like you're thinking about punting on this rather than running the math. A couple of punts that will probably work:
Punt #1:
A big combi boiler that can modulate down to less than 20K-out such as HTP's EFTC-199W or a Navien NCB-210e or 240e will have more than adequate space heating capacity and can still fill a tub at a reasonable rate. It takes at least 90' of typical baseboard per zone/unit to run a 20K min-fire boiler at condensing temperatures without cycling. With the smaller Naviens it takes less radiation- divide the minimum fire input by 200 to come up with the approximate length of baseboard in feet. (The smaller HTP has a higher min-fire, needing more baseboard.)
Let them cool with window-shakers.
With four identical units operated as a single zone per unit that should come in under $30K, maybe under $20K in competitive bidding.
Punt #2:
Without knowing anything about the size and configuration of the four units, it's likely that a 2-ton 3 zone multi-split per unit would cover the loads without being ludicrously oversized, and with reasonable distribution if you place & size the heads correctly. Newburgh's 99% outside design temp is +10F, so the +5F capacity numbers are good enough.
http://meus1.mylinkdrive.com/files/MXZ-3C24NAHZ2_ProductDataSheet.pdf (delivers 25,000 BTU/hr @ +5F, rated down to -13F)
http://portal.fujitsugeneral.com/files/catalog/files/24RLXFZH3.pdf (delivers 25,500 BTU/hr @ +5F, rated down to -15F.)
In my area four of those all installed at the same time/place would come in under $30K in competitive bidding. YMMV.
Hi Akos-
Thanks so much for your contribution. I was at the house today when demo was being done to the basement apartment. The steam system definitely has to go. Pipes everywhere! I can cross that off of the list for options. That leaves me with zero heat, an oversized boiler, and single pipe radiators that can not be switched out to be hydronic with 4 apartments and a common area to heat.
All-
My HVAC guy is suggesting to just swap out the cast iron radiators for floor mounted Fujitsu units. I agree, so it wouldn't be one per unit.
The basement is roughly 1000SF
1st floor- 1700sf
2nd floor - 1700SF
Top floor 1200SF
There would be a unit in every room. Here is what he said:
The basement consist of 1 12k Wall hung and 2 7k wall hung with 1 36k outdoor unit
the 1st floor would consist of 1 12k floor mount with 4 9k floor mounts with a 45k outdoor unit
Second floor the same as the first
3rd floor the same as the basement
Although I believe the hot water boiler heat would be the best for this climate, it makes no sense financially to introduce two separate systems. Especially considering the fact fin type baseboards are not an option and would destroy the look of the house. Strongly leaning towards going straight HVAC. Open to suggestions.
Dana,
Thank you! I like the #1 suggestion but I would need to purchase radiators. I believe that would be quite costly, no? I have to ask my plumber this but I am pretty sure it was close to 30k without the radiators. I believe this would possibly cause more damage to the house and walls this way as well. Don't forget, the top 3 floors are perfect and the basement apartment is a gut reno. Pics would be very helpful but the site will not allow uploads.
Dana,
If I went with a big combi boiler, could I have all units in a mechanical room in the basement running up to each apartment without doing too much damage? I want to run anything new exactly where the steam pipe risers were, whether HVAC lines or PEX . I would box them out so I didn't have to mess with any ceilings or walls. I am going to have my guys rip out the steam system and there are already holes in the floors from the risers. The radiators would get swapped out with floor mounted Fujitsu's or hydronic radiators. Hope this makes sense.
My plumber did suggest combi units at first but he said he wanted to install them on each floor with baseboards which would destroy the look of the house. If I went with hydronic, they would have to be radiators and I would really like them in a mechanical room. I am tight on closet space as it is. 95% sure all pipes are a straight run up from the basement currently for the steam.
Panel radiators could work instead of baseboard, and keep the original feel with a modern twist. You could put them where the radiators were and run 1/2" or 3/8" pex to each one. You can get different styles that have various BTU densities (some are triple layer with convector fins between the panels for max BTU).
Putting combi's in the basement might cause unreasonable delays in hot water getting to the furthest apartments. If you do look into if you can run a recirc pump, some combi's don't play nice with recirc, or require you to install a buffer tank.
Even if your HVAC guy says he'll do a heat loss (especially if you go mini-split), I would strongly advise paying one of the more highly rated professionals to do an independent one. You'll likely more recoup the cost of the heat loss calculation in more accurate equipment sizing (usually smaller). Your tenants will also enjoy better comfort and efficiency with properly sized equipment. It might help direct your reno efforts to deal with any major factors affecting the heat loss.
Sizing mini splits requires a bit more effort than just matching the btu output to the heat loss, since the heating capacity varies on outdoor temperature, and multi head mini splits can have a sizing diversity (sum of heads might be 80-130% of outdoor unit capacity). It's a mistake just to look at the named size, since the actual capacity can often be much higher at the outdoor conditions that matter, or lower in extreme OA conditions.
Depending on the size of the original steam pipes, you may be able to use the existing vertical runs as a chase for new PEX lines — fish the PEX lines inside the old steam pipes to get between floors. You’ll probably (almost certainly) still have to cut into walls/floors in spots to make turns, but at least you wouldn’t have to open up entire sections of wall on each floor. Check that you won’t have any problems with inspectors if you try this — I’ve only ever done this for wiring before.
I don’t see why you wouldn’t be able to use one big boiler in the basement. It’s very common to have multiple zones off of one boiler in hydronic systems. Some systems use a circulation pump on each zone, others are carefully balanced with bypass valves. I think the seperate pumps is probably simpler. You’ll want a good control system.
Bill
I think the issue with one bigger boiler is tenant billing. If they aren't directly paying for heat it tends to get abused.
An option might be to install BTU meters on each unit, we do that commercially all the time with Onicon System 10 meters https://www.onicon.com/products/system-10-btu-meter/ . But it might be cost prohibitive in residential applications.
Hi Josh,
Thanks for chiming in. OK, so Combi units are out as well. This is a good way to narrow things down, by process of elimination. That leaves hydronic and geothermal. Keeping the look of the house is super important to me. I don't love the idea of the maintenance of the mini split system but its really my only con and the price works for what I would be getting.
Buying cast iron radiators new aren't cheap and would add thousands to the cost. I agree about the heat loss, Josh. Do you have anyone you can recommend who can do this in Orange county NY? Ive been searching for someone and would also like to have them go over my insulation options on the house. Any idea what it would cost to put a BTU meter on and how that would work? Maintaining one boiler rather than 4 is a pro to me as long as they can be zoned somehow.
Zephyr7- Thank you as well. Appreciated.
Ive thought the same about using the preexisting steam riser as a chase. I know my HVAC guy said they were too small for him but not sure about PEX. Either way, if they don't work, I will rip them out and box them out. Its the most simple, noninvasive solution without damaging plaster walls or ceilings.
As you can see, I have a big and costly decision to make here. AC is not an absolute must, but for a few grand more would be nice.
Hydronic systems usually pose a significant cost premium over other types of systems. There is no getting around the many expensive parts and labour to install a proper hydronic system. They can provide excellent comfort though. Steel radiators may be much cheaper than iron, and often come with some fittings built in and brackets to reduce extra costs. I have these in my house, I think I paid around $200 for a 3000btu/140F rad and installed them myself with 1/2" O2 barrier pex home run to a manifold in my basement. https://www.purmo.com/en/products/panels/compact-ventil.htm
Air source heat pumps whether they are central or ductless probably make more sense than ground source heat pumps in your application. Top tier air source heat pumps are nothing like the horror stories you heard about heat pumps from a decade or two ago.
I'm in Canada so I don't really have a list of people to recommend, but don't rule out some heat loss providers that are remote. You will have to do some leg work to get the measurements and construction details, but they are good at their job.
Here is one that comes to mind, it's Allison Bailes' company, he is respected in the building science world. Perhaps Dana can recommend some others.
https://www.energyvanguard.com/service-category/hvac-load-calculations
As far as mini split maintenance goes, many of the maintenance issues with mini-splits exist with any ducted system, it's just easier to ignore something hidden in the walls or your basement. I think the floor mounted ones are among the easier ones to service, since they aren't quite as compact and they are located in easy to access locations (rather than 6-7 feet up a wall, or hidden in a closet or ceiling).
Geothermal would be insanely expensive. Even if you were in a county served by Dandelion (a create geo company financed by google) they only do ducted air.
Panel radiators are a real cost multiplier relative to cheap fin tube baseboard. Even used cast iron radiators are many times more expensive than baseboard. Installing enough radiator to operate at geothermal temperatures would be more than twice the cost of what it takes to do with 14o-160F from a mid-efficiency cast iron boiler or mod-con.
I don't have any personal recommendtations for Manual-J provider in Orange County NY, but you might start looking here:
https://www.nyserda.ny.gov/Contractors/Find-a-Contractor/Home-Energy-Rating-System-Provider
Get references, and real-world example Manual-J reports from any potential provider, preferably a Manual-J on an older house, not some pro-forma job on a brand new code-min ranch house.
Dana,
I am a rookie to this site and all the terminology. I didn't mean geothermal, I just was referring to the Fujitsu units. My steam guy is suggesting I re-route all of the steam piping in the basement so I can accomplish what I want to do in the basement apartment and everything would run correctly. I would get to keep all of the radiators to keep the look of the house. The boiler he is suggesting is the Peerless 287,500 BTU gas fired Atmospheric Steam boiler.
All heat would end up being on my dime with no zoning but I would imagine I can get this done for about half the price of the HVAC system. Maintenance cost would be $500 per year as opposed to $2400 per year.
In the commercial multitenant world, it’s not uncommon to “bill” for electricity at a flat rate based on square footage. For example, in my area its common to see “electric” billed as $1/sqft/year, billed monthly, so about 83 cents/sqft/month. Perhaps you could work out something similar to cover your heating costs without the expense of BTU meters on zone lines? Just a thought. It might even be worth taking a bit of a loss on heating to save on boiler maintenance and come out ahead overall.
Bill
A steam boiler with more than 200K of output is still probably more than 2x oversized for the building load @ +10F if you are insulating & air sealing. ASHRAE recommends 1.4x, not more.
Air seal between floors too, and all the plumbing chases. It's pretty common in multi-story steam systems for the folks on top floor to get too sweaty, overheating during colder weather, at which point they crack the windows, throwing away a ton of heat, while freezing the folks on the first floor with infiltrating 10F air.
Dana,
The boiler size was measured taking no insulation into account. I am researching what is possible in that respect, now.
A steam boiler needs to be sized to the radiation, not the heat load. If they were sizing it based on the heat load they're not necessarily doing you any favors.
Reducing the total radiation is probably a first step to re-engineering the system once you have the room by room heat load numbers in front of you. You probably have way more radiator in the building than is necessary to actually heat the place, and maybe enough sizes to re-arrange where they are and reduce the total number to better match output to load. The ASHRAE 1.4x oversize factor is still the right target, but the radiation, not just the boiler has to hit that range.
If the boiler is undersized for the radiation not all radiators will get heat. If oversized for the radiation it creates several other issues. The range that still works for the radiation is reasonable, but not 50% or even 30% over/under sizing for the radiation. Finding competent steam heating designers/techs younger than 75 years old is becoming a problem in my area. In NYC there is a concentration of legacy steam systems that there is at least a critical mass big enough to support a core steam competence spanning multiple generations. If you're going the steam route in Newburgh I hope there are enough people around competent to service the thing.
If the radiators are painted a metallic silver or gold, that's done to cut the output by 15-20% by reducing the direct radiation, making them primarily convectors. But painting them any other color (recommended) would restore them to the original "equivalent direct radiation" (EDR) output. That too should be taken into account when assessing a steam system when running the numbers.
Done right, steam properly sized for both the radiation and heat load can hit it's modest AFUE efficiency numbers using almost no electricity, can be quite comfortable, and requires minimal maintenance. But that's not the typical system.
Assuming it's 1-pipe steam and you are going to stick with 2-3x oversized radiation it will be worth installing thermostatic radiator vents on most radiators to somewhat micro-zone it, and have the means to adjust the room to room temperature balance.
Dana,
VERY helpful information here! Thank you so much. I know finding a solid steam guy isn't an easy task. I actually found my guy at Heatinghelp and he is a pro under 75 :) He really knows his stuff and is one of the highest rated guys on the site in my area. He is the one who came out to see the system and ran the numbers. I am considering hiring him as a consultant for the system design and having my plumber install it. I am going to share your thoughts and suggestions with him. Thanks again!
If you found him on HH.com you should be in great shape- they have been a good resource for my residential steam system.
Comfortwise- nothing beats a radiant system in a cold climate. Once I got my system dialed you pretty much set it and forget it. That said, in a multi-tenant building, I would have concerns with individual units adjusting thermostatic valves on a per room basis- once you turn off even one radiator, it'll send more steam to the others and you'll have variation all over the place. That said it's probably better than them just turning off the shutoff valve. Don't even think about setbacks causing all sorts of noise issues and high pressure.
An ecobee thermostat with maybe 2 remote sensors in each apartment would really help you dial it in to at least get consistency across floors and rooms, as it can average the temperature among any of those sensors. After a couple days using their spreadsheet data you'll be able to see the variations on a floor, room, and apartment level, and then make adjustments to the radiators as needed.
I asked how he sized it and he said:
"An existing steam system is sized by existing equivalent direct radiation, not by a heat loss"
With that being said, I guess there could be a possibility that the radiators could be sized too big and too small for certain areas and swapped out like you are implying. That certainly makes a lot of sense to me. The house was built with many small rooms. Each room only has one radiator.
@KJMass1
Thats nice to hear. Since all of the pipes are totally shot in the basement, everything would need to be ripped out and re-ran. This is no small task and going to be very costly. I can rationalize going this route if I can get the cost to be 50% of the HVAC system. If the cost were 60-75% of what an entirely new HVAC system would be, It just doesn't make sense to do.
He proposed installing a thermostat in the mechanical room and remote temp sensors in every apartment to average it all out.
You really need beef up your insulation/windows/sealing and re-evaluate after you've done a heat load analysis. If these are top/down units, your first floor heat load could be very minimal with a boiler in the basement and a heated unit above them. You could probably remove a large amount of the radiators and just focus on putting them along the perimeter windows and the mass of the entire building will keep things distributed. Your steam contractor is right in telling you to size to the radiation, however the radiation you currently have is way too big. Get your heat load and then swap out the radiators for appropriately sized ones and size the boiler from there. You'll save huge money with an appropriated sized boiler in the long run.
Some nice replacement radiators here but can be pricey
https://steamradiators.com/index.html
Heatinghelp.com has page listing some sources for used radiators.
https://heatinghelp.com/systems-help-center/where-to-find-used-radiators/
If you want to dial things in a keep costs in line, get a heat loss done and then reshuffle your rads to most closely match the heat loss calcs, and purchase whatever else you need.
There are a ton of articles on heatinghelp if you want to geek out about steam systems. Reading them almost makes me want one (maybe for a year or two).
https://heatinghelp.com/systems-help-center/taking-another-look-at-steam-boiler-sizing-methods/
Haha! Great link Josh. Thanks for all the help. I will be sure to keep you all posted on what we end up coming up with.
Kjmass1
Makes total sense! Really good stuff guys. I've learned a lot!
Completely rebuilding the steam system isn't necessarily going to be cost-competitive either. But until you have the room by room load numbers it won't be possible to optimize this very much.
Spending money on lowering the load will also lower the cost of doing it with panel radiators or heat pumps, but where the cost crossovers are isn't entirely clear, but you don't necessarily want a steam system 3x oversized for the design load. I would expect the heat load for a 5700' 4- unit building to come in under 90,000 BTU/hr if it has reasonable air tightness, some fluff in the 2x4 walls and clear-glass double-panes. It could even be under 75K @ +10F with low-E windows & lower-than-current standard window/floor area ratio, and an efficient building shape (a box on a rectangular footprint rather than a gazillion dormers, bump-outs & gables.)
Just throwing this out there just in case it fits: The 1.5 ton 18RLFCD Fujitsu mini-ducted mini-split delivers ~21,000 BTU/hr @ +10F , 18-19,000 BTU/hr @ -5F, and can fit in the top or side of a closet. If mounted vertically it takes up less than 8 square feet of floor space (the existing radiators in any given unit probably eat up more than that.) With a favorable floor plan it's possible to serve 3-4 rooms without any long duct runs taking up space below the ceiling (other than the closet it's mounted in.) With a dead-easy installation could be under $6K, all-in, but $7.5K would be a more typical installed price in my area (average complexity installation.) It doesn't come with a pan heater for clearing defrost ice the way it's true cold-climate cousins do, but in a location with a +10F design temp that's not a huge deal. It has the right type of compressor to deliver decent capacity & efficiency at low temperatures, unlike most competitors' mini-duct units.
I wish they would design a cold climate version of that model with a pan heater & controls since it's still chugging out quite a bit heat at -15F, albeit an unspecified amount. If it scales at the same curve as their wall-coil type cold climate mini-splits are any indication, it would be about 16K @ -15F, but we don't really know.
Dana,
I am so glad I stumbled across this site. The information I have been recieving is extremely helpful. Come to think of it, the steam boiler sizing was only for the top 3 floors and not the basement. It was suggested to run a hot water system in the basement but my understanding is this would not increase the needed BTUs of the boiler, correct? So the 5700 number is reduced by roughly 1000SF.
I will propose the Fujitsu suggestion to my HVAC guy but I would imagine installing this would be tricky and still require floor mounted units in the other rooms. The two middle floors consist of a few bedrooms, a very large living room, a kitchen and bathroom. This would work well for the living rooms. They goal is to not have to rip the house apart installing new mechanicals. The ceilings on the top 2 floors and all the walls are 100% perfect.
The idea is to take advantage of the unit's compactness, and install it centrally where you can run short (like 4 'to 10') efficient runs of round ductwork to adjacent rooms, instead of long home runs to the basement or far corners. Can you post a floor plan or pictures?
With decent insulation, you don't necessarily have to run the heat to perimeter of each wall, just put the supply diffusers on the wall closest to the ducted unit. The diffusers should be selected to have the appropriate amount of throw for the size of the room. Some of the Fujitsu units can be mounted vertically or horizontally to take advantage of whatever space makes sense. You may be able to install them in a way that only requires minimal ductwork/and bulkheads if you're trying to hide it.
Even the smallest floor mounted ductless units are going to be oversized for a typical bedroom if tied to a multi-split, and would have to be on at dedicated compressor to modulate. A decent sized bedroom will usually have a heat load less than 4000 BTU/hr @ +10F, unless it has a lot of windows.
A 3/4 ton KJ09 will modulate down to 2900 BTU/hr @ +47F and not lower, even when on it's own compressor and will do a fair amount of cycling during the shoulder seasons:
http://meus1.mylinkdrive.com/files/MFZ-KJ09NA-U1-MUFZ-KJ09NAHZ-U1_ProductDataSheet.pdf
But tied to an MXZ multisplit it's going to spit out the nominal 11,000 BTU/hr no matter what the outdoor temperature is:
http://meus1.mylinkdrive.com/files/MFZ-KJ09NA-U1_For_MXZ_MULTI-ZONE_SYSTEMS_ProductDataSheet.pdf
If a room's design load is 4000BTU/hr @ +10F outside, +70F inside, when it's 40F outside the load is only going to be ~2000 BTU/hr, which makes the KJ09 more than 5x oversized at that temp and more than 10x oversized for the load at +55F. That's going to be a problem on a multi-split. If the other zones aren't similarly crazy-oversized just the bypass refrigerant running through the KJ09 can overheat/overcool a low load room when other zones on the same MXZ are running long cycles. But on it's own compressor it'll be cycling during the shoulder season, but fine putting out only about 1/4 of the "nominal" output it would on a multi-split.
The Fujitsu 9RLFF floor unit has the same issue, and they don't make them any smaller than that.
http://www.fujitsugeneral.com/us/resources/pdf/support/downloads/submittal-sheets/9RLFF.pdf
http://www.fujitsugeneral.com/us/resources/pdf/support/downloads/submittal-sheets/AGU9RLF.pdf
Installing a KD09 or ARU 9RLF mini-duct cassette to serve 2-4 adjacent rooms won't have that problem, if sized reasonably for the combined load.
http://www.fujitsugeneral.com/us/resources/pdf/support/downloads/submittal-sheets/ARU9RLF.pdf
http://meus1.mylinkdrive.com/files/SEZ-KD09NA4_For_MXZ_MULTI-ZONE_SYSTEMS_Submittal.pdf
The Mitsubishi mini-duct units can only be installed horizontally, and have wimpier blowers that the Fujitsus, but that's not a problem for short duct runs off a wide plenum.
Fujitsu even has a half ton mini-duct unit (about 8K nominal heating) that works with most of it's multi-splits, but they don't have a half-ton dedicated modulating outdoor unit to drive it:
http://www.fujitsugeneral.com/us/resources/pdf/support/downloads/submittal-sheets/ARU7RLF.pdf
Splitting it's output between just two 2-4K load rooms wouldn't be terrible.
With a 4700' of insulated conditioned space your likely load is under 75,000 BTU/hr. Insulating and air sealing the basement walls to R15 continuous insulation (current IRC code min for zone 5) is going to be "worth it" no matter how heat & cool the rest of the place, and should be plenty of freeze protection.
Really good stuff, Dana. I can't thank you enough. Clearly the HVAC guy didn't do his homework and I need to pay very careful attention on how this system will be designed, no matter if I go with Steam or HVAC. I have learned so much today.
As far as the steam, just wanted to point out again, the BTUs were determined by the existing radiators on only the top 3 floors, not the basement which we planned on branching off the boiler for hot water on that floor. My understanding is this is not factored into the BTUs of the boiler so the current radiation is far worse then we thought.
My Steam guy made a good point about where to draw the line because the only thing of any value to me in the house heating wise is the radiators and risers. If the radiators are sized way too big, am I going to go around trying to find all new ones or looking to trade what I already have? Seems like a massive PITA. We were using 5700 as our square footage for that boiler, not 4700. Can I mix and match and use less? Maybe- But I know for sure I need at least one radiator in each room. This throws a big curve ball into keeping the steam system. Im all about the comfort it provides but not going to build one entirely from the ground up. Kind of back to square one now. Just much more knowledgeable.
Knowing the radiation is way too much for the house and assuming majority are the same size, should I check this option off the list? Also, is there a 3rd party I can hire who is 1/2 as smart as Dana and the rest of you to help me design this system in person? My HVAC guy is just reporting this all back to his distributer which is certainly no help. I guess with your help, I can look to pull this off myself? Thanks everyone
@kjmass1 | Dec 13, 2018 03:13pm | #26
@Josh Durston | Dec 13, 2018 03:23pm | #27
In rereading your suggestions, maybe this is a good idea. Makes total sense and something I would have never thought of. I just wonder if I even have the correct radiators to shuffle around to make this work. The house has roughly 25-30 radiators throughout.
Curious to know what size boiler I really should have if I had all of the proper radiator sizes everywhere. I can see this being a huge cost saver over time so thank you all for pointing this out.
In reviewing this pics of the house this morning, I'm really stumped on how I would get HVAC into this house without doing extensive damage, even with the ARU9RLF mini-duct cassette. These old historic homes have small rooms and no closets with tons of plaster.
I was initially looking at the https://www.mitsubishicomfort.com/products/indoor-units/ceiling-cassette from Mitsubishi. These fit in-between the 16 inch joist but would require a lot of damage to the ceiling. I also need to be careful to not run the lines around the entire building as it is located in a historic district and they would never allow for this. Out the back where the units would be mounted, totally hidden from the street is one thing, but not everywhere.. I really wish I could get pics uploaded to the site, it would really be helpful to me and everyone else trying to lend a helping hand.
Conclusion-
Baseboards all around the house are out. Going all new hydronic with all new cast iron or even panel radiators is out due to cost, so we are left with HVAC or Steam. Steam I wold need all new piping in the basement, new boiler, shuffle around and/or replace some radiators because I am oversized, and to me, HVAC design is not going to be an easy task. The way the joist run does not help.
If there is no way to upload pics I will try to transfer everything to a google drive account and provide the hyperlink.
>"In reviewing this pics of the house this morning, I'm really stumped on how I would get HVAC into this house without doing extensive damage, even with the ARU9RLF mini-duct cassette. These old historic homes have small rooms and no closets with tons of plaster."
If it helps, the ARUxxRLF cassettes (unlike competitors' units) can be mounted vertically, if you can build a micro-closet/cabinet to mount them. The 7RLF may be a better fit to the loads than the 9RLF in some zones, if breaking it up into 3-4 zones.
The nominal heating output of the smallest MLZ ceiling cassette is 12,000 BTU/hr, which is quite a bit.
https://nonul.mylinkdrive.com/files/MLZ-KP09NA_For_MXZ_MULTI-ZONE_SYSTEMS_Submittal-en.pdf
Good morning Dana. If I did end up going the HVAC route, I would really like to take advantage of where the radiators were. If I am understanding what you are saying correctly, maybe I could put the Fujitsu ARU9RLF units under the windows and box them out and run the lines up where the risers were, just as I was initially going to do with the floor mounted units? If so, I can see that working out. It would be okay for them to be close to the floor, right? My only option to do minimal damage is to use those exact spots.
1st floor - floor plan
The second floor is almost identical. Working on the 3rd. Basement is a gut reno so no issues there. I’m not concerned with heating and cooling the common areas/Foyer. I planned to do electric heat panels in the foyer and hallways so it could be on the landlord meter.
> If the radiators are sized way too big, am I going to go around trying to find all new ones
With thermostatic radiator vents added, what is the concern with over-sized radiators?
Jon R: The boiler would still have to be sized for the full radiator output, and there wouldn't be a way of determining a-priori how far to scale back to match the settings of the radiator thermostats. If the rads are all sorta-reasonably sized for the loads the vent settings don't much matter, but if a whole bunch of them are limiting output by 1/2-3/4 the other vents (and maybe even the system vents) will all be screaming with a boiler sized for the full radiator output.
Justin S: No doors, except between the family/dining room & bedroom?
Dimensions of the rooms, and the location of existing rads (even the ones that have dissappeared) might be useful too.
But my understanding is that the steam operating pressure is pretty much fixed (so why would vents scream). OK, lack of radiator demand may cause short-cycling. Sounds like a case for a modulating power burner. Less BTU, less steam, little need to cycle.
I see below which has a explanation of why some think that the boiler has to be sized to all the registers (evidently smaller vents fix this and I would expect thermostatic air valves to do the same in a smarter way).
https://heatinghelp.com/systems-help-center/taking-another-look-at-steam-boiler-sizing-methods/
Hi Dana,
I’m having someone work on what you requested and will get it to you ASAP. I created a folder of pictures of the house. Please keep in mind, the house will be going under a major renovation. :)
https://drive.google.com/drive/folders/1r8ffFOktfeqdl-i5KtrAh6Mky70EcTNW
You are worried about opening up a couple walls in the quasi-finished units? Rip it open and design the best system you can at this point. Plasterers are cheap in the grand scheme of things.
@Kjmass1
Its hard to see from the pics but the top two floors are in perfect condition. Sure, it needs cosmetic updates, new kitchens and baths, but other then that, not too much. A good floor refinishing and paint job and a few new windows here and there and those floors are done.
I am a big fan of plaster for its sound deadening qualities, especially in multi family housing. We did a gut renovation of our Brooklyn Brownstone and had to spend a lot of money to soundproof to the best of our abilities from the tenants above us. We have friends a couple of blocks away who live in a original building and there is not much of a difference. Just as quiet if not more. It really comes down to how much damage we would have to do. A little I am open to but not taking down walls or ceilings. I would skip HVAC all together if it came down to that.
Revised layout showing radiators, doors and scale. There is a chase for the plumbing stack in the "living room" that can be used and the basement is wide open underneath.
The ceiling in the living room also needs to be removed and replaced. Kitchen is open to do whatever we want as well. I have more detailed plans coming soon. The kitchen, bathroom and bedroom face the rear of the house where the exterior units would have to be mounted, preferably on the wall of the kitchen.
All,
Good morning everyone. I hope you all had a nice weekend and once again, thank you all for your contribution and help.
I have this narrowed down to two options right now.
1. Stick with the HVAC route if we can design a good system. The middle two floors are the only challenge.
2. Hydronic- Condensing boiler, all new properly sized radiators, BTU meter to separate and bill the tenants and possibly a indirect water heater?
Steam is 100% out. I have someone coming to review the building envelope in person on the 27th. I know it starts there.
If the hydronic route is not 1/2 as much as the HVAC route, I will stick to finding a way to make the HVAC work. Id really like to do this without any soffits to ruin the look of the house.
The "after upgrades" room by room Manual-J is necessary to be able to figure this stuff out.
Sometimes it's possible to route flex duct inside existing floor or ceiling joists without ripping up the ceilings/floors.
It's almost always possible to route PEX to low-temp radiators without ripping up ceilings & floors.
Justin,
Hydronic heating is the most expensive setup, plus the need for separate cooling. There is very little payback in this situation. There are adapters for converting old single pipe steam rads to hydronic, you loose BTUs but would work with some envelope improvements.
The basement is unfinished, you can put the HVAC for the basement and the main floor there (separate HVAC for unit). The ducts for the main floor can then be run easaly inside the floor joists with the some bulkheads in the basement. The basement ducting is easy as it is all new construction.
You can in a similar way put the HVAC for the 2nd and 3rd floor on the 3rd floor and run the ducts from above. For feeding the 2nd floor, you pull up sections of the 3rd floor subfloor to get access to the joist bays. This also makes running any new wiring way easier. I've done this for running pipes for heated floors and sound insulating without dropping the ceiling, fairly straight forward.
You would loose a bit of space on the 3rd floor and basement for the utility rooms and bulkheads but would allow you to keep the two main floors mostly intact.
My $0.02.
Hi Dana,
Got it. Im on it... The company that is coming to do the on site visit to consult on what insulation would be possible, also does the manual J. They are coming by the 1st week of Jan.
Hi Justin, I just happened to see in post 44 that you were concerned about opening the walls in part because you like the sound deadening properties of plaster. I’m assuming you are in an older building with “real” wet plaster over lath walls. They’re good for sound deadening because they are massive. Massive in terms of mass, much more than the usual 1/2” drywall.
You can get much of the sound blocking benefit of wet plaster with a double layer of 5/8” drywall. Even better, hang it on resilient channel. That will keep sound between units down and will be lots cheaper than replacing wet plaster. Best would be mineral wool in the wall cavity, double 5/8” drywall on each side, all drywall hung on resilient channel, and green glue between drywall layers. How much you want to do is a budget consideration. You probably get the most bang for the buck with double 5/8” drywall and mineral wool in the wall cavities. Resilient channel would be the next step up, then green glue last.
Bill
Did you consider the high velocity HVAC systems? They were made for just your situation where you want to save the old plaster and add AC to an old building. They will not be cheap but may be worth it to you.
https://www.unicosystem.com/
Walta
Hi Zephyr7
I did just this in Brooklyn. I agree, it works, but its very costly to do. I used a resiliant channel with double sheetrock with Green glue in Between on several floors. Night and day.
@Walter Ahlgrim
I have considered this route. Extremely expensive and those high velocity units can be noisy. Not ideal for a rental building. I think with some clever planning I can manage to get these Fujitsu units in. Thanks for your suggestion.
Hi Akos
Please take a look at the google drive picture link I uploaded. Pulling up any floors at all are not possible. These are 100 year old floors in very good shape with inlays.
This is my insulation issue guys
https://inspectapedia.com/insulation/Brick_Lined_Walls.php
Is the plaster is applied directly to the nogging, or is there a lath layer?
If you are re-siding, a continuous layer of 2" foil faced polyiso on the exterior would bring that up to code minimum on a U-factor basis. That would involve a lot of window flashing detailing to get right, and redoing all the exterior window & door trim- it's not a cheap fix.
I spent the entire day at the house again today with my contractor and really dug in deep. Moral of the story is I am not going to insulate the exterior, or the interior walls. Its just way too much work and its out of the budget. That being said, that changes things. Keeping my process of elimination going- Steam is out.
Two options remain
1. Large condensing boiler, sized appropriately, with BTU meters for all apartments. I would purchase all new radiators
2. Combination of Fujitsu floor units, wall units or ducted units. The floor units make the most sense but you have a very valid point about the sizing. I am certain my HVAC guy is not doing the proper calculations. There is no way to get these ducted units in without doing a lot of damage. At least no way I can come up with.
I need to do a heat loss. Please see attached. Also, there is no attic.
You may be able to push round duct along joist cavities, which only requires opening access slots at ends of runs and any turns, assuming you don’t have other framing members or blocking in the way. It’s not unlike fishing wire, but it is in much more difficult. With very careful placement of equipment and vents, you might be able to install the ducting with only minimal damage, but it would be a lot of work and lots of opportunities for Murphy to surprise you with obstacles.
You have interesting floor plans, btw.
Bill
@Zephyr7
Interesting is being nice. :) it’s original and bizarre but it is what it is. Take a scroll through the drive link I uploaded with pics if you find the time. It’s just not possible to do that ducting without doing serious damage to the top 3 floors.
Maybe it's time to start a room by room IBR type heat load spreadsheet for sanity checking.
Assuming 4" brick nogging plus 3/4" plaster & lath, clapboards averaging 3/4" on the bottom edges , with interior & exterior air films you're looking at a U0.25-ish (R4 whole-wall). So at +10F outside (the 99% outside design temp for Newburgh) and a code-min 68F indoors, that's a 58F temperature difference.
Every square foot of exterior wall (not including windows or doors) has a design heat loss of about 58F x U0.25= 14.5 BTU/hr. Add a foot to the room height to account for joists.
If the windows are clear glass vinyl double panes or wood sash single panes assume U0.5. If one out of the four reflections of a candle or lighter flame show one that's off-color indicating a low-E coating, assume that window is U0.35. Measure the full opening to the nearest inch, divide the square inches by 144 for the square feet (be sure to subtract that from your wall area measurements.
Assume the paneled exterior doors to be U1.0, U0.5 if it has a storm door. Assume solid exterior doors are U0.5, U0.35 with storm door. (Low-E insulated storm doors such as the Anderson 400 with the low-E options can improve that by quite a bit.)
For an air leakage WAG, assume 10 cfm (600 cubic feet per hour) per window or door if it's leaky, 5 cfm (300 cfh) if not too drafty. Then multiply cfh x 58F x 0.018 BTU per cubic foot per degree. eg: If a room has three pretty tight windows the leakage probably won't be more than 3 x 300 cfh= 900 cfh, with a infiltration load of 900 cfh x 58F x 0.018= 940 BTU/hr.
For the basement, assuming it's 12" thick triple-wythe brick foundation figure on about U 0.30. Count only the area from the foundation sill down to a foot below grade. The below grade losses are more of a constant, not changing much with outdoor temperature, but changing seasonally with ground temperature, and difficult to model accurately. Counting the foot below grade is something of a fudge-factor to account for the below grade losses, including the slab.
No attic, but what is the roof & ceiling stackup on the top floor?
It's well worth air sealing all of the plumbing / wiring/ flue chases & penetrations at the basement ceiling/first-floor subfloor, starting with the biggest holes first. Anywhere it's accessible air seal between floors as well, and weather strip doors between common area stairwells and the apartment units. The stack effect draw of a 3 story with tall ceilings and a full basement is substantial. Air sealing (and possibly insulating) the basement from the outdoors is also "worth it" for reducing stack infiltration drives.
With the crude room by room IBR load numbers it's possible to take a reasonable stab at how much radiator or heat pump it's going to take per room / floor / unit to get there, and where the heat emitters are best placed. It takes about 3x as much radiator to deliver design day heat with 140F water (a reasonable design goal with a modulating condensing boiler) than with 215F steam, but there are decently high output panel rads up to the task, and the pre-existing radiation is usually oversized. Floor mount ductless units can put out quite a bit of heat for their footprint or bulk relative to steam radiators too.
Dana,
Is there an excel sheet or template somewhere I can use to attempt this? Also, how does this differ from a manual J? This is complicated stuff, especially to someone who has never done it before. I would love to get a pro in there to run some numbers for me and size things accurately. I’m willing to swing the bat, but a template would be helpful.
Justin,
Here are links to GBA articles that will help you understand Manual J and other methods for calculating design heating loads:
"How to Perform a Heat-Loss Calculation — Part 1"
"How to Perform a Heat-Loss Calculation — Part 2"
"Who Can Perform My Load Calculations?"
It's pretty straightforward to set up your own spreadsheet. Try to set it up room by room, but allow for universal changes to wall U-factor or design temperature difference in case any of that has to change, making it a single data entry rather than on each room.
Manual-J is a superset of IBR, and includes factors for calculating the cooling load as well as heating load. From a heating equipment & radiation sizing point of view IBR is good enough. The numbers tend to be slightly higher than an aggressive Manual-J, which even includes factors such as curtains, etc. As long as you don't upsize from an IBR load calc "just to be sure", it will usually be the same equipment that you'd end up specifying using Manual-J.
To get a bit more accurate on your wall and ceiling U-factors (which I didn't try to estimate formally with precision) we need more information:
How thick is the brick nogging? (I assumed 4.0")
Is it plaster on nogging, or is there lath under the plaster? (I assumed no lath.)
Is there any sheathing under the clapboards? (I assumed none, with clapboards nailed directly to the framing.)
How thick are the clapboards? (I assumed 3/8" average.)
What are the stud dimensions & spacing?
Why not keep the top two floors with steam and convert the first floor and basement to something else. This way you can gain the radiators you need and minimize the damage to the house since you will have access to the first floor from the basement. Then you only have to purchase a smaller steam boiler and two small alternative heating systems. Then you can convert some of the radiators to forced hot water for the first floor to maintain the look and add baseboard to other areas as needed.
Deleted