Zone 6 go-to wall assembly

Wall assembly for zone 6 new construction should be an easy decision since thousands of them go up each year, and the topic is discussed as nauseam here and elsewhere. We all probably want walls that are durable, dry well and are very well insulated and keep heating and cooling costs low, especially when electricity is expensive. There are so many variations and differing opinions it can get confusing. Double studs eat up a meaningful amount of interior SF. CI with rigid foam or mineral wool presents details that builders new to that assembly will not like, especially when CI is thick enough to comprise +/- 35% of total wall r-value.
So, what is your go-to wall assembly for Zone 6? How challenging is this wall for an experienced builder doing it for the first time?
Gracias.
GBA Detail Library
A collection of one thousand construction details organized by climate and house part
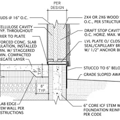
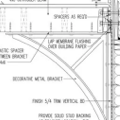
Replies
How does the extra wall thickness "eat up meaningful square footage?"
Unless you are on a very tight lot, the floor area used by a double stud wall doesn't matter to anyone except people obsessed with square footage numbers. It's the interior space that matters and that you pay for; who cares if the wall is 6", 12" or even 18" thick?
I live and work in CZ6 and my go-to assembly is double stud. It's easy to build; it can be insulated with cellulose, an environmentally friendly material; most people like the feeling of the deep window sills.
In certain situations I have used continuous exterior insulation. I dislike the added carbon emissions and the micro-plastic pollution created when cutting and installing rigid foam, and detailing around windows and doors can be challenging.
One further - do you have a "go to" thickness for your double stud walls?
I usually start at 11 1/2" for the insulation cavity; that seems to be the largest that can be easily dense-packed. On my last few projects we went with 8-9" for various reasons.
I’m starting with a floor plan that loses 6” from each exterior wall be 2x6 walls. However, my “duh” moment comes from realizing you likely design the floor plan with the 11.5” wall in mind to arrive at desired room dimensions. That does add to the footprint size, so there is a bit of extra cost there but maybe no more than the exterior foam.
Sound about right?
Thank you.
Yes, I have learned to always start designing with ± 12" walls, as there are some situations where it can be hard to make thin walls thicker. Square foot pricing is only a rough guide; thick walls do cost more to build than thin walls but they save you money and will eventually pay for themselves.