Why bother with batts, when using rigid foam exclusively offers higher r-value?

I’m re-doing the insulation in a 1924 home in Seattle, from the interior. Here’s my question: is there a good reason not to use Rmax rigid foam (commonly sold at Home Depot) exclusively, instead of rockwool batts? Rmax delivers r-value of 6 per inch, which would provide an r-value of ~21 for a 2×4 stud bay.
If I use 1/2 inch of Rmax rigid foam and fill in the rest with rockwool, I only get to an r-value of ~14.
What am I missing here?
much appreciated–
GBA Detail Library
A collection of one thousand construction details organized by climate and house part
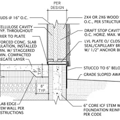
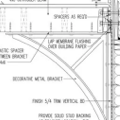
Replies
Here are a few reasons to consider:
Cutting rigid foam to perfectly fit into the stud bays of a 1924 home could be time consuming.
Rigid foam might be more expensive than batts.
You might have a preference for insulation with a lower embodied carbon (which would probably lead you to cellulose over rigid foam or mineral wool).
Because of the thermal bridging of the studs, the increase in total R-value by using the foam is not as great as it might first seem.
Fitting rigid foam into stud bays is often called "cut-and-cobble", so that might be a useful term to google to get more info about your idea. Here's an old post on GBA that's worth a read (along with the comments!) https://www.greenbuildingadvisor.com/article/cut-and-cobble-insulation
Rigid foam is going to be significantly more expensive than batts, and will be more difficult to cut into place since it won't have any give at all. You'll also need to carefully seal it all in place with canned foam to avoid convective air pathways. All that said, it's entirely doable to insulate this way, but it's a lot of labor for very little, if any, practical benefit.
Stick with mineral wool batts in the stud bays, make your life easy. If you want to use rigid foam, use it so that it maximizes the benefits it can offer, which means put it OVER the studs so that it helps with thermal bridging too. Ideally you want to put it on the outside of the wall over the sheathing and under the siding, but you can put it on the interior too behind the drywall.
Bill
Fair enough. These stud bays are not consistently sized, so there will be a lot of cutting regardless of what I use.
Insulation cost is not really an issue, because Seattle's energy costs have increased so much in the last few years (and will likely continue to) that this expense is small potatoes. Also, I don't have a lot of wiring (and no plumbing) to contend with in this part of the house. I'm guessing that there will be an additional 15% of work to install foam vs batts.
Given above, do you still think that an additional r-7 value is 'little, if any, practical benefit'? If this was your house, what would you choose to do?
> I'm guessing that there will be an additional 15% of work to install foam vs batts.
Your estimate is probably wildly off. Probably by close to an order of magnitude. Trust people who have done this work before about how tedious it is.
(Here's a simple "proof": unless you have 3.5" foam, you are doing minimum of two layers of foam, with 2x the cuts and gluing. Even if doing a single layer was as simple as installing a batt, you're already at 2x work, or 100% increase in labor vs. batts.)
> Given above, do you still think that an additional r-7 value is 'little, if any, practical benefit'?
The time and money can be better invested to other things. Consider this, for example: https://www.finehomebuilding.com/project-guides/insulation/breaking-the-thermal-bridge
Having actually done this a little (use rigid foam cut between studs), I would estimate AT LEAST two to three times more work compared to using batts. The reason for this is that batts are more forgiving: cut everything a smidge too big, and stuff it in. Easy. Rigid foam is unforgiving, everything has to fit reasonably well, then you have to use canned foam to seal it in. If you have multiple layers to do, you have issues with lining things up, then getting the canned foam in without causing the layers to seperate and push out of the wall cavity. It's a lot of hassle for little gain.
In practice, you'll see less than the theorectical R value performance over the entire area of the wall, and the higher the R value of the insulation between the studs, the bigger the impact the thermal bridging of the studs will be to the whole-wall R value performance. That's why you're much better off using rigid foam OVER the studs, not BETWEEN the studs.
Bill
User...142,
Apart from the things Brendan and Bill have mentioned, on a retrofit, cutting rigid foam around existing plumbing,. electrical, and blocking would be a nightmare.
"If I use 1/2 inch of Rmax rigid foam and fill in the rest with rockwool"
Why would you use both, are these true 4" deep studs? Your math 6x3.5=21 suggests otherwise.
using 3" rockwool.
Safe and Sound is not exactly the same as Comfort Batt. One is for sound suppression and the other thermal insulation. Yes, you will get thermal insulation from Safe n Sound, but not as much as from the Comfort Batt.
Safe-N-Sound and Comfort Batts are the same thing, for all intents and purposes, they're just marketed differently. At least that's what someone high up in their sales department told me. In fact all of their products are similar, just different densities and slightly different R-values as a result.
The only real difference between Safe'n'Sound and Comfort Batt is that Safe'n'Sound is about 1/2" thinner to allow for an air gap in the wall, which helps with sound blocking (which is the main purpose of Safe'n'Sound). The material the batts are made of is pretty much identical otherwise, and offers the same R per inch. I can also confirm what Michael says, as the manufacturers will send documention about the R value of the Safe'n'Sound batts upon request if you need to show that to an inspector.
Bill
The question remains (or takes new form): why use 3" rockwool and 0.5" foam instead of 3.5" batts?
Excellent question, since 1/2" polyiso is usually rated R2.7, so using 3" of mineral wool and a 1/2" sheet of polyiso gets you.... Wait for it.... R 15.56! All of about 1/2 R value unit better than a full depth mineral wool batt alone. Adding that 1/2" sheet of polyiso is a total waste of time and money. You're not doing any better for air sealing, either, assuming you have some type of panel product (plywood, OSB) already -- there is no need for polyiso as an air barrier right up against another air barrier.
Bill
R/inch is a useful metric if you're trying to cram as much insulation as possible into a given space.
R/$ is perhaps a more useful metric for most people, since most of us have to build to a budget.
So I wouldn't be concerned so much about the first. Decide what total R value you need and then see if you can get it into the given space using lower R/$. If you can't fit it, then look into more expensive options.
There are other considerations of course. Greenhouse Warming Potential (GWP) could be one. If I was upgrading insulation from the inside, in an old wall and therefore continuous exterior insulation wasn't an option I might opt for cellulose batts or dense pack insulation (3.5 to R4 per inch) since they are significantly better from a GWP perspective.
Incidentally cellulose is competitive in terms of R/inch as well. So it probably comes down to price and availability in your area.
Although I'm not a fan of spray foams due to their high GWP (HFO based are much better than HFC) this might be the right application if their are a lot of obstructions such as existing piping and wiring. In that case I'd research whether to go with open or closed cell. In a retrofit application like this I'm not qualified to know which would be better.
I'm not looking at condensation issues in this comment. That would need to be considered as well. But I want to keep this comment focused on just what I've mentioned above. Others can address that if they want to.
Deleted
Polyiso is around R-6/in when new but it ages to about R-5.5/in eventually.
Including thermal bridging through the studs, but not including the R-values of the interior or exterior finishes or air films, which will add another R-1 or so, the true center-of-wall values would be:
R-6/in polyiso: R-19.4 for the assembly.
R-5.5/in polyso: R-17.8 for the assembly.
R-4.2/in mineral wool batts: R-13.7 for the assembly.
R-3.6/in cellulose or fiberglass: R-12.2 for the assembly.
I usually use cellulose for its low levels of embodied carbon, its vapor-open nature and its ability to safely store and redistribute small amounts of moisture, but it's the lowest R/in of the options. Polyiso gets you about 30% more insulation in the walls, if you can't make them thicker. Walls typically account for roughly 10-15% of a home's total heat loss, so the more highly insulated walls will save about 3-5% of your heating bill. If that's worth the extra effort and cost, somewhat higher risk of moisture-related problems and significantly higher levels of up-front carbon emissions, it's probably a better choice for you.
Michael, I think you have a typo in your mineral wool assembly number -- don't you mean R14.7? Mineral wool batts made for 2x4 walls are typically rated as R15.
For the OP: I don't think you're really going to get any noticeable improvement with polyiso in the studwalls. Thermal bridging will reduce the effective improvement more than you'd think when compared to insulating with batts alone, and the cost for polyiso will be MUCH higher, as will the labor to install it. You're never going to recover the cost difference in the form of energy savings. You'd be much better off using the polyiso for continuous insulation, which is what's normally done.
If you want an easy place to add extra R value on the cheap, use loose fill on the attic floor and go up to R60 or more (but be careful of loading the drywall too much if you go much over R60). There isn't much cost difference to go a bit overboard on loose fill insulation on an attic floor, so the payback is more reasonable there.
Bill
Bill, I'm factoring in the thermal bridging through the studs.
Like all insulation companies, Rockwool rounds up their R-values; their batts are R-4.2/in, so a 3.5" batt is R-14.7. Actually, if I recall correctly, it's more like R-4.17/in so a 3.5" batt is R-14.6.
Haven't you wondered how it is that most insulation manufacturers manage to get round numbers for all of their rated R-values?
What I'm getting from this is that thermal bridging isn't as huge as people make it out to be. While every situation is different, I'd suspect that making the wall thicker generally is a better way of getting more insulation that trying to eliminate thermal bridging.
When people want a higher r-value per inch it seems they always go with closed cell spray foam. The installed cost is lower than rigid foam. Plus you get better air sealing.
Spray foam at least offers near perfect air sealing (assuming a decent installation), and a big labor savings since there is no need to cut around obstacles. That labor savings offsets the increased cost of spray foam.
Using cut'n'cobbled rigid foam is like going with pre-cured spray foam, so you take out the "spraying" part. Thus, INCREASED labor savings, and NO guarnatee of perfect air sealing, since you can miss spots and you don't have the expansion aspect to help you out with tight spaces.
I have used cut'n'cobble in three places:
1- When I needed absolute max R value between rafters in a cathedral ceiling application, which had vent channels above the insulation. This was done as a thick piece or two of fiber faced polyiso, and a layer of 1/2" polyiso under the rafters with seams taped behind the finished drywall. All the polyiso between rafters was sealed in place with canned foam. This was safe because it was vented, and the lower layer of 1/2" foil faced polyiso over the rafters makes for very little chance of moisture sneaking up into the assembly. This was a pain to do, even in the ~150 sq feet or so (it was a closet squeezed into the edge of an attic).
2- insulating a wall built with sideways studs dividing the end of an attic from a living space. 1.5" rigid foam was a nice fit here, no batt would be. I put 1.5" rigid foam between the studs, then finished off with another layer of 2" rigid foam over the face of all of the studs. Total R value was around 17.5.
3- When I had just a tiny amount of wall in a corner between an attic and a living space, and I couldn't bring myself to trash the last bit of rigid foam, so I used it up in a small part of the wall.
I would never consider insulating large portions of wall with rigid foam between the studs. It's slow going, and it doesn't gain you much R value, plus you use very expensive materials to do the job this way.
Bill
I use cut-and-cobble a lot when I have an area too small to justify bringing in the spray foam guy but I want a high r-value.
I like to cut slightly undersized rectangles for rim joists and then seal them in place with spray foam. I find if I put the sheet of foam on sawhorses and cut it with a drywall square I can reduce a sheet of foam into a pile of identical rectangles in about five minutes.
You might want to check out the Kraken Bond spray foam on Amazon. It's like a huge can of canned foam, but it expands a lot more than you'd expect from Great Stuff, so it's a really handy substitute for "real" two part spray foam for very small jobs. I've played with the stuff several times now and while I wouldn't try to use it to do something large, like a whole wall or roof section, for a single stud bay, or filling a whole the spray foam crew missed, it's a pretty good product.
I do the same as you for rim joists. I cut sections of EPS foam, then seal them in place with canned foam (I like Loctite's Tite Bond for this, because it's more solid, so better when it's holding things in place and not just acting as an air seal). I cut the pieces with a hot wire cutter I made that is similar to a radial arm saw, with the arm sliding through a slot in the table which lets me quickly change the depth of cut. Once I set it up, I can run sheets through it with zero mess, and I get a perfect factory-like cut. I can shift the top and bottom attachments on the arm with respect to each other too, which lets me set the thing up to make angled cuts on the edges of the foam. I like to cut pieces for rim joists with angled edges, then place them such that the expansion of the canned foam against the angled cut tends to force the foam agains the rim joist. This makes it less likely the foam block will get pushed out away from the rim joist as the canned foam expands.
BTW, pieces of 10 or 12 gauge copper wire are great for holding the foam blocks in while the canned foam cures. I cut them about 1/2" longer than the height of the rim joist, then press them into place as I put the foam blocks against the rim joist. Once all the blocks are held in by the wires, I can go "a'foaming" and keep moving to have less issues with the canned foam setting up in the tip. Copper support wires are safer here than steel, since they are much less likely to spring back at you when you're putting them in and removing them later. After the canned foam as cured, I go back and remove all the support wires for a clean finished appearance.
Bill
Unlikely to be any benefit to increase R value using the foam boards. You can buy energy for probably half to 95% cheaper than going from R-14 to R-18