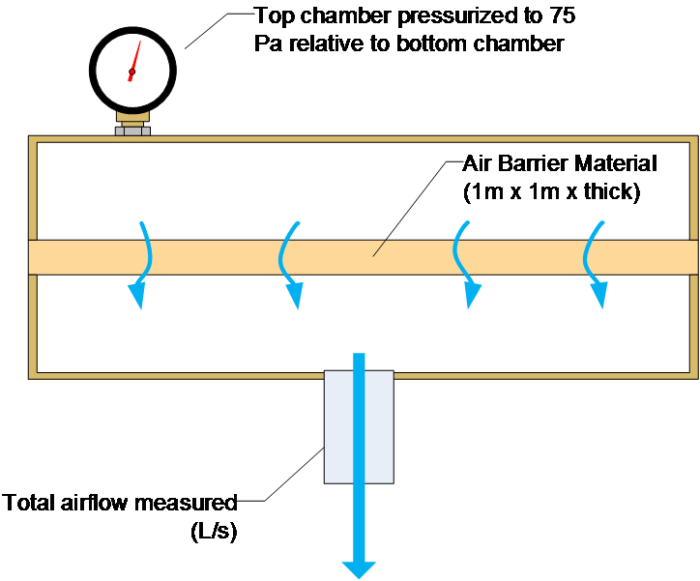
Image Credit: Rick Duncan, Spray Polyurethane Foam Alliance
Many builders use spray polyurethane foam as an air barrier, raising the question: How thick does the spray foam layer have to be to stop air flow? There’s a follow-up question, of course: Is the answer different for open-cell spray foam than for closed-cell spray foam?
As with most building science questions, there is a short answer and a long answer. The short answer is that closed-cell spray foam needs to be at least 1 or 1.5 inch thick to act as an air barrier, while open-cell spray foam needs to be between 3.0 and 5.5 inches thick to act as an air barrier.
We’ll get to the longer answer after some presenting some definitions and data.
What’s the definition of an air barrier?
Most building codes define an air barrier material as a material that has an air leakage rate below 0.02 liters/sec-m² @75 Pa (0.004 cfm/sf @ 1.57 psf) when the material is tested according to either ASTM E2178 or ASTM E283.
This definition was adopted by the 2009 International Residential Code as the basis for the code definition of an “air-impermeable insulation.”
Joseph Lstiburek, a principal at Building Science Corporation in Westford, Massachusetts, told me that he helped develop this definition. “The .02 number was based on a suggestion from Gus Handegord,” Lstiburek told me. “He suggested that an air-barrier material should be defined relative to drywall. We tested drywall and the air leakage rate for drywall was a bit under .02. So that was the basis of the standard.” (For more information on the development of this definition, see Is OSB Airtight?)
Differences between open-cell spray foam and closed-cell spray foam
The main difference between open-cell spray foam and closed-cell spray foam is foam density. Open-cell spray foam usually has a density of 0.5 or 0.6 pounds per cubic foot, while closed-cell spray…
Weekly Newsletter
Get building science and energy efficiency advice, plus special offers, in your inbox.
This article is only available to GBA Prime Members
Sign up for a free trial and get instant access to this article as well as GBA’s complete library of premium articles and construction details.
Start Free TrialAlready a member? Log in
6 Comments
The flexibilibity matters
In the Thermal Metric Project testing done by the Building Science folks, the leakage of the wall sealed with closed cell foam varied by a factor about two over the tested temperature range of 0F to 108F, whereas the leakage of assembly sealed with open cell was essentially the same at both ends of the range. The closed cell wall was tighter than open cell at one of the temperature extremes, but dramatically leakier at the other.
There can be alternative possible explanations of that, but it's likely that the rigidity of the closed cell foam and the differences in the coefficients of expansion of the foam and the structure wood may have been expanding and contracting the leakage at those "obvious" leakage points such as the bottom plate or between doubled top plates, whereas the flexibility of the open cell gave it enough mechanical compliance that the size of those leaks didn't change much with temperature. It would be possible to test that hypothesis, but it's not clear that it matters.
Bottom line is that for air-sealing an assembly it's both cheaper and greener, and at least as effective to use open cell foam rather than closed cell foam. An inch of the typical 2lb closed cell foam has as much polymer as 3-4" of 0.5-0.7lb open cell, and most closed cell foam installed in north America uses HFC blowing agents with a far heavier environmental impact than the blowing agent for open cell foam (water.)
Use of closed cell is only necessary in stackups where it's lower water vapor permeance is an important part of the moisture management aspect of the design (which can usually be designed out.)
Response to Dana Dorsett
Dana,
I agree with your most important point: that open-cell spray foam is less environmentally damaging than closed-cell spray foam, and should be chosen by green builders who need to use spray foam (at least for those applications where open-cell spray foam is appropriate).
Because open-cell spray foam is associated with damp roof sheathing when the foam is sprayed against the underside of roof sheathing, I think that builders should be cautious before using open-cell spray foam in this location. If anyone wants to build an unvented insulated roof assembly, it's always better to install rigid foam above the roof sheathing than any type of spray foam on the underside of the roof sheathing.
To return to the questions raised by the Thermal Metric Project results, I spent quite a bit of time talking with Straube and Schumacher on this issue, proposing different ways that open-cell spray foam might be considered less leaky than closed-cell spray foam at cold temperatures. Straube and Schumacher strongly resisted the implications that meaningful differences in leakage were occurring. As Straube noted, "it's a bee's fart."
The discussion was complicated by Schumacher's insistence that the first round of testing -- the testing that was used to create the graph reproduced here -- had results that displeased the manufacturer of the open-cell spray foam. That manufacturer insisted that the open-cell spray foam wasn't installed properly, and Schumacher eventually agreed that there may have been problems with the wall assembly. (Problems like that never happen on a job site, right? But that's another issue entirely...)
As a result of that discussion, the open-cell spray foam wall was disassembled and/or removed, and a new assembly was created for a second round of testing of the open-cell spray foam wall. Schumacher no longer stands behind the results of the first round of open-cell spray foam testing. Curiously, though, Schumacher had no explanation for why a wall with poorly installed open-cell spray foam might have performed better, not worse, than a wall with closed-cell spray foam.
Responding to future comments
I'll be on vacation from Sept. 26 to Oct. 6, so I won't be able to answer any questions or comments posted here (or for that matter, on any other GBA page) until I'm back in my office on Oct. 7.
That said, I hope the dialogue continues, and that there is a healthy collection of comments for me to read when I return.
I agree the differences are small...
The differences in air tightness of the ocSPF and ccSPF assemblies were small, and the difference between the ccSPF wall and the cellulose wall was even smaller (and that's with damp spraying, not dense packing!) From a practical point of view it's irrelevant, but from an academic inquiry point of view the anomalies are of interest.
The curious factor that the ccSPF leakage changed with temperature, whereas the ocSPF leakage did not isn't a reason to choose one over the other. At these leakage levels with the different temperature dependencies of leakage with different cavity insulation are purely academic- the major leakage in the assemblies was not through the insulation, but through other parts of the framing, which masks the actual leakage through the foam itself. But understanding the root of that phenomenon better may still provide insight.
Clearly vapor retardency is a deciding factor in some assemblies, as noted. Air tightness alone is not a guarantee that there will be no moisture problems- it's necessary, but not sufficient.
Since spray foam is always applied against some other material, it's really the combined air-tightness of the substrate + foam that's relevant. Cheap half-inch OSB may not meet the definition of an air barrier per the ASTM E2178 test, and an inch of open cell may not either. But an inch of open cell sprayed onto OSB almost certainly would. And the air leakage of a wall air-sealed with a flash-inch of open cell on an OSB wall would, as in the Thermal Metric Project assemblies would be primarily at the framing joints outside of the insulation cavity. It's actually kind of silly to be testing slabs of spray foam without the relevant substrate, since it's the air tightness of the assembly that matters the most, not the absolute air retardency within some arbitrary layer.
Sealing seams vs. sealing seives
[Edit: this is a long-winded way of saying some of the same things that Dana says in the post just above, which I didn't see before I posted]
In the test, a free-standing sheet of foam is tested to see whether it woks as an air barrier. That would be the relevant test if you were spraying the foam onto an air-permeable material to make an air barrier. Notice I said air-permeable, not just vapor permeable. For example, if you had a wall that was braced with diagonals and did not need structural sheathing, and you stapled window screen material up instead of sheathing and sprayed the foam on that. Nobody would do that, but the air barrier test is proving that 1.5" of ccSPF, or 3.5" would work all by itself as an air barrier.
In real life there is some kind of sheathing that stops airflow over most of the surface area, and the foam only needs to stop the air flowing through the cracks. Because the crack area is very small, we can tolerate much higher leakage per unit area through the foam, compared to the spec for using it as an air barrier over the whole surface area.
To get an idea of how that works, consider 1280 sq. foot 2-story house, 32' x 20' footprint, 16' high walls. The volume is 10,240 cubic feet; the surface area of the envelope is 2304 sq feet, or 72 4x8 sheets--sheathing or ceiling wallboard.
At 75 Pa, with a barrier material that just met the spec over the whole area (0.004 CFM/ft2), it would leak 9 CFM, or 0.05 ACH_75. That's pretty negligible for sure, but you'd care if it got much worse than that. For example, maybe 1.5" of open-cell sprayed on window screen would give 3-4 times that much, or 0.15 to 0.2 ACH_75. That probably OK, if it is the total for the wall, including the cracks that have been sealed now and all the surface area. But in a real application it should work better:
If we only need to seal the seams, we have much less area to worry about. Below I estimate that the effective area to be sealed might generously be 300 sq. ft. In that case, the leakage with 1.5" of ocSPF seems like it would be less than 4 CFM, for less than 0.025 ACH_75. I think that's plenty good enough.
My conclusion is that the thickness needed for an air barrier has little to do with the thickness needed to provide air sealing, and that 1.5" of ocSPF is fine from that perspective.
How I got 300 sq. feet: There are 1728 linear feet of edges of the 4x8 sheets needed for the envelope. The linear feet of seams is less, because some seams are where two panels are next to each other and my math so far double counts that. But then there are more seams because of windows and doors and other penetrations, so let's call it 2400 linear feet of seams to seal. The actual cracks might be 1/4", but if the air coming in a 1/4" crack spreads out as it works its way through open cell spray foam, a rough and conservative effective crack width to use might be the thickness of the foam. With an effective crack width of 1.5" and 2400 linear feet of cracks, that 300 square feet.
Would be interesting to see
Would be interesting to see discussion of the validity of the third paragraph here:
http://nationalfiber.com/docs/CelluloseVsFlashAndBatt0212.pdf
Roughly: movement->cracks->air leaks, well after the blower door test.
Log in or become a member to post a comment.
Sign up Log in