Waterproofing Paints and Foundation Walls

So I asked this question and I did get a lot of help but I thought I would rephrase my question. DC mentioned at worse waterproofing your walls from interior with paint like drylok can cause walls at worse to rupture or collapse because water pressure has no where to go. The way my basement is set up 2 walls are not underground. 1 wall is buried under my front concrete patio and 1 side wall is buried half in dirt. Obviously this is only side I ever see moisture coming from. Not liquid running water but moisture, mostly from floor coming up. So the question is how dangerous is using drylok? Do I have a high chance of complete foundation collapse? I do not plan to cover concrete behind walls. What is a safe membrane to use if any? Can I only waterproof membrane the floor? Is there anything I can use to make concrete walls white? Mike mentioned using wbitewash on walls. There is an article on this site that tested the different waterproofing products but they did not mention the risk of wall collapse or damage.
GBA Detail Library
A collection of one thousand construction details organized by climate and house part
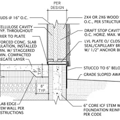
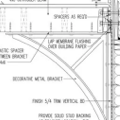
Replies
Joe, coatings like Drylok or parging will not cause a foundation to collapse. They won't hold a failing foundation together for long, but if the foundation is in good shape the coating will flake off from hydrostatic pressure and/or vapor pressure long before the walls cave in.
In my opinion anything applied to the interior of concrete as waterproofing is a Hail Mary play with almost no chance of long term success. The amount of relentless force water applies will win in the end.
To win in the long game you have 2 options
One on the outside slope the ground so the water drains away from the house combined with a footing drain connected to daylight is the best and most expensive option.
Two collect the water after it enters and pump it back outside.
The paint will not make the walls collapse! The paint will flak off the wall and look like heck is the worst case. On the floor old could limit your flooring option.
Understand with an old house a truly dry basement is a very rare thing. Back then people did not consider a basement as living space. Damp and musty with an inch of water from time to time was normal and expected. They put the furnace up on blocks so it would be out of the water and you could store stuff if you kept it up off the dirt floor. You trying desperately to turn the old basement into living space on the cheep is bound to fail. If you do not have the budget for egress window and a drainage system, I say save your money until you do.
Walta
A concrete wall can withstand water pressure. Think about all the swimming pools out there, small dams, etc. Water pressure on a typical basement wall isn't going to collapse the wall. The only issue that can SOMETIMES come up in SOME situations is where the wall fills up with liquid water that would have otherwise leaked out, and then that water freezes INSIDE the wall. The freeze/thaw cycles can break up the block. It's not the water pressure, its the expansion of the water as it freezes. This is the same process that causes road surfaces and other outdoor concrete things to break up over time from freeze/thaw cycles.
In the vast majority of cases, water proofing paints don't add any risk to your wall. Just be sure that you've done everything you can on the exterior to stop bulk water problems (slope the grade away from the house, put up gutters, drain the gutters away from the house, etc.), so that the waterproofing paint is only the last barrier and isn't constantly dealing with huge amounts of water.
Bill
Before I moved in there was some work done underground to divert water (this is a family home). Basement use to flood but now it seems dry but the floor always looks damp in some spots. Last summer I sloped dirt away from the home into a gravel pit away from house, I looked at a diagram of underground gutter on here. Still seems damp though. I know the slab is super thin, maybe a quarter inch, I patched a hole one time and saw the actual thickness. Must have been an old dirt floor that was covered at one point. Basically without ripping out the entire slab and starting over it will be a constant battle. Cheaper option would be to build up floor with foam and wood but I don’t have much ceiling height. I’m also scared to play with an old basement, every thing gets wonky in an old house, just wasn’t meant to be living space as someone said. That’s why I’m looking for a system of constant maintenance. It won’t be a situation where I can cover walls or floors until major renovation. I’m hoping with an addition on the side of house I’m planning soon that some of the problems will be alleviated when they dig for a new footing on side of property. My plan for now is to drylok the walls, use something on the floor to seal it not sure if you guys have any idea. Drop down foam tiles or rubber tiles on floor and just check on what’s going on periodically underneath and on walls.
1/4" doesn't really even count as a slab, it's more of a "smooth out that concrete I spilled over there" kind of a thing. I can't even see how that would hold up at all.
You could use some of the fiber reinforced resurfacer/leveler stuff to build that slab up a bit. The fiber reinforced material is much better if you're stuck with having to do a thin layer. This might help cut down on cracking and make the floor a little better before you put the tiles down.
Bill
Joe G,
FWIW I sealed off a very water prone block basement with Thoroseal mixed from powder (not the premixed) about 1990. I left the house in 2012 and it was still doing its job. The floor like yours was a thin skin of concrete over dirt that was done in sections - badly. While all the effort put into redirecting downspouts helped certain areas of wall, the floor remained a damp mess to the day I left. Putting anything like foam or plastic tile over a damp floor will only insure a mold farm. Your choice, but if you want to live down there and not end up with a wheeze, consider biting the bullet and fixing the floor slab.
Roger, you are the second person to mention theroseal today and I never even heard of it. Is this the green building gods talking to me? What about using tile or that ceramic tile that looks like wood and putting soft foam on top of that?
Joe G,
At the time I was rehabilitating my basement, I was also renovating a different basement with several cracks and weeping form ties. The gentleman doing the crack sealing was both chatty and helpful, directing me to Thoroseal, which is perhaps more frequently used to seal silos and water tanks. He cautioned me to be sure I used the powder form and followed the mixing instructions exactly, not to add water for easy mixing or brushing. I did buy it at his favorite concrete supply shop which carried many wonderous products not then seen at consumer box stores.
At the time, it came in gray or white, perhaps it does still. The mixed product is very thick, but not so thick it could be troweled. Fortunately, I was young then and my wrists hadn't given out, though I thought they might after brushing three walls totaling 300 plus s.f. with two coats. If you do go for the Thoroseal, find a mason's brush and cut the bristles back to about 2 1/2 " to make them less floppy. The brush will need to be loaded more often, but the handling and film thickness is more controllable. I was doing block which had a fairly coarse texture, so perhaps a cast wall will behave better. I used a strong TSP solution to wash everything before I started. The tuck pointing repairs were also done before coating.
As to dealing with the floor.... I am not sure what to say that won't potentially march you out on a limb. I gave up any hope of salvaging my floor due to water lurking just below the surface in a few spots. I tried the patching concrete once to fill in a low spot, but that failed after about 10 years. By the twenty year mark one patch erupted with a magnificent crystal farm. Before attempting any surfacing of the floor, it is paramount to establish water control outside. If possible.
Despite very careful efforts to control gutters and drainage paths, I had to finally surrender to the fact that the house was built into a hill and most likely I was dealing with water flowing along some subterranean path. You mention two walls are above grade and one is half buried with the last protected by a concrete patio. Have you closely watched how water is distributed by the patio? You may yet have a repeat water offender lurking at the side edge of the patio. If you have a large hard surface tipping to one point, then grading the soil will only help so much.
If your basement slab is less erratic than the one I had, AND you are a gambling sort of man, then perhaps setting a porcelain tile like the wood plank you mentioned would cap off most of the moisture load. Unfortunately, I have set that type of tile and on anything less than a dead flat surface will present many problems keeping them from presenting high corners. A smaller square tile like 10x10 will be a bit more forgiving on a wavy slab, though still fraught with peril. Setting tighter than normal to reduce the grout lines and thus the transmission surface of slab moisture MIGHT make the basement palatable. At least it won't actively support mold like a foam tile would. My work station floor mats were very grotty underneath as they trapped the rising moisture. Since I was filing and grinding stuff there, the floor mat was just one more icky feature. Downsides include the floor erupting and breaking the tiles.
If you are open to left field ideas, then I would suggest thinking about using pre-made deck tiles made of teak or at least cedar. This would allow the floor to give off its moisture to the air and simultaneously retain access if needed. Dropping pens and other things might make such a floor annoying, but some deck tiles are set close enough to not let too much through.
Level the tiles as you go with plastic shims and use a long 2x4 or similar to keep the overall field mostly level.
I will disclaim any proof if viability or liability, but hope this helps your thinking as you proceed. I know how tough it is to make do on a tight budget, I had plenty of years trying to do the same.
Deleted
Roger,
Had to look over this post for your instructions on thoroseal. It has since been renamed masterseal, maybe they were bought out by another company. About to tackle this project in a few weeks but ran into a dilemna. I have heard of contractors using thoroseal, it has certainly been around a long time. You also know it held up from experience. Drylok is latex based while thoroseal is cement based. Is thoroseal a stronger waterproofer because it is cement based? Thoroseal is worth the extra effort if it is a better product. Does it make a difference or is drylok just a newer product that is easier to use? I also wonder about perm rating, DC recommended a low perm rate in my post about carpeting a basement. Thoroseal says it has a perm of 12 (0.1), drylok I can’t find those specs. Anyone think one should be used over the other? Maybe just on what it is made of to begin with? Again these walls may remain unfinished with just the waterproof coating.
The only negative (interior) side waterproofing I've seen used is Xypex. It's a crystalline waterproofing advertised for that purpose, made to react in the presence of moisture and clog the pores of concrete.
I've only seen it used on commercial projects. "Patch n Plug" at the footing/wall intersection and then a coat of their "Concentrate". Solved a wet elevator pit issue below water table. No joke.
Hammer,
Thoroseal is still very much out there. The MasterSeal is BASF as are Thoroseal trademarked items. The MasterSeal seems very similar to what I used, just packaged in a 5 gal bucket for more convenient mixing perhaps. They date to 1912. You want to block water and moisture so one might logically look for low perm numbers. Xypex might be useful if a cast foundation, but it is colorless and migrates into the concrete. It is not useful on cracks greater than 1/32 according to their own literature. I used it as an admix for my entire foundation pour - footings and walls. My wood shop is dry as a bone so I am happy.
Regarding Thoroseal, there do seem to be variant forms of the bagged powder - T1180, T1018, T4002. I can't get to the Thoro.com site due to insecure certificate warnings from my virus program. Same for ThoroProducts.com If you are braver than I, you can google the two sites and see what you get. I am attaching two sheets I did manage to download, one from Belgium? the other from the Depot. The depot sheet pretty much outlines exactly what I did. Remember that a full bristle tampico brush is going to be a crappy applicator. Shorten the bristle length and you will find it much more useful. You might also find certain small kitchen brooms amenable. Just cut the handle down.
55 years ago when I worked part time in a hardware store, one of the "animated" displays we put out was from UGL Drylok. It was composed of a standard cinder block sitting in a tub of water with a small fish pond pump that squirted water into the two cavities. One half of the block was coated with Drylok, the other half raw. Water would pool up to the top of the closed core thanks to Drylok and the other core would never fill, the water weeping out too fast. Made a very convincing display. I think Drylok probably is still a good product, but I have not used any.
My very weepy cinder block basement would have sucked up an exorbitant amount of Drylok thanks to the very coarse surface. Plus, brushing it into a zillion little pits to ensure coverage would have been a true nightmare. If you have a cast foundation the coverage rate will be much more palatable. How full of little air bubble pits and unconsolidated aggregate patches will inform your ultimate decision.
Do consider dollars per coverage when choosing. The Thoroseal for my circumstances provided better overall coverage thanks to the "pancake batter" consistency filling the pores and texture much more quickly. The second coat I put on selected areas spread very well and coverage was greater. Drylok on a cast foundation might provide excellent coverage. You will need two coats to make the wall tight. There is a newer Drylok EXTREME, which has a 15 year warranty and greater static water resistance claims.
One thing to observe no matter your final product choice is CLEAN THE WALLS. There are no short cuts if you want success. I used heavy TSP first round, bleach and water second round, a rinse, and spot kills with full bleach. All with wire brushes and hard bristle scrubbers. No basement more than a few years old (and I would still wash once minimum for new walls) is going to be clean enough for direct application. The residual forms oils/release agents might not be visible, but still exist as a hydrophobic film. The addition of cobwebs, and whatever forms of combustion residues and biological goo that has accumulated will all need to be scrubbed off. Almost all paint failures, caulking failures, taping failures I have seen or had to remediate basically failed due to poor preparation of the surfaces.
It took me three weeks of after work and weekend time to prep and seal my three block walls. (one was entirely above ground) It will be major PITA no matter which product you select. Just know that getting it on the wall right means peace later.
Hi Roger thanks for the advice. It will take time to clean. I’m having my walls resurfaced beforehand so hopefully it will be less surface preparation. I’m assuming even with a new layer I would at least need to bleach and scrub it down? Also a new surface needs curing time before using the thoroseal. One of the instructions you linked said wall and floor application. I wonder if this has ever been used on a floor. It reminds me of turning the entire basement into a swimming pool liner. Yet I have never heard anyone using this for anything other than walls. This will take me some prep time, I have 2 small kids so they will probably need to leave to vent this stuff out, not sure if it has a smell to it. Drylok is certainty easier to use but I don’t think it as strong as thoroseal.
Hammer,
I do hope whoever is resurfacing the walls is prepping before hand. Couple of questions. Why are you resurfacing them if you plan on Thoroseal/Drylock? What are they resurfacing with that won't give you a more water tight finish? If they do a good job prepping the original walls and leave you with a new surface of ??? then ask if there is a cure time before adding the Thoroseal. I would think no prep would be needed if no bugs, mildew, or efflorescence is present. Might try contacting Thoroseal or a local concrete supply store for additional real life input.
As I best recall, the Thoroseal merely smelled like wet cement, which it sort of is. I haven't smelled Drylok in so many decades that I would hesitate to say anything. It is latex based, so one might expect it to be like latex paint. Some paints are stinky some aren't.
I suppose you could make the basement into a pool if the floor will take the load. Thoroseal was pitched to me as being what they used on grain elevators and water tanks. I have seen references to coating actual outdoor pools and fish ponds, but I think the water chemistry needs to be controlled so as not to kill the fish by introducing them too soon after. I guess the new tank smell needs to be flushed out.
Roger,
The wall has some areas that the concrete has flaked off or deteriorated over time, not in a structural way. The walls are parged cement over stone if I’m wording that right. I might end up with more watertight walls from the resurfacing alone. The thoroseal will give it a nice clean white finish look, and make it more water tight on top of what I’m doing already. With a new layer much of the prepping will be done and I will have a clean surface to work with, would make it much easier for me to apply thoroseal. I suppose you can somewhat resurface with thoroseal but I’m thinking it wouldn’t be thick enough to really give some spots a flat surface. It would probably work on small holes or chips but then again I’m ridding myself of some of the prep work by doing this.
Hammer,
Not to be the endless Cassandra, but it might be worth your time to take a small hammer and tap at the parge coat before it gets re-parged. If the parge is well adhered to the stone and mortar between them, tight parge should go "plink". If it has debonded from the stone or mortar it will have a duller sound. Try near a known flaking spot and work outward to get an ear for it. If everything "plinks" the same, wonderful. Shining a light to skim along the wall might reveal subtle blisters that should be tested. Just best to find any weaknesses now.
You are correct, the Thoroseal , even as thick a coating would not level a surface. The white finish is slightly sandy looking if my memory is not completely shot. The brush marks will be present at the end, so work with that and treat it like a stucco texture if no further walls are being built.