Workshop Foundation: Crawlspace or Raised Slab

I am planning to build a workshop (36’ wide by 32’ long) and I’m trying to decide upon the “best” type of foundation. I live in southern middle TN, so that puts me at the very southern edge of Zone 4 (mixed-humid) from a climate point of view. The shape of the building will be simple, a gable roof from front to back and no plumbing will be installed. (See attached sketch.) There will be one interior wall that divides the interior space into an area 24’ wide on one side and 12’ wide on the other. The 12’ wide area will definitely have a concrete slab floor (so a vehicle could be parked on it) and the 24’ wide area will be the workshop (used primarily for woodworking and misc. other projects).
There is a slight slope to the building site. The lowest corner is approximately 26” below the highest corner of the building. If I go with a slab foundation for the entire building, I assume that means it will need to be a raised slab (a poured concrete footer, CMU foundation wall, interior filled with gravel to make everything level, 6 mil poly and 4”-5” concrete slab). If there’s a simpler way to build a slab foundation on this lot, I’m very open to suggestions. I’m clearly not a foundation expert.
From what I’ve read on this website, a slab foundation has several advantages over a crawlspace. My biggest deterrent to a slab is that concrete is not very comfortable to stand on all day long. I realize that makes me sound like a whiner, but it’s an important factor. I have a brother-in-law that recently built a new house with a finished, stained concrete floor. If he doesn’t wear good shoes in his house, his knees start hurting. It’s a legitimate concern. I’m also not a big fan of placing anti-fatigue mats (over concrete) at various places in the shop. It’s difficult to get them placed everywhere you need them, they don’t cover a very large area and some of them are easy to trip over.
My ideal floor is a ¾” hardwood floor (with a plywood subfloor) over a standard crawlspace (wood floor joists). It’s nice to look at, easy to clean, equipment can be easily rolled around and most importantly, comfortable to stand on. I’ve seen examples of hardwood flooring applied over a concrete pad, but it usually involves setting 1 or 2 layers of plywood on the slab, then fastening the wood flooring to the plywood. That doesn’t sound very comfortable to me. I can’t imagine the plywood gives enough to make any noticeable difference. I found a GBA article “Installing Rigid Foam Above a Concrete Slab” which described how you could put foam above a slab, then 1 or 2 layers of plywood, then a wood floor but it didn’t say this was a widely used process. It said it could be done. Would the rigid foam provide enough cushion to be noticeable when walking on it?
Whatever the solution, I’d prefer to stay as close to “conventional” construction techniques as possible. There’s not an abundance of builders or crews with experience in energy efficient or advanced building techniques. The simpler the solution, the better. Is there a flooring material that can be placed over a concrete slab that gives the feel and characteristics of a traditional hardwood floor? Is there a significant cost savings to building a concrete slab versus a crawlspace if I still need a footer, CMU wall, gravel fill and the slab itself? I’m certainly not opposed to crawlspaces; I like the access and flexibility they provide to change things in the future.
Thank you for your advice and input.
GBA Detail Library
A collection of one thousand construction details organized by climate and house part
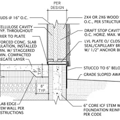
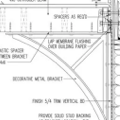
Replies
Your project sounds like a perfect fit for a thickened edge structural slab, except for the comfort part. A crawlspace will not be worth the cost if there is no specific reason for it, like plumbing. Also, as soon as you have a floor below grade like in a crawl space, you need to drain your foundation, which has its own challenges.
I would look at the structural slab and then look to get some form of matting, something durable like in a gym. Hardwood is not your ideal floor finish for a workshop for a variety of reasons.
My 2 cents.
Putting the plywood subfloor on sleepers -- 2x4's turned on their side -- should make the floor as resilient as if it were on joists.
Except for the parking pad there's no reason to have concrete. I don't have it handy but GBA had an article about a concrete-free foundation that I thought was clever. As I recall it was a concrete rim wall, gravel fill, vapor barrier, foam insulation sleepers and plywood subfloor.
I would make the parking area unheated and treat the wall between the parking area and the shop as an exterior wall. It's really hard to condition a space with a garage door.
Go with the slab, no question. Advantages to the slab include, but are not limited to:
1- STRONG! Place any tool anywhere you want, without worry about the floor load.
2- STRONG! Park your car in there if you want. Park MULTIPLE cars if you want.
3- STRONG! Pour a thick-edge as a footing and you can usually build right on the slab.
4- FAST! Get the ground ready, place some remesh, call for concrete... Slab is poured in a day. After curing, you're ready to start framing.
5- EASY! After curing, the floor AND foundation are done. No need to frame a floor.
6- EASY! Leave it as a concrete floor, or polish it, or epoxy it, or tile it, or... Anything that is OK on a slab is fine as a finished floor, or just leave the concrete AS the finished floor. This can save another finish step.
For a workshop, concrete offers a lot of flexibility. I like it for strength, which gives flexibility for placing heavy equipment. You just don't have to worry about it. It's also pretty immune to damage if you drop or spill anything on it. It is a hard floor, but you can get interlocking rubber mats to put down around a workbench, or wherever you expect to be spending a lot of time on your feet. I can also recommend the Dr Scholl's gel inserts for shoes, which I've found help me a lot when working and walking around on concrete floors all day in commercial buildings.
I would put down a vapor barrier under the slab at a minimum, and ideally I'd put some XPS under the slab for insulation. I would put remesh in the slab, on chairs so that it's near the center of the slab, which will greatly improve strength and cracking resistance for little additional cost.
Bill
I'm w/ Bill on this one. Concrete is very flexible in the short and long term. Good shoes and insoles are something that you should be wearing anyway if you spend significant time on your feet. And only put pads in locations where you spend a lot of time (eg, standing in front of the CNC machine).
Also, a cold hard concrete floor is way worse than a hard concrete floor; do the subslab insulation. You'll also appreciate it if the building ever turns into your doghouse/is converted to living space.
If you would like a wood floor that is comfortable to walk on that is built over a slab, take a look at end grain flooring. I have worked in several machine shops that had this style floor and it was extremely comfortable throughout the day.
https://www.jennisonwright.com/woodblock.html
Bluegoose68,
If you want a wood floor for your shop then I would do as DC suggested: Build a perimeter foundation of stem-walls on footings, prep the entire interior with compacted fill, pour the parking area as a slab, and on the workshop side put down foam and two layers of plywood.
If in the future the use changes, it's easy to remove the floor and pour the rest as a slab.
https://www.greenbuildingadvisor.com/article/the-concrete-free-floating-plywood-slab-assembly
I'd like to say a big "Thanks!" to everyone that commented. I'm taking your advice seriously.
Not much love for a crawl space around here; that's to be expected...
I'll give in and commit to pouring a slab. I need to talk with the builder and see if he prefers a monolithic slab vs the footer/stem wall/slab scenario.
I've been researching how to add insulation beneath the slab and to the perimeter. Unfortunately, the termite level at my location is considered to be "heavy" by those that decide such things, so that's a serious consideration. I've seen several examples of how to add foam to the perimeter of a building but most have the caveat "check with your local codes if termites are a problem". That's a pretty huge caveat. If anyone knows a reliable, durable, termite-proof method of adding foam to the perimeter of the slab, I'd love to hear it.
For those that suggested skipping the slab (using the footer/stem wall only) and building on the dirt, I appreciate the advice but that's a bridge too far for me. I've got enough moles in my yard right now I'd be concerned that they start burrowing under my new floor. I don't doubt that that method works, but it's a little too radical for my taste.
Thanks again.