Wood, Air and Water: The interplay of temperature, humidity and wood moisture content

I’ve been thinking about the interplay of temperature, humidity and wood moisture content, and I’ve put together a synthesis of some things I’ve been thinking about, and some counterintuitive conclusions I’ve reached. Wood moisture content is important, you want to try to keep it constant in buildings because wood can change dimensions when the moisture content changes which can lead to warping and splitting of the wood and in structural members can lead to distortion of the structure. You also don’t want it getting too high, if it gets above 15% you can start seeing corrosion of fasteners and above 16% you start seeing mold and rot. There is a complex interplay between the moisture content of wood and the air, for a given set of temperature and humidity wood will reach what’s called equilibrium moisture content or EMC. At this site is a chart of EMC vs. temperature and relative humidity, which I’ve used for my calculations: https://www.woodworkerssource.com/wood-moisture-content.html Note that while air absorbs more moisture as it gets warmer, wood works the opposite way and absorbs less moisture the warmer it is. If you have a sealed system of some wood and some air, when you warm it moisture will flow from the wood to the air, and when you cool it moisture will flow from the air to the wood. Note also that at a given relative humidity, as the temperature increases the EMC decreases. What I wanted to look at was the impact of absolute rather than relative humidity, because often when you’re thinking about moisture you’re working with assemblies that span different temperatures. So I took the chart of EMC vs temperature and humidity, and working with air moisture capacity numbers I made up a companion chart that is EMC vs temperature and dewpoint. I’ve attached a screenshot of the chart as an image, if you want to dig into the numbers I used I’ve uploaded the spreadsheet to: https://docs.google.com/spreadsheets/d/1PmunKPhShzuZR-oZeajEQu8gWiVbTvvy/edit?usp=sharing&ouid=111289139815730196554&rtpof=true&sd=true I guess the big takeaway is that wood is really sensitive to temperature. At higher temperatures it’s hard not for it to be dry — think the framing in an attic. And at cool or cold temperatures it’s hard to keep it at a safe moisture content. I have to think about that a bit because lots of houses have lots of wood that is exposed to winter temperatures, I don’t know if it’s OK because it can dry to the exterior or that microorganism growth slows way down at cooler temperatures. Similarly, the usual building science advice is that assemblies that unable to dry to the exterior should be kept above the dew point so that condensation can’t occur — the red zone on the chart. But wood can be damaged by moisture at temperatures above the condensation point.
GBA Detail Library
A collection of one thousand construction details organized by climate and house part
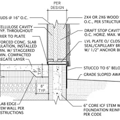
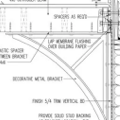
Replies
Have you explored the tons of data the USDA has about wood. I would be shocked if anyone could think of a wood related question, they have not funded a study about.
https://www.fpl.fs.usda.gov/
Walta
This is really good info. I can see why I'm struggling with dimensional stability of my bamboo flooring (besides the fact the bamboo has stability issues) over heated floors. When the floor is heated up, to maintain the same MC, the house has to be much more humid than simple calcs would suggest which is what I found empirically.
Thanks.
Yeah, as an example if your house is at 70F and a dewpoint of 50F, which is 50% RH and a pretty comfortable indoor condition, the EMC is 9.0%. To get that with a temperature of 100F you'd have to have a dewpoint around 80F. If the underside of the floor is at 100F and the room is at 70F you'd have to have over 100% RH (which is impossible).
This is fascinating. I have no business learning about this, but I find it really interesting.
When you say you don’t want MC getting too high, above 15%, that seems extremely low. Is that the actual MC of the wood rather than the interior conditioned space RH? So if my house is 70F and 40% RH does that mean it’s damaging the wood like flooring, cabinetry, framing, fasteners etc?! Or not so much with a vapour retarder behind the drywall at least for the structure?
On that note… our vapour control layer is going on really soon, maybe next week, and I believe the edges are to be lapped not taped as apparently the ROI is low for the labour to do the taping. We are using Intello smart membrane. Outside the 2x6 framing is 4” EPS with Tyvek on top.
While RH and MC are both expressed in percent, they aren't the same thing at all and the relation is complicated, that's kind of the point of this post.
Moisture content of wood is expressed as a percentage of the dry weight of the wood. While it varies by species it's generally assumed that 28% moisture content is saturation, beyond that the water drips out of the wood. That would be analogous to 100% relative humidity for air.
Note that on the chart in the original posting, when the dew point equals the temperature -- which means relative humidity is 100% -- the equilibrium moisture content is always 28%. Beyond that there's no fixed rule for the relationship between EMC and RH.
In typical Midwestern home that is heated to 70F and 40% RH the wood will have about 11% moisture content. If you live in a swamp or a desert it will be higher or lower by 5% or so.
Walta
Ahhh, I see. So kiln dried wood is like <19% MC which isn’t as “dry” as it sounds… 12-14% is better. So it seems keeping the temp around 70F and 40% RH is a good idea, that’s all I can comprehend for now. And for those of us who like it a bit warmer than that, say 75F and 50% RH, that isn’t necessarily bad because the warmer air is holding more moisture so the wood MC is not going up as much as if the temp were lower? Tricky to balance the low moisture content for wood and the very high moisture content for humans.
I don’t understand how a typical vented attic assembly holds up through winter in a cold climate. It’s a relatively confined space, low temp, full of wood. Are we to assume the wood MC is extremely high? How does it not rot then? According to the chart, the wood should be fully saturated.
Of course, now I want to buy a moisture meter to test wood. Completely unnecessary.
The vertical scale on the chart is dew point. In the winter dew points are low, outdoor air is going to be in the green zone.
Oh, duhhh! I assumed the temp goes below DP when it’s really cold, now that I think about it that’s not even possible. I had forgotten what the dew point even is because it seems the temp is never dropping below DP… This should give hope, if I can someday understand this stuff then so too can anyone else.
I’m curious what you do for work DC? You and several others on this site seem to know quite a lot about a range of topics, which has me wondering how.
Lets think about air infiltration leading to moisture in the wood structure of the home.
# Direction and humidity
Where there are cold winters air infiltration will be dry and help to dry the wood. Humid indoor air that exfiltrates the house can moisturize the wood, although the effect is reduced to the extent the wood is warmed.
When it is humid outside air infiltration will add moisture to the wood. Exfiltration of drier indoor air will dry the wood. However, if the air is cooler indoors but not dry enough, it could lower the temperature of humid air coming in from outside and thus contribute to moisture.
# Stack Effect
The stack effect will push hot and possibly humid air out the attic/roof in the winter and in through the attic/roof in the summer. Attic/roof ventilation may be able to normalize humidity to mitigate this effect. However, air ventilated to the outside can still be exposed to conditions with very high humidity.
In the summer cool air will exfiltrate out the basement- whether it is also drier may depend on whether a dehumidifier is ran in the basement.
# Ventilation
Most houses have more exhaust than supply in their ventilation and thus are likely to leak air in from parts of the wood assemblies closer to exhaust points.
In hot and humid climates some advocate for ventilating dehumidifiers. They will both dry the indoor air and positively pressurize the house- seems ideal for protecting the wood. The cheapest way to provide fresh air is to connect a supply directly to the furnace- helping to keep the house positively pressurized. Switching that to an ERV goes from positive fresh air to balanced. Any exhaust ventilation that goes out the ERV will not de-pressurize in the house, but other exhaust will have a greater effect if there is no supply. The ERV (those that support it at least) can be setup (in the summer) to introduce a mild amount of positive pressure to counteract exhaust. The kitchen range and dryer exhausts may have the largest exhausting effect.
# Air conditioning
In the summer, the dehumidification of air conditioning would have a drying effect on humid air infiltration. However, the cooling of the air risks lowering the temperature of infiltrated humid air and having water condense on the wood.
# Wind
A strong wind can induce more air infiltration than any of the other effects discussed. The air might come in one side of the house and go out another. So at any time of the year there can be a net inflow/outflow in any spot in the house.
# Conclusion
The information posted here showing wood being more resilient at higher temperature would temper the negative effects of humid summer air infiltration. However, it may heighten concerns of humid air exfiltration in the winter.
Humidity differentials determine the effect of air interchange. The main driver of air interchange on windy days is wind. On calm days, it is the HVAC system.
Several temporary conditions can lead to wood gaining moisture but drying back out when those conditions revert. The question is then has any damage occurred in the mean time?
Prolonged outdoor very high humidity conditions can lead to the wood gaining too much moisture. This can occur at cooler temperatures in the Pacific Northwest. At hotter temperatures it can occur in the Southeast and sometimes in other areas of the eastern US.
A greater threat though may be what the HVAC does to the air. Cooling air without enough dehumidification can have a moisture inducing effect on wood. This may be seen the most on humid summer days at the basement rim joists due to the stack effect. Warming air and humidifying can have a moisture inducing effect on wood (on cold windy days).
In general you don't have to worry about outdoor air, in the winter it has too little moisture content and in the summer wood has too little ability to absorb moisture. What you worry about most of the time is indoor air when it's cold out.
I can think of two exceptions. One is when it's cool and humid. There have been reports here of houses in the Pacific Northwest with vented roofs having moisture problems. The second is when it's hot and humid outside, and cooler inside. You see this a lot in basements in the Northeast and in the Southeast in air-conditioned buildings.
Thanks, my comment was a work in progress and was definitely missing winter air exfiltration besides the roof. Generally though houses are under negative pressure and air is instead infiltrating and drying. Wind would cause exfiltration on one side of the house. And if that part of the house does not experience air infiltration when it is calm and exhaust ventilation pulls air in then it won't dry as quickly. Still with very dry air it should dry back out when the wind calms. The main issue might be wraps/membranes that prevent drying?
It’s going to take me a while to absorb all of this.
I can’t stop going back to the problem of the air pressure balance. Depressurization complicates all of this, yet it seems pretty hard/expensive to avoid. Because most people do not measure it, maybe it seems like a non-issue. I know this is sort of a different topic but it seems like something we should be able to control fairly easily. We can’t control the wind, I accept that. I will post separately so as to not hijack this topic to ask about programming ERVs.
Deleted