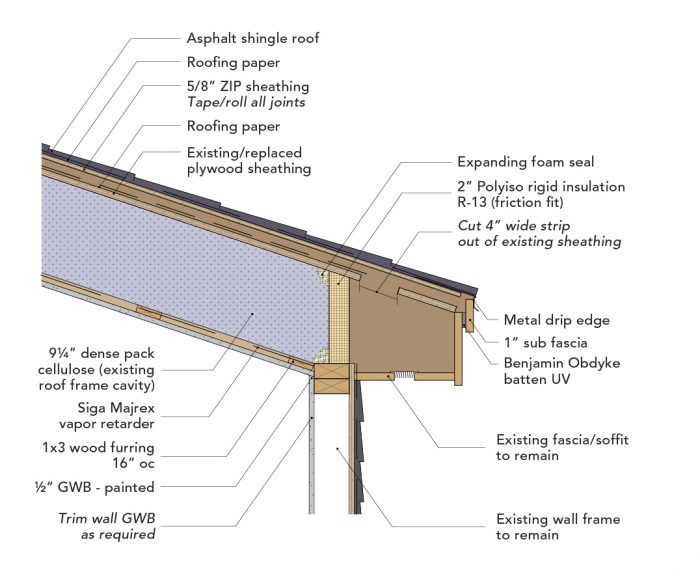
On a recent renovation project, Steven Baczek Architect was faced with a mid-1970s low-sloped improperly vented roof. The long side of the roof measured 30 ft. in length, and the framing was 2x10s 24 in. oc. with multiple intermediate bearing points. The roof was vented with typical vent chutes held tight to the underside of the roof sheathing, and the rafter cavity was packed with batt insulation. At numerous locations the cavities were interrupted by blocking and skylights, which left many of the cavities unable to vent.
Batt insulation is air permeable—a condition exaggerated at the end of the rafter cavities, where they meet the soffit overhang. As a result, on this house wind washing at the soffit led to annual ice damming on the roof and associated water leakage. After the demo was complete, we discovered large areas covered in mold, especially at the cavities where venting was restricted. Despite all good intentions, this roof assembly failed at water, vapor, and thermal control.
The project scope consisted of removing all the interior drywall, batt insulation, and vent chutes. The existing roof rafters and sheathing remained. On the exterior, the roof shingles and building paper were removed. A new strategy to prevent wind washing, control vapor, and manage thermal conditions was put in place. In areas of low mold risk, the mold was simply scrubbed and the plywood sheathing was left to dry. In the areas with a lot of mold, the plywood was replaced.
Fixing an improperly vented roof
The most important aspect of this retrofit was developing an effective ventilation strategy. The new detail at the soffit uses the existing fascia/soffit vent assembly. A 4-in.-wide gap running the full length of the soffit was cut into the existing sheathing. This provides an air path through the soffit…
Weekly Newsletter
Get building science and energy efficiency advice, plus special offers, in your inbox.
This article is only available to GBA Prime Members
Sign up for a free trial and get instant access to this article as well as GBA’s complete library of premium articles and construction details.
Start Free TrialAlready a member? Log in
12 Comments
What was the pitch of the low-sloped roof and to what extent did the low slope cause issues in addition to the others that were noted?
The existing roof slope was a 3:12 and it wasn't so much the roof slope that caused problems but rather numerous places where intermittent blocking was introduced for framing and or skylights.
If I understand correctly, this is a conditioned ceiling with a vent space between the original roof deck and a new deck with new roofing. What drove the decision to go unvented w/fluffy insulation vs. a demonstrably safer conventional assembly with interior or exterior foam, neither of which preclude a vent space below another roof deck? Cost? Objections to foam?
Brian,
Although as Paul said the sleepers aren't called out on the section, I think it is constructed as you describe wth a vent channel above the original sheathing. Roof assemblies with vent channels either above or below the the sheathing are considered to be vented. The primary difference between them is that when the air gap is above, any moisture has to first move by diffusion through the sheathing before being vented, but that's not unlike a roof with venting below the sheathing that uses plywood baffles.
Thank you, Malcolm. The baffle analogy makes perfect sense.
a minor objection to foam was part of the decision process but the roof was a 3:12 with multiple rafter lengths making up the 30+ foot long roof slope. as well as by venting above we were able to add another r-10 of insulation to the roof frame and most importantly we were able to seal the insulation cavity to any air penetration.
I think the top drawing is forgetting to mention the sleepers to keep the zip sheathing above the old roof (so the new 4" cut in the old sheathing can vent to upper)?
Paul, you are correct the note calling out the 2x4 sleepers that were aligned with the rafters below was not in the detail.
A good retrofit which I'm sure solved the problems. I'm a bit confused by the comments on wind washing though. I don't understand how wind-washing of the batt insulation with cold exterior air would cause either mold or ice-dams. It wouldn't even significantly reduce the R-value of the batts at the eaves. Both problems were more likely caused by combination of air leaks from the interior, and the lack of ventilation. I think retrofitting the foam blocking is a good idea to contain the cellulose, but not for the reas0ns the article suggests.
https://www.rdh.com/wp-content/uploads/2018/06/Wind-Washing-Summary-Report-RDH-Tech-Library.pdf
the wind washing issue introduces air movement into the system. air movement can generate an order of magnitude of moisture when compared to simple diffusion. A lot of the mold that we saw in the failing roof was primarily due to air moving moisture and then the air being stopped at certain locations. this creates micro climates in some of the rafter cavities which displayed an order of magnitude of mold growth compared to some of the other rafter cavities so we viewed it as stopping the air and creating a sealed six sided box of cavity insulation with venting above provided the best long term approach.
Thanks Alexandra, although I confess I'm still no closer to understanding that part of your explanation.. What distinguishes the air that is purposely introduced into a typical roof cavity through the above insulation vent space (which is seen as desirable) from the you are calling wind washing? That air can "generate an order of magnitude of moisture when compared to simple diffusion" is usually accepted as referring to interior air leaking into building assemblies, and I'm still struggling to understand how it applies to exterior air movement.
The blocked cavities accumulated moisture that came primarily from interior air-leaks and perhaps some minor night-sky radiance, because there was no path for it to be removed, not because there was air introduced from the eaves.
I've always understood wind-washing to be the degradation of thermal resistance in permeable insulation, but as the research I linked to shows, even batt insulation only suffers a 5% to 8% loss - so I don't see how this degradation of R-value would aid the accumulation of moisture in the cavities.
I'm not at all sceptical about what you did to solve the problem, just the mechanisms you are ascribing to what caused it..
I am still a bit confused about the venting. The article states that the existing venting was interrupted by skylights. How is that corrected by laying 2 x 4 on top of the old sheathing and then laying on a layer of Zip sheathing? The skylights still has to penetrate through the new sheathing and the old sheathing to get the light to the interior. Perhaps you are picture framing the skylight openings with 2 x4 material, and then leaving a gap between the picture frame and the 2 x 4 applied over the rafters?? If so, that will allow for a continuous air flow, but the article does not say that is what you designed.
Log in or become a member to post a comment.
Sign up Log in