Insulating an Attached Garage Roof

Climate Zone 7. Attached unheated garage. New construction. Low slope roof.
Question – will condensation be a problem with my proposed roof stack?
Constraints
* All insulation needs to fit inside 12″ deep rafter bay
* 420 lb/sqf snow load (can’t make rafters shallower due to snow load, or deeper due to height variance)
* Height variance (no space for rigid insulation above rafters, will have thermal bridging)
* Lowest roof temp is -5F (cold, but no snow yet); most of the time, roof is under snow (32F roof temp) – not sure how this plays out with spray foam thickness and dew point.
* Budget (willing to sacrifice some performance, cannot afford steel roof deck which would allow rigid foam below sheathing for thermal bridging)
Proposed roof stack #1 – condensation problems? (from outside in):
* Comp shingle
* Water and Air barriers (roof assembly will dry to interior)
* Roof deck (plywood)
* 12″ rafters filled with mineral wool batts (R53)
* Drywall
Proposed roof stack #2 – difficult to do 8″ of foam? (from outside in):
* Comp shingle
* Water barrier
* Roof deck (plywood)
* 12″ rafters filled with 8″ closed cell spray foam (66% of R) + 3.5″ mineral wool batt (R15) – R55 total (derated spray foam to R5/inch for long-term aging and low temperature)
* Drywall
Both stack #1 and #2 will probably perform around R45-R47 due to thermal bridging (rafters are 16″ O.C.). Stack #2 probably okay for condensation.
I can insulate below the rafters, but not sure if that has any benefit.
I’m open to ideas for a better stack (it all needs to fit inside the 12″ rafter bay).
GBA Detail Library
A collection of one thousand construction details organized by climate and house part
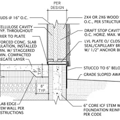
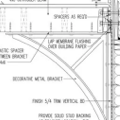
Replies
Mineral wool in a roof needs to be vented, so option 1 is out of the running. Not just for code compliance, but in CZ7 vapor drive will be pretty much entirely toward the exterior, so you are at high risk of moisture accumulating in the sheathing. The assembly will "dry to the interior" only when the cavity is already damp enough to cause problems.
Option 2 will work, it will just be expensive, involves high levels of up-front carbon emissions and there is always the risk that the foam won't cure properly. It's rare but it happens.
If you have the option to insulate below, my usual approach here in CZ6 is to use a gusseted rafter system for a vented roof using relatively low-carbon materials such as cellulose, but fiberglass or mineral wool will also work.
@michael - thank you for your guidance!
The roof is low sloping and cannot be raised due to height restrictions (we already have a 29" height variance, which was hard won).
I'd love to avoid the spray insulation. Is there any way to vent this? Would a slat ceiling (with generous gaps between slats) instead of drywall provide adequate venting?
Unfortunately, not really in your situation. Martin wrote this often-referenced article about it: https://www.greenbuildingadvisor.com/article/insulating-low-slope-residential-roofs. There are plenty of successful unvented roofs with fluffy insulation, but they are very risky. I avoid foam whenever possible but low-slope roofs are one of few locations where I use it. A slat ceiling would be worse than drywall; your indoor air is warmer and wetter than your outdoor air on most days in your climate zone, so the indoor air is always trying to get outside.
Thanks - I just read Martin's article. Haha - the slat ceiling is definitely not a vapor retarder!
Your comment "the indoor air [warm] is always trying to get outside [cold]" is a helpful way for me to think about where to put air/vapor barriers.
As I go down the rabbit hole of Lstiburek et al, it's clear that option 2 (spray foam) is coming out on top (including top cost).
@michael - a few more thoughts.
I really wanted to do a cold roof, but with 7-8 feet of snow on top of the ridge, a cold roof didn't seem like an option. I could vent out the side of the ridge with a simple ridge plenum to collect the air from each of the rafter bays. But, the vent at the ridge needs to be quite large (ridge vent sqf needs to equal (better to exceed) the eave vent sqf). A low-speed vent fan could reduce the ridge vent size, but that's another thing to check and service, not to mention power.
We are located in the WUI of the California Sierras. All vents need to be ember and fire proof. We see lots of cold roofs in the Rockies, but they are fairly rare out here. A vented roof seems daunting between the deep snow and the severe fire risk.
The garage probably rests at 37F and 50% RH during the winter, assuming some residual heat from the attached house, plus insulation and reasonable air sealing (when the garage door is closed). This can still lead to moisture problems.
I read this article "Venting a low-slope roof" https://www.greenbuildingadvisor.com/article/185062
It seems like Option 2 is not optional.
But this brings me to a different but related issue:
The garage floor is, in effect, a high-mass 37F "roof" for the living area below. So I have the same insulation problem there, too, although better RH and temp control.
I'd really like to avoid spray foam in the living area. But I'd like to avoid mold in the living area even more.
Any thoughts on how to insulate below the garage floor using greener methods and materials?
What's the reasoning behind insulating an unheated space to such a high degree?
Great question. My reasoning... Condensation control? Mathematical laziness? Herd mentality?
Your obvious question is worth the effort. Here goes...
The uninsulated roof will mostly be at 32F (snow), and the garage ambient will be about 37F (assuming residual heat from the attached living area, solar gain, reasonable envelope sealing, some baseline insulation).
Rain is 100% RH
Snow forms at about 70% RH
Dry weather is about 50% RH
Looking at dew points for 37F garage temp (no heater, residual heat from house only):
At 100% RH (raining), dew point is 37F; 32F (roof) < 37F (dew), condensation at roof
At 70% RH (snowing), dew point is 28F; 32F (roof) > 28F (dew), no condensation at roof
At 50% RH (dry), dew point is 20F; 32F (roof) > 20F (dew), no condensation at roof
Looking at some dew points for 50% RH (dry weather):
At 50F ambient, dew point is 32F; 32F (roof) = 32F (dew), condensation initiates
At 60F ambient, dew point is 41F; 32F (roof) < 41F (dew), condensation at roof
At 68F ambient, dew point is 49F; 32F (roof) < 49F (dew), condensation at roof
At 72F ambient, dew point is 53F; 32F (roof) < 53F (dew), condensation at roof
Conclusions when snow on the roof:
Dry weather = keep the garage below 50F for no condensation
Snowing = keep the garage above 28F using residual heat from home, solar gain and insulation
Rain = condensation inevitable if snow on roof (no skiing either)
Garage needs to be above 28F and below 50F (fairly wide range). This seems reasonable, and also why people with basement living areas have issues if they heat them above 50F without adequate insulation. Adequate insulation should keep the condensation surface itself at 50F or higher (for 68F room temp and above).
Now I just need to know how much insulation is needed to keep the garage between 28F and 50F with worst case of -5F outdoors (10-15F more typical).
This is a super interesting result (IF it's correct), because it shows that people are probably over-insulating their attached garages if they just use energy guidelines for their climate zone. Equally interesting is that flash-and-batt can be cost effective if moisture control is your only objective (not comfort).
A ceiling mounted radiant space heater is all you need when you want comfort in the garage. If you want to work for extended periods of time, then more insulation might make sense. But even so, you want to keep your ambient temp below 50F and just wear warmer clothes.
I used this online dew point calculator:
http://www.dpcalc.org/
Thank you for your question!
Zetetic,
Insulating garages for condensation control is a new concept to me, so I'm not sure I fully comprehend all the implications, but I do question some of your assumptions.
For example, I would not use outdoor RH as a proxy for interior RH unless there is tons of air exchange. (BTW, it's not always 100rh at ground level when raining but that's a pedantic point. Rain cN actually reduce humidity by causing condensation of lower level air on its way down)
Heating air does increase its moisture 'holding' capacity but that does not necessarily increase the RH or adversely affect the dewpoint calc. There needs to be a source of moisture for the air to pick up, and it takes time depending on how available that source is.
Countless garages have been built with zero insulation and no condensation issue in my climate of Maine but I'm not familiar with your climate beyond having done some hiking in the Sierras (beautiful!).
Insulation will only help dew point isue if it is something like closed cell spray foam moving the *first condensing layer of interest* to a warmer temp.
Any air and vapor permeable insulation is actually *increasing* condensation risk by lowering the temperature of that first condensing surface behind it. I wonder if you could just apply a relatively thin layer of CC foam and call it a day?
All that said, insulation may simply make the garage more comfortable, and if you are ever going to work in there certainly there is benefit. Also, perhaps I have somehow misunderstood your logic for the dewpoint control and if so my apologies!
*edit: I just saw your other post with more context-- https://www.greenbuildingadvisor.com/question/zone-7-insulating-a-garage-over-living-area
I'm not sure I understand your calculations. Heating a space doesn't change the dew point of the air inside it. Absent a source of moisture, the dew point of the air inside a building will be the same as the dew point of the outside air.
In an occupied building you assume that each occupant introduces about 3 ounces per hour of humidity. That's why the interior dew point is going to be higher than outside.
That said, garages tend to be humid because cars are often wet or snow-covered when they come in, and that moisture has to go somewhere.
@tyler and @DC - thank you! I don't know what I don't know, which is why I'm here to meet experts like you..
@tyler - It never even occured to me that rain can reduce humidity - not pedantic at all. Rain precipitating more precipitant - wow. Also, good point on the need for a moisture source.
I'm thoroughly convinced by you and others, and all the research and real world evidence that anything but CC foam (or other impermeable insulation) can be a problem against a condensing surface.
I like your idea of a thin layer of CC foam (tighter envelope, warmer condensation surface). Might be just good enough without breaking the bank. Even in freezing weather, I'd rather be wearing a dry T-shirt than no shirt or a wet shirt - maybe not the best analogy.
@DC - Thank you for mentioning some important sources of humidity. Nice to know that I'm losing 3oz of water (via respiration) every hour if I don't drink. Good point that wet cars are a moisture source even when the garage door is closed - forgot about that significant source of humidity.
-----------------------------------------
I've been around plenty of garages that seem fine without insulation. So why? Why do some garages fare better than others?
My dew point exercise was a crude first order estimate of "what temperatures might condensation occur" (worst case would be garage door open), and then try to use that to inform "how much do I insulate or not" (and under what conditions). I realize that designing for worst case can result in overbuilding or even introducing a new set of problems.
In the process I learned (with my assumptions) that condensation is more likely above 50F (dry, Spring weather, snow melting) if I have an ice cold ceiling from the winter snow remaining on the roof. I also learned that if I can keep my garage above 28F while it's snowing (or with a wet car in the garage) I probably won't see condensation.
I know the analysis is crude, but it puts some coarse bumpers on my condensation conditions - keep the garage above 28F and below 50F while there's snow on the roof AND no insulation. So maybe I don't NEED insulation if I can keep my garage between 28F and 50F during the winter, but I might want some insulation to make the space more comfortable, but not so comfortable that the garage ambient jumps above 50F during the spring. Again, lots of assumptions, but it's better than throwing darts with a blindfold.
Just to be clear, the 3oz per hour is from "occupant behavior." That includes respiration, but also cooking and bathing.
I won't comment on the insulation as that's been pretty much covered here. I chose to go with spray foam directly against the roof sheathing for my shop to go along with a ridge beam retrofit/vault to make room for a lift. Rafters were 2x4. I removed about 16 ft of collar ties and replaced with a ridge beam/restructure in place. See attached.
Your garage is attached so insulating it make sense for a few reasons. One is to reduce heat loss from your home, but the other is to moderate temps. You'll have an EV in the near future (if not already), and you will benefit in a real way from keeping it as close to 68 F as possible to save costs on preconditioning, whether heat or cold.
Even in a detached, unheated garage, moisture from snow melt is a challenge and will create a high humidity environment regardless so a bit more heat (by insulating the envelope) is a good thing. Snow melt will be your biggest moisture issue. I have a drain pad (pic 2) made from EPDM roofing and racedeck flooring which is needed to contain snow melt from our EV. It drains to a vacuum system, but the windows frost up all the time with the heat off, regardless.
Last night our low was -12 F, but the shop did not drop below 24 F. No heat added, and completely detached. Zone 7A. Attached and insulated, your garage would likely do better. I have a single 8' steel roll up door which is "insulated" but R3 at best.
That's some great practical feedback for CZ7. Gives me much hope. Questions, questions!
How much foam did you spray against the roof?
What's the rough R-value for your walls?
Is the ground/earth your only heat source? Do you live any lights on, for example?
No EV yet, but it does seem inevitable at some point. We're wiring the garage for a proper high-amp charger. It seems all of our friends have EVs, and their batteries drain so fast when they visit us - they're heading down the mountain at 4am to get time on a fast charger before their batteries die. 68F duly noted.
I'm still sticking with my 3-pedal ICE cars, which are more old school fun than practical at times. What I'd give for a proper car lift, though. Nice shop, BTW!
I did a "wow" on the windows frosting up. Makes sense, though, if the glass is acting like a thin membrane and cooling off rapidly.
I'm looking forward to the addition and remodel after 30 years of living with single pane windows from 1966, and a vintage R4 roof, R9 walls, and towering cathedral ceilings. If we lose power or propane, the house gets down to the 30s pretty quickly, even with the fireplace fully stoked.
Shop was built in the 70s I suspect. 2x4 walls with fiberglass. Roof foam is an about 3” closed cell with 5/8 type X over. No heat source over the period I quoted. You’re not seeing anything magical there..it’s just moderating day and night lows. Charging the EV for a few hours would theoretically create some heat, but given the 400kg pack, and the relatively leaky shop, likely not enough to detect.
If you still want a 'decent bit' of insulation, flash and batt would save use of spray foam vs just all spray foam. I guess I just wondered if it needed to be to such high levels. Buy obviously if doing flash and batt, you need to consider your ratios, which it looks like you're aware of.
The only other point I'd make about your dewpoint assumptions is that the way you've gathered dewpoints for 'ambient dry' conditions doesn't make a lot of sense to me. It's strange to claim you need to keep the garage below a certain temperature (50f you say) to avoid condensation. Especially if that temperature is reached via heating which reduces RH and does not increase dewpoint. I would phrase it rather as needing to keep the dewpoint of the interior air below a certain value. There's no reason i can see to correlate a 50f interior temp with a specific dewpoint.
True, in the end it's all about dew point (which is a function of temp and RH).
If I talk about designing to a dew point with anyone other than an energy consultant or the kind experts here on GBA like you, I think I might get either an eye roll, or they'll tell me that they don't want to look at psychometric charts (I hated looking at them when I was in school, too, so maybe I'm biased - hah).
But you're right, the GBA audience probably finds it easier to talk about dew point than T or RH.
Assumptions are helpful to simplify complex problems. The assumption that there is a condensation surface at 32F is not entirely unreasonable if there's no insulation in the roof and there's a ton of snow and some ice on it. It's certainly a worst case, and even a likely one.
Temperature and RH are indeed variables that are hard to nail down without gathering some data to find the max/min values. I can find cheap Temp/RH meters, but dew point meters/sensors are harder to find. So I'm working with variables that are easier to measure with off-the-shelf tools, and easier to talk about with people without whipping out the psychometric chart.
Spring temperatures of 50f with snow on the roof are also a real possibility. Moisture sources in the garage (e.g. car) during mud season are also possible. Although corner cases, they're also not 100-year events.
In terms of insulation, it seems I can also flash with no batt. The flash is to raise the temperature of the exposed condensing surface (roof). A thin layer of CC foam might have the most impact (both as air barrier and to raise the condensing surface temp). As soon as you add batt, you need to consider ratios so that condensation doesn't get absorbed by the batt. Removing the batt from the equation gets rid of the absorption / mold problem - well, at least in the ceiling where mold is frequently a problem if not insulated correctly.
But as was mentioned earlier, the world of EVs might be upon us in the next decade and a warmer garage might be important. So flash and batt might be the answer after all.
If your roof is at 32F with snow on it you're going to have a bigger problem, ice dams. In snow country roofs are best ventilated for that reason.
Haha, just last week...
Icicles are 12 feet long. R4 roof pretty much says it all.
Well, you just made your argument for insulating that garage! It should also give you an idea of thermal contributions your attached wall (s) is making to the space. Parking a few warm ICE cars in there adds a fair bit of heat as well.
I'm going to say that when it comes to managing humidity, warmer is always better on the interior. It creates more of a vapor drive to dry to the exterior. Even if this building can't dry through the roof it still can dry through the walls and through air infiltration. Also, wood is the opposite of air, it absorbs less moisture as the temperature increases. At a given dew point, the amount of moisture absorbed by wood declines as the temperature increases. Conversely, you can have a dew point that is fine at a warmer temperature that creates a mold risk at a lower temperature, even if there is no condensation.
I've looked at passivhaus design, and it's almost so extreme that the building cannot dry out passively (irony) without either human intervention (open/close windows) or sensors and fans. I'd like to strive towards a bit more balance, for sure.
Very interesting and counter-intuitive that wood absorbs less as temperature increases. Without any science, I would think wood is drier and has more water absorption capacity at higher temperatures - especially when there is more water to absorb in the air. Is this a cellular thing? Do all woods behave this way? I'd love to learn more about this out of curiosity.
Also interesting that mold risk exists without condensation. I guess somehow the mold can feed on water vapor? Perhaps a minimum RH for certain molds?
If one frames the phase transitions of water in terms of energy states, it makes perfect sense that solids (including wood) 'give up' water when heated and air will 'collect' water when heated.
When water goes from a solid to a liquid to a gas, the energy state is increasing (endothermic-- heat is added to the system). So if heat is added to ice, it melts and becomes liquid. If heat is added to liquid water, it evaporates and becomes vapor.
Likewise, if heat is added to wood, it will encourage evaporation of any liquid water, making the wood drier. If heat is added to air, more water molecules from the surrounding environment will (by gaining a higher energy state) enter the gas phase, effectively 'filling' the air with vapor. The energy that is 'added' to bring the water molecules to the next higher state is known as the latent heat (of fusion between solid and liquid, and of vaporization between liquid and vapor).
The other neat thing about wood is that it's hygroscopic, which means it will adsorb water from the air even if dewpoint temp has not been reached. It does this mostly in accordance with relative humidity (and varying a bit with temperature). See 'sorption curve.'
Here's a chart of wood equilibrium moisture content vs air temperature and humidity:
https://www.woodworkerssource.com/wood-moisture-content.html
For example, with air at 50F and 98% RH the equilibrium moisture content is 26.9%. That air has a moisture content of 52.5 grains per pound and a dewpoint of 49F. If you were to warm that air to 70F, it would still have a moisture content of 52.5 grains per pound, but its relative humidity would be 47%. Interpolating on the chart between 45% and 50% at 70F gives an equilibrium moisture content for the wood of 8.8%. At 50F, with the same air, the wood is going to absorb three times as much moisture as at 70F.
At moisture content above 20% wood is susceptible to rot -- although 50F is right at the bottom of the temperature range where mold will grow.
Note also that wood that is saturated has 28% moisture content, wood with 26.9% moisture content as in this example is very close to saturated.
"I can find cheap Temp/RH meters, but dew point meters/sensors are harder to find. So I'm working with variables that are easier to measure with off-the-shelf tools, and easier to talk about with people without whipping out the psychometric chart."
True. And if you know temp and RH, you know dewpoint! I guess my point was less that dew point is the sole metric of import and more that temperature and RH are not statically related— i.e. if temperature goes up, RH goes down. Dewpoint would remain constant however, until more vapor is evaporated.
Not that it really matters if you're spray foaming anyways, but what I'm trying to get at is that saying "Dry weather = keep the garage below 50F for no condensation" is focusing on the wrong metric in the wrong place. First, it assumes that the interior is identical to the outdoors. Secondly, let's say it's 72F out, the idea would be to cool the building to get to 50F? Clearly that doesn't make sense. And if it's 45F out with an RH of 50% and you heated the garage air to 50F, you are reducing RH while dewpoint is remaining the same, so you are actually-- as DC points out-- making the assembly safer. So my point is that the focus should be on the interior metrics (RH, Temp, dewpoint), which are related to outdoor metrics but not directly mirrored.
I'm also curious if the idea that an unvented roof is always 32F with snow on it is borne out in reality. I suppose it makes sense it would be kept somewhat close to that (or colder when it's colder out). And I suppose that's why the vented roof is ideal- as you know :)!
One other point about condensation safety: I think it's possible that many uninsulated garages in similar situations to yours would experience some seasonal wetting, but the period of time it experiences that may be short enough that it's a non issue. That is taken into account in the codes in terms of exterior-to-interior insulation ratios, i.e. some wetting is considered OK as long as there is more drying that wetting.
Tyler, I can tell you that the temp at the ground surface with snow cover in zone 7A will be pretty much 32F , but this is assuming geothermal heat. Lots of research on this…and I have a sensor in my backyard to confirm. From +39F to -25 F, that sensor has been at 32F +- .8 F.
In my (98%) unheated garage, there is no way that the roof deck will be 32F as the roof deck has no geothermal heat source, and the building interior is often below zero. There has been zero evidence of even an icicle on that building in cold temps.
For a non-vented roof with spray foam where the building is heated (and roof deck non-vented)..for sure the roof deck will be 32 F and maybe warmer at the roof surface if covered with snow. It follows that venting the roof deck itself in a non vented assembly make sense for cold climates to avoid ice dams.
For this zone, a vented attic where you can add r80 cellulose over 2” closed cell makes for a far less expensive and safer assembly.
Zete, you have 12" to play with so the "safe" roof assembly for your garage (assuming you will add some heat to it) is to leave a 2" vent space at the deck (you will need a ridge and soffit vents), and fill the rest with insulation. Do your vapour barrier, then 5/8" type X. Or go with 2" EPS before drywall for an effective thermal break. This would be a safe assembly that can dry outwards, include a thermal break, and reduce/eliminate icing issues on the roofing.
Although I used cc spray foam for a non vented assembly, I only did this due to the space challenges of 2x4 rafters. Somewhere down the line if there is leak, it will likely persist for some time unnoticed as the roof deck is sealed up with cc foam. With a vented space, at least the sheathing could dry to the vented space, and a leak be detectable via a visible leak inside. I suspect we'll see issues surrounding this issue down the line with non-vented assemblies.
Dennis, thank you for the suggested "safe" vented assembly. This is the dream assembly for sure.
Is there such a thing as a cold roof without a ridge vent? Is there such a thing as a ridge vent that works under deep snow (8 feet)?
I had a few ideas on alternative passive venting for the ridge:
* Vent downward at the ridge where it extends over the eave
* Vent to the side at the end of the ridge
* Use very small eave vents (1/4"?) to reduce the demand for ridge venting
The challenge of these strategies is vent size and air flow. For a passive vent, I'm assuming that the square footage at the ridge vent needs to be the same as or more than the square footage at the lower eaves.
If the ridge square footage is significantly less than the eave square footage, could there be enough pressure to drive air movement in the cold roof between exterior breezes and temperature differentials?
Is there a minimum eave vent size?
We're located in the WUI, so all vents need to be protected against embers and flames, and the cold roof itself would need to be fire-rated. The WUI protections are relatively straight-forward, just costly with all the fire-rated materials (because embers can still get by the best ember-resistant vent) and additional detailing.
I'd like to avoid active venting, such as fans to drive air flow in the cold roof. It's another thing to maintain and service. We're on a steep hillside, making ridge access a bit precarious.
This almost seems worthy of a new post.
In order for the roof to vent due to convection there needs to be a height difference between the vents. Whichever vent has the smaller area will limit the effective amount of venting. Sometimes vents are put on the gable, it's not as effective as a ridge vent but is a way if ridge vents aren't feasible.
Vent fans aren't generally a good idea. They tend to suck air out of the interior of the house. The primary purpose of ventilation is get rid of moisture which accumulates under the roof when the outside temperature is lower than the inside temperature. That moisture comes from moist interior air which leaks through the ceiling. Mechanical venting increases the amount of interior air leaking through; it not only doesn't solve the problem, it makes it worse. It also raises your heating bill.
There was a Joe Lstiburek video posted a couple of days ago where he talks about the tradeoffs with roofs -- vented roofs are more likely to catch fire or be blown off by high winds, unvented roofs are subject to ice dams and rot. If I recall correctly, his recommendation in snow/fire areas was to build an unvented roof, then build an over-roof to provide ventilation.
I really like vented over-roofs - I'd build one if I could. Still trying to find a path if I can, but venting through 8 feet of snow via the gable or perhaps adjacent to the chimney is a real challenge. There's a large ridge skylight just to complicate things further.
Is there any sense to build an over-roof that is only vented at the soffits (no ridge vent)? Or is partial venting (soffit vents only) a wasted effort (relatively stagnant air?), or perhaps even worse than no vents at all?
The unvented cathedral roof below an over-roof would follow Lstiburek's recommendations (partial venting not withstanding).
The roof stack from top to bottom:
Over-roof (1/4" full-length fire-rated soffit vents, no vent at ridge)
-- comp shingle
-- WRB
-- 5/8" sheathing (fire rated?)
-- 1.5" vent gap (2x4 stringers)
Unvented Cathedral
-- 5/8" sheathing (fire rated?)
-- 8" RayCore polyiso SIP (R52 minus R6.5 due to thermal bridging = R46 net)
-- Grace Ice and Water air and water barrier
-- 4x6 double T&G ceiling deck exposed below (R4)
-- living space (no attic)
If I can't do a vented over-roof, would an unvented over-roof (just a 1.5" air gap between the RayCore SIP and the roof deck) be a problem?
The reason for an unvented over-roof, if a vented over-roof is not feasible, is aesthetic. It would increase the existing roof stack thickness so that the roof over the addition and the roof over the existing structure can be integrated seamlessly (matching thickness).
For structural reasons we cannot build the addition roof the same as the existing roof - this would otherwise vastly simplify things if we could.
Any thoughts greatly appreciated.