Will a higher R-value in the wall and sealing compensate for the absence of a slab-edge insulation?

We are building a Built Green home in WA state where we have a mixed climate with hot summers/cold winters. The concrete sub did not intall a 2×4 where the slab meets the foundation. The walls are R-28 and the ceiling is R-50. Will the walls and ceiling make up for the lack of insulation at the junction. Energy Star requires an R-5.
GBA Detail Library
A collection of one thousand construction details organized by climate and house part
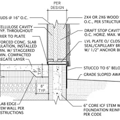
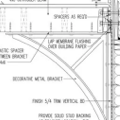
Replies
Kris,
The brief answer is no. You really don't want a bleeding energy leak like this — a glaring thermal bridge — for the life of the building. While adding more insulation to your attic could, in theory, lower your energy bills slightly to make up for the lost heat at the foundation perimeter, there are other issues, including comfort and potential mold formation, that the attic insulation will never address.
However, all is not lost. It should still be possible to come up with a way to insulate your foundation. You write that the sub forgot to insulate "where the slab meets the foundation." Give us more details:
1. Is this a basement slab or a slab on grade?
2. What type of foundation wall is the slab meeting?
My first reaction is, "Insulate the entire exterior of the foundation." But I'm not sure yet what your foundation looks like.
It is slab on grade and the foundation wall is concrete.
As a follow-up to the above does anyone have know of a way to create a thermal break where the foundation wall meets the slab. I am planning on insulating on the outside of the poured concrete foundation wall and under the slab. I am however having a problem in determining how I can achieve a thermal break where the foundation wall joins the footing. If I was insulating inside the foundation wall this would not be much of an issue but I want to insulate on the outside and use the walls thermal mass to moderate diurnal temperature fluctuations.
I had considered opartially achieving this by iusing a layer of ICF block on the foundation slab and then pouring the wall on and into the ICF with rebar tying it all together. I was told however that "code" would not approve this.
Does anyone have any suggestions?
Don
What we typically do is pour the slab to the wall with a 2x4 between the slab and wall. Then we remove the 2x4 and insert a 1/2" foam board and fill the space with concrete. This create the thermal break and gives it an R-5 value. We are worried about moisture because we are laying bamboo flooring. We sealed the area with a moisture barrier but still worried about laying the bamboo. The bamboo will be glued down.
Kris,
Your options are:
1. Cut back the concrete slab with a concrete saw, demo a concrete strip, clean out the trench, and fill the trench with rigid foam or closed-cell spray foam. If the specs require insulation at this location, and the concrete sub didn't do it, then the work should be done at the concrete sub's expense.
2. Install exterior rigid foam insulation on the outside of the foundation wall; protect the foam with fiber-cement sheets, stucco, or metal flashing. Be sure to carefully flash the junction between the siding and the foam protection board. This detail is shown on our GBA Web site here:
https://www.greenbuildingadvisor.com/cad/detail/monolithic-slab-cold-climate
By the way, there is no 1/2-in. foam board that provides R-5. The most commonly used foam board for foundation insulation is extruded polystyrene (XPS), which has an R-value of R-5 per inch -- so 1/2 in. would provide R-2.5.
The material we use for the 1/2 foam is actually a P-2000 product. You can see it at http://www.P2000insulation.com. Thank you for your answers.
Kris,
Beware; marketers of P2000 insulation are notorious for running afoul of authorities due to their exaggerated R-value claims. P2000 insulation has an R-value of about R-3.8 per inch, so 1/2 in. of P2000 has an R-value of about R-2 or less.
To learn more about P2000, see
https://www.greenbuildingadvisor.com/blogs/dept/musings/beware-r-value-crooks .
Thank you. Good to know.
Martin,
While I agree with you about R-value scams, to be fair to R2000 it must be noted that they are claiming R-10.2 for an assembly not the insulation itself.
Including 3/4" and 5-1/2" E-0.05 air spaces and 1" of R-3.87 foam board, their ASTM C1363 test results are not far off the mark.
But using a low-E material tight to a concrete slab (like with the bubble foils), offers no radiant advantage.
Robert,
Unfortunately, your faith in the accuracy of P2000 marketing claims is misplaced. There have been many documented examples of P2000 marketers claiming an R-value for their product that is actually an assembly R-value, not a product R-value -- claims that are so unclear (and illegal) that purchasers like Kris believe that when the product is sandwiched between a slab and a concrete wall, the foil adds to the R-value. An example of a misleading claim was provided in my report (the table used for the illustration).
We do use P2000 as a thermal break on the house but do not claim any R value. The P2000 salesman provided us with documantation "verifying" it's R-value. However we do not think there is enough there to matter.
One of the big issues with the P-2000 is the fact that it is a radiant product. It may work just lovely in walls or ceiling where there is an air gap across which the radiant properties of the material can work, but if it is buried in/under the concrete, it is not doing any sort of radiating, only conducting. I've seen it in basement slabs and it doesn't insulate well at all.
Kristine, sorry for the hijack, but instead of installing and then pulling out the 2x4, why not just use 1-1/2" foam as your thermal break and leave it in there after the pour? If you're concerned about the top of the foam showing you can taper the top edge on a tablesaw before installation.
Did you install a vapor barrier and/or foam insulation under the slab? That will have an impact on moisture issues as well.
Yes we did install the vapor barrior and foam insulation under the slab. I like the 1-1/2 foam for future projects. We glued down bamboo for the flooring. Any opinions on that? We are in a hot/cold climate in the Northwest but not damp.
With insulation under the slab, condensation due to the slab being cooler than the air should be minimized. A vapor barrier should mitigate moisture movement up from the earth. Considering how dry eastern WA is, moisture issues are not as large a factor as they would be in western WA or the northeast US anyway--but they are still a factor.
I've never glued a wood or bamboo flooring to a slab, but it sounds like you have taken the proper steps to ensure success. How long did you allow the slab to cure? Did you check the moisture level of the bamboo or the slab?
I must also apologize for the hijack but this thread seems to be the closest active thread i can find after extensive searching for a solution to my issue. My existing house has a 4" slab with no footings and wood siding. The edge of the slab is completely exposed, in fact small animals have tunneled underneath the slab. I would like to dig down to frost depth and simply simply install rigid foam vertically on the slab edge. My issue that is it wont be easy for me to do the entire perimeter in one shot and i am worried that i might create air pockets between the soil beneath the slab and the interior face of the rigid foam board. I am not worried about the load without footings as the load has not caused the slab to break though the coldest Michigan winters for 40 years. I have been trying to come with the simplest solution and can't. Can anybody help me!?
Dear Kzoo Kid,
Your proposed insulation retrofit idea is probably doable. However, if you think you lack the skills to complete the work, that's a pretty good sign that it's time to call in an experienced contractor.
Michael, the concrete cured for eight weeks and we had the bamboo sitting in the house for eleven days before we laid it. The outside temperatures were 80's and 90's during that time. We moisture tested the concrete before we laid the floor.