Zone 5 – Different wall options

Building in Nebraska (Zone 5). Builder proposed 2×6, 1/2″ spray, then fiberglass batts.
I understand 1/2″ sprayfoam would raise condensation issues. In meeting with the builder soon, I will propose three alternatives:
-2×6 wall but 2″ sprayfoam, then fiberglass batts/blown fiberglass/cellulose, depending on price and availability.
-2×6 wall and 2″ rigid foamboard on exterior, then fiberglass batts/blown fiberglass/cellulose (my builder has not done this before and may not be comfortable with this)
-Double stud 2×4 walls with fiberglass batts/blown fiberglass/cellulose, just as shown at buildingscience.com (I doubt he has done these either, but this involve less of a learning curve?)
I realize the two latter options are clearly better than the first, but ultimately I’m limited by what builders around here are capable of and willing to do. Do these three options sound good? Am I safe using 2″ of sprayfoam in the first option? Also, if we do double stud, I’m confused as to the best way to reduce the risk of condensation. Any thoughts would be greatly appreciated.
GBA Detail Library
A collection of one thousand construction details organized by climate and house part
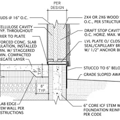
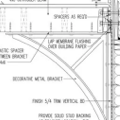
Replies
Cameron,
Q. "Do these three options sound good?"
A. Yes, but they are not equally good. The flash-and-batt option does not address thermal bridging through the studs, so it will not perform as well as the other two options.
Q. "Am I safe using 2 inches of sprayfoam in the first option?"
A. Yes. More information in these two articles:
Calculating the Minimum Thickness of Rigid Foam Sheathing
Why Flash and Batt Makes Sense
Q. "If we do double stud, I'm confused as to the best way to reduce the risk of condensation."
A. This article will help you understand the issues: How Risky Is Cold OSB Wall Sheathing?
Cameron,
For the double studs walls in climate zone 5 - please see attached detail. You practically build a conventional 2x4 house and tape all plywood airtight. Then add a second 2x4 wall and use a vapor open reinforced membrane (SOLITEX MENTO Plus) as a blow in membrane.
This will get you a good airtight/vapor retarder (or intelligent) layer on the interior - combined with a vapor open exterior. This will get you the safest wall, without depending on foam.
Other options for walls can be found here:
475 Details
With the 2" spray foam + cavity inside the stud cavity you've fixed the wintertime moisture loading issue, but still have a HUGE thermal bridging issue with the framing. A wood clad house with 2x6 16" o.c. (~25% framing fraction) with 2" (R13) spray foam + 3.5" (~R13) fiber may come in at R27-ish center-cavity, but is still only about R14-R15 after thermal bridging of the R5.5 studs.
With either 2" of type-II EPS (R8.4) or poliso (R12) the exterior and R20 fiber in the wall cavity the same wall comes in at R20+, and gives the sheathing far better overall drying capacity than the 2" of closed cell spray foam. EPS also delivers only 1% of the greenhouse gas damage from the different blowing agent used, and it's less money too:
The installed price of 2" EPS is about a buck a square foot, whereas the 2" of closed cell spray runs twice that. You're adding a bit of cost with the deeper the fiber, but not a buck a foot. With polyiso you'd be at about R25- nearly 2x the performance at about the same money.
Thanks Martin and Floris. That information is helpful.
Dana,
I appreciate the specifics. I am a bit surprised the thermal bridging factor is so high.
I understand what you're saying, and don't disagree. The problem is that flash and batt is considerably easier in this situation--the builders/subs are experienced and comfortable with it and it does not require significant framing/floorplan changes. So I'm trying to get a sense for how significant the differences are, how much additional work the two better options are, etc.
I apologize for my rant upfront, but this subject rubs me the wrong way every time, and it is meant to be good advise.... I'm always amazed why good folks HAVE to be satisfied with "just good enough" or "what is normal in my area". The fact is, you should not have to settle for what is unacceptable practice. You are paying a great deal for a good house and you should get what is right. If your builder or subcontractors do not know how to work with a good system of building homes, they should educate themselves in good practices or you need to get a good builder.
This is why most homes built today are less than acceptable, because people are satisfied with bear minimum code housing at best. If the price of your house gets to be higher than expected (mostly because of lack of education but contractors), then reduce the house size to the point you can afford a well built house with all the right systems in place.
Armando: no apologies necessary. But a few points-
-We are not doing merely what is normal in our area or good enough. Many other aspects of our house buck the trend significantly (we've got to be the only ones within 20 square miles without 3 car garage, for example). How many new construction buyers even learn the difference between spray foam and rigid foam (or have any idea how their house is insulated)?
-This is not really an issue of cost. Rather, it's an issue of getting the work done, period. I have had multiple subs in the past simply refuse to do this work when I called them to get quotes for these things, without even talking about cost. Good contractors SHOULD be hesitant to do work they are unfamiliar with, and if very few customers want a certain technique, it does not surprise me that there aren't green building experts all over. That said, I have not really pressed this issue with my builder, and he may be entirely willing--notice how I phrased this in my OP.
-Correct me if I'm wrong, but a proper flash and batt job as I described above is not "less than acceptable." It is not ideal, but it is certainly not unacceptable. House building is full of compromises, and even something as important as energy efficiency does not trump all other concerns.
-The insulation of a house, as you know, is just one part of the equation. Our house is very nearly square, with four walls and pretty much four corners, for example. The garage is attached but without living area above it. We plan to invest heavily in the HVAC set-up. Etc.
During the planning phase of this build, I've received lots of advice from lots of helpful folks, and it has immensely benefited our future house. I incorporate all of their advice to the extent reasonable and possible, but I will not make perfect the enemy of the good. Thanks for your thoughts.
Cameron,
In general, I admire your attitude. There is only one red flag: your statement, "We plan to invest heavily in the HVAC set-up."
That's too bad. If instead you plan to invest heavily in your thermal envelope, you should be able to install an HVAC system that costs much less than those of your neighbors.
Martin,
Again, we're willing to invest what is necessary to get as good of an envelope as we can. The question is what we can get done here. I can't force contractors to take my job, particularly when our market has picked up significantly.
I should say too that when I mean invest heavily in HVAC, I had in mind the possibility of a geothermal system, if that makes sense--not a system good enough to make up for a bad envelope.
Martin, I believe you were the one who mentioned (on another thread, if I'm not mistaken) that flash and batt can be a good system; am I incorrect here, that this is merely a matter of good vs. great? Should I really insist on one of the better two options I presented above?
Thanks again for your advice.
A flash'n'batt 2x6 wall meets the current IRC code-min for US climate zone 5, that's it. It protects the sheathing somewhat better than some other code-min stackups, but it is what it is, a code minimum way to build.
This isn't about good vs. great, merely code-min vs. somewhat-better than code at comparable or lower cost. Exterior foam isn't rocket science, and you can get a higher-R more resilient stackup for the same or even less money than flash'n'batt. Rather than spending MORE on the building envelope- it's spending SMARTER. (And significantly greener, when you compare the greenhouse gas power of the HFC blowing agents used for that flash-inch of closed cell foam to that of EPS or iso.)
R13 + 5 (2x4 with an inch of iso or XPS, or 1.5" of EPS) also meets code min for zone 5, but it's pretty easy to turn that into R13 + 10, or R13+ 15 and gain significant resiliance against moisture drives. I've yet to find a contractor who couldn't deal with R13 + 5 in some fashion, and it's not a huge step from there to R20 cavity fill + R8 foam 2x6 construction, not a very big step at all. Even production builders can get it down pretty fast, and a custom builder who balks at it is a custom builder I'd personally want to avoid. They might have a hard time figuring how to quote if fixed price, but if you explain it well enough just about any builder can get there.
Martin can link you to the relevant articles on this site detailing how to "get her done" on insulating sheathing, and violating the copyright by printing it out to explain to the builder what you want is probably going to be OK, eh? ;-)
Okay Dana, well-put. You all have me convinced; I'll give this a real attempt, and even offer to pay for the time to get up to speed on these techniques if that's an issue.
That said, I think I've reviewed all of the articles on this site and many on others regarding these techniques, and basically it seems there are quite a few options (where to put house wrap, how to do windows...). Is there a single technical document which lays out how to install exterior foam board? If I only have a host of articles, I think I'll create the wall drawings myself in CAD, but surely someone has already done this (someone who knows how to do this properly and won't have to glean it from articles)?
Again, I really appreciate all of the advice and thoughts.
Cameron,
Start with this article: How to Install Rigid Foam Sheathing.
Okay, several additional questions I can't find a clear answer to:
-If we use OSB sheathing and intend to put vinyl siding over 2" foamboard, can I just nail the siding in through the foamboard into the OSB? Do I need to worry about furring strips? The vinyl siding will NOT be foam-backed. It seems like the foam behind the hung vinyl will be enough for a rain screen, even without setting it up on furring strips? I see you usually recommend furring strips, but that seems to be in conjunction with foam sheathing, and I see another Fine Homebuilding article where the author says this is not necessary with OSB. (http://www.finehomebuilding.com/PDF/Protected/021181088.pdf)
-Do we need to move the sill plates back from the edge of the foundation to accommodation the additional thickness of the foamboard?
-Should we do 2 x 1" thick boards with staggered, taped seams or 1 x 2" board with taped seams?
Thanks for your indulgence with my persistent questions.
I’m glad Dana and Martin are much better to convey the message than I (I always got C’s in writing, A’s math and sciences, and F’s in patience…;-)) Having said that, this is not rocket science, You and your builder can go to must all manufacturers of building products and download good practice details for free; usually in PDF and CAD formats.
I disagree with “Good contractors SHOULD be hesitant to do work they are unfamiliar with”; to me Good contractors SHOULD keep up with their own education and best practices in their industry and SHOULD be embarrassed to offer less than that. There are plenty of videos, articles and details your builder and subcontractors can take a short time studying and give you a stellar job. If your builder is a member of a Home Builders Association, they too offer lots of classes and seminars to educate their members. I know, I teach Green Building and Building Science.
Cameron,
Check with the vinyl siding manufacturer to determine the maximum thickness of rigid foam that you are allowed to nail through. According to Paul Fisette, the maximum thickness of rigid foam that you can nail through is 1 inch.
If you want to use thicker exterior foam, I recommend that you install furring strips. Of course, that raises an entirely new controversy. While I don't think there is any reason to worry about vinyl siding installed on furring strips, some vinyl siding manufacturers are very conservative, and don't recommend the practice. More information here: Can Vinyl Siding be Applied Over Furring Strips?
If your contractors don't like to read, start by making them watch the movie first:
https://www.greenbuildingadvisor.com/video-how-install-rigid-foam-insulation-outside-house
Then they might be able to better follow the details in all of the links on Martins "How to" blog page.
In-re thin foam and 10,001 nails, the thermal bridging of all those nails adds up, since steel is >100x as conductive as foam. Better to use fewer penetrating fasteners- timber screws 24" o.c. holding the furring has but a fraction of the total cross section of all those long-nail penetrations of the foam. Using ring-shank nails to nail to 1x furring for better retention may be necessary in high wind areas.