Why does my house SUCK?

It appears that most are concerned with proper ventilation considering the tightly built homes of today. I have a very severe flooring problem that I believe to be caused by negative pressure within my home and would like an opportunity to discuss with people more knowledgeable than myself. Allow me to explain a bit about the construction of my home, myself and my problem.
Let me start with my occupation as it will explain some of the things done during construction. I work for a company that specializes in building automation. We install control systems within schools and commercial buildings. I’m don’t know exactly what you specialize in (I would assume you’re a pro when it comes to pressure, considering your published article), but we basically go in and control hvac equipment for occupant comfort & health along with energy management done through metering, scheduling, etc..
The construction of my home… My home is a 2 level, 2400 square foot home. I used the most efficient windows, doors, wrap and other materials I could afford. I used a spray foam insulation for the walls and the roof deck. The 2nd level has a bonus room over the carport and the rest of the 2nd level over the remainder of the home is used for attic space which houses my wife’s junk along with all of my network gear. The home is built over a crawl space and sits high off the ground 4’ in some spots. I used bat insulation under the floors and installed a poly moisture barrier on the dirt in the crawlspace. Under my hardwood floors a 30lb felt paper was installed. My hvac unit is a Carrier Infinity heat pump with all duct work installed in the attic. I have a 4” duct installed from the outside of the house to the return duct for providing outside air.
I have install a BACnet control system throughout the house taking the following measurements:
-house temperature
-house humidity
-crawlspace temperature
-crawlspace humidity
-attic temperature
-attic humidity
-house differential pressure
-house CO2
-HVAC fan status
-HVAC supply air temperature
-HVAC return air temperature
-a smart meter that measures everything from power factor to voltage
Besides just monitoring these in real time I also keep the point data on all of these. I basically take a reading every 15 minutes and keep it for historical reference so I can chart the values so I can see trends.
I have a small 4” duct coming off a branch in my attic for supplying cool air to my attic. I have an actuator installed on a damper installed inside the duct that works as a high limit in the attic. Basically I wrote a program that says if the air in the attic reaches 82 degrees I open the damper until the attic reaches 78. I do this because of the networking gear potentially overheating.
I also have the same setup on the 4” pipe ducted into the return plenum of from the outside. I control this damper with a program that says if the fan status is on for the main unit and the pressure inside the home is less that +0.003 OR the co2 inside the home is greater than 1000ppm open the damper. This will provide fresh air and will only open when the unit is on to safe guard against a backdraft.
The problem I’m facing….I’ve been inside the house for 6 months and we have began to notice the hardwood floors are cupping. During construction I was very particular with the installer about acclimating the floors to the normal humidity levels we would have inside the home. I am sure based on moisture meter readings done during the installation that I am not experiencing an installation problem. My crawlspace humidity is high, typically around 70-85%. I realize this is unacceptable but I don’t think this is truly the cause of the problem, although I’ve already started the process to correct the humidity for mold or rot issues. I think the problem is being caused by negative pressure. Because the house was built extremely tight I think because of the negative pressure I’m experiencing I am pulling this humid air through the floors causing condensation under the subfloor above the insulation, which I have inspected and found to be extremely bad, almost dripping. My wet subfloor is transferring moisture to the bottom of my hardwood and causing the floor to cup.
The pressure inside my home is always negative even with the fresh air intake open with the unit running. It of course gets worse when a bathroom exhaust fan or the range is turned on.
I guess my question is what can I do to create a positive pressure inside the house. In a commercial building I usually control a makeup air unit to correct these problems. I cant find ANY information online about this type problem. If anyone would like to have a phone conversation I would be all for some professional advice. I am attaching some trends for your viewing pleasure.
GBA Detail Library
A collection of one thousand construction details organized by climate and house part
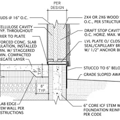
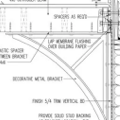
Replies
Cole. I'm sure others will post some helpful suggestions. In the meantime, this thread deals with a similar issue: https://www.greenbuildingadvisor.com/community/forum/general-questions/17825/why-are-my-wood-floors-cupping
Also, tell us where you are located. BTW. Impressive automation setup.
You're thinking 70-80% humidity in the crawlspace is not the cause? Why not? If the absolute humidity on the underside of the flooring is dramatically higher than room, cupping is a symptom to expect.
Relative humidity is, well, RELATIVE (to the temperature). Is the crawlspace temperature roughly the same as the conditioned first floor?
Is the crawlspace insulated at the first floor subfloor?
Is the crawlspace vented, or unvented? If unvented, has the crawl space been properly air sealed at the foundation walls, and is there ground vapor barrier?
If the crawlspace were sealed and insulated at the foundation walls ( and not the first floor subfloor) and ventilated with a modest amount of air from the room above, it wouldn't matter if the house was positively nor negatively pressurized, or neutral. The humidity would be the same on both sides of the floor. See:
https://www.greenbuildingadvisor.com/blogs/dept/musings/building-unvented-crawl-space
#30 felt is not a vapor barrier- it's semi permeable, and it's permeance varies by moisture content.
Putting the house at positive pressure relative to the outdoors in a cold climate can cause rot issues at slow leak points, since it actively drives moist humid air out the leakage points, which may accumulate moisture.
Cole,
As Steve said, we really need to know your climate zone or geographical location to provide useful advice.
My gut tells me that Dana is right -- you have a damp crawl space. In general, installing fiberglass batts between the floor joists above a crawl space is a discredited approach. For more information on this issue, see Building an Unvented Crawl Space.
Since you have made a significant investment in home automation equipment, I'm guessing that you can afford to pay for some diagnostic work. If you are worried that your house is depressurized with respect to your crawl space, it's easy enough to check whether your guess is correct. Hire a home performance contractor who owns a blower door to check the relative pressures of the two spaces.
Gentlemen,
Thanks for all the responses. I'm going to try and answer all the questions.
Mr. Knapp: My home is built in South GA, Sylvester, GA to be exact. I'm on a hill but the front of the house is on a slope. I've attached a picture for reference. The back of the house is about 2 foot closer to the ground, sorry I don't have a side view.
Mr. Dorsett: To answer your questions first: The batt insulation is installed under the floor joist, see the attached pictures, the crawlspace is also vented. Let me explain my thoughts a little better on my belief that negative pressure is causing the problem. I'll start by backtracking 2 months ago. I installed electronic locks on my home, the kind you press the code to open/close the deadbolt. If you aren't familiar with these type locks they basically have the electronics board mounted on the inside of the door. The only thing exposed on the outside is the locking mechanism and the keypad which has a harness that goes through the lock and attaches to the board on the inside of the door. I began having a problem with 2 of my locks, they began just beeping as if someone was entering the wrong code from the outside. I assumed the locks were faulty but after a couple of days of them making the beeping noise they started to malfunction to the point that they would not even operate. I took the cover off from the outside and saw that the batteries in the first were leaking battery acid. I removed the batteries cleaned the battery harness out thoroughly and installed new batteries but they kept malfunctioning. I then removed the entire lock assembly and to my disbelieve they were completely filled with water (I had mistaken this for battery acid). Because of the negative pressure on my house I was sucking air through the keyholes which was leaving condensation inside the cool locks and this caused the electronics to of course fail.
Now I told that story to explain better my train of thought on the floors. My locks failed because I have a negative pressure on the house and its humid outside. If my house was maintaining a slightly positive pressure this would not have occurred. Now I'm definitely not arguing the fact that in the case of my crawlspace that the humidity is causing moisture to collect between the subfloor and the batt insulation but I anticipate if my house was not trying to suck air through my floor to equalize pressure that this might not occur. If I indeed has a slightly positive pressure I would be forcing cool dehumidified air through the floor into the crawl space and might actually help with the humidity under the house and I would assume keep my floors dried out. This is all dreamed up in my head, I'm here asking for help and I definitely appreciate you taking your time to give me your expertise.
In my area there are please of homes that don't have encapsulated crawl spaces. My previous home for instance had a very high humidity in the crawl space but I never had moisture form under the subfloor. I would agree that if I fix the humidity problem by properly encapsulating the crawl space and installing a dehumidifier this would effectively solve the problem. The prices I have received for the work are coming in between 5-7k for this to be done. I feel that I could possibly solve the pressure problem for much less. But from what I'm gathering your not of that opinion which is what I was looking to discuss with someone more knowledgeable that myself on the matter which I'm sure you are.
Mr. Hollady: Concerning the diagnostics of the differential pressure inside the home in comparison to the crawl space. I am already monitoring this and have attached a picture of my current data. Its clear that I am pulling air from the crawlspace. This is not only evident by the negative pressure I'm ready but I can also look at my humidity trend and clearly see it sky rocket between the unit cycling. I would guess its actually causing my unit to go into humidification even when I'm at set point, particularly when my unit is not occupied. The pressure trend history I have attached has some dips where it becomes more negative, this is being cause by my bathroom exhaust fans.
Mr. Dorsett,
You also asked about my crawlspace temperature in relation to the living space. See the attached comparison. Notice the lines are color coded for their respective measurements.
If anybody would like other trends or info please don't hesitate to ask, I'm happy to share my data.
Cole. I don't think the water in the lock is conclusive. Seems like you could have a moisture issue if a lot of air is channeling in or out of the metal housing..
I suspect you are having issues because you built a tighter house while overlooking some best practices. You may be overventilating and introducing more moisture than your house can handle. Proper ventilation rates is a controversial topic, but you might want to consider dialing back your intake until you have more information on how your house is performing.
I think you would see a big improvement by making your crawlspace unvented. You already have a vapor barrier on the ground. All that's needed is to seal your vents and insulate your perimeter. You could use reclaimed foam and DIY much or all of the project. Martin's article has the details you need to understand the process.
This is a very interesting trend. Here I have pulled out todays histories on my main units supply air temperature, crawlspace humidity and temperature. Its clear that when my unit went unoccupied when I left for work that my crawlspace humidity began to increase.
By the way. I stuck a small dehumidifier in the crawlspace on Saturday to begin the process of drying out the floors until I come to a permanent solutions((Which may very well be installing a dehumidifier properly sized for the space.))
Hopefully you guys will find all this data interesting. It clearly very hard to find historical data when it comes to the residential market which I found out when trying to make educated decisions when building my first home. No shortage of opinions though.
Mr. Knapp,
Concerning the over ventilation. The damper on the intake was closed completely prior to discovering the problem with the locks, I hadn't yet finished with the installation of the control system that controls the actuator. The damper is a fire damper that has a rubber gasket around the edges, basically its a truly sealed damper. As far as over-ventilating the house, I'm reading a negative pressure so at this point I'm actually pulling air from the outside. If anything I would say I'm under-ventilated. Can you elaborate some more on your thoughts of why you would think over-ventilation could be causing the problem. Thanks for your thoughts and taking the time to respond. I really appreciate the help.
You're in climate zone 3 (Warm-Humid).
A couple of things crossd my mind.
#1 Newly built house which means a lot of construction associated humidity within the structure itself.
#2 Vented crawl space.
#3 Perhaps your HVAC system is oversized a little or there's an air leak in the ducts.
IIRC it takes up to a year to get the humidity out of a new house. Being that you live at the more humid southern edge of Climate Zone 3 I would think that's probably the issue and not the slight depressurization.
I would look at buying a dehumidifier to see if you can get the humidity under control then of course you have the problem with the vented crawlspace.
My 2 cents.
Cole,
It doesn't make any sense to install a dehumidifier in a vented crawl space. That's like putting a dehumidifier outdoors.
When you leave your vents open, you are raising the humidity levels in your crawl space. Seal those vents!
Thats my plan Mr. Holladay. I've already closed the vents but I plan to come back and seal them properly. Thanks for mentioning though, you are exactly right.
A vented crawl space guarantees that outdoor air enters the crawlspace due to the stack effect, since it's (almost literally) impossible to air seal between the crawlspace and first floor, at least nowhere near as reliably as at the foundation walls and foundation sill. The outdoor air is almost certainly the source of the moisture, and almost certainly the cause of the cupped wood flooring.
The vents to the crawlspace are at the very low end of the "stack", and any air leaks to the exterior anywhere else in the house would be at a higher point, which defines the amount of stack effect pressure pulling air into the crawlspace. As long as the crawl is vented to the exterior, there will be some amount of stack pressure moving air & moisture from the crawlspace to the first floor (unless you air condition the first floor to below the subsoil temperature in your area, which would be uncomfortably cool for most zone 3 locations.)
Looking at your temperature charts, it's unusual to see the crawlspace well ABOVE the subsoil temperature, and to vary so widely in temperature over the course of a day. That hints at the likelihood that the air handler is depressurizing the house. This can be due to improper return duct sizing, or inadequate return paths from rooms with supply ducts forcing leakage to the outdoors from those rooms while it's running.
The only way to get the crawl space up to 80F+ is by drawing massively more air into the crawlspace than would ever occur from stack effect drives alone. Deep subsoil temperatures in most zone 3 locations are in the low to mid 60s Fahrenheit, and without massive air exchanges with hot summertime air the temperatures would vary within a 5-10F window over the course of the year, dropping to the deep subsoil temp or a few degrees cooler in winter, to about 5F above those temps in summer. In Sylvester GA the deep subsoil temp is about 66F, 67F tops, and with an unvented insulated crawlspace the temperature down there would never break 72F. It's averaging 78-79F in your graph, despite the fact that it has an air conditioned floor above it averaging maybe 70F.
http://www.earthrivergeo.com/img/geothermal-article/geothermal-subterrainean-temperature-contour-map.jpg
Simply stopping the air leaks at the vents and foundation walls would be enough to fix the moisture draw issue, even without fixing the likely duct imbalance issues that are depressurizing the house. A vented crawlspace is a universally BAD idea in the humid southeast, and an even WORSE idea when the house is air conditioned, and it's only worse when the floor is insulated with fluffy stuff. Stratification of the air in the conditioned space put the coolest layer of conditioned air at the floor, which makes the subfloor cooler than the outdoor dew point much time during the cooling season, which causes it to accumulate moistur. If there weren't insulation under the subfloor it's temperature would track more closely to the temperature in the crawlspace, which reduces the moisture accumulation. The higher the moisture content of subfloor, the more likely it is to rot or grow mold, and this is a common problem with vented crawlspaces in the southeastern US, a problem that has become more common with central air conditioning and insulated floors. Also, when the subfloor's moisture content is low, it is also a pretty good vapor retarder- less than perm at a moisture content of 10%, but over 5 perms when it's moisture content is in the 25% + range, where mold & rot become an issue.
Peel back the insulation in a few places, see if there are any hints of mold growth (I'll be surprised if there isn't at least some.)
IRC code min insulation for insulated sealed crawlsapces in zone 3 according to TABLE 1102.1.2 (about halfway down the page: http://codes.iccsafe.org/app/book/content/2015-I-Codes/2015%20IRC%20HTML/Chapter%2011.html ), is R5. That's pretty cheap & easy to hit using fire rated 1" polyiso (eg Dow Thermax), taping the seams with foil tape, and sealing the edges with can-foam. Don't let the cut edges of polyiso contact the soil- lap the ground vapor barrier up against the foundation, between the polyiso and the foundation. You can leave the batts in place (though the installation quality in the picture looks like about the worst possible- that woudn't pass inspection if anybody cared), but it needs to be pulled back for air sealing the foundation sill and band joist areas. If the inspectors allow intumescent paints for fire protection of exposed spray foam, may be able to air seal and insulate the foundation, foundation sill, and band joists all in one go with a flash-inch of 2lb closed cell polyurethane. That's usually more expensive, but it will be quicker.
If you are in a termite zone it's wise to have an inspection strip along the perimeter of the foundation that can be quickly uncovered and replaced. That's probably going to be easier to do with rigid polyiso than with closed cell spray foam, but it won't be quite as air tight (but still pretty good.) The inspection strips can be cut-in after the foam is already up, using a straight edge (a 4 foot level works), and a 4" taping knife sharpened along the edge. See:
http://www.finehomebuilding.com/2009/01/29/theres-a-better-way-cutting-rigid-insulation
Looking at the crawlspace picture again, it looks like the house is supported only by the CMU piers, with no foundation wall per se, just skirting type of enclosure around the crawlspace. Is that correct?
Mr. Dorsett:
Read your comments about the elevated temperature of the crawlspace. I built another trend from yesterday. This trend shows the supply air temperature from the unit, which basically shows the cycling of the unit along with the temp of the crawl space. I really don't see anything there that would lead me to believe the unit is causing the suction. Seems the temp is pretty much staying in the same spot even through my unit isnt running while I'm at work. I think the reason the temperature may be elevated right now is because I put a dehumidifier in the space on Saturday and its been running ever since (see the attached trend on humidity since then, and I closed the vents when I put the dehumidifier under the house in an effort to dry the subfloor out faster which is soaking wet.
I also have attached my duct plan along with the layout of my first floor. I actually contracted the design of the duct system separately form the rest of my mechanical. I decided it was best to have a 3rd party that had no monetary gain in cutting corners on the design of the actual duct system. I hired a firm got their design and handed off to my mechanical company.
Concerning the layout of the piers. I have also attached that page from my plans. The plans were followed to a "T" by my contractor. He had no input on the structural design. He priced to construct what the engineering professional stamped.
I met with a contractor (same contractor that did my foam install) that emcapsulates crawl spaces yesterday. I have hired him to install 12 mil poly on the floor and run 1 1/2' up the piers and perimeter wall. He will be sealing the poly to the walls and piers with closed cell foam, he will also be sealing all the existing vents and covering with dry cell foam. New dehumidifier is also on the way. I ordered a Santa Fe Max Dry Dual XT.
Do you think I should remove the existing insulation under the floors??
I would like to hear more on my duct imbalance and how to correct this problem. I've been talking to mechanical contractors and mechanical engineers that I'm associated with and hearing alot of mixed information.
Cole,
Now that we know that your subfloor is "soaking wet," we have all the evidence we need to explain your cupped flooring.
Your crawl space is between 81 degrees F and 83 degrees F, and is filled with humid outdoor air.
Your house subfloor is somewhere around 70 degrees F (under the influence of your home's air conditioning system). The only thing between your hot, humid crawl space air and the cold subfloor is the air-permeable fiberglass batts. No wonder the subfloor is soaking wet!
Without the outdoor air temp the crawlspace temp trend against cycling of the air handler wouldn't show much. The thermal mass of the dirt keeps the crawlspace temp from changing rapidly unless the air flow is pretty extreme as well as the difference in crawlspace temperature to the outdoor temperature. Running at night the outdoor air may be at a lower temp than the crawlspace temp, and during the day somewhat higher. The thermal mass will average it all out.
But seasonally it would change it lot faster and further than it would in a sealed crawlspace.
Logging the %RH and temperature and crawlspace temp independently isn't as useful as measuring the dew point of the crawlspace air and logging it against the dew point of the outdoor air, and the dew point of the conditioned space air . RH is an almost useless number, since it's relative to a moving temperature. Dew point is a measure of the absolute humidity of the air. In a sealed crawlspace the humidity of the crawlspace should crudely track that of the conditioned space air (unless there is a vapor barrier between them) on an weekly-average basis. In a leaky crawlspace the dew point would track that of the outdoor air, whether the house is sucking air up from the crawlspace or not. The air conditioning will dramatically lower the dew point of the conditioned space air.
The duct plan looks like they threw a supply duct at (nearly) every window, but it's not clear where all the returns are, or the relative sizing of the returns. Many rooms have only one register, presumably a supply with no apparent return. When the door of a room with only a supply register is closed, that pressurizes that room relative to the rest of the house (and to the outdoors) while depressurizing the rest of the house relative to the outdoors. If you have air leaks in the floor (100% guaranteed!), the air-leaky crawlspace becomes part of the return path. With a sufficiently large gap at the threshold of the door the pressurization is pretty small, but jump ducts and wall or door grilles are another way to lower the impedance of the return path within the overall pressure envelope of the house, minimizing the amount of return air pressure equalization via the "great outdoors". More:
https://www.greenbuildingadvisor.com/blogs/dept/musings/return-air-problems
https://www.greenbuildingadvisor.com/blogs/dept/musings/all-about-furnaces-and-duct-systems
Unless the skirting around the perimeter of the crawlspace can be made truly air tight to the ground vapor barrier, and the ground vapor barrier perfectly air tight to the piers you may not make be able to make much headway against air-handler or wind-driven infiltration into the crawlspace, and the dehumidifier would effectively be trying to dehumidify the great outdoors. Houses with CMU or poured concrete foundations on the perimeter rather than non-structural skirting are usually easier to air seal reliably at the foundation. But yours may be one of those cases where it's better to sheathe the bottom of the joists and air seal a the sheathing layer. Using 1" rigid polyiso insulation as the sheathing, cap-nailing it to the joists makes it pretty easy to air seal using a high quality foil tape or housewrap tape to seal the seams, and can-foam to seal the edges and penetrations. The foil facers are true vapor barriers, and having R6 of insulation on the bottom of the joists keeps them warm enough to prevent condensation, both winter & summer. Air seal the band joists before sheathing it all in.
As installed the batt insulation doesn't look very effective, with lots of gaps that would allow convection bypassing, and doesn't even have an air barrier on the bottom. They appear to be supported by stiff steel wire bails or something(?). Do they have a facer on the other side? Is there air between the batts and the sub-floor? What is the nominal R? (R19 would be IRC code-min for your climate.)
The batts need to be re-installed, whether or not you end up sheathing the bottom of the joist bays. As you re-install it, sealing all of the seams & penetrations of the subfloor is worthwhile from an energyiuse point of view, and will reduce the volume air handler driven pull of outdoor air into the crawlspace. To perform at it's rated R, batts have to be in contact with an air barrier on both sides, and have no gaps or compressions. If the batts have kraft facers and are not full-depth it's usually easier/better to snug them up to the subfloor as the top side air barrier, and use the facer as the other air-barrier. A kraft facer is not a great air barrier from an air infiltration point of view, but is way better than nothing, and will improve the as-installed performance of the batt. The air sealed subfloor would serve as the primary air barrier. If the batts have no facers, you'll have to come up with some other plan. Flexible broadsheet goods like housewrap can serve that purpose without creating moisture traps, but it's neck-breaking work, hunched down in a crawlspace, to be sure.
Well I've pretty much made my mind up. I'm burning down the house and starting over with a slab.
Not really, the wife wouldnt approve. I hope to have the crawlspace "encapsulated" in the next 2 weeks. The larger dehumidifier will be here tomorrow and I'll get it installed this week (I know the crawlspace needs to be sealed properly first but what can it hurt besides my power bill). I will begin trending dewpoint along with outside air temp so I can post back with results comparing outdoor temp to my crawlspace temp. after I get everything dried out. I really appreciate all the comments, help and discussion regarding my problem. Its a really overwhelming feeling (building your first house) when you put so much thought into designing a home, hiring contractors, selecting building materials, and get moved in only to start finding problems that you could have avoided. I put more thought into building my home than any other person I know. Most houses in south GA just aren't built to these standards and trying to explain to contractors why I was making some of the choices I was making.... well let just say alot of them just looked at me cross-eyed when it came to foam insulation, tankless water heaters, building automation system, submetering, sealed attic, etc..
Again I truly appreciate all the input from you all.