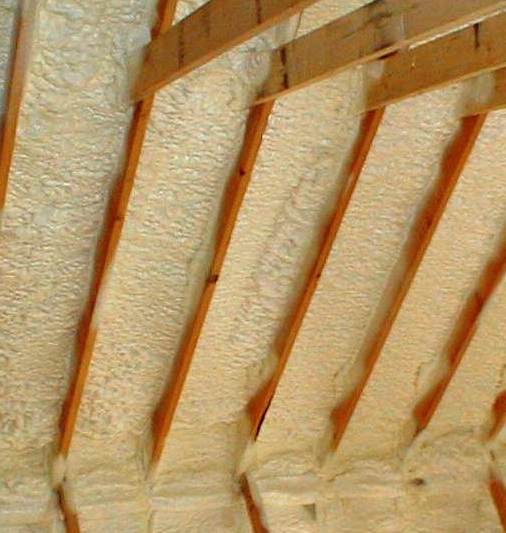
While energy experts often advise builders to exceed minimum code requirements for insulation, Icynene Incorporated, a manufacturer of open-cell spray polyurethane foam, is swimming against the tide. Surprisingly, Icynene is trying to convince builders to install less insulation than the code requires.
Icynene’s bizarre campaign against thick insulation is the second controversial move by the Canadian company. Last year, Icynene ruffled energy experts’ feathers by waging a spirited (and successful) lobbying campaign to defeat a widely supported effort (the so-called “Thirty Percent Solution”) to raise the stringency of insulation requirements in the International Residential Code.
The motive for Icynene’s current effort — let’s call it the “it’s OK to skimp” campaign — appears to be economic. The company has apparently decided that the only way Icynene can compete with less-expensive types of insulation (like cellulose) is to convince builders that they can get away with less insulation than code books require.
Air sealing requirements in the code
There’s no way to fathom Icynene’s tangled logic without first taking a look at existing code requirements for sealing air leaks.
In the 2006 International Residential Code (IRC), air-sealing requirements can be found in section N1102.4. The code requires that “The building thermal envelope shall be durably sealed to limit infiltration. …The following shall be caulked, gasketed, weatherstripped, or otherwise sealed with an air barrier material, suitable film, or solid material:
1. All joints, seams and penetrations.
2. Site-built windows, doors and skylights.
3. Openings between window and door assemblies and their respective jambs and framing.
4. Utility penetrations.
5. Dropped ceilings or chases adjacent to the thermal envelope.
6. Knee walls.
7. Walls and ceilings separating the garage from conditioned spaces.
8. Behind tubs and showers on exterior walls.
9. Common walls between dwelling units.
10. Other sources of infiltration.”
The real zinger in this list is #10: “Other…
Weekly Newsletter
Get building science and energy efficiency advice, plus special offers, in your inbox.
This article is only available to GBA Prime Members
Sign up for a free trial and get instant access to this article as well as GBA’s complete library of premium articles and construction details.
Start Free TrialAlready a member? Log in
311 Comments
2 More Problems with "The Code"
1. the word "sealed" has no units....how tight is tight enough?
how can an inspector judge by observation alone?
2. The code does not address thermal bridging
Air Barrier
NIST did a study that attributed significant energy savings (range) to a well air sealed commercial building. Could ICYNENE be inferring here that since our product is an air barrier therefore it has inherent energy saving gains that, when combined with their insulation values equate to R38?
R38 is R38
Spray foam is not the only way to achieve airtightness.
John, you're right
John,
If you or I were writing the code, of course we could do a better job. The clearest way to establish air-sealing requirements is to include a threshold -- so many cfm @50 Pa, or so many ACH @ 50 pa, or a similar threshold. But — heavens forbid! — such a logical approach would require builders to conduct a blower-door test. That's a requirement in Sweden, but here in the U.S., we're evidently suspicious of such a crazy idea.
As any good builder knows, the small investment in a blower-door test yields very valuable information. If this information is used appropriately — to do a better job of air sealing — the returns (in energy savings) far outweigh the small investment.
Now, just because the code is poorly written, doesn't mean that lax enforcement is justified. Many measures in the code are written in tangled language, but code officials still have to enforce them.
I can walk through a building site and, with my naked eyes, find examples of absurd air leaks that the builder has no intention of fixing. If I can do it with my naked eyes, so can a building inspector.
For example, how about this approach? During an insulation inspection, the building inspector asks, "I see you are using fiberglass batts. Please explain the techniques you used to ensure that each batt is surrounded by an air barrier on all six sides." If the builder can't explain his techniques, pull back a few batts and get out your flashlight.
"Equate to R-38"?
Terry,
You ask, "Could Icynene be inferring here that since our product is an air barrier therefore it has inherent energy saving gains that, when combined with their insulation values equate to R-38?"
Let's say you manage to make a building completely airtight. (No one can, but let's say you do.) If you then install R-20 Icynene, what's the R-value of your insulation? That's easy -- it's R-20. It does not "equate" to R-38. Physics does not recognize this equation.
Of course Icynene can be used as an air barrier. So can taped Advantech sheathing, or the Airtight Drywall Approach, or carefully taped interior polyethylene.
The fact of the matter is that the code requires at least TWO elements relating to building envelope performance: air sealing AND minimum insulation R-values.
shingle warranty when foaming under roof deck
Folks you may want to check if you put foam under a roof deck SOME shingle companies will not warranty the roof, thus just nulling it.
Shingle warranties
John M,
As far as I know, both Elk and CertainTeed will honor asphalt shingle warranties even when the shingles are installed on an unvented roof.
Remember, most builders scoff at the value of shingle warranties. The typical warranty will cover the pro-rated value of the remaining years of the warranty period -- not including labor. So if the shingles have a 20-year warranty, and you make a claim in year 13, you MIGHT receive 35% of the cost of the shingles -- but nothing for labor.
Ahoy hoy
Hi Martin
I have been following your writings with Energy Design Update and the like for years; keep up the good work.
One thing I can't understand though, is why you are supporting R-38? We all know the physics, and there's a negligible difference in heat transfer between R-20 and R-38 in a cavity application. It's just overcompensating for thermal bridging: The theoretical improvement from doubling R-value to R-38 represents 2% of the total theoretical heat loss, while your studs are leeching far more than that.
Regardless, the theoretical improvement between R-20 and R-38 is exactly that: theoretical: the building must be airtight to achieve this gain. In a real house, the anecdotal evidence that the difference in performance is so great is the result of air flow: R-38 allows less air flow because there's just so much more material.
Economically, we all know that the studs are the issue. There is so much wood in houses, that in both theory and practice you get better performance out of R-20 cavity and R-5 continuous. Why don't you champion that instead?
Fact is no buildings are airtight - it's a waste of money and a burden on our energy security to mandate the doubling of insulation requirements for all new homes when the reality is that we can all exceed the field performance of R-38 fibreglass with R-20 fibreglass and $50 in cans of Dow Great Stuff.
Minimum insulation requirements
Dan,
I certainly agree with you that any builder who wants to build an energy-efficient house has to address thermal bridging. If you review the articles on this topic in GBA, I'm sure you'll agree — we've consistently advocated insulation techniques that address thermal bridging.
The fact of the matter is, a builder can't drop the ball on any of these details — air sealing, minimum R-values, or thermal bridging. All of these issues must be addressed.
The best energy modeling programs (including the Passive House Planning Package) take into account all three factors when modeling a home's energy performance.
Designers who are designing buildings to meet the Passivhaus standard or to achieve net-zero energy find that in a cold climate, one often needs R-50 or R-60 insulation — even using techniques that address thermal bridging and even in buildings with low levels of air leakage. To meet these demanding standards, R-38 just doesn't cut it — not to mention R-20.
The reason is simple: a roof insulated to R-60 loses heat at a slower rate than a roof insulated to R-20 or R-38. Measurements of actual buildings, as well as the best available modeling software, prove this to be true.
If we're going to achieve the carbon reductions necessary to preserve a livable planet, we all need to learn to build much better buildings. These buildings will have envelopes that minimize thermal bridging; are much more airtight than typical new buildings; and have thicker insulation than current code minimum levels.
Equations and Evasions
It IS possible to write a prescriptive thermal performance equation in which, for instance, R-20 Icynene with 1.5 ACH50 has equal value to R-38 fiberglass with 5 ACH50, though the equation would be quite arbitrary since "leakiness" has different effects in different climates, site exposures, building heights, etc. And it would fuel an advertising war between insulation manufacturers that is already out of hand and out of bounds.
What's more surprising to me, however, in this wool-pulling-over-eyes campaign of - not just Icynene, but much of the spray foam industry - is that knowledgeable designers and builders have accepted the graphic representations of drastically diminishing returns for increasing foam thickness (such as this one from the "R-Value Fairy Tale web page": http://www.homefoam.ca/articles/R_Fairy_Tale/Reduction.gif) Icynene presents similar charts at their website.
The disinformation at the Icynene site is typical: "increasing the insulation from 6" to 12" provides an additional heat flow reduction of only 2%". It's astounding that, with the FTC regulations on R-value advertising, the spray foam industry is allowed to get away with this.
Disinformation
Robert,
As I'm sure you know, doubling the thickness of insulation from 6 inches to 12 inches will cut the heat flow through the assembly in half.
Where does Icynene get the 2% from? I haven't looked at the page where you got the quote from, so perhaps they provide a footnote or a parenthetical explanation. But the 2% number only makes sense if they are comparing the heat flow through both insulated examples with a totally uninsulated assembly — I guess that means a tent.
But in the absence of an explanation of what they are comparing these heat flows to, their 2% number is a head-scratcher.
Questionable Numbers
Martin,
I found this report on "The Economic Thickness of Thermal Insulation." I wasn't able to figure out who conducted the study, but perhaps you could share your thoughts...
http://www.insulright.com/PDF%20FORMS/economical%20thickness.PDF
Many silly graphs
James Moyer,
Thanks for the link to the Icynene document. It appears to contain much of the same information as this similar document on the Icynene Web page:
http://www.icynene.com/insulation-reliability/
The document contains a lot of silliness. It's hard to address it all. Here's a stab at addressing a few silly items.
1. The document claims, "This test procedure (ASTM C-518-02) measures the thermal conductivity of insulation material. ... This measurement solely defines the conductive heat flow resistance of the insulation material, the R-value."
I've had to refute this fallacy so often that it is tiring to address it. Here, I'll just provide a link to one of my blogs, "Understanding R-value," in which I discuss the fallacy that R-value only measures resistance to conductive heat loss.
2. In a series of bar graphs, the author of this document compares heat loss through a tent to heat loss through Icynene-insulated assemblies. But no one really cares about heat loss through a tent. If this wall was in a house, it would be illegal.
If we're looking at, say, a ceiling in North Carolina, why not start, for purposes of comparison, with an R-38 ceiling instead of a tent? After all, that's the legal minimum. You can't go any thinner without breaking the law.
Of course, the heat loss through the tent is 50 times more than through a code-minimum ceiling. This huge difference skews the graph and leads the reader to believe that the differences in the suggested options are trivial. They aren't. Compared to a code-minimum ceiling, the suggested assembly with 6 inches of Icynene loses twice as much heat. In other words, it's significantly worse than the minimum ceiling allowed by law. It only looks good when you compare it to a tent.
3. Further on, the author compares an Icynene-insulated house, using REM/Rate software, to a house with 0.7 ACH nat. That's a lot of air leakage. Depending on what formula you use, that much air leakage translates to 12 or 14 ACH @ 50 Pa. But a 2002 study of 24 newly built homes in Wisconsin -- typical homes -- showed them to have air leakage rates averaging 3.9 ACH @ 50 Pa. In other words, new homes have air leakage rates that are only 30% as high as the example chosen by Icynene to make fun of homes without Icynene. This is a classic "straw man" example -- choose a bad house to compare your product to, and you can make yourself look good.
The math is pretty clear
1/20 = .05
1/38 = .0263
.05 - .0263 = .0237
.0237 rounded off = .02 = 2%
They are comparing the two scenarios to an R-1 assembly.
So, if you have an extremely
So, if you have an extremely tight house achieved through aggressive air sealing, and you are reducing the thermal bridging by, lets say, R-10 insulated sheathing on the exterior... increasing the thickness of insulation in the wall/ roof cavities isn't all that important?
Im not arguing, just want to understand this...
Not important?
James,
I'm not sure of the origin of your argument or conclusion that "increasing the thickness of insulation in the wall/ roof cavities isn't all that important."
Yes, it's important. A wall with a whole-wall R-value of R-20 will lose twice as much heat in a given amount of time than a wall with a whole-wall R-value of R-40.
I should be more specific...
Extremely tight house through aggressive air sealing
2 inch R-10 insulated sheathing, or 2 inch gap between a double wall to control thermal bridging
Cold climate design- 5,700 to 8,500 HDD
Is there reason to increase the insulation in the wall cavities from 5.5 inches to 7.5 inches by using a 8 inch staggered stud wall (common plate wall), or perhaps even 12 inch double wall? Am I wasting the homeowner's money exceeding a certain thickness of wall cavity insulation?
About your math
Michael,
You're right. If you click on the link provided by James Moyer, you can read the assumptions about the R-value of the tent: "Let us include the outside air film at R-0.2 and the inside air film at R-0.7. The total R-value before the application of any insulation is 0.9."
Since such an assembly is illegal, it's irrelevant.
Designing walls and roofs
James,
I'm not sure whether you are wasting the homeowner's money or not. It depends on what you are trying to achieve.
As a starting point, you have to meet the local building code. After that, it's up to you — or your client.
If you are advertising that you are designing a green building, I certainly hope you will exceed minimum code requirements for insulation. Many cold-climate designers are now insulating basement walls to R-20, and above-grade walls to R-40, and ceilings to R-60. But it's still legal to build homes with less insulation.
I agree
I absolutely agree if you are promoting yourself as a "greenbuilder" you better be exceeding code required insulation levels.... and by exceeding I don't mean switching from 2x4 to 2x6 walls. I've seen plenty of "green" homes built in this area with 2x6 walls/R-38 attics which sickens me.
I was just wondering if there was ANY legitimacy to the Icynene study.
What Icynene says
James,
Icynene correctly points out that there are diminishing returns (in terms of energy dollars saved per year) from successive investments in thicker and thicker insulation. This is true of all types of insulation.
If you double the insulation thickness, you cut the heat loss in half. But an increase from R-5 to R-10 saves more money than an increase from R-10 to R-20, because there's less heat escaping as insulation improves -- and therefore fewer opportunities for savings.
All that said, thicker insulation means less heat loss. If you can afford to build it, a house with an R-60 shell will perform much better than a house with an R-20 shell.
Deciding where to draw the line often depends on your gut instinct about future energy costs. Many analysts have concluded that, even at current energy costs, code minimum insulation levels are too low. An increase in minimum requirements is therefore likely to be cost-effective.
Finally, cellulose is cheaper per inch than Icynene. That's the main reason that Icynene advocates thin insulation -- to compete.
Ahoy hoy
Has anyone tried using Fourier's to calculate the improvement offered by R-20 or R-38 over an uninsulated piece of gyprock? As is found in many existing homes throughout the US? R-2 maybe?
After air sealing and installation of R-20, what is the percentage improvement? 4%? That's still negligible for the amount of insulation.
Seems like a waste of embodied energy to me. What's the percentage improvement via R-60? That doesn't just seem like a waste of embodied energy - it is.
It'd start making sense if we started talking in real BTUs, or barrels of oil. If an unfathomable number of houses are unsinsulated, or more appropriately, not air sealed, what is the average BTU flow? What if for every 1000 BTU or barrel of oil these houses are losing, moving from R-20 to R-38 will yield a 10 BTU / 1 ounce of oil improvement? Then it stops being worth it to even discuss on the internet - you are better served focusing your attention on installing R-20 in existing building stock.
"you are better served
"you are better served focusing your attention on installing R-20 in existing building stock"
Too bad, as Martin pointed out, to do this economically contravenes code. If only there was a company willing to contravene code to improve energy performance...
Doesn't the building code have a Performance based method? Why isn't that mentioned in the original article?
On the cost-effectiveness of insulation
Dan,
You ask, "After air sealing and installation of R-20, what is the percentage improvement? 4%?"
I'm not sure where you get the 4% figure. Even using the Icynene document, the reduction in heat flow from an uninsulated assembly to an R-20 assembly is a 96% reduction in heat flow, not 4%.
According to Icynene representative Ed Reeves, Icynene advocates the use of R-20 where R-38 is the minimum requirement -- even when builders are following the prescriptive rather than performance method.
Icynene solution
If Icynene is so confident they can get by with 1/2 of the code allowed R-value, they should be willing to provide monitored results for homes insulated with Icynene to prove it. I asked for this several years ago and all I got was a long rambling letter from the Icynene engineer on how their product defied gravity, it was complete garbage.
The only way I see getting to the bottom of these trumped up claims is to monitor a house with Icynene foam insulation. As I said earlier, if Icynene was so great and cost effective the production home builders would be using it.
The value of monitoring
Doug,
I'm not sure that much would be gained by monitoring. I expect that if someone followed Icynene's recommendations and built a house with R-11 walls and an R-20 ceiling, it would perform exactly as expected — just like a house with R-11 walls and an R-20 ceiling.
scary spray foam failures
It's possible the whole explanation for encouraging installations no thicker than 5" is that the product has not been tested for flame and smoke at any thickness other than 5". Claiming 5" is sufficient for energy conservation may just be a dodge to avoid questions about code compliance.
The photo accompany this post does not show a framing cavity (very much) underfilled, but I commonly find 2X10 and 2X12 rafter bays filled with 5-8" of spray foam. Homes I look at are not using the prescriptive requirements to meet the energy code, so that in itself is not a problem (unless one actually wants a well-insulated home). However, what is an enormous problem, bigger even than poorly installed fiberglass in a poorly-sealed home, is the gap between the backside of the drywall and the face of the foam when it is left open to the top attic, as it would in the photo above. That not only does not meet code, no matter how you plan to meet code, but it is an inexcusable, classic bypass created by the most expensive insulation strategy you can buy.
Sure, knowledgeable installers would never let that happen, but apparently those are in somewhat short supply. As evidenced by the other scary foam failure I've seen several times: cracked and delaminated foam.
All said, foam's liabilities make the true cost of foam much higher than its already hard-to-justify cost.
Maximum thickness restrictions
Li Ling Young,
The question of maximum thickness restrictions for spray foam is complicated and often ignored by code officials. I wrote an article on the question for the April 2008 issue of Energy Design Update.
In that article, I wrote:
The uncertainties over the meaning of maximum thickness limitations were highlighted in a public letter from John Hogan, the senior code development analyst for the Seattle Department of Plan-ning and Development. In his January 23, 2007 letter to the ICC-ES Evaluation Committee, Hogan noted: “The ICC-ES reports specify maximum thicknesses for the products ranging from:
• 6 inches maximum in ESR-1383 (BioBased 501),
• 2 inches maximum in ESR-1615 (Insulstar),
• 6 inches maximum in ESR-1172 (Sealection 500), but only 3.5 inches maximum for attic walls,
• 5.5 inches maximum in NER-420 (Icynene), but 6 inches in certain attic constructions,
• 2 inches maximum in ER-3974 (Froth-Pak).“
Hogan continued, “It is worth noting that, in the IECC and the energy chapter of the IRC, the attic insulation requirements for all climate zones are never less than R-30 and in the colder climates reach R-38 and R-49. Consequently, none of these spray foam insulation products would comply with the prescriptive requirements for attic insulation when used individually. Further, the wall insulation requirements for the colder climate zones are R-19 or R-21. Consequently, some of these spray foam insulation products would also not comply with the prescriptive requirements for wall insulation when used individually.”
The article is available online:
http://www.naima.org/pages/resources/library/pdf/RP067.PDF
Hi Martin
The 4% is an engineering estimate as follows:
- R-2 is the base case, uninsulated gyprock in an attic: 1000 BTU loss over period X
- air sealing to prevent convective losses, resulting in new losses of 500 BTU over period X (this improvement is substantial in existing building stock due to latent heat)
- R-20 insulation installed, resulting in new losses of 80 BTU over period X
- R-38 insulation installed, resulting in new losses of 40 BTU over period X
The above analysis is not limited to Icynene: it is a general analysis of how heat is lost through a ceiling plane regardless of insulation type. However it does illustrate why spray foam insulation as an industry is capable of generating such huge improvements. In reality, the 50% improvement via air sealing is nearly always underutilized.
It seems like a breakdown in education is pervasive as well; otherwise far more construction would use the performance method. The fact that the spray foam industry is still trying to put buildings through under the prescriptive code is laziness. With proper air sealing, I could building a house that meets the Performance Method using nothing but R-5 continuous insulation, Caribbean-style overhangs, and triple glazed windows; such is the impact of thermal bridging, solar gain, and air leakage losses of humid air.
With regard to flame spread testing, why would a company invest in fire testing at a thickness greater than what meets Performance Method?
Ling, I can't see your photo, but depending on the location of the gap, it may have no impact on heat loss.
On the value of air sealing
Dan,
I have been preaching the value of air sealing for many years; no argument there. Anyone who builds a new house without doing a good job of air sealing is ignorant — and, as I've shown in this article, violating the building code.
So we're all on the same page on air sealing. In Vermont and Minnesota and much of Canada, builders of new homes have been performing a variety of air sealing techniques for many years. It should be assumed that these techniques are standard practice.
As you know, the use of Icynene is not required. Many builders are building fairly tight houses without any Icynene.
Your decision to compare heat loss in an Icynene-insulated building with heat loss in a tent doesn't impress me much. No one is building uninsulated buildings.
If you think you can build a building with R-5 insulation and still get code approval by using the performance path, so what? That may be an interesting parlor trick, but I still wouldn't want to live in your proposed building. It would still be a code-minimum building — and a lousy one at that.
We're all going to have to learn how to build much better buildings, rather than proposing fairly ridiculous ways to beat the building code at its own game — for example, by your proposed method of installing the thinnest insulation we can get away with.
Icynene solution
Dan,
If you are going to continue to ramble on, at least identify yourself as an employee of Icynene.
More on Ivynene
I used Icynene in a new house completed in 2008. Icynene was sprayed in 2007 by a local "certified, trained" whatever you want to call them. I walked the project with the Icynene installer explaining what I wanted, obviously meeting code. His cohort tried to tell me "they" are talking about that there is no such thing as conduction because the Icynene does such a great job of air sealing. I told him to quit talking so stupid. While I was picky about the installation on the walls where they neglected to get into corners in a stud space--I ended up using great stuff to fill in--I missed the roof in many places. The way these guys installed spray foam in the wall, there was no way they would achieve Icynene's air sealing properties. Icynene's R-20 is just ignorant and shows their contempt for the consumer and builder and doing the industry a dis-service. With roof inside insulation surface temperatures of about 45F with inside of 70F and outside at 9F, I knew I needed to do something. I ended up using Demilec over top of the Icynene and improved the comfort of the house and reduced the energy bill. Icynene will NEVER got any business from me, I will do everything possible to influence friends and business associates to not use their product and go with a company that has more reputable installers and treat their customers with dignity instead of like some ignoramus. Am I mad at Icynene, absolutely!
Gibberish
Uh can I get a translator for Dan's ramblings?
I am not an Icynene employee,
I am not an Icynene employee, nor do I support any spray foam manufacturer that is uninterested in educating their client base on the use of Performance Approach for compliance.
And I would like to state that yes, I do agree that we need to provide stronger enforcement on air sealing, and work to ensure the high performance of our building stock moving forward. However, I don't agree with the European method of over-insulating with foam board - it's just so much petroleum. Insulation has diminishing returns and embodied energy which must be balanced. You can't infinitely add insulation without significant energy investment. And then there's window to wall ratios which reduce the relevance of R-values further. Eventually you realize that it's better for national energy security to accept a certain quantity of energy bleed, which is replaced via renewable resources, rather than building out R-60 walls. R-60 walls just mean you're burning petroleum now, as opposed to over the life of the building.
And is the topic carbon reduction, or building code compliance? Because ignoring a base case as a theoretical "tent" ignores the fact that likely all of building and housing stock in the United States built prior to 1985 is either at 7 ACH50 or above, or has an insignificant amount of insulation. If you want to argue this, then pick a new year until the statement is correct. Perhaps the statement is correct for buildings built prior to 1975. Regardless, it is a significant portion of the building stock.
I am doing my best to not sound biased - I'm trying to look at the big picture here. That means ignoring building codes and focusing on carbon reductions only. Physics predicts that significant carbon reductions can be made across a large portion of the US building stock via attic application of R-20 insulation and a $50 worth of Great Stuff. I hope everyone can agree with this statement.
What about cost / benefit? The cost to upgrade a new air-tight attic from R-20 to R-38 is approximately the same as upgrading an uninsulated attic to air-tight and R-20. However, the carbon reductions derived from the existing building upgrade is orders of magnitude greater than the new building upgrade.
If I'm rambling, it's due to my passion.
Retrofit work versus new construction
Dan,
1. The topic of my blog is Icynene's attempts to convince builders of new homes (and building code officials) that R-20 Icynene can be substituted for R-38 insulation in new construction. I did not address retrofit work.
2. You raise an entirely new question: what is more cost-effective, installing R-20 in an uninsulated existing house or increasing the R-value of the insulation in a new home from R-20 to R-38? Of course you are right — it's more cost-effective to retrofit the old home. No argument there. But that wasn't the topic of my article. So, should we go after low-hanging fruit? Of course.
3. I disagree with you concerning the wisdom of investing in R-60 ceiling insulation. Many embodied energy studies have shown a reasonable payback for such levels of insulation. If you want to reduce the embodied energy of your ceiling insulation, just switch to cellulose; as far as I know, it has only 25% of the embodied energy per unit of R-value as Icynene.
QUALITY: Installation vs Product
Kirby:
As with most trades, there are companies that "do it right" and those that are willing to do whatever it takes to get the job, even if it means doing it wrong. I hope you will be able to separate the COMPANY that did your insulation work from the PRODUCT they were installing.
The foam manufacturer can only do so much when it comes to the actual quality of the installation. They can, and do, teach proper techniques... but it doesn't mean that the installer actually does it this way. It is the responsibility of the installing company to ensure proper installation - period.
I've seen many different BRANDS of foam installed, by many different COMPANIES. A thoughtful design (location, thicknesses, etc) and successful implementation have nothing to do with the BRAND, only the COMPANY.
I suggest directing your anger toward COMPANIES that don't pay attention to QUALITY installations, instead of toward the manufacturer of the PRODUCT they're installing.
Conduction + Air Leakage = Higher protection aganst conduction
For what we know about the actual formula to calculate R-values, it is based on conduction prevention. It has nothing to do with blocking air-leaks. This is a VERY interesting argument. One thing I want to point out is that the requirement of r-values in building codes has INCREASED 30% or more in most areas of the US in the last 5-10 years.
Please visit http://soy-based-spray-foam.com for the latest info on spray foam and other green energy efficiency products.
Since many structures insulated with mineral fiber types of insulation the air-leakage can easily result in a 40% heat loss/gain. The code officials decided that instead of monitoring the air tightness and retesting the actual air-sealing benefits of spray foam and other types of insulation that make a building air-tight, they would take one simple factor - R-VALUE - and go home with their Owens-Corning sponsor money.
What should take place is a total re-evaluation of the requirements to make the home energy efficient upon the sale of the home. Each region has and should have it's own set of regulations. Blower door tests should be performed to determine a minimum air-seal requirement (which exists but is overlooked). Then these test shells should be evaluated for their heat loss/gain using different products and r-values.
Once the tests are performed and evaluated new codes should be written and put into action. Of course this means that every home being built/sold will have to undergo a blower door test to check for air-tightness which brings the cost of a home inspection up significantly (one reason why it has been avoided.) Also, if the home fails the tightness factor there are few options other than spray foam and/or a complete renovation to solve the issue.
I disagree with the silly practices of Icynene but understand that they are trying to make a HUGE point when it comes to raising r-value codes to compensate for heat loss/gain. Code officials should understand the difference between the air-tightness of a home and the conductive values eliminated by insulation. Test the theories and re-write the codes.
R-Values and Roofing Issues
OK, right off the bat, I AM a foam insulation contractor, and I DO spray Icynene.
All of this theoretical stuff is nice and "they should change the codes" is a great statement that leads nowhere. In the end, I still have to fill out and pass a ResCheck. And this is a ResCheck that does NOT take air-sealing into account, and in North Carolina is NOT allowed to have a UA tradeoff for super-efficient HVAC equipment. If I pass this in a house using six inches in the roof deck and 3.5 inches in the walls, where is the problem????
I do believe in performance R-values, especially those arrived at by building 30 houses in ten different climates, insulating them using batts and foam in various configurations and measuring the energy use to heat and cool them for two years. (See "The Economic Thickness of Thermal Insulation" http://www.icynene.com/assets/documents/pdfs/Resources/Building-Science/The-Economic-Thickness-of-Thermal-Insulation-Dec08.pdf ) I particularly believe in performance values researched signed and stamped by an engineer. HOWEVER, ResChecks and CommChecks don't allow for these, so I go from there.
Manufacturer's propaganda aside (and that is the propaganda from 20 foam manufacturers, eight cellulose manufacturers and a half dozen fiberglass manufacturers I'm talking about) the current standard is the current standard and you have to meet it, flawed or not. I'm standing here reading statements from people who are getting emotional, stubborn, angry and inflammatory about side-issues. The real one is: CAN I PASS THE CURRENT LAWS AND CODES BY INSTALLING IN THE RECOMMENDED FASHION? If not, then you need more.
As for roofing issues, I am currently in posession of letters from the following roofing manufacturers which state that they will honor their full warranty when open cell spray foam is applied to the underside of their roof decking in a manner consistant with the codes both local and international.
CertainTeed
Elk
GAF
Coastal Metals
DaVinci Roofscapes
EcoStar-Carlisle
Life Pine Products
Pinnacle Steel Resources
Triad Corrugated Metals
Union Corrugating
Plus IKO's warranty drops to a 10-year limited from their standard warranty when insulation is placed against the roof deck.
If anyone is in possession of more than those, please let me know... I can always use more!
I guess that my biggest question to everyone is: Why are we fighting and trying to tear down one brand or another, when we should be using our energy to that lofty goal of improving the codes.
Thank you for your time,
Rich Brown
Spray Foam Contractor
Certified Spray Foam Installer
1/2 lb Open Cell Foam vs. 2lb. Closed Cell Foam
A very interesting Marketing Approach here. While I am a Canadian Installer of 2lb. Closed Cell Spray Foam, we do agree to some degree with what Icynene is claiming. We however feel we can actually achieve a greater level of air tightness with a 2lb. Closed Cell product and have twice the R-value per inch than Icynene. Lets all keep in mind that Icynene is just a 1/2lb. Open Cell SPF.
But the core argument is sound. Greater air tightness will allow for less R-value to perform as well from an energy loss perspective in the whole building. We as an industry need to get away from Manufacturer sponsored "data" and get some real non-biased independant research. Herein lies the problem. Research is usually funded by the manufacturers. The aparatus for tests are made to skew favorable results. No wonder our Building Codes are a mess when the influencers are always manufacturers with large marketing dollars to produce research that becomes fact. How many lawsuites are pending on the missuse of 1/2 lb. foam when vapour permeance levels were higher than claimed?
Air Currents Within the Insulation vs. House ACH50 Tightness
Martin: Once again you've done an admirable job of exposing misleading/incomplete claims regarding R-value. At any specified ACH, more insulation is better than less. Alternative methods can achieve air tightness, bulk spray foam is just one (rather expensive) way.
However there is a subtle distinction between air tightness as measured by a blower door test's low ACH50, and cold air currents which can circulate inside the insulation itself. For example, a house with a tight interior air barrier (e.g. airtight drywall) could have a very low ACH50 yet cold air in winter could circulate inside its fiberglass batt insulation, significantly degrading its R value.
Some years ago ORNL found that fiberglass attic insulation lost significant R value in very cold weather, as convection currents circulated cold air inside the fiberglass. Even worse, the colder the temperature, the lower the effective R value. ORNL found that using cellulose or even blowing a layer of cellulose on top of the fiberglass attic layer effectively slowed these convective air currents, preserving R value.
Fiberglass wall insulation is best installed with an air barrier on all six sides, but not all houses achieve this. A house could have low air infiltration and low ACH50 blower door results, yet cold air currents are wind washing inside the wall and ceiling insulation (although not penetrating the interior air barrier plane).
Does anyone know of any good studies which quantify an R value degradation effect, if any, of air infiltration, wind washing, or convective air currents inside the wall insulation itself (i.e., separate from the well known effect of cold air infiltrating directly into a house via holes in its interior air barrier)? Knowing the quantified magnitude of this effect for the various types of wall insulation (loose cellulose, dense pack cellulose, fiberglass kraft faced, fiberglass unfaced batt, etc.) and also for various wall thicknesses, could be a valuable guide for both new construction and, in particular, cost effectively retrofitting existing construction.
Time to weigh in
This has been a very interesting conversation to lurk around, waiting for the right time to chime in. I am a fan of spray foam insulation, and I have a pretty close relationship with Icynene, having used it on all the projects I have built or renovated in the past several years and I often recommend it to clients. That said, it does appear that they are not doing as good a job at representing their product with respect to energy codes, and as Isaac mentioned, you have to separate the installer from the company. It is practically impossible to control what each installer says to their clients.
Regarding the R38 ceiling vs R20 roofline insulation, I have seen excerpts from the same study that Jan mentioned (If anyone has the complete study, I would like to see it) regarding degradation of Rvalue of loose fill insulation in cold weather due to convective currents in the product itself. That would imply to me that as it gets colder, the R20 in the roof will approach, and eventually exceed the performance of the R38 in the ceiling when cold. Since hot weather doesn't ever reach the delta T from inside to out as cold weather, there won't be any significant amount of conduction heat gain in summer (it will almost exclusively be radiant heat gain) I believe that roof insulation will match or exceed the performance of ceiling insulation at the discussed values.
Finally, I agree with Rich Brown - if your house meets (or hopefully far exceeds) the code through the performance path, then why worry about a particular level of insulation that is based on the prescriptive approach?
Good arguments coming up
"At any specified ACH, more insulation is better than less."
I don't agree with this statement. In a building with large window to wall ratios, and high levels of both thermal bridging & air leakage, and R-40 - R-60 foam board walls & ceiling (new condominium buildings?) are a waste of petroleum and detract from energy security. John Straube's presentations have the equivalent energy transfer for this type of assembly as R-2, similar to a "tent", or uninsulated assembly.
In this type of example, I hope we can agree that it's the implementation of energy saving features, and not R-Value, that dictates energy consumption. Is this applicable for residential buildings? For custom homes it is - these tend to have high window / wall ratios.
Tract built housing there's another avenue.
With regards to changing the model, moving away from minimum code compliance, and eliminating reliance on manufacturer supplied data, I've heard rumblings that the Tokyo system of condo ratings is moving to Canada. If memory serves, this is a program developed by the Real Estate association in order to give agents competitive advantage over each other, and boy have they ever taken to it. Condos are rated based on kW/sqft, and pricing is reflective of this rating.
With regards to costs associated with blower door testing, costs can be lowered by random inspection, say 1 in every 10 - 20 houses in a tract subdivision. If the test houses fail, the entire subdivision fails. The subdivision is rated by the real estate association accordingly, and the selling price is reflective of the investment in energy efficiency made by the builder.
What's the problem?
Rich Brown,
You asked, "If I pass this [code requirements] in a house using six inches in the roof deck and 3.5 inches in the walls, where is the problem?"
The answer is, there's no legal problem -- just a performance problem. There may be many ways to meet minimum code requirements. Congratulations, you found a way to barely meet code. But shame on Icynene for encouraging such tactics -- because the tactics result in underinsulated buildings.
Underinsulated Buildings that Use Half the Energy?
Martin,
Again, where is the "performance problem" when my customers are coming back to me to say such things as their new house that is 6,700 square feet is using the exact same amount of energy for heating and cooling as their previous three-year-old home that was 3200 sq feet? Or is their a "performance problem" with documented savings of 37% in existing homes where we sprayed only the roof and crawl ceiling with 6" and 3" respectively (TESTIMONIAL: http://www.foamworkinsulators.com/audio/BradKrantzTestimonial3_1-00.mp3).
Are you putting your name on the line to say that their results would be another 37% or 50% better had I sprayed ten inches in the roof decks? I have a letter from a V.P. of a fiberglass manufacturer, documenting significant savings of both gas and electric in a house that was UNOCCUPIED last year and OCCUPIED this year, but had the heating and cooling set to keep it reasonable for showing the house last year. The difference is that between this year and last, we sprayed 5 1/2 inches of Icynene to the roof deck, while his family used power and gas this year for more heat and cooling, and for TV's and hot water and cooking and computers. All of these results were acheived by "meeting the minimum code requirements." So, bring on the minimum requirements with foam, as opposed to exceeding them with methods that don't include air sealing.
I, personally, would love to sell everyone a foot of foam in their roof and floor, and five and a half inches in every wall that will take it. Reality says that nobody can afford it. Fourier's law of thermodynamics suggests that I'd be cheating the customer after six inches. (Again, see "The Economic Thickness of Thermal Insulation" as documented above).
OK, I didn't want to get sucked into the sarcasm and such. Sorry. I am satisfied that the research and especially, my own experience for three years as a spray foam contractor show that there is serious benefit to spraying reasonable amounts of foam into a structure.
Thanks again for your time,
Rich Brown
SPRAY FOAM FOLLY
Carl,
That study that you and Jan are referring to seems to be talking about fiberglass insulation.
I have not seen it....but it Smells like a red herring.
Assume that you had a good air barrier at the attic floor, a radiant barrier roof deck and a vented attic.....
Do you really believe that R-20 spray foam at the roof deck will outperform R-38 cellulose at the attic floor?
Don't forget that there may be 25% to 60% more roof area than attic floor area.
Ask your Energy rater.
Now suppose you wanted to do something really crazy like go beyond minimum code.........
Can you increase the spray foam at the roof deck and still be code compliant?
Can you increase the cellulose at the attic floor....and still be code compliant?
Spray foam may provide an expensive way to achieve "good" performance .....
But That's It.......then you have HIT the ceiling.........
I urge you to look beyond Spray Foam and it's limitations.
John,
8 & 12 pitched roof =-
John,
8 & 12 pitched roof =- a 20% gain, what roof pitch has a 60% gain?
David C. James
Big Hair Houses
David,
You have not been to Dallas...
Thanks David
I should have merely said up to 67% more....
16/12 roof pitch is very popular in Dallas now.
15/12 roof pitch would be 60% more
We have many neighborhoods with minimum 12/12 pitch mandated by the ACC and 16/12 is preferred...I have seen taller too!
One word: Expensive
It seems that all of the peeps who are in favor of spray foam in this blog are promoting spray foam as a good air sealer which equals the better performance.
Are air sealing details in wall and roof assemblies that complicated?
Is it really that hard to seal the exterior side of the wall and execute an airtight drywall install on the interior side, allowing for a fibrous insulation material such as blow in fiberglass or cellulose?
If this is too hard for you, you shouldn't be building homes!
And why the hell are people cheating insulation levels, or trying to find other ways to just meet code? Isn't this a GREEN building blog?????
The proof is in the results
I would be very interested to see some actual performance data for Icynene insulated homes expressed in Btu's/sf/hdd, please include the insulation thickness and R-value for all assemblies. If you are really brave, the ach50 as well.
Insulation Study
John - I have excerpts from the study, I have been unable to find the original, it was done by Ned Nisson in 1992 and I believe it involved Oak Ridge National Labs. if anyone has the complete report, I would love to see it. I don't believe that it is a red herring (interesting analogy - red herrings were used to take dogs off their scent on hunts). This study did show that convective loops in fiberglass (not cellulose) insulation decreased the effectiveness by as much as 50% as temperatures dropped very low. I don't believe that spray foam is the answer to everything, I firmly believe that the answer always depends on the situation. I have been doing quite a bit of research recently on insulation for a book and there is very little information regarding the effectiveness of insulation in attics without a 6 sided air barrier. Everything I have come up with is to use more insulation because the top several inches don't do much since there isn't an air barrier on the top side of the insulation. (If anyone has more concrete information on this, I am all ears). I know from my experience in the field and as an energy rater (given than energy modeling has some serious limits), that attic insulation can be very effective if everything else is done correctly, but it rarely is. I have also done some budget studies comparing a complete air seal on the ceiling with all the important things like energy heels, insulated and sealed access, blocked up framing for decking, etc. and have determined that the total cost of spray foam on the roofline is not significantly higher than doing the ceiling correctly. If you happen to have HVAC in the attic, then the reduced system size (in a cooling climate) can actually make the spray foam system lower in price. Different conditions, say a cold climate with no HVAC in the attic probably will cost more to do the roofline. In any case, we are so used to people basically just doing a crappy job with standard insulation products, that high performance products such as spray foam look more expensive. When you start looking at the total cost to get equivalent performance, the cost differences drop significantly. Basically if you are used to building crap, high performance costs more. If you do it right, the costs are much closer. I am not attempting to defend any deceptive marketing practices that may be going on, but I don't think that vilifying a product such as spray foam insulation isn't the right path to take here.
I had some clients who were worried about using spray foam after reading this original blog post and I don't think that is a message we need to be sending to the building community. Every product can have a place in a project when it is specified and installed correctly.
Don't get excited
Carl,
Your latest post raises a lot of new issues. These are topics that my original article did not address. The topic of my blog was a marketing ploy by Icynene — specifically, Icynene's argument that R-20 insulation could be substituted for R-38.
1. I never directly addressed the issue of whether Icynene is a good insulation compared to fiberglass. However, anyone who read the article carefully will notice that I referred to air leakage through fiberglass batts as a major problem.
2. I never addressed the question of whether it makes sense to bring an attic into the thermal envelope of the house, or, if someone chooses to do so, which insulation is best for insulating between rafters.
For the record, spray foam is a useful product. As I have written many times, spray polyurethane foam does an excellent job of air sealing and insulating. I can't think of any situation where fiberglass batts would be anyone's preferred insulation.
Ned Nisson is a journalist, not a researcher. Nisson's 1992 article on fiberglass performance in attics appeared in Energy Design Update. (Nisson was EDU's founder and first editor; I later took over the job.) The first of Nisson's reports on the issue actually appreared in EDU's October 1991 issue.
The research on the effect of convective currents in fiberglass insulation on attic floors was conducted by Ken Wilkes at Oak Ridge National Laboratory.
Here's a link to his paper:
http://www.osti.gov/bridge/servlets/purl/10177817-Mls6OH/
Here's another EDU article on the topic:
http://www.ecp1.com/science/Oak-Ridge-Report.pdf
When I get a chance, I'll post information from the Oct. 1991 and Jan. 1992 articles from EDU.
More from Energy Design Update
Carl,
Here's some information from Ned Nisson's article in the October 1991 issue of EDU:
Loose-Fill Fiberglass Versus Cellulose in Cold Attics
Tests performed at the University of Illinois and Oak Ridge National Laboratory show that loose-fill fiberglass suffers performance degradation under cold conditions, but that loose-fill cellulose, if installed at relatively high density, is apparently immune to the problem.
The Insul-Safe III tests -- Trouble below 30°F
Certainteed Corporation is sponsoring a comprehensive research project at the University of Illinois Building Research Council to study the performance of fiberglass insulation under actual installed conditions.
Illinois researchers built a test building with eight separate test cells consisting of various combinations of vented, non-vented, flat, and vaulted ceilings. Each test cell is equipped with heat flux sensors that can measure the effective in-service R-value of the attic insulation system.
This past January, while monitoring the performance of four test cells, Project Leader Bill Rose observed that one attic, insulated with 14 inches (R-34) of Insul-Safe III loose-fill fiberglass, showed a noticeable loss of effective R-value at cold attic temperatures. During that one-month period, the "indoor" temperature in the space beneath the attic was maintained at 70°F, while the attic was allowed to track outdoor temperature, which varied from 0°F to 38°F.
Heat flow through the attic insulation performed as expected until the temperature in the attic dropped to about 30°F. Below that point, the heat loss increased geometrically with temperature difference, indicating a loss of effective R-value. The drop in measured R-value with temperature is plotted in the graph in Figure 1. At very cold temperature (10°F), the effective R-value dropped over 50%.
The apparent cause of the performance degradation is air convection into and within the insulation.
Similar results for Advanced Thermacube Plus
The results observed at the University of Illinois for Insul-Safe III are very similar to those obtained at Oak Ridge National Laboratory for Owens Corning's Advanced Thermacube Plus (see EDU, February and March 1991). The Oak Ridge tests suggest that convection begins to occur at about 50°F mean insulation temperature; the Illinois tests showed performance degradation at about the same point. Both experiments show about 40%-50% loss of R-value at extremely cold temperatures.
No problem with cellulose
After the initial tests on fiberglass were released, the Cellulose Industry Standards Enforcement Program (CISEP) hired Oak Ridge to run a series of tests on loose-fill cellulose in the Large Scale Climate Simulator (LSCS).
To provide a direct comparison with fiberglass, cellulose was installed in the LSCS at a thickness sufficient to obtain an R- value of R-19 (same as the fiberglass tests). It is important to note that the density of the installed cellulose ranged from 2.3 to 2.4 pounds per cubic foot -- about 15%-20% above the bag label density. The "inside" temperature beneath the test attic was maintained at 70°F, while the "outdoor" temperature above the insulation was varied from 40°F down to -18°F.
The results showed no decline in R-value at cold temperatures (Figure 2). In fact, the measured R-value of the insulation system actually increased slightly from R-18 at 40°F to R-20.3 at -18°F (Figure 2).
[The observed increase in R-value of cellulose at colder temperatures is expected. In the absence of air circulation within the material, the R-value of most insulation increases as the temperature decreases. The reason is because radiant heat transfer within the insulation decreases with mean temperature. Tests on fiberglass batts show similar increase in R-value with declining temperature.]
Before switching away from fiberglass attic insulation...
Although these test results clearly make sensational promotional copy ("Tests at national lab show 50% loss of R-value with fiberglass and zero loss with cellulose"), we do not yet know exactly how significant they are. The bottom line factor is obviously the impact on seasonal energy costs.
The observed problem with fiberglass occurred only when the attic air temperature dropped below about 30°F, and it didn't cause excessive loss in R-value (30% or more) until the attic air temperature dropped to around 0°F. For mild climatic regions where the attic temperature drops to 0°F only a few hours per year, these findings are probably irrelevant. On the other hand, in Edmonton, Alberta, or Fairbanks, Alaska, where the average outdoor air temperature is below 0°F for several months each year, low-density, loose-fill fiberglass may be unsuitable unless covered (see the following article on convection blankets). Between those extremes lies an area of uncertainty. Is there a problem with low-density, loose-fill fiberglass attic insulation in Minnesota or Vermont? No good answer yet.
The Illinois tests on Insul-Safe III found that the average increase in heat loss through the attic over the month of January due to convection was about 25%. Assuming that the attic accounts for about 20% of the total heat loss of an average house, that increase translates into about a 5% increase in overall fuel costs for the month of January.
Oak Ridge scientists are now running bin weather analyses to calculate the actual impact of the observed degradation on fuel consumption in various climates. CertainTeed Corporation is running full-year monitoring of test attics at the University of Illinois to measure the actual impact in that climate.
Batts not a problem
To avoid misunderstanding, it is worth noting that tests on batts at the University of Illinois showed no evidence of convection or loss of R-value, even at low temperature.
R-values not enough; What's your Rayleigh number?
These test results point out that thermal resistance (R-value) alone may not always adequately describe the in-service performance of insulation. Resistance to air circulation is also important.
The ability of an insulation system to resist convection depends on several factors, including insulation thickness, air flow permeability, and temperature difference across the insulation, as well as R-value per inch. These factors can all be combined to calculate a physical property known as the "Rayleigh number." The higher the Rayleigh number of an insulation system, the more likely that convection will occur.
Because cellulose is more dense, less permeable to airflow, and has a higher R-value per inch than fiberglass, a cellulose insulation system will usually have a lower Rayleigh number, and thus be less prone to air convection, than a loose-fill fiberglass installation of the same R-value.
Concern over fiberglass "fluffing"
The University of Illinois and Oak Ridge test results create additional concern over the practice of fiberglass "fluffing" which has been commonly observed in some regions of the US. Fluffing produces lower installed density. Lower density means a higher Rayleigh number and greater likelihood of convection in the insulation.
This concern probably does not extend to cellulose, which is much more difficult to fluff. The Oak Ridge tests included measurements of cellulose at two different densities. In both cases, there was no indication of convection within the insulation.
Concern over new "lightweight" cellulose products?
A couple of manufacturers now produce and sell lightweight cellulose with installed density around 1.6 to 1.7 pounds per cubic foot. Theoretically, those products are more prone to air convection than the product tested at Oak Ridge, which had a density of about 2.4 pounds per cubic foot. At this time there are no test data and no reliable models to predict under what conditions convection might occur in these lightweight cellulose products.
For more information, contact Ken Wilkes, Oak Ridge National Laboratory, Box 2008, Building 4508, Oak Ridge, TN 37831-6092; (615) 574-5931, or William Rose, Building Research Council, University of Illinois at Urbana-Champaign, One East Saint Mary's Road, Champaign, IL 61820; (217) 333-1801.
Wilkes' and Rose's reports are published in the proceedings of the ASTM symposium, (ASTM STP 1116, Graves/Wysocki, editors), available from ASTM, 1916 Race St., Philadelphia, PA 19103; (215) 299-5400.
Still more from Energy Design Update
Carl,
Here is information from Nisson's article in the January 1992 issue of Energy Design Update:
Good News on Fiberglass Attic Insulation Performance
The sensational discovery: Loose-fill fiberglass attic insulation may lose up to 50% of its effective R-value at very cold temperatures due to air convection (see EDU, October 1991).
The surprising consequence: The impact that this loss of R-value has on total annual fuel bills may be insignificant, amounting to less than $20 per year in severe climates like Minneapolis or Bismarck, and almost nothing in mild climates like Philadelphia and Washington.
The simple explanation:
With relatively thick (R-35 to R-50) insulation, the absolute amount of heat loss through an attic is so small that even a 20%-30% average increase over a year will not amount to much. For example, an R-38 attic in an 8,000 degree-day climate (northern tier US) loses only about 7.4 million Btus per year (assuming the insulation is working properly). At typical gas costs and efficiency, that amounts to less than $60 per year. Even if the heat loss through the attic were to increase a full 30% due to air convection in the insulation, the total impact on the annual heating bill would only be $20.
How cold for how long?
Another reason for the relatively low impact is that significant loss of R-value (25% or more) occurs only at very cold (12°F or lower) attic temperatures, and the worst degradation (50% loss of R-value) occurs only at -18°F. Most US climatic regions experience relatively few hours per year at those temperature extremes.
Table 1 is a listing of "bin" weather data showing the number of hours that the outdoor air temperature falls within each 5°F temperature bin during an average year for 16 US cities. These figures are from the Handbook of Fundamentals published by the American Society of Heating, Refrigerating and Air-Conditioning Engineers (ASHRAE). (Unfortunately, the ASHRAE handbook does not yet include Canadian bin weather data.)
Notice that in Chicago, the outdoor temperature falls below 0°F only 40 hours during an average year. Even Minneapolis experiences only about 230 hours below zero per year. Washington, DC, Seattle, and Philadelphia experience no hours below zero during an average year. [Note: "Average" weather data do not reflect extremes. Obviously all those cities do occasionally experience more extreme cold temperatures.]
Calculated energy penalty due to convection in insulation
Using research data from Oak Ridge National Laboratory and bin weather data, we calculated the theoretical energy penalty caused by convection in fiberglass attic insulation for a 1,700 square foot house located in each of the 16 cities listed in Table 1. The results are shown in Table 2. ( See sidebar for description of calculations and assumptions.)
Notice that the total theoretical increase in annual energy cost for Bismarck is only $16.50! And for mild climates like Philadelphia or Washington, there is no significant increase in annual heat loss. The percentage increase in heat loss caused by convection is high (27%), but because so little heat passes through R-44 insulation, the absolute increase is relatively small.
Rough estimate with better data coming
This analysis assumes that the attic air temperature is always the same as the outdoor temperature. In reality, attics are usually warmer than outdoor air by anywhere from 3°F to 30°F, depending on solar heating, ventilation rate, and other factors (see Reader's Forum, page 4).
Ken Wilkes at Oak Ridge, who supervised the fiberglass test program, is now performing computerized calculations using a sophisticated attic simulation model that he developed. When his research is complete, we should have a much more accurate picture of the problem.
However, even if this current analysis is off by a factor of two, it appears that the actual Btu or dollar impact of the fiberglass convection problem may be relatively minor.
Spray Foam Performance & Price Barrier
Carl,
I want to say something good about spray foam.
It has taught us that with a good air control layer...we can achieve good performance.
It is a good tool for achieving good performance.
Spray foam strategy has it's limits...code limits and economic limits.
Spray foam strategy can meet the 2010 goals of the 2030 challenge.
but just barely
2010 IS HERE!
I think it is time to switch horses.
We need to learn other Air Control Strategies and switch to High levels of affordale insulation.
I believe that one possible strategy would be a Structural Sheathing Air Control Layer.
https://www.greenbuildingadvisor.com/community/forum/energy-efficiency-and-durability/16103/affordable-low-energy?page=1
We can continue to build 2010 homes or we can start thinking about the future.
Exterior air barriers
John,
I agree. Yesterday I attended Efficiency Vermont's "Better Buildings" conference — one of the best regional conferences in the country. Marc Rosenbaum gave a great talk on air barriers. He's tried them all over the years. His favorite is now to use wall and roof sheathing as the air barrier.
He uses either the Huber Zip system or conventional sheathing (OSB or plywood) with taped seams. If you're taping OSB seams with peel-and-stick tape, you need to use a primer first.
Build your house with no overhangs at the rakes or eaves. At the joint between the roof sheathing and the wall sheathing, fold over your tape to connect the wall air barrier with the roof air barrier. Then you can install your exterior foam (if you intend to use any).
The rake overhangs and the eave overhangs are built as separate units, tacked on to the walls after the air barrier is complete.
He says he is getting Passivhaus-level airtightness results with this simple and robust air barrier system.
Response to Andrew's Feb. 10 post
Andrew,
You wrote that Icynene's "core argument is sound. Greater air tightness will allow for less R-value to perform as well from an energy loss perspective in the whole building."
Of course we are all in favor of greater air tightness. Every energy expert in the country agrees on that point. But:
1. Icynene is not the only way — or even the best way — to improve a home's air tightness.
2. It is disingenuous for Icynene to compare the performance of its product with competing products installed in leaky homes. It's now time to assume that ALL homes will be built with attention to air tightness.
A response to Rich Brown's second post
Rich Brown,
You asked, "Are you putting your name on the line to say that their results would be another 37% or 50% better had I sprayed ten inches in the roof decks?"
Here's exactly how I would phrase it: Assuming that two roofs have comparable thermal bridging, the heat loss through a roof that is insulated with R-40 Icynene will be half the heat loss through a roof insulated with R-20 Icynene.
Thanks for the info
Martin
Thanks for the details on Nisson's study. I've been searching for more info for months. Should have asked you earlier.
On this comment of yours: "It's now time to assume that ALL homes will be built with attention to air tightness." all I can say is, DAMN, you are quite the optimist.
Unfortunately, I think that we are still far away from the time that all homes will have that much attention paid to air tightness. In the field, at least where I work, there are so few builders and remodelers that have even the vaguest idea of air sealing, we have a very long way to go.
Regional differences
Carl,
Your post is a reminder that there are strong regional differences in construction practices. I just returned from Efficiency Vermont's conference in Burlington, where hundreds of Vermont builders attended workshops on airtightness.
We've been doing this for so many years in Vermont that the level of discussion is far beyond "Should I pay attention to airtightness?" Instead, we're discussing issues like, "What makes more sense -- using the flash-and-batt system to establish an air barrier or taping the exterior sheathing to establish an air barrier?"
NOT at the Roofline!
Martin,
What I am proposing as a Structural Sheathing Air Control Layer is not the same as you have just described.
I propose to add structural sheathing directly above the Ceiling Joists....creating an attic floor deck sheathing that wraps over the Structural Wall Sheathing.
Thermal and Air Control at the attic floor uses far less surface area and can work well with high levels of affordable Cellulose.
All of the Rake type insulations are problematic, expensive and Awkward to construct.
Fiberglass and Cellulose Study by CCHRC
Martin,
Have you seen the Roof Insulation Monitoring Study by the CCHRC Research and Testing Facility (RTF) which monitors temperatures within fiberglass and cellulose insulation in an attic?
Not being a scientist, I cant really get to the bottom of the results.
Your thoughts on the study would be much appreciated.
Here is the link:
http://www.gwscientific.com/cchrc/rtf_data/roof/roof.html
About the CCHR graphs
Brett,
While the graphs have valuable information, I don't see any way to draw any useful conclusions about the relative performance of the two types of insulation based only on these graphs.
"Skimping" on Insulation
I have become aware of a vigorous discussion taking place on this forum regarding Code requirements, minimum R-values, the performance path and similar issues. Unfortunately, the landscape has become cluttered with simplistic arguments with various parties trying to take credit for 100% of the performance innovation of certain design approaches and apportion 100% percent of the blame to a competing technology or manufacturer.
As one of the named parties, on behalf of Icynene Inc., I will take the unusual step of accepting blame for Icynene representatives making simplistic arguments regarding unvented roof designs that show an R-19 unvented attic outperforming a conventional R-38 vented attic using air-permeable insulation. To say that the improved performance is wholly a result of the insulation is simplistic and not reflective of what is truly happening in terms the building performance as a system.
To say that Icynene advocates “skimping” on insulation is equally simplistic and does not reflect our motives and desires in finding the most effective way of improving buildings.
In recent years, the unvented attic has gained popularity as DOE and others have recognized its value in:
• Making attics easier to air seal more effectively and consistently,
• Limiting duct leakage to the exterior by bringing ducts within the conditioned envelope
• Gaining efficiencies by bringing mechanical equipment within the conditioned envelope
• Solving insulation installation issues that allow convection and air leakage through and around the insulation.
I will also freely admit that the increasing popularity of the unvented attic design approach benefits spray foam manufacturers and installers because our products are particularly suited to this application.
With respect to how much insulation to use, or what performance is required of windows or how efficient the mechanical system needs to be, the ICC codes allow tradeoffs in the Performance Path, to meet required levels of energy efficiency. This is commonly used by building officials to promote innovation and is not an “Icynene interpretation” of the facts.
I would also like to go on record as saying:
• Icynene supports higher insulation levels as a means of achieving, energy efficient performance, environmental benefits, and a secure energy future for our children.
• Icynene was part of a broad coalition of interested parties who voted against the so called “30 percent solution” to upgrade the 2009 code when hearings took place in 2007. In this case, the devil is in the details because the wording of a number of provisions in the proposed changes to the Code was either poorly crafted, or contained proprietary language that limited competition for no good technical reason.
• In the 2012 Code cycle, Icynene has supported the DOE’s “30 percent solution” precisely because it is well reasoned, balanced and it attacks the logical next steps in improving building performance.
Does more need to be done… yes absolutely! Should people go beyond “Code Minimums” in terms of insulation and air sealing? Again, my answer is yes absolutely!
To the extent that designers and builders are interested in Net 50, Net 30 or Net Zero housing, we want to be there helping them do it. We want to have the tried and tested solutions available when regulatory authorities need it. To that end, our most recent Evaluation Service Reports for our various products have supplied tested applications for foam that allow for thicknesses up to and including R-50.
The spirited debate in this forum shows me that people care about the issues. My hope is that we move the discussion to the real issue… meeting the demands for greater energy efficiency and improved performance.
Sincerely,
Paul Duffy, M.A.Sc., P.E.
Vice President, Engineering
Icynene Inc.
Thanks for your post
Paul Duffy,
Thanks for your statement. I appreciate the honesty of your statement, "I will take the unusual step of accepting blame for Icynene representatives making simplistic arguments regarding unvented roof designs that show an R-19 unvented attic outperforming a conventional R-38 vented attic using air-permeable insulation." Thanks for taking responsibility, and thanks for realizing that Icynene's original argument was simplistic.
I hope and trust that Icynene's future marketing efforts will be less simplistic and more accurate.
You wrote that "With respect to how much insulation to use, or what performance is required of windows or how efficient the mechanical system needs to be, the ICC codes allow tradeoffs in the Performance Path, to meet required levels of energy efficiency." When I interviewed Icynene's engineering manager, Ed Reeves, while researching this story, I specifically asked him whether Viktor Ginic's letter was being used for builders using the performance path, or whether Icynene also advised the use of Ginic's letter for the prescriptive path. He told me, "Either one -- performance or prescriptive."
Has Icynene changed its policy? Are you now stating publicly that Ginic's letter refers only to the performance path approach and not the prescriptive path?
Prescriptive or Performance Path
This was / is clearly the Performance Path. Sorry if there was any misunderstanding.
Best regards,
Paul Duffy
Question for Paul Duffy
Paul,
In North Texas... we typically use open Cell foam.
What is the maximum thickness and R-value that would meet code?
Can you describe your "R-50"product.
"The Economic Thickness of Thermal Insulation" is bad analysis
I have reviewed the Icynene document that has been referred to over and over again--The Economic Thickness of Thermal Insulation--and their analysis is quite poor. The argument about loss of BTUs per Fourier's Law is accurate, but the attending economic analysis is garbage. They reference the ORNL study that found a 50% reduction in the efficacy of fiberglass at very low temperatures, due to convective looping within the insulation material. This was solved by simply layering a few inches of cellulose on top or by wrapping the fiber glass in air impermeable bags. They then use this to inform REM/rate economic analysis based upon envelope leakage, which is related to convective looping in insulation, but is certainly not what the ORNL study dealt with. They then proceed to test the economic returns comparing Fiberglass insulated homes with nACH 0.55 against Icynene insulated homes with nACH of 0.1. They assume this low air exchange value based upon either unstated research or convenience. I would simply add that REM/rate does not allow one to differentiate between the air permeability of different insulation materials, you can only specify installation grade, thickness, R-value per inch. So, using it to simulate the economic impacts of two insulations, based upon features that are not even captured in the model, is pretty misleading. In other words, it is impossible in REM/rate to distinguish between types of insulation. Their analysis only identifies that reducing infiltration is important, which we already know is a no brainer.
No Reason to "Skimp This Much"
While Spray Foam Insulation is a great product for providing an air seal and thermal insulation all in one product, the images provided along with the story clearly illustrate the flaw in their logic On This Home. The foam insulation shown is installed to 5.5 inches thick in what appears to be a nominal 7.5 inch deep wood assembly, there will be a significant amount of thermal bridging across the framing members which will conduct and radiate into the un-vented attic assembly they show constructed. For this approach to actually work in the "real world" you need to completely cover all the wood surfaces that directly contact the roof deck with spray foam insulation, or the attic space will overheat on warm days. We even found that a "thermal break" at least an inch wide must be cut out of the radiant barrier foil if it is on the roof sheeting and the barrier travels out of an area that requires spray foam into the attic space where foam is not required in direct contact, or it will also transfer a lot of heat under the foam and warm the attic space...
[email protected]
surprisingly, I find myself in disagreement
Surprisingly, I find myself in disagreement with most most of the comments posted on the first page of this thread.
First, let me state for the record that I'm not a big fan of spray foam insulation, as there are less expensive ways to achieve equivalent air sealing and insulation performance in new construction when one has control of the process. I also agree that manufacturer marketing hype is often just that. I get crazy when I see those energy savings comparisons based on ridiculously unrealistic baselines. And finally, I'm no tree hugger. You won't find me getting wrapped up in arguments about embodied energy. My only concern is to ensure my clients get the most efficient, comfortable, durable and healthy house their budget allows. And as we all know, budgets are never unlimited.
All that being said, I'm often asked to do HVAC loads and energy modeling for homes with spray foam. I've come to the conclusion that encapsulated attics *may* be cost effective for some homes, in some climate zones, when there's no other option than to put HVAC in the attic (of course, that's the designer's fault, not the builder's). On the other hand, new homes would be much more efficient if they were designed around HVAC and other efficiency considerations rather than the other way around. But that's a topic for another day.
I doubt I'll change many minds here, but in general, I have no problem recommending less than "code" for foam insulated roof decks over tight attics. While I don't always agree with what manufacturers and dealers have to say about spray foam, I can find no fault with this particular recommendation.
To me, this trade-off seems obvious for two reasons. First, during summer, thermal loads at the roof deck of a non-vented attic are significantly less severe than at the ceiling plane of a hot vented attic. Second, as has been discussed ad ad nauseam here, foam insulation isn't subject to convective effects. Indeed, these are precisely the reasons why codes require much higher R-values for ceilings than for walls. Buffering against a 145 degree space using unencapsulated fiber-based insulation takes a lot of thermal resistance. Encapsulated attics are another animal entirely.
Infiltration is a critical, yet separate consideration. But I give spray foam no extra points for making that job easier. Either way, my homes are going to be tight.
In general, the prescriptive tables found in every energy code attempt to achieve a reasonable balance between thermal loads on walls, floors, windows and ceiling, while considering compliance costs (e.g., codes don't require windows with wall u-factors because they wouldn't be affordable). Beyond that, prescriptive tables are a blunt instrument, meant to address the sad reality of enforcement practice. Check-offs are easy.
Just about everyone posting in this thread seems to be saying that energy codes *require* R38 (or whatever) on the roof deck of an encapsulated attic.The last time I looked, there's no prescriptive R-value for encapsulated attics (admittedly, I haven't seen 2009 tables yet). Of course, it's not surprising that building inspectors refer to the ceiling insulation requirement in the case of an encapsulated attic. Without further guidance, what else can they do? But satisfying a code official isn't equivalent to being correct. In any case, the performance path makes this argument moot. At least in this regard, Icynene stands ready to support its dealers with paper when they encounter a reluctant building inspector.
In homes I design or consult on, it's rarely necessary to invoke the performance path since my homes typically exceed all prescriptive requirements. However, when it comes to encapsulated attics, the prescriptive path lets me down. If you force me to put R38 on the roof, I would have to divert dollars from a more productive improvement. How can that be good? It's always a balancing act. Prescriptive codes simply can't achieve this type of optimal balance.
David Butler
optimalbuilding.com
Whetstone: You've got it backwards
Studies have measured roof sheathing temperatures of 165° even on vented roofs, and a Florida Solar Energy Center study of roof types and venting strategies showed peak mid-attic temperatures of only 142° with a vented black shingle roof, decreasing to 107° and 96° respectively for white metal and white tile vented roofs, with mean attic temperatures varying between 82° and 91°.
An unvented unconditioned attic can become an oven in the summer sun, but the roofing and roof sheathing can become a griddle on a "hot roof".
Additionally, a recently-published ASTM Journal study demonstrated that, both in Miami and Boston climates, an unvented hot roof with either fibrous or open-cell insulation will dry out much faster after a leak event than an unvented roof, while a closed-cell insulated hot roof with self-adhering membrane roofing underlayment simply does not dry after a leak.
Perhaps the only justifiable reason for minimizing the thickness of open-cell foam on a hot roof would be to decrease the drying time of the sheathing following a short-term leak. Your rationalizations are not based on facts.
Response to Whetstone Green
Dear Whetstone,
1. Although several readers have interpreted my article to be a criticism of the practice of cathedralizing an attic, my topic had nothing to do with this debate. I did not attempt in any way to criticize the practice of bringing an attic within the thermal envelope of a house. Instead I raised the question of whether it is appropriate to substitute R-20 insulation for R-38. I also questioned Icynene's marketing tactics.
2. I'm glad you wrote that "Infiltration is a critical yet separate consideration. But I give spray foam no extra points for making that job easier. Either way, my homes are going to be tight." We agree on that point. Assuming that to be the case, what possible justification do you have for writing, "I have no problem recommending less than ‘code’ for foam insulated roof decks over tight attics"?
It seems to be that you are simply second-guessing the intent of code officials. You're saying, "I know that code officials want R-38. But in my own personal judgment, I think R-20 is enough."
3. Your statement, "The last time I looked, there's no prescriptive R-value for encapsulated attics (admittedly, I haven't seen 2009 tables yet)" is rather astonishing. Table N1102.1 lists the minimum ceiling R-values for those following the prescriptive path. I have never heard any builder or designer make the argument that shifting the ceiling insulation location from the attic floor to the sloped rafters somehow exempts the builder from ceiling R-value requirements.
Here's the dialog between Whetstone and the building inspector:
Whetstone: "I have encapsulated my attic. I see that there's no prescriptive R-value in the code for encapsulated attics, so I just installed whatever I felt like."
Building inspector: "But right here it requires a minimum of R-38 in the ceiling of your thermal envelope. So where is your ceiling?"
Whetstone: "Well, I moved the insulation up to the rafters. So that requirement doesn't apply to people like me."
Building inspector: "Your ceiling has to be insulated. I don't care where you put your ceiling, but the code requires R-38."
There is an exception that applies to some sloped ceilings. According to N1102.2.2, in a house with an insulated ceiling — a house "without attic spaces," which probably does not apply to catheralized attics used to contain HVAC equipment — it is permitted to reduce the R-value of the ceiling down to R-30, but only for an area of 500 square feet or less. This exception doesn't provide a loophole big enough for Icynene's ridiculous recommendation to install only R-20.
4. Your final argument is weak tea indeed. You wrote, "If you force me to put R-38 on the roof, I would have to divert dollars from a more productive improvement. How can that be good?" Well, let's list the ways it might be good: (a) A house with an R-38 ceiling will require less energy for the life of the building, saving the homeowner money. (b) A house with an R-38 ceiling will require less energy, reducing carbon emissions that are threatening the future of life on our planet.
Boo-hoo, R-38 costs more than R-20, and now you can't afford some other amenity you hoped to include in the house. Well, sharpen your pencil. Build a smaller house.
Robert, FSEC has done
Robert, FSEC has done numerous studies on roofs and attics, but the the stats you quote do nothing to refute my premise. Prescriptive R-values for ceilings are selected for worst-case, not for tile, metal or low-e roofs. As with encapsulated attics, the performance approach would show that the prescriptive requirement is overkill in those situations.
As for the ASTM study, you'll get no argument from me regarding the wisdom of using closed cell on roof decks. In fact, I find very few situations where 2 lb. foam makes sense at all. But the ASTM study (at least the portions you posted here and elsewhere on the net) have nothing to do with my comment. Moreover, that study deals with vaulted ceilings, which have different thermal characteristics than an encapsulated attic. The latter acts as an indirectly conditioned buffer zone.
My comment is in no way an endorsement of non-vented attics. In fact, I agree that vented attics offer better cost-performance and durability in most cases (durability and health/safety objectives trump efficiency, but in this case there's no conflict).
What I take issue with is blind acceptance of prescriptive requirements as some sort of sacred minimum. In the case of indirectly conditioned attics, the additional cost to get to R38 using spray foam will likely be more productive if used on other efficiency improvements. Depending on house design and local climate and overall efficiency goals, I've recommended anywhere from R21 to R32 for encapsulated attics. All of these homes were in CZ3 or 4. Based on my limited experience with cold climates, it seems that ducts are less likely to be located in the attic.
BTW, I do take issue with the notion that R20 is somehow optimal for all situations and CZ's. I wasn't aware Icynene itself ever said that.
More fallacies
Whetstone,
I have no idea why you think that "Prescriptive R-values for ceilings are selected for worst-case, not for tile, metal or low-e roofs. As with encapsulated attics, the performance approach would show that the prescriptive requirement is overkill in those situations."
In fact, the prescriptive R-values for ceilings are the MINIMUM insulation levels required by code. They are not simply requirements for worst-case roofs. It is legal to exceed these minimum requirements but not to skimp.
The performance path NEVER shows that any prescriptive requirement is overkill. On the contrary; the performance path simply gives the designer an energy budget for a particular house and allows the designer to exceed code requirements in some areas as a trade-off for other features that are sub-optimal. As long as it can be demonstrated by software that the house will perform at the required energy budget, the designer's chosen specifications can be used. This performance calculation does not "show that prescriptive requirements are overkill" -- it just allows a designer more flexibility.
Higher R-value
Several questions since my original post have dealt with higher R-value so I thought I should follow up and answer the questions put forward.
1. Insulation thickness: (Q) How thick does light density foam have to be to get an R-value of R-50? (A) Assuming R-3.7/inch the answer is 14 inches.
2. Thermal bridges: (A) Why does the photo show framing not insulated?
(A) I assume the photo is of a 2 lb/cu.ft. foam (i.e. not Light density Icynene). To get the same R-value, half pound density foam will be thicker. At higher R-values, it would be standard practice to encapsulate the framing members, thereby limiting thermal bridges.
3. Optimal Thickness: (Q) What is the optimal thickness of insulation? (A) There is no "one size fits all" answer. The optimal thickness varies based on climate, fuel source/cost, and other design specific variables.
Final comment: at greater thicknesses (i.e. greater than 6"), light density foam can become a Class III Vapor Retarder such that no supplemental vapor retarder is needed. This may be beneficial in some situations.
I trust this information is helpful.
Regards,
Paul Duffy
What's about thickness limitations?
Paul,
Thanks for your recent post. Many questions have arisen concerning whether Icynene installed at thicknesses greater than 6 inches can meet code requirements for smoke and flame spread. The current ESR posted on the Icynene Web site provides some assemblies with up to 10 inches of Icynene, but these assemblies require the inclusion of controversial intumescent coatings.
Do you care to comment?
More questions here:
https://www.greenbuildingadvisor.com/community/forum/building-code-questions/16171/statement-icynene
Increased thickness
Smoke and flamespread (ASTM E-84) is not the issue... that test uses thicknesses of foam limited by the apparatus. Typically, other (assembly) tests such as NFPA 286 and the Modified NFPA 285 test are used to gain approvals at greater thicknesses.
As demand for greater thicknesses has grown, we have been doing a lot of testing to gain approvals at greater thickness. Typically, the test for limited access attic and crawlspace applications, results in the need for vertical surfaces to be covered by an ignition barrier. Some 2 lb/cu.ft density foams can be left exposed on all surfaces but they carry a significant premium in cost.
Typically, details other than attics and crawlspaces require separation of the foam from living space by a thermal barrier (e.g. 1/2" drywall.) The primary limitation here is whether the structural system can permit additional thickness to be used. Usually builders will opt for insulating sheathing before opting for double wall assemblies and the like.
Still Confused
I am still confused about whether rafter encapsulation (with open cell sprayfoam) at the roofline is code approved.
I assume that the photo in the following blog depicts an Icynene project(based on Carl Seville's reported close relationship with Icynene.)
https://www.greenbuildingadvisor.com/blogs/dept/green-building-curmudgeon/when-will-we-reach-beautiful-simplicity-green-building
The roof rafters are very likely at least 5-1/2" since almost all roof rafters are at least 2x6.
The photo seems to show rafter encapsulation.
Therefore I assume that the foam is more than 5-1/2" in some places.
Paul Duffy ....
Does Carl's photo appear to show a code approved application?
How About this example?
https://www.greenbuildingadvisor.com/homes/old-house-gets-superinsulation-retrofit
see image 8
this example is a Building America Project
Does this one appear to be legal?
Not sure I want to be dragged into this fight, John
I don't have the technical expertise of many of the people commenting on this subject, so being pulled back into the fray doesn't make me too comfortable. I'll just keep a low profile and maybe no one will notice.
Smoke and flame spread testing
John,
OK, since Paul Duffy hasn't answered your question yet, I will.
The IRC requires (in section R316.1) foam insulation to meet smoke and flame-spread standards. The mandatory test is ASTM E84. The same test is also required by ICC-ES document AC 12, "Acceptable Criteria for Foam Plastic Insulation." Most foam manufacturers are unable to pass the ASTM E84 test at foam thicknesses greater than 4 inches. That's a dilemma for foam manufacturers.
So the foam manufacturers have used alternate test methods. These alternate test methods are all assembly tests, not material tests. If a certain assembly passes this alternate test, the results are only usable by builders who replicate the exact same assembly (for example, 2x8 framing filled with foam and covered by 1/2-in. drywall). If you alter the assembly in any way, the test cannot be used to justify your use of foam.
Many spray foam manufacturers justified the use of spray foam in crawl spaces and attics using a controversial test, SwRI 99-02, that called for foam to be covered with an intumescent coating. However, this test, SwRI 99-02, is not one of the tests listed in the IRC section R314.6, which includes a list of acceptable test procedures.
The most controversial aspect of test SwRI 99-02 is that the ICC-ES allowed manufacturers to compare the flammability of spray foam with an illegal baseline: namely, fiberglass batts with exposed kraft facing. This comparison is astonishing, because IRC R320.1 prohibits kraft facing to be left exposed, and kraft facing is known to be highly flammable. To pass this test as interpreted by ICC-ES, all a spray foam manufacturer had to do was to show that the foam was less flammable than exposed kraft facing -- an illegal installation.
There was a further criticism of the SwRI 99-02 test: intended as a crawl space test, the results were being inappropriately applied to attics — where the sloping rafters behave differently in a fire. In fact, sloped foam in an attic is likely to ignite more quickly and burn more intensely than the crawl space foam tested by SwRI 99-02.
The tactic by the spray foam industry of adopting the SwRI 99-02 test drew ridicule. Some in the spray foam industry, including Neal Ganser, former president of Corbond, were alarmed at the implications. "Could we be headed for disaster in an actual building fire that moves to an attic? Could the known flame-spread characteristics of SPF in an exposed condition endanger lives?"
Mason Knowles, a well respected spray foam consultant, echoed Ganser's concerns. Knowles wrote, "Spray foam has a 'reputation' in the construction industry as being extremely flammable if not covered. If a fire is started in an attic and there is no ignition barrier, our concern is that the foam will be perceived as contributing to the extent of the fire and the whole industry gets blamed."
After being shamed in technical journals — and perhaps alarmed at the liability issues — the spray foam industry is now trying to back away from the ridiculous test comparing foam to exposed kraft facing. According to an article in the February 2010 issue of Spray Foam Magazine, the spray foam industry has agreed to phase out the use of the controversial SwRI 99-02 crawl space test. By June 2010, new test methods will be required. In the meantime, a confusing variety of interim test measures will be accepted.
Few code officials are qualified to interpret all of the documents submitted by foam manufacturers to evaluate whether the proposed foam installation is, in fact, safe. For builders worried about future liability, it's always best to cover all spray foam installations with a layer of 1/2-in. drywall.
Martin: What's the Controversy?
What's the controversy you've referred to several times about intumescent coatings?
Martin: also...
You stated: "Most foam manufacturers are unable to pass the ASTM E84 test at foam thicknesses greater than 4 inches."
Is it true that they've been unable to do this because the foams won't pass at greater thicknesses or only because of the technical limitations of the fire tunnel equipment?
Intumescent coatings
Robert,
I wrote an article about intumescent coatings in the November 2007 issue of Energy Design Update. Here's an excerpt from that article:
The only problem with intumescent paints used as spray-foam ignition barriers is that they may not meet code requirements. For any material other than the six materials listed in R314.5.3 to obtain approval as an ignition barrier, it must meet the “specific approval” criteria set forth in IRC section 314.6: “Foam plastic not meeting the requirements of Sections R314.3 through R314.5 shall be specifically approved on the basis of one of the following approved tests: NFPA 286 with the acceptance criteria of Section R315.4, FM4880, UL1040 or UL1715, or fire tests related to actual end-use configurations.”
Whether or not any intumescent coatings on the market have passed the code hurdles listed in R314.6 is a matter of technical dispute. Intumescent coating manufacturers often cite the fact that their products have passed a crawlspace fire test (SwRI 99-02) developed by the Southwest Research Institute. According to Mason Knowles, former executive director of the Spray Polyurethane Foam Alliance (SPFA), “Using this test procedure [SwRI 99-02], some SPF suppliers have obtained evaluation reports from ICC-ES that allow the use of their spray foam with specific intumescent coatings in specific applications, or even bare foam in some applications. There is some controversy over this test procedure.”
One manufacturer that refers to SwRI 99-02 in its intumescent coating marketing materials is Aldo Products, the manufacturer of AldoCoat 757: “AldoCoat 757 Ignition Barrier Protective Coating is an interior intumescent ignition barrier coating for spray polyurethane foam insulation. … This product has been successfully tested (SwRI 99-02) as an ignition barrier protective coating over spray foam insulation in non-living-space environments, such as crawlspace and uninhabited attic areas of residential insulation applications.”
When SwRI 99-02 is used to justify the use of an intumescent coating on spray foam installed in an attic, critics note:
• The test procedure is not one of the tests listed in the code (R314.6).
• Results from a crawlspace test may not apply to attics, where intumescent coatings are often installed on a slope.
• An interpretation by the ICBO Evaluation Service has muddied the waters by ruling that products that perform better than exposed kraft-faced fiberglass insulation in a test for flash-over and burn characteristics are acceptable for use in crawlspaces and attics.
One SwRI 99-02 critic is Neal Ganser, the president of Corbond, a manufacturer of spray polyurethane foam. In an article in the August 2007 issue of Spray Foam magazine, Ganser wrote, “Currently, there are several intumescent paints on the market that claim to be ignition barriers and are sold as such for attics and crawlspaces. This claim seems to be based on a Southwest Research Institute (SwRI) Test Procedure 99-02, which is not among the code-accepted test criteria. The SwRI test is configured as an 8 foot by 8 foot underfloor crawlspace, not an attic. … This means that the test is conducted in a vastly different space than the attics for which the product is intended.” Ganser also wrote, “Attics and crawlspaces are located in very different areas of a building and they may act quite differently at the onset of a fire. As such, SPF applications in these two distinct areas will likely require different test approaches to indicate the value of various fire-retardant coatings.”
Well, At Least It’s Better Than Exposed Kraft Facing
In an April 11, 2000 letter, Brian Gerber, a senior structural engineer at the ICBO Evaluation Service — the precursor to the International Code Council Evaluation Service (ICC-ES) — provided a widely quoted ruling on ignition barrier tests for spray foam installed in crawlspaces and attics. Gerber wrote, “At the July 9, 1999 hearing, the Evaluation Committee agreed with the proposal to permit recognition, in ICBO-ES evaluation reports, of foam plastic insulation without an interior covering on exterior walls of attics and crawlspaces under Section 6.7.5 of ICBO ES Acceptance Criteria for Foam Plastic Insulation (AC12), based on successful completion of one of the following three tests: 1. Comparative crawlspace tests where the performance of the foam plastic is compared with that of 3 1/2-inch-thick kraft-faced fiberglass batt insulation. The time to flash over and the time to burn through the wood-framed floor/ceiling must be less for the foam plastic assembly than for the assembly with fiberglass insulation. … In all three cases, testing will be satisfactory to justify foam plastic installed, without covering, on walls of both attic and crawlspaces, either on the interior or exterior side of wall framing.”'
When asked about the letter, Gerber explained to EDU, “We have procedures acknowledging that paper-faced insulation could be exposed in a crawlspace or attic, so the procedures call for comparing the fire performance of an installation of paper-faced insulation against an installation with foam plastic, or block foam. The laboratory will make observations of the heat and smoke, and will determine if the comparison is favorable for foam plastic.”
Some builders have reacted with astonishment to Gerber’s contention that kraft-faced fiberglass insulation can be left exposed in crawlspaces and attics. As most builders know, IRC R320.1 prohibits kraft facing, which is highly flammable, from being left exposed. As explained in Technical Bulletin No. 27, published by the Insulation Contractors Association of America, “Standard foil-faced and kraft-faced batts do not conform to the requirements of any model code for exposed applications. Their facings have flame spread indices greater than 25. The only acceptable application of standard foil-faced and kraft-faced batts is when the product shall be behind, and in substantial contact with, an approved ceiling construction material as required by the building codes.”
“Confusing” Test Reports
Any testing procedure that determines how fast a product ignites compared to exposed kraft facing has chosen to set the bar remarkably low. In an e-mail to EDU, Bob Brenk, the president of Aldo Products, wrote, “ICC-ES has published reports with a few manufacturer’s products (mostly 0.5-pound-density open-cell SPF products, a fundamentally different product from 2-pound-density closed-cell foam) saying their products can be used without an ignition barrier, although even these test reports can be confusing and (to some) seemingly self-contradictory. These products mentioned in such test reports have passed [SwRI] 99-02 when using the paper-faced fiberglass batt as the baseline test but probably have not been tested against a baseline of 1/4-inch plywood.” Brenk emphasized that the SwRI test for AldoCoat 757 compared the AldoCoat product to 1/4-inch plywood, not to exposed kraft-faced fiberglass.
One recipient of Gerber’s April 11, 2000 letter — an insulation manufacturer employee who prefers to remain anonymous — told EDU, “A house of cards has been built based on this code interpretation.”
How Well Do Intumescent Coatings Work?
In the spray-foam industry, opinions vary on the effectiveness of intumescent coatings used as ignition barriers. Mason Knowles has written, “While I believe the intumescent coatings probably are effective as an ignition barrier, I am not so sure that bare foam is safe in the conditions being allowed now.”
Unlike Knowles, Ganser has expressed doubts about intumescent coatings. “In burn test performed at UL, Class I foam covered by a code-specified ignition barrier of 1/4-inch oriented strand board (OSB) structural panel was compared to Class I foam with a high quality intumescent coating at various mil thicknesses up to 20 mils. At its best, the intumescent was only 2/3 as effective as the OSB as an ignition barrier. Had we compared it to the 3/8 gyp, also specified in the code, perhaps that divide would have been even greater. We further compared these results with 1/8-inch of a cementitious spray-on material (which is rated by UL as a full thermal barrier over SPF at 1/2 inch) and found the 1/8-inch application to outperform the OSB three times over. Good ignition barriers do exist, but they don’t look like intumescent coatings, in spite of our wishes for a simple-to-install product that actually works.”
ASTM E84 test
Robert,
You asked, "Is it true that they've been unable to do this because the foams won't pass at greater thicknesses or only because of the technical limitations of the fire tunnel equipment?"
The answer is: the problem mostly concerns the limitations of the test equipment. However, one expert I interviewed said that some spray foam manufacturers have only had their foams tested up to 2 inches (using the ASTM E84 test) because the foam can't pass at 4 inches -- even though the equipment can easily test 4 inches of foam. Here's more information from my article in the April 2008 issue of Energy Design Update:
Sometimes called the “tunnel test,” the ASTM E84 test is performed with a tunnel-shaped test apparatus measuring 20 inches by 25 feet. After foam is installed in the tunnel, the material is exposed to a 4-foot-long flame at one end of the tunnel for 10 minutes. The material is then rated for smoke development and flame spread.
The tunnel used in the ASTM E84 tests has physical limitations. “The E84 tunnel has a lid that drops down, and a water bath around the tunnel to create an airtight seal,” explains James Andersen from BASF. “The maximum thickness you can test is typically 4 inches. In some cases they can use aluminum foil around the edge of the lid and test a sample above 4 inches, especially if it is a sample of even thickness. But that is tough to do with spray foam, because of its unevenness. So, for the E84 test, we typically say that 4 inches is as good as it goes.”
If It’s Tested at 4 Inches, You Can’t Install It Thicker
Mason Knowles, a consultant and spray-foam expert from Reston, Virginia, confirms Andersen’s account. “To get your E84 test on foam plastic, it has to be tested at the thickness intended for use,” Knowles told EDU. “The great majority of test facilities can only test up to 4 inches, although some can test up to 5 inches.” …
It’s Easier For Thin Foam To Pass the Test
Manufacturers establish maximum thickness limitations for their spray foam products for two reasons: it’s harder for thick (e.g., 4-inch) layers of foam to pass the ASTM E84 test than thinner (e.g., 2-inch) layers; and full-scale testing of wall and ceiling assemblies is so expensive that many manufacturers choose not to pay for them. “Some manufacturers have gone in and performed the E84 test at less than 4 inches, because the thinner the foam, the easier it is to pass the smoke and flame spread tests,” says Andersen. “It’s tougher to meet the flame-spread and smoke requirements at a thicker application.”
Carl......not trying to single you out
Carl,
I referenced your photo because it was a handy Icynene Example....
There are examples of rafter encapsulation EVERYWHERE
Including BSC, Building America and my own work.
Missing the point of the article
We have been throwing everything in but the kitchen sink. The point of the article is that the project was being proposed to knowing not meet code. As pointed out, the code requires the home to be airtight and a certain amount of insulation in the building.
The product is required to be installed between framing members so we are installing the material between studs. For many stud cavities, they are sheathed with OSB and therefore are already airtight. If the contractor only installs the material between studs, they have missed 90 % of the air sealing required. From what I have seen in the field, the contractor wants to spray foam and walk out. Their whole argument then is bogus. They talk about their material being a air retarder (it is not a air barrier – at least it does not meet the requirements of ABAA and many states) which is good but installing the between studs is a small amount of the work required to air seal a house or building.
We should spend the time and effort to have homes and buildings built right. If someone disagrees with the Code, have you submitted Code change proposals and provided the rational for the change? If not then don’t complain.
The article was a good article and is factual – period.
Laverne, you're ignoring some of the facts.
I responded to your unfounded claim in this blog:
https://www.greenbuildingadvisor.com/blogs/dept/green-building-blog/open-cell-foam-beats-closed-cell-foam
But I'll copy it here since you're repeating your misinformation as if it's fact:
I'm no advocate of spray foam of any density, but your refusal to accept the tested air resistance of open-cell foam makes me wonder what product you ARE selling.
I have a copy of an ASTM E-283 test report, dated 6/26/2000, AIR-INS inc. # AI-01645-A, which documented two 1M² samples of Icynene - 3.25" and 5.25" thick - sprayed in a wooden frame with center dividing member, backed by tar paper interrupted at the center divider (which, itself, is not an air barrier), which resulted in 0.008 and 0.0049 L/sec respectively.
To state that testing the material in an assembly that mimics real-world applications is less stringent that testing the material in isolation, suggests that you either don't understand the facts or have an agenda.
In fact, the Air Barrier Association of America allows assemblies to be ten times as leaky as materials: 0.20 l/sec-m² @75 instead of 0.02.
Martin, thanks for the clarification, but...
If the ASTM test apparatus limits the thickness of material that can be tested, we can hardly blame the foam industry for that. And the only foam I can find that has limited their testing to 2" is Froth Pack. I believe your article indicated that NCFI Insulstar was also tested at 2", but their website gives a 4" test result. Several manufacturers show maximum testing thickness at 5.5" to 6".
And I have to differ with your assessment (as I did above with Laverne's) that whole assembly testing is somehow less accurate or "cheating". While material testing allows an objective comparison of materials in isolation, that's not how they're used. Testing actual assemblies offers much more useful information for real world applications.
On blame and cheating
Robert,
I'm mystified at your comments.
I never blamed the foam industry for their decision to perform assembly tests. Nor did I write that assembly tests are "cheating."
On Insulstar's ICC-ES report
Robert,
In April 2008, when I published my article on maximum thickness limitations for spray foam, the most current version of ESR-1615 for Insulstar was dated February 1, 2005. That report included this sentence: “Insulstar Spray Foam Insulation is a spray-applied, semi-rigid, cellular polyurethane foam plastic insulation having a maximum thickness of 2 inches and a nominal density of 2.0 pcf.”
Since then, the ESR-1615 report has been updated. The latest report allows "a maximum thickness of 4 inches," with further references to tested assemblies that include Insulstar up to 12 inches thick.
Martin Holladay’s post says
Martin Holladay’s post says pointedly that “it’s time for building officials to enforce the code as written.” We couldn’t have said it better ourselves. As a responsible industry, we respect – and follow – building code requirements. Where companies feel that a building code should be modified, there’s an appropriate forum to make that case.
Thanks
Jake Vandevort,
Thanks for your comment.
Icynene is beginning to look rather lonely.
I decided to poke around...
Icynene installers really need to clean up their act. I decided (out of curiosity) to look at how Icynene dealers in North Carolina — the state where the infamous Viktor Ginic letter is being distributed — are marketing their product. The very first Web site I visited contains a blatant exaggeration. Here's the Web site:
http://activerain.com/blogsview/663470/Icynene-Foam-Insulation-How
The entire Web page promotes Icynene. Here's what it says:
"How Effective is Icynene® Spray Foam Insulation? Foam insulations generally offer twice the R value per inch thickness as standard fiberglass batt insulation."
Talk about deception! The R-value per inch of Icynene is about the same as that of fiberglass batt insulation. But the weasly ad copy takes credit for the superior R-value per inch of a competing product (closed-cell foam insulation) and implies that Icynene is just as good.
Come on, Icynene. You can do better.
This thread is really getting
This thread is really getting interesting. Allow me to circle back to readdress several instances where you (Martin) misrepresented my words:
I never said that it does. The compliance burden clearly falls on the builder/designer to satisfy the inspector.
I have that prerogative, using the performance path.
We're not shifting the location of the ceiling. It still resides below the joists. By shifting the thermal boundary to the roof deck, we're no longer talking about ceiling insulation. This is more than semantics. This shift fundamentally changes the hygrometric and thermodynamic properties of the attic assembly. The IRC addresses the former; the IECC fails to address the latter.
However unlikely, I believe an inspector would be within his rights to require performance compliance (even with R38) on the grounds that the prescriptive insulation tables don't address encapsulated attics. In reality, inspectors simply refer to the ceiling R-value. No one complains because this interpretation is rather conservative, and anyone who desires to use less can use the performance path. Even I'm not complaining. The codes don't need to be "fixed".
Here I think you genuinely misunderstood my point. Indeed, this is the strongest argument and the only one that really matters. By "more productive improvement", I was referring to more productive *efficiency* improvements. I thought that was obvious from context. When I recommend or specify less-than-code on any component, I do so to achieve a greater overall reduction in energy usage. It's always a balancing act. When spray foam is used, the cost per inch is sufficiently high that optimizing the various insulation values and other efficiency measures can achieve a higher level of performance without increasing costs. Better yet, I talk the client out of using spray foam ;-)
You yourself often make the diminishing returns argument. This is no different except that my approach is to systematically optimize the entire enclosure within a given budget or efficiency objective. In most cases, my recommendations exceed all codes. We can argue as to whether my thermal modeling for encapsulated attics is valid or not; I think that was the point of Robert's response. I'm always interested in seeing more data that helps me refine my modeling techniques. Spray foam on floors over crawl is another area where I've found that the code minimum is not always optimal.
Again, I think you misunderstood. I wasn't suggesting that minimum ceiling codes don't apply to homes with tile/metal/low-e roofs. I was just pointing out the fallacy of Robert refuting my premise by citing temperatures from vented attics under white tile or metal roofs. When developing minimum ceiling R-values, a building code writer would naturally assume worst-case thermal loading, as might be associated with a typical dark asphalt roof.
Martin, thank you for your excellent articles and the always thoughtful commentary provided here. We operate in an industry that's full of difficult issues. We all gain from this kind of discourse.
David Butler
optimalbuilding.com
Performance versus prescriptive
David,
Thanks for your clarifications; they are helpful. With these clarifications presented, I think that your position and my position aren't that far apart.
If you are following the performance path, you may, of course, be able to design an envelope with an R-20 ceiling that still passes code. (Depending on the climate, it won't be a great building — but it can be made to pass code.)
Ed Reeves of Icynene told me that Viktor Ginic's letter was being used to advise builders following the prescriptive path. In a post responding to my blog, Paul Duffy of Icynene has backed away from that position, and now claims that Icynene intended the advice only for the performance path. This seems unlikely, since those following the performance path always perform software calculations that make such a letter unnecessary. Be that as it may, it reflects an apparent about-face by Icynene.
Those following the performance path can do a lot of funny things -- include huge areas of glass, or thin layers of insulation — as long as they balance these oddities with components that make up for energy losses in their unusual design. I have no problem with this approach, but what really matters is your bottom line — namely, your energy budget. A house with an R-20 ceiling still has a thin cap, even if you make up for it elsewhere, and is likely to use more energy than those of us in the green building community are striving for.
Finally, your distinction between the ceiling below the attic and the insulated sloped rafters remains a little puzzling. Are you advocating installing insulation in both places -- at the ceiling under the attic as well as at the sloped rafters over the attic?
Are you advocating installing
No, that would be a disaster.
I regret introducing the building code issue into this discussion. I thought it would help shore up my point. Instead it became a distraction.
Again, I do not advocate for R20 or any other one-size-fits-all approach. By using R20 as a straw man, you marginalize the benefits of sound analysis. My specs for encapsulated attics are typically closer to R30, and in all cases require 1" rafter overspray.
I've seen my share of homes where an architect abused the performance path to do some pretty stupid things. I hope I've clarified that my approach always seeks the 'biggest bang for the buck' in terms of energy performance. BEOPT exemplifies the approach I try to follow and should make my job much easier. I anxiously await its public release.
BTW, Whetstone Green refers to a 54-home net-zero energy subdivision I'm developing near Whetstone Arizona. My goal is to demonstrate an optimized approach to efficient design. HVAC and DHW loads will be individually monitored so various design approaches can more readily be compared. I also intend to log thermostat set-points in real-time in order to help normalize for occupant behavior. I recently signed a letter of intent with Building America to get some help with the monitoring system. However, infrastructure financing prospects look pretty bleak right now.
David Butler
optimalbuilding.com
BEOPT = GOOD
David,
I also am looking forward to the release of BEOPT
your stock is rising ;-)
The proof is in the pudding, boys!!!
I have a 2200sf home in Virginia that averaged $32.25/month in 2008 for heating and cooling only. The domestic hot water costs were approximately $40. This home has the least expensive vinyl window with low E and a Goodman 14 seer heat pump. Nothing Special. Except, 5.5" of Icynene under the roof deck and 3.0" in the walls. I didn't just install insulation, I installed a system.
From what I've read, that seems to have been lost. R-value is only part of the picture. Having the home work as a system is very important. Icynene is only one product in achieving that goal.
If I had spent $1000 for more foam on the roof to save $25 a year would that have really been worth it. I know some will say yes but it's my home and I have the right to say no. Some will say that I would have saved more than $25 but not acording to REM Rate. The numbers don't lie. My god!!! If I can design a home that can heat and cool for around 20 cents per square foot for the year, isn't that good enough for the average home owner.
I know everyone has their own opinion and way of saving energy but this way works too. It seems like many people on here and our industry think that they are right and theirs is the only way. Isn't it time to be open minded?
Disaster?
Why is this a disaster? As long as it's proper insulation and any vapor barrier installation is correct, what is the harm in insulating the ceiling if the deck under the roof is also insulated?
DC
Disaster?
DC wrote:
Because for most climate zones,encapsulated attics depend on conducted heat transfer through the ceiling to prevent wood components (especially the roof deck itself) from reaching dew point (or 45F, as required by IRC 806.4). See this link:
http://tinyurl.com/yzqqftq
OK now for actual field data
Howard seems like a very knowledgeable person. However, we all know we can make claims that may lead us to theoretical conclusions and I agree actual field data is where we should focus the discussion. Howard take a look at http://www.baihp.org/data/CFRes/index.htm, do you have a theory on how this house performs the way it does using a R20 roof assembly. A 4200 sq ft house operating on 3 tons of HAVC, I wonder how it would perform with R38? I believe the study Icynene references is from Oakridge Labs, a govt research lab that has "no dog in the hunt".
I believe Howard's analysis misrepresents the SPFA position. I would like to see Howard's field reseach of a house using R20 vs. R38 in a unvented attic assembly.
Correction
My comments should have referenced Martin's comments not Howard.
I look foward to seeing Martin's eight years of field reseach on this topic!
Thanks for the link
Todd,
You have provided a link to a study of a house in central Florida. It should come as no surprise to readers to learn that an R-20 roof is more appropriate to the Florida climate than it is to the climate in North Carolina or Vermont.
Here's a simple fact of physics: an R-38 roof will allow only 53% of the heat flow that occurs through an R-20 roof.
I'll put it another way: If you change an R-20 roof to an R-38 roof, you have cut the heat loss through the roof by 47%.
Oakridge Lab Study
Thanks Martin. The confusing part of your argument is how heat flow reduction is different from Florida to Vermont or North Carolina, heat flow reduction is heat flow reduction regardless of weather it is in Florida or Vermont. If you look at the data provided on this site you will find that the average roof deck sheathing temp in the summer at around ~173 degrees. Conversely Dr. Craig Dewitt of Clemson University studied a dark rook in North Carolina during the same time of the year and similar weather data and found sheathing temps of ~168 degrees.
The actual studies from Oakridge labs and others have in fact verified the percentage of heat flow is not reduced by 47% from a R-20 to a R-38.
I would encourage you to work with with a mechanical engineer and run a HVAC load in multiple climate zones using the the same ACH, similar window to wall ratios and only change the R-values in a unvented attic assembly from R20 to R38. Since a HAVC load specifically considers heat loss/gain and given your argument of a 47% improvement I would expect to see dramatically lower loads for the R38 unvented attic houses. I think what you will find is the loads do not change much at all. I also believe you are missing the physics of how vented and unvented attics actually work. There are numerous studies by Building Science Corp on the unvented attic you may want to look at. In North Carolina, as in most of climate zones 2-5 HAVC systems are typically located in the attic area. As you will find in the study I sent attic temps rarely exceed 85 degrees using the R-20 unvented attic assembly. At the same time attic temps in Florida and North Carolina using a vented assembly on a dark roof often exceed 130 degrees, We have actual field studies in North and South Carolina that illustrates drywall temps on the vented attic areas using R30-R38 fiberglass and cellulose in the summer averaging 99-105 degrees. While on a similar unvented attic in the same climate using R-20 foam has a drywall temp of 82 degrees or lower. I think you can determine from this analysis where you may be misinterpreting Icynene's postion.
Can you provide actual performance data from studies you have completed? I need more than academic theories using a test method, ASTM 518 that has not changed for over 50 years. Will a material perform differently at 75 degrees vs.170?
Response to Todd
Todd,
Vermont builders usually include more roof insulation than Florida builders — not because the physics of heat flow through roofs changes between Florida homes and Vermont homes, but because of the greater delta-T. The greater the delta-T, the more the investment in thicker insulation is justified.
Utility bill savings attributable to an upgrade from R-20 to R-38 in Florida may be slight. In Vermont, however, where the delta-T is greater, the utility bill savings attributable to the upgrade will be much higher.
Plenty of Passivhaus designers and designers of net-zero-energy homes have run modeling programs with different insulation scenarios, and plenty of very low energy buildings have been built since 1980. If you are striving for very low energy consumption, a cold climate builder should strive for R-60 insulation levels in the roof. Of course it's possible to build an R-20 roof -- and plenty of homeowners seem willing to pay the increased energy costs associated with thin roof insulation. As energy prices increase, however, some of these homeowners will have buyers' remorse.
Your article
Martin, I want to focus you back to your article. It was not focused on Vermont, but I believe North Carolina. PLEASE provide me reseach and field studies on your position if you cannot I would suggest you continue your reseach and correct your article based on field studies from PHD's who have actually reseached the issue. Should we consider Vermont weather data on all homes built in the US? I think not. You have not answered most of the questions I have raised, when should I expect them? I truly do not feel the vast majotty of the buidlers in Vermont have truly reseached why they install R-60.
Please focus on the facts I have presented and run a HVAC load and tell me even in Vermont if your article and feedback is correct. Please compare a R60 vented attic to a R30 unvented attic and let me know how this supports up your argument.
I have read thousands of articles from folks like youself and have never seen any of them provide actual in field performance data thatt supports their position...I only hope you can!
What a mess you have started...
Martin, I would agree with Todd that your original post clearly attempts to discredit Icynene for suggesting that a R20 roof line in North Carolina zone 3 and 4 is illegal in some way. In fact you have stated it is illegal many times in your article and many other post to this thread. The fact of the matter is that your statement is 100% false and is clearly full of misinformation. I would ask the editorial staff of this blog to take a closer look at your comments and attitudes toward the spray foam industry as slanderous. You sir are dead wrong. When you build a house in Vermont you cannot insulate the roof deck with R20, anyone with a pulse knows that. I would challenge you to find any field applications or comparisons to back up your opinion. There are several studies by BSC and others completed where identical homes relating to size and construction type were insulated with different insulation materials. All of these tests clearly show the homes with spray foam installed under the roof deck with R20 verus comparison fiber homes with R30 ceiling insulation have a 20 to 40% reduction in the heating and cooling cost of the home. The bottom line is that it is clearly a better. All of the math in the world cannot explain why this is. Please do your homework.....
Todd wrote:
The confusing
Todd wrote:
As Martin pointed out, the issue is the delta-t. In that sense, heat transfer is very different in VT than in FL. The difference between FL and NC is much less, or even similar, depending on where the studies were conducted. As Scott pointed out, no one in their right mind would recommend R20 on roof deck in Vermont, as was implied in some of the previous comments.
Encapsulated attics are a different type of "cap" from a thermodynamics standpoint, and therefore deserve special consideration when evaluating the appropriate R-value.
I will say this... This argument is definitely more salient in warm climates. I've noticed that my models (which admittedly are flawed, due to the dearth of research on this configuration) make less of a distinction between vented and unvented attics in cold climates than in hot climates. Intuitively, that makes sense, since in heating season, you don't see the extreme delta-t in the attic compared to outside delta-t, and in fact, we all know that vented attics are often warmer than the outside air during the winter due to radiant heating. For that reason, the rationale for unvented attics is much weaker in places like Vermont.
One more thing...
Yes, the heat flow through R38 is 47% less than through R20. If you apply R38 to the roof deck, you are not reducing the heat flow through the ceiling by 47%. The attic acts as a buffer zone.
The question is 47% of what, and at what cost.
David Butler
optimalbuilding.com
one more thing
You cannot measure energy use reduction based on the difference between R20 and R38 heat flow reduction. One reason you cannot do this is because the Rvalue test is flawed as it relates to the installed application. The difference in thermal reduction between the two values assumes all insulation materials reduce heat flow or perform the same when exposed to the same delta T. This is why an R38 fiber insulation DOES NOT perform at tested Rvalue when the temperature delta is much higher. It will only produce the tested Rvalue when the mean temperature is 75. This however is not the case for foam insulation products. For goodness sakes, open your mind.... Can anyone explain why spacecraft are not insulated with fiberglass at R1 million? Rvalues are not the only consideration in determining the thermal performance of a material, period.
Scott, I think we're on the same side
Scott, I think we're on the same side of this argument. If you refer to my original comment on previous page, I talked about the performance difference between foam and fiber insulation (especially fiber that isn't encapsulated on six sides). The point of my previous comment, however poorly made, was that in addition to that, an unvented atttic is a different animal from a thermodynamics standpoint. The attic creates a buffer zone, thus a simple Rvalue comparison is meaningless.
These are the reasons why R38 in a vented attic is not comparable to R38 in an unvented attic, and why these different configurations should not be held to the same standard for what is cost effective. Moreover, a simple Rvalue comparison doesn't speak to the issue of reduced conducted heat gain into hvac equipment and ducts located in the attic.
David Butler
optimalbuilding.com
same side
David, you are correct there is no way to compare the performance of a system i.e performance of the house by only calculating the thermal resistance of an insulation material. This is why a home insulated with fibrous materials and conventional vented attics does not perform in the same way as a home that uses foam in the walls and roof line. The problem with the industry for some people is that they are drinking the kool aid which has been propagated for over 30 years in that the only measurement of energy performance is how much Rvalue you put in your home. I would think a GBA on this blog would be a little more informed on how a home uses or consumes energy. After all the first principle of the Green movement is to reduce the carbon foot print of buildings. The only true measurement of this principle is how the home actually performs as it relates to the energy consumed to heat and cool the house compared to standard building practices. When you compare standard buildings with R38 ceilings against new technology that considers all componets and ways them in a way that reflects the real world. Foam allmost allways wins hands down when we look at energy usage and comfort. To answer the question at what cost, The capital investment for foam homes is usually recovered within 8 years.
Thank you to Scott and David
Both Scott and David are exactly correct and if I in some way implied someone should install R20 on a unvented attic in Vermont, that was not my intention.
What I am saying is that Martin's article was focused on North Carolina not Vermont and because it was he misinformed his audience and actually slandered Icynene.
I agree with Scott and David, and if Martin has any measure of professionalism he should retract his article. Or maybe as Scott suggests, the editors of GreenHomeAdvisor should ask Martin to retire as he clearly does not understand the issue very well or has another agenda.
It seems Scott and David are much better equipped to lead a blog on the topic of Energy than Martin.
Thanks you Scott and David!
Thanks, but I disagree with you on one point
Scott, don't take yourself so seriously. I think calling for retraction is a bit of an overreaction. A lot of smart folks have different opinions on this issue, and may not deal with it very often. This blog provides a forum where we can hash things out in front of those who care to read through all the posts. None of us has all the answers in building science. And I for one have learned more reading GBA than most any other energy efficiency blog on the net, even if I don't always agree with the original articles.
And by the way, Martin IS the editor and chief guru of this blog, in case you didn't notice.
I agree
David,
No doubt that this blog is a great source of information, BUT, Martin clearly went outside his realm of knowledge, attacked a company and misrepresented the Icynene and SPFA position, for this he needs to retract and apologize. If we all are to "get along" Martin needs to stop and think a little before writes such a reckless article.
Another response to Todd
Todd,
In response to your post of March 5:
1. It would be nice to know your name and your profession. Most serious posters provide their first and last names.
2. You have avoided addressing the points I raised in my blog with a classic straw-man response. You have challenged me to point to a study with certain characteristics and field data — presumably a side-by-side study of two identical houses in North Carolina, one with R-38 fiberglass insulation and one with R-20 Icynene. Obviously I am not a researcher with a big fat budget, and obviously I am in no position to run out and conduct an expensive, tailor-made study at your whim. However, the fact that I have not conducted your specific study in no way invalidates my remarks.
I welcome data and I love field studies. I have reported the results of field studies (as editor of Energy Design Update) for years. But my love of field studies and data does not prevent me from thinking or writing on an issue that does not require a field study — namely, Icynene's outrageous use of a letter to convince local building officials to allow insulation that fails to meet prescriptive requirements.
3. At no time have I ever proposed that the climate in North Carolina is identical to the climate in Vermont. Nor have I ever proposed that minimum code requirements for ceiling insulation should be identical in North Carolina and Vermont.
4. I agree with you that the majority of builders in Vermont have not researched why they install any particular thickness of insulation. However, the point is irrelevant.
5. My article did not address performance differences between vented unconditioned attics and unvented conditioned attics. I have no idea why you and some other readers have become obsessed with this issue. I never raised it, and it is irrelevant to the point of my article.
6. The point of my article was to challenge a marketing tactic by Icynene, not to attack spray foam insulation in general or Icynene insulation in particular. Anyone who has read my writings over the years knows that I believe that spray foam insulation performs much better than fiberglass batts.
Respone to Scott
Scott,
In response to your March 5 post:
1. Again, it would be nice to know your full name and your profession.
2. Concerning the legality of R-20 roof foam in North Carolina: if a local code official approves of something, it's legal. If a builder follows the performance code, it's possible to install ceiling insulation that is thinner than R-38, as long as the performance calculations show that the home's energy budget meets code minimum requirements. However, if a builder follows the prescriptive code, ceiling insulation must be R-38, at a minimum.
3. You have said that my article is full of misinformation. If so, I invite you to cite an example of misinformation.
4. You have called my statements "slanderous." The word "slander" is usually reserved for the spoken word; journalists like me are more likely to be concerned with libel than slander. I feel confident that my reporting is accurate, and therefore I don't worry at all about libel litigation.
5. You wrote, "When you build a house in Vermont you cannot insulate the roof deck with R20, anyone with a pulse knows that." In fact you can — as long as you follow the performance code.
6. For years, I have reported the results of studies that show that spray foam insulation performs better than fiberglass insulation. I know it, I believe it, and I report it. Why do you think I believe differently?
7. You are all riled up because you believe that the R-value test is misleading. You wrote, "R-values are not the only consideration in determining the thermal performance of a material, period." I agree. I never wrote that they were. Of course an airtight assembly performs better than a leaky assembly! That's why green builders preach the virtue of air sealing. This is not 1972. Trust me — everyone reading this page knows the value of air sealing. It should be a given for any reputable builder.
8. In your next post, you return to the same point when you write, "The problem with the industry for some people is that they are drinking the kool aid which has been propagated for over 30 years in that the only measurement of energy performance is how much R-value you put in your home. I would think a GBA on this blog would be a little more informed on how a home uses or consumes energy."
I can only assume that you haven't bothered to explore our Web site or actually read anything we've written. Here are a few sentences, taken almost at random from our "Insulation Overview" page: "It takes more than just insulation to slow heat. Stopping air leaks is just as important—maybe more important—than adding insulation. Unless builders prevent air from leaking through walls and ceilings, insulation alone won't do much good."
On my retirement
Todd,
You wrote, "Maybe as Scott suggests, the editors of GreenHomeAdvisor [actually, this Web site is GreenBuildingAdvisor] should ask Martin to retire as he clearly does not understand the issue very well."
Of course it's up to my employers to decide whether to give me a gold watch (or perhaps just an empty cardboard box to clean out my desk). I'll let you know if there are any developments in that arena. So far, I'm still here.
To address the question of whether or not I understand the issue very well, I must admit that my opinion differs from yours. Sadly, there are few U.S. journalists capable of writing on issues relating to heat flow and insulation. Whenever I attend the Department of Energy's Conference on Thermal Performance of Exterior Envelopes of Whole Buildings — something I have done faithfully since 2001 — I am the only journalist there. I doubt there are many journalists in the country who have devoted themselves as assiduously to understanding these issues as I have.
To David, a.k.a. Whetstone
David,
Thanks for the kind words.
Response to Martin
Martin, please see my comments below on a point by point.
1. My name is Scott Nichols, I am the principle of Environmental Resource Partners. I am a senior Resnet rater for 5 years, LEED H program manager, Certified Green Rater, EarthCraft House technical adviser. My company provides green building consulting, LEED H program certifications, Energy Star, HVAC load sizing and training, Home Energy audits, etc.
2. In North Carolina there are two methods in achieving energy compliance. One is to following the prescriptive requirements of the energy code i.e. R13 walls, R19 framed floors and vaults, R30 ceiling below vented attics and window performance < than .40 Ufactor .40 SHGC. The second method is to show compliance via the performance method which compares the as built homes envelop u average to the prescription envelop requirements of the sites climate zone. when the as built home meets or exceeds the prescriptive requirements the home is in compliance of the written code. Correct me if I am wrong but this method is the national code. So basically there are two methods to demonstrate energy compliance. This has nothing to do with a local code officials interpretation of the code or an alternate method approval by the local code official as you have stated many times. It either prescriptive or performance compliance, the code does not favor or prefer one method or the other as you seems too. NC is currently under the 2006 ICC with state amendments which requires Climate zones 3 and 4 to have R30 in the attic floor and vaulted ceilings can be R19. Please check your facts.
I will respond to your others points as time permits.
Performance and prescriptive
Scott,
Your description of the difference between the prescriptive and performance code does not differ in any substantial way from my description (except for the fact that a code official from Carrboro told me over the phone that the local code in Carrboro has a minimum prescriptive ceiling R-value requirement of R-38, not R-30 -- this may vary depending on different locations in North Carolina due to the climate map).
Ed Reeves, Icynene’s engineering manager, told me that the letter boasting that R-20 Icynene performs as well as R-38 fiberglass insulation was being used by builders following the prescriptive path. Once my blog was published, Icynene backed away from that position, claiming that the controversial letter was intended only for those following the performance path. This explanation from Icynene strains credulity, however, since builders following the performance path would have no need for such a letter, since they would be demonstrating code compliance with a software program and thus would have no need for such a letter.
Name and number
Martin, please send the name of the code offiical you spoke with that imformed you R-38 was required in this jursidication.
ORNL Study
Martin,
Based on the study from ORNL I believe Ed maybe correct relative to the performance of fiberglass materials on a vented assembly. Please provide your comments on this study given your reference to other ORNL studies you have posted and agreed with in past blogs?
http://www.ornl.gov/info/ornlreview/rev26-2/text/usemain.htm
Code official
Todd,
On February 1, 2010, I called the Carrboro Inspections Department. The gentleman who answered my questions there was Rick Wade. He told me that the R-38 requirement for Orange County was found in the North Carolina State Building Code. His answer was consistent with requirements in the 2006 IRC.
The link does not go to a study
Todd,
The link you provided goes to a page describing the Building Envelope Research Center at ORNL. Your link does not go to a study.
Complaince Facts for North Carolina
1) In your article you say "In Climate Zone 3 — an area that includes architect Sophie Piesse’s home town of Carrboro, North Carolina — the minimum prescriptive requirement for ceiling insulation is R-38. If a contractor wants to install Icynene insulation in a Carrboro ceiling, the minimum required depth is 10 1/2 in., not 5 1/2 in" - This factually incorrect –See table N1102.1 of the North Carolina 2009 Energy Conservation Code. If you do not have a copy you can purchase a copy of the 2009 NC code online for $85. You will find that for all counties located in climate zone 3 require R-30 attic/ceiling insulation not R-38 as you incorrectly say in your article.
2) In your article you say and imply on numerous occasions that using R20 in the assembly both Icynene and Sophie was referring to “the unvented attic using R-20” and you illustrate pictorially on you posting that this is illegal and this is factually incorrect. You go on to say I believe in a response to Scott that if the code official says it’s not allowed then it is not. The facts are that this code official should read his own darn code and the contractor should have ask for an interpretation by NC code council and in the case the code official would be overruled. You seen to understand the performance path, did you ask this code official about this when you spoke with him? If you did not ask, I guess I’m confused why as you represent yourself a journalist. Martin you should become a bit more informed on the code before you attack a company or persons. Below is from the NC 2009 Energy Conservation Code. The code official is correct that the prescriptive requirement is R-38 for Orange County. However the very first paragraph of the NC 2009 ECC is below and he should have informed you of this or as a journalist and “Energy Expert” you should have asked if NC had stated language in the code for performance path Compliance. This should have been clearly noted in your article if you are a “fair and balanced” journalist! I guess all of those log cabin homes in Vermont are performing very poorly if prescriptive r-values for walls this the only path as you imply, a 7” cedar log has a prescriptive r-value of what? http://www.universityofloghomes.com/rvalue_for_log_home.htm
N1101.2 Compliance. Compliance shall be demonstrated by either meeting the requirements of the International Energy Conservation Code or meeting the requirements of this chapter. Climate zones from Figure N1101.2 or Table N1101.2 shall be used in determining the applicable requirements from this chapter. ResCheck 4.0.0 for the 2006 IECC shall be permitted to demonstrate compliance, except that a SHGC of 0.4 is required for all zones and that envelope requirements may not be traded off against the use of high-efficiency heating and cooling equipment. No trade-off calculations are required for termite inspection and treatment gaps required for slabs and basement walls.
3) Martin, you seen to have issue for whatever reason with companies like Icynene providing a different opinion than yours. I as many of your readers did not speak with the people you did at Icynene, the code official or with Sophie or for that matter have reviewed the entire letters you say you have. But based on the way you misrepresented the facts in your article that I and others have informed you of I can only conclude that you have taken many journalistic liberties with the facts.
4) What I would have hoped you would be more frustrated with is the as you call it “bamboozling” of the codes and homeowners from the fiberglass industry for many years. The facts are that Icynene is correct; a material that provides both effective R-value and an effective air barrier does perform better at lower r-values than fibrous materials. This is backed up by ORNL Research paper “Fighting the other cold war”. This study proves what Icynene I believe informed you of, in that convective loss through loose- fill fibrous insulation reduces its effective performance by up to 50%. So to use your logic and if ORNL research is correct, in Vermont installing R-60 loose fill fiberglass on a vented attic the homeowner is actually getting R-30 performance – now Martin who is “bamboozling” who now? I guess in Vermont we need R-120 of fiberglass to get the prescriptive r-value performance homeowners are being sold. Where is the “Dereliction of duty” now Martin!
Misinformation
Martin, in one of your responses back to Scott you asked him to provide one instance of misinformation. I believe in my last response I provided at least one and I believe many more given the logic behind your article.
North Carolina has two climate zones
Todd,
As I'm sure you know, North Carolina has two climate zones — Zone 3 and Zone 4. Carrboro is in Zone 4, according to the IECC list of countries (Orange County).
I have several copies of the IRC and the IECC, going back several years, and therefore I have access to Table N1102.1 and consulted it when I wrote the article.
I am confused by your statement that "The code official is correct that the prescriptive requirement is R-38 for Orange County." Since, as far as I can tell, Carrboro is in Orange County, you appear to be contradicting yourself. If it's R-38, then we agree.
However, even if the prescriptive code in Carrboro requires a minimum of R-30 insulation, that doesn't mean Icynene is off the hook. The use of R-20 insulation would still not meet prescriptive code requirements, so my objection to the Icynene letter still stands.
A simple word search of my article reveals that I never wrote that the use of R-20 Icynene in Carrboro is illegal. The word "illegal" was only used in reference to leaky homes that fail to comply with air sealing requirements.
As I have written many times, anyone who follows the performance path can choose to install any type of ceiling insulation he or she wants, as long as other features of the home somehow compensate for the increased heat flow through the ceiling. My objection is to the use of the Viktor Ginic letter from Icynene to convince code officials to allow R-20 insulation by builders following the prescriptive path. If I had asked Rick Wade, "What is the minimum requirement for ceiling insulation in Carrboro for builders following the performance path?" the question would have been meaningless. There is no answer to the question; the code specifies a minimum ceiling information only for those following the prescriptive path. So I fail to see what my decision not to ask a meaningless question leads you to conclude that I am not a journalist.
I would strongly advise against anyone building a 7-inch-thick log home in Vermont unless they were willing to insulate the walls on the inside.
Todd, I've written several articles on energy code compliance, including "A Builder's Guide to Energy Codes" (Journal of Light Construction, June 2007), so I really don't need you to lecture me on the well-known difference between the prescriptive path and the performance path.
It astonishes me that defenders of Icynene are so adamant in their advocacy of installing R-20 ceiling insulation. If you just slowed down and took a deep breath, you might realize that selling R-30 ceiling insulation would mean that Icynene could actually sell more insulation. And guess what? A home with an R-30 ceiling loses less heat than a home with an R-20 ceiling.
“Fighting the other cold war”
Todd,
I continue to be mystified by your references to the ORNL Web page called “Fighting the other cold war.”
http://www.ornl.gov/info/ornlreview/rev26-2/text/usemain.html
Although you insist on called this Web page a "research paper," it isn't. It's simply a description of the test facilities at ORNL's Building Envelope Research Center. (It's nice to see a photo of researcher Andre Desjarlais, who I have interviewed many times, but visiting this Web page doesn't promote your argument in any way.)
Research by any other name is research
I'm not sure why you choose not to read the article through Martin. Can you also address the rest of my last posting or do you just choose to focus on weather you call the information in the article research or not? It is stated that the facility was used by researchers to prove what I said in my post. Again, can you address all of the other items in my last posting or do you want to focus on what you deem research or not? How about those illegal log cabins that do not prescribe to your prescriptive R-value argument?
Using the LSCS, ORNL researchers working with Energy Saving Solutions, Inc., a private insulation manufacturer, determined that, under cold winter conditions, up to 50% of the heat loss through attics insulated with some types of low-density, loose-fill fiberglass is a result of convection--warm air circulating through the insulation.
Researchers confirmed the presence of this convection cycle by analyzing infrared photographs of the top surface of various types of attic insulation. Infrared photos of low-density, loose-fill fiberglass attic insulation showed a pattern of six-sided hot and cold areas that is characteristic of convection heat loss. This evidence, combined with direct measurements of ceiling heat loss in the LSCS, led researchers to question the effectiveness of some common types of blown-in fiberglass insulation in very cold weather.
Loose-fill fiberglass insulation
Todd,
I have never advocated the use of loose-fill fiberglass insulation in attics, so you are clearly introducing a new red herring. Energy Design Update has reported extensively on the question of cold-temperature convection in loose-fill fiberglass; this is an old issue that dates back several years. Those who use cellulose insulation don't have to worry about it.
If you are unlucky enough to have a house with loose-fill fiberglass insulation in your attic, you should hire a cellulose contractor to blow a cap of cellulose insulation on top of the fiberglass.
In any case, the percentage of U.S. homes with loose-fill fiberglass attic insulation is small. Most use batts, which don't suffer the convection problems to the same degree.
I have consistently advised builders to choose building systems that emphasize air tightness. Anyone who asks my advice for insulating an unconditioned attic gets the same advice:
1. Install an impeccable ceiling air barrier.
2. Insulate with cellulose insulation to a level that exceeds minimum code requirements.
Icynene's reputation is severely damaged by tactics like yours. You have sought out a discredited insulation technique — loose-fill fiberglass insulation — which amounts to one of the worst available insulation options on the market. After pointing to this lousy stuff, you brag that R-20 Icynene can equal its performance. Who cares? Both options stink. The code calls for R-38. Why not install R-38, and do so proudly?
NC Climate Zones
Martin , it really does not matter what you write, now does it. You asked Scott to provide one item where your article was incorrect, well I gave you one where you said R-38 was required in NC climate zone 3, that was incorrect, right? Martin, I know it's hard but can't you say, I made a mistake this one item?
I fail to understand where my agreement that NC climate zone 4 does requires a prescriptive R-38, somehow contradicts my position? What I do say is that NC clearly provides for compliance to this using the performance path and this is not mentioned in your article in any real detail.
BTW - there are three climate zones in NC 3-5.
Why do you not post the entire letter from Victor as I'm fairly sure he would not represent R-20 as meeting prescriptive R-value. As you have misread most of my information it should be clear that you also may be misrepresenting Victor's letter.
I will get my own copy of the entire letter from Victor? He is with Icynene right?
Martin, I have read many of your articles and agree with much of what you write. On this matter you are dead wrong. I am not an advocate of any foam mfg, I and a very large proponent of not misleading people as you have done in this particular article.
You again are incorrect a R30 vented attic will not outperform a unvented R20 using foam especially when HVAC systems are also located in the attic and R20 of foam will most certainly outperform R30 or R38 of fiberglass in a vented attic.
Cellulose to the rescue
Martin, you must know we have audited numerous homes using R30 and R38 cellulose where the homeowner complained of comfort issues in their upper levels, I guess that's working well. My neighbor has this problem and if you would like to call him I how he would love to hear from you.
Facts please
In your response above you say that using R-20 in a unvenetd attic ( the assembly Victor and Sophie were discussing) will increase the heat flow into the conditioned space is again false. Every study you will find will prove this. If you are not a fan of this assembly, that is fine but I do not believe you should misrepresent its performance. I suggest you research this assembly and write an article. Maybe folks like me will stop responding to the poor article you wrote.
Once again the prescriptive home performs poorly
Even though Martin you would not advise anyone to build a log home without interior insulation can you explain the contents of this study? Oh yes, I'm sure the log home industry in Vermont will also have a few choice words to add! I would love to buy a log home and see drywall on the interior! See http://www.universityofloghomes.com/rvalue_for_log_home.htm. An R10 7" log wall assembly outperforming a R13 stick built wall assembly by 24%, I assume the stick built house used something other than foam, but I would need to call to verify. How in the "blank" can this happen if we are to believe your argument of prescriptive R-values and heat flow reduction? You did not address this in your post about log homes, if you did I may have missed it.
If there are any log home mfgs that follow Martin, I would love to hear from you!
Todd
take a chill pill buddy... have someone check your posts too... weather?..... is you know... rain... sun... what's going on outside Todd... whether... that's the word you were looking for above. You are ranting so hard that your sentences are on the verge of being incoherent.
as to your rant... my take on it... both of you are correct in different ways....
Unvented roofs are way better than vented for sure. I have built such with Icynene... 5" sprayed encapsulating truss structures... great performance... I am very happy. That said... I am now shooting for Passive House insulation levels (high high R-values with cellulose) at prices my customers will be feeling are affordable.
Work with Marten Todd... yes? the rant is counterproductive my friend...
hey... Todd... if you like learning... try looking up game theory... diners dilemma... prisoners dilemma... very interesting reading Todd.
adjac
Nice Adjac
The weather was great here today...on the back porch conversing with Martin...enjoyable....
We're not getting very far with this dialog
Todd,
I'm about to wind down this dialog, since we seem to be talking past each other.
1. I'm glad you agree that the prescriptive code for Climate Zone 4 requires R-38 or better ceiling insulation. We agree; my article was correct on that point. (Whenever my article referred to this requirement, I used the word "prescriptive." For example, I wrote, "Since the local prescriptive code (the North Carolina State Building Code) requires ceilings to be insulated to a minimum of R-38..."). I have no idea why you are making the accusation that my article said that R-38 is required in Climate Zone 3. I wrote, "In Climate Zone 4 — an area that includes architect Sophie Piesse’s home town of Carrboro, North Carolina — the minimum prescriptive requirement for ceiling insulation is R-38."
2. I'm glad that we agree that the NC code (like every energy code in the country that I am aware of) allows builders to choose between the prescriptive path and the performance path. We agree on that point as well.
3. You wrote, "You again are incorrect a R30 vented attic will not outperform a unvented R20 using foam." I have no idea what paragraph, if any, you are quoting from. I never said any such thing. In case anyone is still confused, I'll restate my position: (a) My article never addressed a comparison between unvented conditioned attics and vented unconditioned attics. (b) The laws of physics dictate that R-30 insulation outperforms R-20 insulation.
4. Concerning your point: "We have audited numerous homes using R30 and R38 cellulose where the homeowner complained of comfort issues in their upper levels" — I have no reason to doubt you. There are lots of reasons why this is possible; I suspect the homes you audited had inadequate ceiling air barriers and insulation installation defects. I'm glad you are auditing these homes and helping these homeowners. I have performed similar work and I have probably provided similar advice to the advice you provided to these unfortunate homeowners.
5. I have no idea why you think I should defend the log home industry of Vermont, other than the fact that I live in Vermont. You're really out in left field here. (By the way, it's very common for log homes in Vermont to be finished with gypsum drywall on the interior. Come on up and visit, and I'll show you a few of them.)
Response to Scott
Scott,
Thanks for identifying yourself — "Scott Nichols, I am the principle of Environmental Resource Partners. I am a senior Resnet rater for 5 years."
Readers may be interested to know that Scott Nichols is also (along with his brother Todd) a principal and co-owner of Carolina Foam Solutions.
http://67.199.14.253/uploads/file/Charlotte/Fall%2008-%20PDF's/CFS.pdf
According to the home page of Carolina Foam Solutions, the company is "a dealer for the Icynene Insulation System."
http://www.carolinafoamsolutions.com
Mysteriously, the RESNET directory of certified RESNET raters does not include a listing for Environmental Resource Partners or Scott Nichols.
Question
Martin,
I believe the premise of your article is that unless we insulate structures using prescriptive R-values (with air sealing and material performacne being equal) then somehow the structure will perform poorly. Am I correct or am I misreading your article?
Was this you?
Martin,
Did you publish an article in 2005 entitled "Every Failure Holds A Lesson"?
The premise of my article
Todd,
No, the premise of my article is not that "unless we insulate structures using prescriptive R-values (with air sealing and material performacne being equal) then somehow the structure will perform poorly."
The premise of my article is that R-20 insulation allows more heat flow than R-38, and therefore performs worse.
If you are referring to the article in Energy Design Update, then the answer is yes, I am the author.
Article
Martin, on this site you provided a link to the article you wrote "Every Failure Holds A Lesson". Unfortunately the link to this article is broken. Do you have another site URL where I can access the article?
Article premise
Martin, your article is discussing ceiling or roof insulation R value requirements of climate zone 4 of the 2006 IECC. Yes or No ? I hope we can agree the answer is yes on that question. That being said let's look at your last post carefully. Here it is below.
No, the premise of my article is not that "unless we insulate structures using prescriptive R-values (with air sealing and material performance being equal) then somehow the structure will perform poorly."
The premise of my article is that R-20 insulation allows more heat flow than R-38, and therefore performs worse.
Your first paragraph say's "unless we insulate per the prescriptive code the structure will perform poorly."
This statement is the problem we all have with your posting. You are saying that if you do not follow the prescriptive code for component Rvalue's your home will perform poorly. That statement has serious flaws and is misleading.
Now back to the component Rvalues for ceilings. I have a few questions to establish a baseline of understanding.
1. What is the installed performance of loose fill fiberglass in and attic ceiling? I have several studies that provides this information, but I am sure your have the same, but please state your understanding of the test results.
2. Given the installed performance of loose fill fiberglass based on tests conducted, do you believe the assembly should be required to add additional R value?
3. Are you aware of any tests conducted on an foam attic or wall assemblies that demonstrates the in field performance of the installed foam assembly?
4. Is it your opinion that blown in fiber glass attic assemblies perform or maintain their component tested RValue's in the field application?
On the Resnet listing issue, I have decided not to renew my membership as of today, which does not mean we a not in good standing with ResNet it just means I have not paid the $400 listing fee on the site.; I am not sure why that is even an issue here.
Response - North Carolina has two zones
I think I may have already stated this, but NC actually has three climate zones...3-5.
Martin, you have said several times that you never used the word illegal in your description of using something less than R-38. In your March 7th response you say...
"A simple word search of my article reveals that I never wrote that the use of R-20 Icynene in Carrboro is illegal. The word "illegal" was only used in reference to leaky homes that fail to comply with air sealing requirements.'
Were in past response to a post on this site you said....
"If we're looking at, say, a ceiling in North Carolina, why not start, for purposes of comparison, with an R-38 ceiling instead of a tent? After all, that's the legal minimum. You can't go any thinner without breaking the law."
I'm don't know Martin how any reasonable person or finder of fact can determine anything different that you did in fact say that unless R-38 was used it is illegal or as you say specifically "breaking the law". Unless that is you are a fan of people like Bill Clintion and we need to talk about "it depends on what the meaning if is....is.... Or I guess becasue you did not say this in your article, but did say in a reposnse to a post, you are right, you did not say this..right?
Piece of work...you next gig maybe the New York Times, you'll fit in well!
RESNET membership
Scott,
Thanks for letting us know that "I have decided not to renew my membership" in RESNET. The only reason that might be what you call an "issue" is that you recently claimed "I am a senior Resnet rater." Perhaps you meant "was."
You are obsessed with tracking down the worst-performing products in the U.S., so that you can prove that Icynene can match its performance. It’s sad that your customers accept such low-bar comparisons.
N.Y. Times
Todd,
I'd be happy to go up against you, vying for any journalism job in the country (although evidently you have a lower opinion of the New York Times than I do).
You pulled a quote out of thin air. You wrote, "Your first paragraph say's 'unless we insulate per the prescriptive code the structure will perform poorly.' " But I never wrote that sentence — either in my first paragraph or any other paragraph.
According to my 2004 Supplement to the IECC, North Carolina has two climate zones. If, in fact, the local code differs from the IECC, or if a subsequent code change has modified the code to include 3 zones, then I appreciate the correction. I haven't had a chance to verify this yet.
If you want to pin me to the wall because a posting I made in response to a reader's comment used the term "illegal" with respect to R-20 Icynene in North Carolina — even though I never used the word "illegal" in that context in my article — that's fine with me. I'm happy to admit that my choice of wording in that response was not strictly accurate; by implication, the discussion was focused on the prescriptive code, and I got tired of writing the word "prescriptive" in each sentence. However, you are right that those following the performance code can get R-20 approved, meaning that R-20 ceiling insulation can be legal in North Carolina.
However, after countless postings and rambling accusations, this is a pretty weak branch on which to hang your objections to my reporting.
Nevertheless, consider this: your competitors are proudly installing R-38 ceiling insulation. Some of them are even installing R-60. Where do you want to be as an installer? Do you want to be fighting tooth and nail for the right to install R-20 ceiling insulation? Is this the proud legacy on which you want to build your company?
ResNet Memebership
Martin, just so you are clear in your mind. Being listed on the ResNet web site has nothing to do with being an active rater. You can call Steve Baden on confirm this if you woudl like. The listing on the ResNet web site is not a listing of raters who are in good standing but only those raters who have paid to be listed.
I am not obsessesd with comparing the worst performing insulations to another as you stated. I am trying to understand your thought process in your posting. Could you please provide answers to my questions.
Link Please
Martin your 2005 article "Every Failure Holds A Lesson" has mysteriously disappeared from the internet. Do have another link to access it?
https://www.greenbuildingadvisor.com/blogs/dept/musings/top-ten-news-stories-decade
Martin my my focus is on technologies that work. More importantly my focus is on satifying my clients. Have you ever attended a EEBA seminar "Houses that work"
"But the proof comes now in the results. I have a home in Virginia around the same square footage as my home here in North Carolina. The home in Virginia has standard insulation, and my heating bill there in December was $450. Here in North Carolina, my December heating bill was only $188. This is an exceptional product." Lou Panoe.
reponse to your post on 3/7/10 @ 4:07
Martin , below is your post on this day.
"If you are unlucky enough to have a house with loose-fill fiberglass insulation in your attic, you should hire a cellulose contractor to blow a cap of cellulose insulation on top of the fiberglass."
Please help me understand exactly how much cellulose should be installed over the top of the loose-fill fiberglass to improve performance. Given the density and weight of cellulose how much Rvalue is lost to the existing fiberglass by the compression from the weight of the cellulose? Given that we are trying to improve the performance by increasing the R-value in the attic don't we need to account for the decrease in Rvalue of the existing insulation. Wait, why do I need to add more cellulose on top. Doesn't each product has a tested Rvalue why not just add more fiberglass to increase the Rvalue of the assembly. Since higher Rvalue equals improved performance why not just add more loose fill fiber glass insulation to the assembly?
Try this link
Todd,
Try this link — it works for me:
http://docs.google.com/viewer?a=v&q=cache:oPC_MZHpBjMJ:showroompartners.com/spray_applied_foam/comfort_foam_closed_cell/download_brochures/2151.pdf+%22Every+Failure+Holds+A+Lesson%22&hl=en&gl=us&pid=bl&srcid=ADGEEShcSXq_o4i5bFUPkfEGL4z3uWJ7Y2gAFRTM881_tn3mZHBIdO2AmC0u755xxA3JBckuLH8NtwdeKU75iUGg1ZXLnSZvDlZiv2ZhMLhl4tyDiJdgONpocdJLiM291A1oPmtKm_rP&sig=AHIEtbRV42E4fVXFXVqymYwzYNTTK-xfQA
Capping with cellulose
Scott,
Energy Design Update reported extensively on the ORNL testing that showed that some types of loose-fill fiberglass insulation has a performance problem at very low temperatures (well below zero). If you want to learn more about the testing, find a good academic library and look up the following back issues of Energy Design Update — issues that contain over a dozen articles on the research and manufacturers' responses to the research:
EDU, May 1990
EDU, August 1990
EDU, February 1991
EDU, March 1991
EDU, July 1991
EDU, January 1992
EDU, February 1992
EDU, March 1992
EDU, December 1992
EDU, May 1993
As you can see, the research you refer to is two decades old. Blown-in-place fiberglass manufacturers have changed their products in the intervening 20 years to better address the problem of cold-climate convection, so the findings of the 1990 research are obsolete.
Concerning the question of capping loose-fill fiberglass with a layer of cellulose, the answer to your question is either "2 inches" — based on research by ORNL — or "as much as you can afford to install" (if R-value matters to you).
Here are the results of further ORNL testing, reported in the May 1993 issue of Energy Design Update:
"Researchers at Oak Ridge National Laboratory are exploring ways to prevent or fix the problem of air convection in low-density loose-fill attic insulation.
"Previous testing at Oak Ridge showed that low-density (0.5 pounds per cubic foot [lb/ft3]) loose-fill fiberglass suffers up to 50% loss of R-value at very cold attic temperature (-18°F) due to air convection within the insulation. However, laying fiberglass batts over the loose fill effectively stopped the convection problem. What if the low-density material was covered with higher-density loose fill instead of fiberglass batts?
"To answer that question, Oak Ridge scientists tried blowing both cellulose and 0.7 lb/ft3 fiberglass on top of low-density R-30 loose-fill fiberglass. The results were mixed: cellulose worked, fiberglass didn't.
"When approximately two inches of cellulose (R-8) were added over the R-30 low-density fiberglass, the measured overall R-value remained at R-38 down to -18°F, indicating that the cellulose covering effectively prevented convection.
"But the higher-density fiberglass apparently failed to stop convection at low temperatures. When an R-8 layer was added over the low-density material, it added R-8 to the overall R-value, but failed to restore the lost R-value due to convection.
"What about very high-density loose-fill fiberglass?
"Some loose-fill fiberglass products have installed densities even higher than the material tested in the most recent Oak Ridge tests. For example, Owens Corning's (OC) "Standard Blend" has an installed density just under 1.0 lb/ft3.
"The ability of a loose-fill insulation material to resist convection depends on its air permeability, which is strongly dependent on density (see EDU, April 1993). The higher the density, the better. David Yarbrough at Tennessee Technological University (TTU) has just completed a series of permeability measurements on several types of loose-fill insulation products. (Some of Yarbrough's results are reported in the April 1993 EDU.) Yarbrough told EDU that products like OC Standard Blend are most likely immune to convection. Further testing is necessary, however, to determine whether they would work as a retrofit fix over existing low-density products.
"For more information on the Oak Ridge tests, contact Ken Wilkes, Oak Ridge National Laboratory, Box 2008, Building 4508, Oak Ridge, TN 37831-6092; (615) 574-5931. For information on the TTU study, contact David Yarbrough, Department of Chemical Engineering, Tennessee Technological University, Cookeville, TN 38505; (615) 372-3494."
Capping with cellulose
Martin, so the research you have quoted showed a difference in the field tested performance of cellulose and fiberglass? That is the way I read it anyway, please let me know if you read the results differently. I hope by now we can agree the there is a difference between lab tested steady state tests and in the field tests as it relates to the performing Rvalue. Do you agree with this thought process?
R-value is defined by law
Scott,
A material's R-value is a material property. It's also possible (although less common) to measure an assembly R-value; building scientists, however, prefer to use U-factor for building assemblies, and to save R-value for materials measurements.
The R-value of a product (for example, a fiberglass batt) is measured in a lab according to ASTM standards and the Federal R-Value Rule. The R-value of that product is what it is.
The thermal performance of an insulation product varies widely, depending on the skill of the installer. Spray foam can be installed poorly; so can fiberglass batts. A poorly installed fiberglass batt has the same R-value it always had — the R-value that the manufacturer reports in its literature. It is the thermal performance of the fiberglass batt that varies widely, not its R-value. The thermal performance depends on the skill of the installer and the details of the building assembly.
RESNET raters
Scott,
You wrote, "Being listed on the ResNet web site has nothing to do with being an active rater. You can call Steve Baden on confirm this if you would like. The listing on the ResNet web site is not a listing of raters who are in good standing but only those raters who have paid to be listed."
So I decided to e-mail Steve Baden. Here's what he wrote: "Only RESNET rater members can call themselves RESNET raters. All other must call themselves certified home energy raters." So, according to Steve Baden, it would appear that your claim, "I am a senior Resnet rater," may need to be adjusted.
RESNET raters
What is your point Martin? I am certified to evaluate the energy performance of homes, does that make you feel better. Are you certified by anyone to evaluate the energy performance of homes? What can you tell us about your building scence credentials?
R-value is defined by law
Thanks for the repeat lesson Martin. Don't try and confuse the issue U-factor is the inverse of R-value. We are discussing the thermal resisance f heat transfer through an insualtion material. If you perfer to quote the U values of products we can do that do. The thermal performance of many products differ greatly even when they are installed properly. One of the studies you quoted came to that conclusion as well. Please go back and read my questions carefully and respond without changing the question before you answer.
Questions, questions
Scott,
I have been patiently answering your questions, and to extent that time allows, I will continue to try to do so.
1. "Martin, so the research you have quoted showed a difference in the field tested performance of cellulose and fiberglass?" Yes.
2. "I hope by now we can agree the there is a difference between lab tested steady state tests and in the field tests as it relates to the performing R-value. Do you agree with this thought process?"
No. "Performing R-value" has no technical meaning (although the phrase, and many similar phrases, is often used in advertising).
Questions, questions
Martin, since you have agreed that tests have shown a difference in field performance perhaps we can make some conclusion together. ASTM-C518 (the procedure used to determine R-values or the U-factor of an insulation) does determine the thermal resistance technically under steady state conditions.The question begs to be answered what should a homeowner pay more attention too or value more? The way an insulation performs in a controlled lab environment should be considered but more importantly how does the product perform when you install it in my house? Your own ORNL study showed up tp a 50% loss of the Rvalue tested performance when it was subjected to increased delta T temp. I cannot understand your position when considering all the relevant studies. A prescriptive Rvalue of an insulation material is only one of the areas that should be considered when we a designing a more energy efficient building. The premise of your article is that the Rvalues of insulation is the only factor in determining how well the house will actually perform. If we are trying to reduce the energy consumption of buildings we need to consider actual field component testing methods. If our houses where in a climate where the temp was constant the Rvalue test would be a better gauge of the true performance of the system. If you know that loose-fill fiber glass looses up to 50% of it's insulating power when exposed to cold temps why would you not considered this when making recommendations to improve a building. I guess if you are using loose-fill fiber glass, the rule of thumb is the old R38 is the new R19.
Please read what I have written
Scott,
You're making straw-man arguments — proposing ideas I never proposed, and then shooting them down.
"The premise of your article is that the R-values of insulation is the only factor in determining how well the house will actually perform." Nope. Never said that. Air leakage is even more important than the R-value of the insulation when it comes to thermal performance.
"If you know that loose-fill fiberglass looses up to 50% of it's insulating power when exposed to cold temps why would you not considered this when making recommendations to improve a building?" I do, Scott. That's why I never recommend the use of loose-fill fiberglass in an attic (and that's why I suggest you stop your obsession with the product.)
The type of blown-in-place fiberglass studied in the 20-year-old ORNL study that you are obsessed with is no longer on the market, in any case, so it's a moot point.
By the way, the number of hours that attics in North Carolina are actually at -18°F is close to zero, meaning that even if some fool could find some of that terrible loose-fill fiberglass tested by ORNL 20 years ago, the R-value degradation would rarely, if ever, occur.
Your qualifications
Martin, could you please list your building science qualifications for the readers?
No qualifications
Scott,
I have no qualifications. If you want to play the "I have more certifications than you do" game, I am happy to concede immediately. You win.
No qualifications
No need to play that game. My qualifications are limited compared to Dr.Joe, Dr.Craig Dewitt and many other PHD's that I read studies and opinions from. The difference between me and you is that I give advise to people based on their hard work, vast in field experience and real world applications of physics which is clearly something you are failing at. I have recently reviewed several new studies by BSC and the Institute for Research in Construction and the NAHB that ironically enough prove the 20 year old studies that you discount today still today have a lot of merit and are still applicable to the issue at hand. If you would just open your mind and stop promoting the cellulose industry you would actually gain some creditability despite your conceded lack of qualifications to discuss the topic.
BTW, it is 72 degrees here today so I guess my neighbors loose fill fiberglass R30 is actually able to reduce the heat transfer per the prescriptive test measurement of the insulation.
On another note have you ever reviewed testing that shows the R-value of cellulose reduces over time do the weight of the product. I have and it is not pretty for the owner.
Have you ever reviewed studies that show how the rvalue of cellulose can vary according to the installers mix settings? Not pretty for your argument either.
As with all blown in products that mix with air, over time the air is compressed out due to the weight of the product and that it is usually fluffed during installation to make it cover more area.
What does this mean to the homeowner?
After 3-5 years the new R38 is no longer an R38, many factors will determine the current R value. But we can say that when compression occurs and it will at some point, we no longer have an R38 in the attic.
Data are always relevant
Scott,
I never discount a research paper merely because it is old. Data are always relevant, and I am an avid consumer of research papers. I merely pointed out that manufacturers of blown-in-place fiberglass insulation have modified the products they sell, due in part to the ORNL research. That fact is relevant.
Many insulation products, including spray foam insulation, are tricky to install; in-field inspections and (where possible) monitoring studies of all types of insulation are extremely useful, and help installers learn how to do a better job.
Most cellulose installers are fully aware of the settling issue, and provide insulation depths that anticipate settling.
Every single available type of insulation has strengths and weaknesses — advatanges and disadvantages — including cellulose. Builders have to weigh these pluses and minuses when they specify insulation.
Even a casual review of my writing over the last decade will show that I have often championed the performance advantages of spray foam insulation.
If you re-read my article, you'll find I'm not attacking spray foam. I'm just advocating in favor of higher R-values. For a start, at a bare minimum, I advise builders to insist on the minimum R-values in the prescriptive code. Even better: exceed the code minimum.
In the long run, the insistence of Icynene and your spray-foam company that R-20 roof insulation is acceptable in Climate Zone 4 is more likely to damage the reputation of Icynene than enhance it.
Wow you made total sense with the last post
My point to you is that research shows that foam insulation provides greater energy savings in buildings compared to fiber glass and cellulose. Because foams like Icynene and Demilec address more than one method of heat flow, those benefits should be considered when judging the effectiveness of the envelop. A perfectly installed foam house in zone 3 and 4 with R20 in the roof deck, R13 walls and R19 floors with have lower heating and cooling cost than a fiberglass or cellulose house using R38 ceilings, R13 walls and R19 floors. This fact is not consistent with your opinion that all homes need to have R30 and R38 in zone 3 and 4 to be equivalent to the intent of the energy code.
Yes the prescriptive Rvalue code should be followed if you are only considering the Rvalue of component test as it relates to energy consumption. But there are ways to meet or exceed the prescriptive code using insulation products that are air barrier themselves.
What homeowners want is a lower power bill at the end of the day and their are many ways to do just that.
The R20 roof deck will perform just fine it's is not the first house to be done that way and show better results than the prescriptive code house built next door.
What?
Scott,
Your claim above sounds wacky to me.
The only way it could make sense is IF you assume that the "cellulose" house has a poor air control layer and IF the mechanical equipment and ductwork are in the attic.
Spray foam is NOT the only way to achieve a good air control layer.
Mechanical Equipment and ductwork should NEVER be placed in an unconditioned attic.
Thank you, John
John,
You're right, of course. This whole argument— which boils down to "an R-20 Icynene cap performs better than an R-38 cellulose cap" — is based on several skewed assumptions, including Icynene's apparent assumption that any builder who uses cellulose knows nothing about air barriers, and the assumption that people who use cellulose always install HVAC equipment and ductwork in their unconditioned attic.
These are pretty big assumptions! No research scientist would consider this comparison valid.
It's not wacky just the truth
I am sure the frustrating thing for you guys is that you cannot explain why one house with a foam envelop and with less total Rvalue performs better than the same size house next door using cellulose or fiber glass. I have studied and compared this for years in this field. There are no assumptions in my statement. The vast majority of homes in North an South Carolina are built with HVAC equipment in the attic or crawl spaces. Again there are hundreds of studies that show a foam house with less Rvalue out performs or uses less energy compared to the same house insulated with fiberous insulation. I have my own in the field results, or you can visit the BSC web site and review what Dr. Joe and his team have found as well.
What studies show
Scott,
Several studies have shown that on average, homes insulated with spray foam have lower levels of air leakage than homes insulated with fiberglass batts. The data on cellulose homes aren't quite as clear, although at least one New England study did show that on average, homes insulated with spray foam have somewhat lower air leakage rates than homes insulated with cellulose.
So, if you want to draw a conclusion, here it is: builders who pay no particular attention to air sealing will get better results from spray foam than from fiberglass batts.
However, Scott, the readers of this Web site are obsessed with air sealing, and are unlikely to be building leaky homes. If you compare a well-sealed home insulated with cellulose (including R-38 attic insulation) to an Icynene-insulated home with R-20 roof insulation, the cellulose home with R-38 will be the clear winner.
Finally, your argument still does not address the question of why anyone would want to stop at R-20 instead of installing R-38.
What studies show
Martin, I think it is pretty clear that foam by it self is more expensive than fiber glass or cellulose. Certainly every homeowner is or should be concerned with the cost benefits of adding additional levels of insulation and if the increase in the levels will provide a justified ROI during the life of the home. Doubling the amount of R installed does not at the end of the day provide for a twice the energy savings. However properly installing foam insulation at less than prescriptive code requirements will almost always provide a homeowner with lower energy cost than if they had built the home using conventional methods. I do realize this fact does not carry the same benefit across all climate zones. Think of it this way. If you need transportation and time is money, it is a wise purchase decision to buy a Ferrari that can go 180 MPH instead of a Ford Focus ? I would say not.
What drives you crazy is that a foam house with less rvalue on average performs better than a conventional fiber house. This does not sit well the premise of your argument.
"A conventional fiber house"
Scott,
No one is arguing in favor of a "conventional fiberglass-insulated house." If you read what I've written, I advocate that every single house be tested with a blower door. Many GBA readers are striving for 1.5 ach50, 1.0 ach50, or even 0.6 ach50. We're not in Kansas anymore, and we're way beyond stuffing 2x4 stud bays with R-11 batts.
Once your home with an R-20 ceiling is complete, the homeowners have to live with their energy bills until they get around to retrofitting their insulation to R-38 or R-60. That's a shame, because the opportunity for a better insulation job was lost when the builder made a short-sighted decision to install less than the minimum permissible insulation thickness under the prescriptive code.
A conventional fiber house
Martin, my customers are perfectly happy with their energy bills because their energy bills are lower than their previous house with less square footage. They are even more happy with their R20 foam roof deck because their energy cost are far less than their neighbors house which was insulated per the prescriptive code with fiberglass. My customers also appreciate that fact that I did not recommend the use of higher rvalues and more cost when those increases would not provide a reasonable return on the additional expense. I have documented homes that have a total monthly energy cost of .03 per square foot. Considering heating and cooling accounts for 40% to 55% (per all experts) of the total, there is not a lot of room for improvement to the envelop no matter how much more rvalue is added.
In addition, I wonder why you have chosen to single out Icynene on this issue. Installers of all brand of foams in my area recommend R20 in the roof deck.
If you really want to expose a real problem, why not write about the ridiculous claims solar panel companies make in reducing energy cost by installing solar DHW systems. Write about how our government is subsidizing 50% - 60% of the cost of these systems and how the tax payers are being ripped off.
"A conventional fiber house"
Martin,
I get your premise that a home's thermal envelop should only be allowed to comply with the prescriptive code and not the performance based code. It does not matter to you what the insulation type is only that the required R value is installed per the prescriptive code. The problem is prescriptive code does not mean better performance versus performance based code. Your premise is only your uneducated opinion and you know what they say about opinions.
Now for the truth
It is clear that Martin prescribes to what he wants to believe in his view of the world. What is very clear from Viktor's letter below is that Icynene in the configuration used and noted by Sophie does in fact comply with the code as Viktor notes in his first sentence. It;s amazing this was left out of Martin's version of the letter! Further more it can be easily proven that this configuration, R20 in a cathedral or unvented attic will out perform any house in this area using prescriptive r-values on a vented attic assembly. Martin in the future, being the fair and balanced journalist you are you might want to include the entire transcript of either letters you reference or discussions you have with people.... Given full disclosure Martin, please post the entire transcript authorized by Sophie. If we are to believe your version of the conversation, I’m sure you would have no problem producing this.
Viktor's letter:
Re: Thermal Performance of Icynene®
The International Energy Conservation Code, (Chapter 4), allows for the use of the
Performance approach in approving insulation thickness. Compliance with this chapter
requires an analysis of the annual energy usage.
Icynene engineering department has performed numerous energy analyses for new
construction and retrofit projects. Icynene uses REM/Design software developed by
Architectural Energy Corporation from Boulder, CO. Attached is their letter regarding the
code compliance capability of software.
Icynene® is a thermal insulation and an air barrier material. We provide improved energy
performance as a result of convective heat flow control. The air seal advantage of
Icynene® provides improved energy performance over much higher R-value insulations
that are air permeable.
When The Icynene Insulation System® is installed in accordance with manufacturer’s
installation instructions to a minimum thickness of 3 ½” and 5 ½” in roof/ceiling
application it will thermally perform equal or better then R-19 and R-30, respectively, with
mineral fiber insulation.
If you require further information please do not hesitate to contact the writer.
Yours truly,
Viktor M. Ginic, P. Eng.
Viktor Ginic's letter
Todd,
Thanks for sharing the complete version of Viktor Ginic's letter. When researching my article, I contacted Sophie Piesse, who was understandably reluctant to be drawn into a controversy. I quoted from the portion of the letter that she chose to share at that time. I also contacted Ed Reeves at Icynene, who verified the accuracy of the letter and who misinformed me concerning Icynene's position concerning the use of the letter for builders following the prescriptive code.
I'm glad that Sophie Piesse has now decided to share the entire letter, and I'm grateful to you for providing it.
Solar hot water
Scott,
You asked, "Why not write about the ridiculous claims solar panel companies make in reducing energy cost by installing solar DHW systems?" You can find my article on solar hot water here:
https://www.greenbuildingadvisor.com/blogs/dept/musings/solar-hot-water
Concerning overblown claims, see this blog:
https://www.greenbuildingadvisor.com/blogs/dept/musings/martin-s-useless-products-list
Solar Hot water
Martin, I have read the article you mention above and found it to be an informative dialog. My charge to you would be to write about why the fed and state gov'ts are subsidizing the cost of these systems. This is throwing good money after bad. If we want to address energy consumption of our buildings why is our gov't spending so much on a technology that only addresses a small fraction for the energy used in a home. People selling installing this systems love to use the subsidized cost of the systems instead of the actual cost. There is no money tree our there, it not free and we are all paying for this ridiculous subsidy.
Solar incentives
Scott,
Solar thermal incentives have the same drawbacks as photovoltaic incentives, which I wrote about in this blog:
https://www.greenbuildingadvisor.com/blogs/dept/musings/thinking-about-net-zero-energy
As I point out in that blog, "Many homeowners receive PV incentive payments, so they don’t have to pay for the true cost of their solar equipment. Tax-credit and rebate programs established by utilities, state governments, and the federal government shift a portion of these PV costs to utility ratepayers and taxpayers.
"While these subsidy programs are a financial boon to PV manufacturers and installers, it’s worth considering a few points:
— PV incentives disproportionately benefit middle-class and upper-class homeowners.
— By artificially lowering the cost of expensive technology, PV incentives warp investment decisions and draw money away from more logical investments like efficient appliances and improved ductwork.
— As long as the government neglects investments in low-hanging fruit — for example, by failing to enact improvements in residential energy codes — it makes little sense to invest in energy-efficiency measures that are demonstrably not cost-effective."
Come on down
Martin, please consider a road trip to North Carolina where I would be happy to assist you in evaluating the performance of a few foam houses that were completed in the last 2 years based on the performance based energy code. I can also bring you their neighbors houses that were completed based on the prescriptive rvalue for assemblies. Just let me know if you are up for the offer.
If I'm ever down your way...
Scott,
If I'm every down your way, I'll stop by for sure.
Bravo......
We found something we agree on, let's get the word out.
Recent study of interest
Martin, below is a link to a study that might be useful. I would appreiciate your commnets on the findings.
http://www.nrc-cnrc.gc.ca/obj/irc/doc/pubs/nrcc50847.pdf
Bravo?...What?
Scott,
I am confused....
Which comment or point Do you and Martin agree on?
Have you decided to see things Martin's way?
Bravo?....What?
We agree that Solar systems are not a viable option to reduce energy consumption in homes.
Agreement with Martin
John, as I and many others have out identified many times, Martin has misrepresented many if not all of the individuals and facts mentioned in his article.
It's frankly laughable for Martin to include/remember the vast majority of the contents of Viktor's letter based on a verbal conversation with Sophie but miss the first sentence where Viktor clearly states Icynene follows the performance path that Martin has agreed complies with the code, whereas in the article implies and elsewhere specifically says it was unlawful. It's certainly obvious that if someone includes in their article "signed by Victor", he in fact had the entire letter and purposely left out key portions to advance his position.
Secondly, what I do know about what Sophie told Martin is that he took out of context her conversation with him. What she also said is that she loves the unvented attic assembly and to this day highly recommends it's use using R20 over other materials in a unvented attic. She said she never had an issue with the builder or contractor as Martin suggest. Lastly, Sophie feels Martin was not trying to understand the situation, but tried to change her postion. In full disclosure, I did not speak directly with Sophie, but spoke with others who have about Martin's article. If I'm wrong or somehow misrepresented Spohie position then Martin should have no problem releasing the full transcript authorized by Sophie.
So John, is this the actions of a real journalist? It's clear that Martin and others from the EECC have a bone to pick with Icynene and others from the defeat of the EECC 30% solution. We all agree that Energy Efficiency must increase, but of the 7 proposals submitted to ICC in 2008 for consideration and debate, only one was adopted and it was not the one from EECC. Code should be ratified by consensus not by people using tactics like this!
We have proven through the last week that Martin did misrepresent the facts....
The letter
Todd,
I reprinted all of the letter available to me at the time I did my research. Sophie Piesse posted the letter I quoted. All of the wording of the letter came from Sophie's posting; a simple word search of our site will bring you to her original posting.
I'm glad you were able to obtain the entire letter — something unavailable to me. I can assure you that my quoting of the letter was entirely consistent with Sophie Piesse's post. I did not edit the portion of the letter which she shared. All you have do to is read her original post to see that my quote is entirely consistent with her posting.
As I've written many times, the information about the prescriptive path came from Ed Reeves, an Icynene employee.
I'm not sure why you continue to bend the facts. You just wrote, "She said she never had an issue with the builder or contractor as Martin suggest." There is nothing at all in anything I ever wrote that suggested that she had an issue with the builder or contractor. That is entirely your invention. Don't try to pin something on me I never wrote. (For the record, in her posting, this is what she wrote: "I was concerned about the Icynene thinness as well but then I received documentation and a letter from the company." In my blog, I wrote, "When Piesse questioned the contractor further, she was presented with a letter from Icynene." The idea of there being an "issue" with the contractor is something you made up out of whole cloth.)
The Post
Martin,
I conducted a "simple" search and found only the following. Can you direct me to the post you mentuon?
https://www.greenbuildingadvisor.com/search/node/Sophie
R-value myth
Martin, I think it's very clear from all the postings that R-value, while important has only a marginal impact on home performance once certain R-value levels are achieved. If you and John want to only base your argument on percentages then I believe you are doing your readers a tremendous injustice. From John’s post and one I agree with is Ufactor is a proper measurement of insulation performance, although Chris Mathis with EECC disagrees.
So….Martin, the premise of your article is that you are comparing R20 as the 100% value and R38 as the improvement value, right? A simple example of this would be a lumber yard last year sold 20 tons of lumber and this year sold 38 tons. That means a YOY improvement of 47% over last year. Martin and John, just using simple percentages, while more easily understood provides no merit to your argument; this is where I guess the “tent” comment comes from? R-value is essentially a marketing term used to help people understand that more R is better.
Technically, it should be expressed in decimal format or Ufactor as the ASTM test is done.
R20 = .05 Ufactor
R38 = .0263 Ufactor
.05 -.0263= .024 or 2%
BTW – this 2% of actual improvement is very much in line with Icynene and the SPFA’s analysis using Fourier's steady-state heat flow equation.
I look forward to your reply and frankly how in your "Understanding R-value" article you can claim the ASTM-518 test method considers convection in its prescriptive test? Please consider the ORNL research on loose-fill fiber in your response.
Post of January 28
Todd,
Here's the link:
https://www.greenbuildingadvisor.com/community/forum/green-building-techniques/16019/what-best-wall-construction-north-carolina?page=2
Check out her post of January 28.
Convection
Todd,
The ASTM 518 test measures convection effects at the temperatures at which the test is conducted. It does not measure convection effects at -18°F. Many building scientists — including, most recently, Joseph Lstiburek — have proposed different testing protocols for R-value, including protocols that test insulation performance under a wider range of temperature conditions than current tests.
Stay tuned; it's always possible that ASTM will eventually adopt testing protocols that include performance of insulation at very cold temperatures. However, it's unlikely that many North Carolina homeowners care about insulation performance at -18°F.
U-factors and R-values
Todd,
It's not clear what your chart proves:
R-20 = .05 U-factor
R-38 = .0263 U-factor
.05 -.0263= .024 or 2%
I'm with you for the first two lines. Clearly R-38 allows only about half the heat flow as does R-20. So far, so good.
When we're talking percentages, however, I have to ask what you are comparing to. If the minimum ceiling assembly according to prescriptive code is R-38 (and I know that thermal bridging through framing members affects assembly R-value or U-factor, but for the sake of this discussion let's assume we're talking about an R-38 assembly), than an R-20 assembly is only 52% as effective as an R-38 assembly at limiting heat flow. I'm comparing the R-20 assembly to the R-38 assembly.
The only way you can minimize the difference between these two assemblies -- and achieve your 2% result, which implies that Icynene is wonderful -- is to introduce a new assembly: a tent. Compared to a tent, R-20 does a pretty good job of insulating. But why do you insist on comparing the performance of your insulation to a tent instead of a code-minimum house?
TRY THIS
Scott and Todd,
I am a little surprised that you are having such a hard time understanding what Martin is trying to teach you.
I thought that one of you was an Energy Rater?
Surely you could experiment with your software and see that increasing R-value continues to reduce heat flow and reduce the energy required for heating and cooling.
Try it... upgrade from R20 to R38 and see what happens.
I think you are confusing the cost of installing R-value with the performance of R-value.
There IS a diminishing return on DOLLARS invested to achieve higher R-value.
Because the spray foam strategy is SO costly ... the break point is falling BELOW code minimum R-value standards!
If you do not care to use the Remrate software... you could also try this simple Heat Loss Calculator
http://www.builditsolar.com/References/Calculators/HeatLoss/HeatLoss.htm
What happens when you double the ceiling R-value from R20 to R40?
Is it a 2% improvement in ceiling heat loss performance or a 50% improvement?
2% is pure BS
I hesitate to jump back into the fray, but...
Todd, you can't subtract two u-factors and call that a percentage!
.05 - .0263 = .0237 This is not a percentage!
Instead, divide the 0237 difference by .05 and you get 47%, just as before (e.g., R38 has 47% less heat flow than R20), or the other way around: .0237 / .0263 = 90% (e.g., R20 has 90% more heat flow than R38). U-value is just the inverse of R-value, but you already knew that. The 2% argument is pure BS.
When comparing two homes with R38 and R20 encapsulated attics, my point all along is that because the attic is a buffer zone, it would be incorrect to say the ceiling load increases by 47% when reducing the roof from R38 to R20. That's the key issue that John, Martin and others seem to be missing. Foam's inherent performance advantage is not the real issue here, because as Martin and others point out, similar performance can be achieved by other means, often at a lower cost (foam manufacturers and dealers never tell you that). However, rigid or sprayed foam is the only practical alternative for insulating the roof deck.
So if 47% does not accurate represent the increased ceiling loads, then what is? Unfortunately, there's no way to directly calculate this value. It requires a complex time-series analysis (buffer zones create significant lag), further complicated by interactions with ducts and HVAC equipment. To my knowledge, no one has developed an appropriate software model for this. I have developed my own conservative modeling technique that allows me to make reasonable judgments.
As I stated previously, the argument for using less roof deck insulation for unvented attics is mostly an A/C issue, and thus applies in cooling dominated climates such as Carrboro (where I once lived, btw). On the other hand, an encapsulated attic can actually work against you in a heating dominated climate, especially in areas with cold and relatively sunny winters. This is because it reduces the beneficial radiant heat gain that would otherwise occur with a vented attic. It's hard to say where (geographically) the trade offsets the benefit.
David Butler
optimalbuilding.com
Plenty of modern homes have cathedral ceilings
David, Todd, and Scott,
Plenty of modern homes all over the country have cathedral ceilings that are insulated and finished. Insulating between the rafters is not limited to semi-conditioned attics containing HVAC equipment. Sloping roofs are often insulated because that's where the ceiling is. Think of A-frame buildings, Capes with finished 2nd floors, and modern houses with sloped ceilings.
Moreover, it's not true that cathedral ceilings must be insulated with spray foam. Here in Vermont, builders often install sturdy panels to create a ventilation chute, and then install foil-faced polyiso at the bottom of the rafters, and then install dense-packed cellulose between the polyiso and the ventilation chutes. Strapping and gypsum wall board finish the job.
So you guys are just muddying the waters by pretending that my article has anything to do with a comparison between vented unconditioned attics and unvented conditioned attics. I never addressed the issue.
Cathedral ceilings?
Marin, why introduce catheral ceilings into this debate? In my previous comment where I said "rigid or sprayed foam is the only practical alternative for insulating the roof deck", I thought it was clear from the context that I was referring to encapsulated attics. As you point out, cathedral ceilings can be insulated with fiber-based products. Also, they don't create a meaningful buffer zone.
Your last paragraph is spot on, but please don't associate me ("you guys") with that! Indeed, I think part of the reason this debate has gone on for so long is that Todd/Scott are comparing an R20 unvented attic with a conventionally built vented attic. I don't think many would disagree with this, at least in hot climates (although I've questioned whether unvented is cost effective in homes with very high pitched roofs).
On the other hand, you (and others) are saying an R38 (or R30) encapsulated attic is somehow automatically worthwhile compared to reduced R-values for encapsulated attics.
As I previously stated, due to the buffering effect, one cannot say that R38 on the roof will reduce the ceiling load by 47%, compared to R20 on the roof. Let me try to put some numbers on this.
I believe the reduction in *peak* loading on the ceiling is more likely closer to 20% or 30%. For example, with 100F outside and 75F inside, an R20 encapsulated attic might reach 85F in late afternoon (based on lots of anecdotal reports). If you increase the deck to R38, the ceiling loads are only reduced by 2 or 3 degrees, which represents 20% to 30% of the 10F delta-t at R20. The seasonal impact on ceiling is less than 20% to 30% (more so with buffer zones than with low-mass non-buffered assemblies). And we haven't yet factored in the approximately insulation value of the ceiling itself on an already low delta-t (approx R-1.5 with 5/8" drywall and air layers). And don't forget that the ceiling load is only a small portion of the overall thermal load of the building, which is usually dominated by windows in southern climates. This is clearly an issue of diminishing returns. You'd rather put your money where it buys the greatest energy savings.
Having said all of that, it always better to put ducts inside conditioned space, in which case an encapsulated attic is unlikely to every be cost effective, compared to the alternative -- properly air sealing the ceiling and beefing up the ceiling insulation.
David Butler
optimalbuilding.com
Encapsulated attics
David,
Why do you think that "you (and others) are saying an R38 (or R30) encapsulated attic is somehow automatically worthwhile ..." Where did I raise the issue of encapsulated attics?
Ceiling insulation can go lots of places -- attic ceilings, attic floors, or sloped cathedral ceilings. As I read the prescriptive code, the minimum R-value for ceiling insulation, wherever your ceiling happens to be located, is R-38 in Carrboro. Moreover, R-20 performs worse than R-38. Let's leave a discussion of encapsulated attics for another blog, OK?
About insulating roof decks
David,
By the way, why do you think that "rigid or sprayed foam is the only practical alternative for insulating the roof deck"? What prevents you from insulating it with dense-packed cellulose blown between a ventilation channel and polyiso, as I described?
Compare
Here you go John
The measurement of conductive heat flow resistance is made using the guarded hotbox apparatus. This test procedure (ASTM C-518-02) measures the thermal conductivity of insulation material. In this test, one side of the specimen is heated to a specific temperature and after steady state heat flow has been reached, the temperature on the opposite side is measured. Through this temperature measurement the R-value is calculated. The outside surface of the test apparatus and the specimen is sealed and insulated to minimize the heat loss through the edge and eliminate the effects of any convection or radiant heat flow. This measurement solely defines the conductive heat flow resistance of the insulation material, the R-value.
Once the R-value of an insulation material is determined, the heat flow through it can be calculated using Fourier’s steady-state heat flow equation.
Q = A x ΔT
_________
R
Where:
Q = Rate of heat flow, BTU/hr
A = Area, ft2
ΔT = Temperature differential, ° F
R = Resistance to heat flow, hr.ft2 ° F/BTU
This equation is used to calculate the benefit of increasing the thickness of any type of insulation as long as there is no air movement (convective heat transfer) through the insulation.
As an example, consider 1000 ft2 of insulated area with a temperature differential of 40°F. Let us include the outside air film at R-0.2 and the inside air film at R-0.7. The total R-value before the application of any insulation is 0.9. Increasing the insulation thickness by 1” increments at R-3.6/inch provides the variuos heat flow rates and the improvement from R-20 to R-38 will show only a 2% improvement.
I have conducted REM calcs using R20 and R38 and will send as soon as I figure out how to post a image on this blog.
Unvented attic - why all the fuss
I reason the issue of encapsulated attics can up is because THIS is the assembly Sophie was asking about. This points out the issue with your article and frankly the code, as the code does not take new technologies, like the unvented attic into consideration it only focuses on R-value which we all know, I hope is based on a faulty test procedure at a mean temp of 75 degrees.... How many walls, attics and floor do you know only reach a temp of 75 degrees?
Encapsulated attics
Martin,
Can you provide a cost breakdown, material and labor for the dense pack cellulose, baffle and poltiso board you mention? Also, what is the % decrease in proformance one you expect from field based issues related to improper detail based on typical labor used today in the field?. Lastly, how does this comply with R804.6 or does it need to?
How many houses have you been in
Martin says:
"Most cellulose installers are fully aware of the settling issue, and provide insulation depths that anticipate settling."
Now that is funny! How many attics have you been in Martin!
What!
John,
If you want to go after most all home builders in the vast majority of the US and insists that all HAVC systems be installed in another place than attic....good luck! Yes you also may want to also talk to the vast majority of the homeowners and explain why they should use valuable and yes taxable conditioned space to host a HAVC system....LOL!
It works!
Martin,
My first post to you provided a link to a 8 year study of a house in Florida using a R22 foam unvented attic, http://www.baihp.org/data/CFRes/index.htm. You quickly discounted its effectiveness in a climate zone equal to Vermont.....not sure how we got from North Carolina to Vermont...but that's fine. You may want to provide the BIN data from central Florida, to Carraboro NC to somewhere in Vermont to help yourself.
Please provide me a link to a 8 year study in climate zones 2-4 where a 4,200 sq ft house can effectively operate on 3 tons of HAVC using R38 or hell R whatever you want in a vented attic using cellulose - btw and the hard part is you cannot change anything else other than R-value in the attic.
Cost question
Todd,
"Can you provide a cost breakdown, material and labor for the dense pack cellulose, baffle and polyiso board you mention?"
Costs will vary, and I don't have cost information at my fingertips. Either spray foam insulation or cellulose and polyiso can be used. If I were building a new house, I would cost out both alternatives and choose whichever is cheaper. To be fair, of course, you have to compare R-38 to R-38.
Concerning the Florida study
Todd,
In the south, where a surprising number of builders install HVAC equipment and ducts in unconditioned attics, many homeowners suffer from the poor performance and high energy bills associated with these badly designed systems. The article that you linked to lists the advantages of cathedralizing an attic containing HVAC equipment and ducts.
I couldn't agree more: If you're going to put the equipment and ducts up there, then for goodness' sake, insulate the roof.
This is a great solution to a persistent problem. And the relevance is....?
Florida Study
Great we agree on one more item....
Martin, In speaking with a number of builders from across the country, I believe the "HVAC" in the attic is much more prevalent than you might think.
The relevance of the unvented attic is again this was the assembly Sophie was referring to.
Is Fourier Wrong?
The measurement of conductive heat flow resistance is made using the guarded hotbox apparatus. This test procedure (ASTM C-518-02) measures the thermal conductivity of insulation material. In this test, one side of the specimen is heated to a specific temperature and after steady state heat flow has been reached, the temperature on the opposite side is measured. Through this temperature measurement the R-value is calculated. The outside surface of the test apparatus and the specimen is sealed and insulated to minimize the heat loss through the edge and eliminate the effects of any convection or radiant heat flow. This measurement solely defines the conductive heat flow resistance of the insulation material, the R-value.
Once the R-value of an insulation material is determined, the heat flow through it can be calculated using Fourier’s steady-state heat flow equation.
Q = A x ΔT
_________
R
Where:
Q = Rate of heat flow, BTU/hr
A = Area, ft2
ΔT = Temperature differential, ° F
R = Resistance to heat flow, hr.ft2 ° F/BTU
This equation is used to calculate the benefit of increasing the thickness of any type of insulation as long as there is no air movement (convective heat transfer) through the insulation.
As an example, consider 1000 ft2 of insulated area with a temperature differential of 40°F. Let us include the outside air film at R-0.2 and the inside air film at R-0.7. The total R-value before the application of any insulation is 0.9. Increasing the insulation thickness by 1” increments at R-3.6/inch provides the variuos heat flow rates and the improvement from R-20 to R-38 will show only a 2% improvement.
I think you are sincere
Scott & Todd,
I think you are sincere about your zest for spray foam.
I know that convincing builder's to move the ducts and air handlers into conditioned space is going to be a hard sell.
I remember the resistance to seat belts by the auto industry and the public.
If you guys can convince Builders and homeowners to spend $14,000 to upgrade to spray foam on a 5,900 sf project....(see page 30)
http://www.homeenergyexpo.com/images/Nichols.pdf
Then I say there is a good chance that builders could also be convinced to invest in an alternate air barrier strategy AND install MORE than code minimum R-value instead of LESS than code minimum.
I realize that you can not post any attachments here at GBA...but I would still like to merely see your results(HERS index) and (Normalized, Modified End-Use Loads) from upgrading the spray foam in one of your projects from R20 to R38.
Please also report the size of the home and the window area and assume both homes achieved the same blower door results(3 ACH50 or less)
Fourier Example
Scott and Todd,
the "Fourier Example" that you keep bringing up is the same as the TENT analogy.
At the very least you should be comparing your projects to code minimum projects NOT TENTS
Tent
John,
The "tent" comment initially came from Martin, not me.
Can you answer the question below?
Fourier law illustrates a 2% improvement in heat flow between R-20 and R-38? Right or Wrong?
John, below is a summary of a Rem analysis between R-20 foam, R-38 foam (vaulted as described by Sophie in Martin's article) and R-38 Fiberglass (vented)...
The 2 ½ story house has 4 bedrooms, 4,222 sq ft, and open crawl space. House is located in Durham, NC in climate zone 4A. This illustrates as Martin suggests that using R-20 was not "unlawful". Now, I do realize the EECC, a group you and Martin may follow would like to eliminate performance path, but the below illustrates the issues with their argument.
Option 1:
R20 attic (vaulted) Icynene, R13 walls Icynene and R20 floors Icynene, .10 ACH NAT
- Heating load = 32.4 (kBtu/hr)
- Cooling load = 29.7 (kBtu/hr)
Option 2:
R-38 attic (vaulted) Icynene, R13 walls Icynene and R20 floors, .10 NAT
- Heating load = 30.3 (kBtu/hr)
- Cooling load = 28.1 (kBtu/hr)
Option 3:
R-38 attic (vented) Fiberglass, R13 walls Fiberglass and R20 floors Fiberglass, .55 ACH NAT (
- Heating load = 43.2 (kBtu/hr)
- Cooling load = 40.8 (kBtu/hr)
When we increased the Icynene roof insulation from R-20 to R-38 (90% increase), the heating and cooling load decreased 6.5% and 5.4%, respectively. I would have thought a 90% improvement in R-value would have provided different results. So much for percentages....
Finally, some numbers
Todd,
Thanks for confirming that switching from R-38 ceiling insulation to R-20 ceiling insulation increases a homeowner's heating bill by 6.9%. If a homeowner were convinced to downgrade the wall insulation as well -- a tactic recommended in Viktor's letter -- then the homeowner's heating bill would be even higher.
Obviously, the fiberglass comparison only works if you assume that the builder installing fiberglass insulation ignores air sealing measures. That introduces a new variable into the equation.
Finally, "Fourier law illustrates a 2% improvement in heat flow between R-20 and R-38? Right or Wrong?" That one's easy: wrong. The heat flow through an R-38 assembly will be only 52.6% as much as (that is, will be 47.4% less than) the heat flow through an R-20 assembly.
Thank You Todd
What was the HERS index and window area for the 3 options?
I think you are sincere
Sorry I must have missed you at this HUD conference in 2006 at York Technical College! Can you answer my question about Fourier? Second request.....
A couple of comments John:
- The actual upgrade cost for this home would have come in at $9,500 if we consider the elements initially specified by the builder were taken out (i.e. HAVC tonnage, reduced SEER from18 to 14, framing normally required in bonus over garage, venting products and more) Yes the "client" was very happy not to mention that they added additional 375 sq ft of additional space in the attic area a few years later and did not need to add another HAVC unit or additional insulation. Given the added area the total cost of the improvement on this house using Icynene was a little over $4,000. Now if we look at cost of acquisition vs. operation I believe the client has been cash flow positive for over 4 years...not such a bad deal! BTW, it was the homeowner who decided to use Icynene, not the builder. If we look additional costs for air sealing, thermal ply etc. to achieve the performance we are seeing with THIS house the story gets even better.
Lou Pone - Homeowner
"But the proof comes now in the results. I have a home in Virginia around the same square footage as my home here in North Carolina. The home in Virginia has standard insulation, and my heating bill there in December was $450. Here in North Carolina, my December heating bill was only $188. This is an exceptional product.
- In the over 1,300 projects we have been involved in "no" house has ever had a blower door above 1.4 ACH NAT, using Icynene and many were below .1 ACH NAT.
- Yes, we have many pics of air sealing typical in this country by Energy Star raters - amazing what you find!
John, I read some of your earlier postings in reference to Martin's article and it's clear that you are no fan of the spray foam industry, at least that is how I read it with the way you reference or imply a salesman was consulting with Sophie. What you and Martin will find is that those who choose to spray foam, especially Demilec and Icynene Dealers are much more aware and educated on home performance issues than the vast majority of conventional insulators in the US and many of the "Energy Experts" My conclusion of this is these folks have actually been involved in projects and see results.
Proof that spray foam has vastly improved performance qualities over fibrous materials is the growing popularity in the entry by conventional insulation firms such as CertainTeed, Johns Manville and Guardian. Who knows one day we may see a pink foam!
John, this may be surprising to you but we do install other materials other than foam. In addition we value engineer homes to make the best use of these materials based on budget and payback.
John, do you remember a few years back when EStar was going to require full fill cavities under floors of bonus rooms over garages when using fibrous materials and after a lot of lobbying by NAIMA, A EECC member Estar backed off....You take about hypocrisy....
Finally, some numbers
Martin in Fourier's analysis already considers R-value. His math illustrates the actual improvement after R-value is determined......
R13 was used because this is the prescriptive code for NC zone 4A - I thought we are comparing a prescriptive home to a performance based home? I guess I missed something. If you read the full letter I sent, Viktor said in his first sentence he was following the performance path, either way he is still correct. So to you it makes sense to install R-18 more material to save how much on heating costs....in a area just on the edge of climate zone 4? I think there are better areas in a home to spend money then on R18 more spray foam and our over 1,000 of our clients would agree...
I think you have already stated that the path Viktor was refering to his his letter was not "unlawful" right? All theree of the homes in the REM I sent meets or exceeds NC 2009 ECC....right?
Right, they are all lawful alternatives
Todd,
They are all lawful alternatives, but the house with the R-20 ceiling has heating bills 6.9% higher than the house with the R-38 ceiling. And it's quite possible that an R-38 cellulose ceiling will be cheaper than an R-20 Icynene ceiling. That would be ironic -- to pay extra for insulation and end up with a higher heating bill.
John Brooks - Is this you?
http://johnbrooksbuilder.com/articles/fox59.htm
We don't install R-20 Ceilings
John, we do not use R-20 Icynene on ceilings.....so I would never know the answer to your question.
Recent study of interest
Martin, have you had a chance to review the study I mentioned in a previous post ?
Mar 12, 2010
10:33 AM EST Recent study of interest
by Scott Nichols
Martin, below is a link to a study that might be useful. I would appreiciate your commnets on the findings.
http://www.nrc-cnrc.gc.ca/obj/irc/doc/pubs/nrcc50847.pdf
Wall energy rating
Scott,
I read it quickly, and determined that the WER (wall energy rating) is a proposed metric for measuring wall thermal performance in a way that takes into account R-value and air leakage.
I can see where this proposed metric might be useful. Joe Lstiburek is working along similar lines, although he's had a lot of trouble setting up his lab equipment and making measurements.
Todd's questions
Todd,
I am another John Brooks... not the one you linked
I did not attend the HUD conference that you mentioned.
As to the Fourier Question... I thought Martin already answered it well.
I agree with Martin
Did you have any other questions for me?
My question for you is about the HERS index and the window area of your examples?
I do not have anything against spray foam homes other than the high cost that limits the R-value.
I live in a spray foam home myself...
I did however specify better than code R-value and I would have gone for more R-value if foam were not so expensive.
Fourier
Thanks John,
I'm fine with both your and Martin's feedback on this topic, that is what you believe and I respect that. Your readers can decide to believe each of you or Fourier.....
John, I'm also glad you decided to install prescriptive Icynene even though the analysis shows the additional costs provided you very little return.
John, I'll get back with you Tuesday or Wednesday with the HERS scores and window to glass ratios...I need to run to a meeting.
One more thing...and a few more questions
There may also be a limit to how much spray foam can be applied and still meet fire and safety concerns.
I have been getting answers all over the place and have yet to get a clear answer from a foam supplier or a Building Official.
Todd and Scott,
Is there a limit on how thick you can apply open cell foam at the roof deck?
What is the thickest you have applied?
Have you ever installed a fire retarder coating?
How much more does the coating cost?
One more thing
I would suggest to you the following:
- Visit the ICC ES site and search by manufacturer - this will provide you with the ESR reports and the various thicknesses they have decided to test to. This has little to do with the max they could spray, but is what they decided to test.
- The governing document for spray foam is called AC-377
- The current test procedure is called NFPA 286 and NFPA 286 (modified) will be required by AC-377 January of 2011
- Several mfgs have already passed the NFPA (modified) test to be left uncovered
- Other tests that several mfgs have also run includes ASTM D 1929. Thus far a few foams have shown that the spontaneous ignition temp at 1004 degrees F with a flash ignition of 824 degrees F. This compares to wood at 500 degrees F. I guess we should choose another building material besides wood or require all wood be coated with a fire proof coating.
- I would suggest you join the SPFA to educate yourself on what the industry is doing. You just missed the last convention held in Florida several weeks ago.
- If you would like to compare foam fire safety to cellulose you may want to read the document from NAIMA....not a pretty picture for cellulose on fire safety and other issues they identify.
- The max thickness we have installed is 7" in climate zone 5. This was the thickness needed to meet/exceed the dew point calculation, per the code under R806.4
- We install coatings as required by the various ESR reports
- Icynene has tested to provide ZERO fuel source to a fire...How about that newspaper insulation after 4-5 seasons of wetting by RH.....any testing you know of on fuel source contribution or it's ignition temps?
.
I should not have changed the subject
Todd,
Sorry about changing the subject....I realized as soon as I posted that I should not have.
I appreciate your feedback.
I am more interested in the HERS index and window area in your example.
I thought that these numbers were easily read from the REM/Rate report.
REM Analysis
Hello John,
As Viktor mentioned in his letter he used REM/Design, so to be consistent we did as well. REM/Design as you know is often used as a modeling tool by many Energy Professionals and is also accepted by many code jurisdictions to prove performance path compliance. REM/Rate is as you know used to certify homes for Energy Star and does provide a HERS score.
Given this if you would like to calculate the HERS score using REM/Rate for the three options you are welcome to do so. The issue as you know is that most if not all homeowners and builders with correlating a HERS score to actual energy usage. Given that, I have provide for you below the average energy usage for the three options. The .55 ACH NAT was used for the fiberglass home as this is the published average ACH determined by the NAHB Research Center. I know many of Martin's friends at EECC once worked for the NAHB Research Center, so I thought it relevant to use their numbers.
Data:
The total windows area is 398 sq ft, so the window-to-floor area ratio is 0.085
Average Monthly Energy Bill:
Option 1 - Icynene R-20 (vaulted), R13 walls and R-20 floor over vented crawl - $211.00
Option 2 - Icynene R-38 (vaulted), R13 walls and R-20 floor over vented crawl - $209.00
Option 3 - Fiberglass R-38 (vented attic), R13 walls and R-20 floor over vented crawl - $272.00
I hope this answers you question. If you run a cash flow analysis of an improvement costs of $6,500, assuming the R-20 (vaulted) Icynene home vs. the R-38 fiberglass home with a $63 a month delta and assuming a 6% APR what do you come up with?
HERS index vs. actual energy consumption
John,
After thinking about your request of a HERS score. I have attached an e-mail from a past client to provide more context on my point that the HERS index does not necessarily translate to energy consumption. Dave, my client sent me this e-mail a few days after I met with him to deliver his Estar docs.
"Todd:
To answer your question about our rates. Our home is 5,100 s.f. The maximum monthly KWH we've used since last November is 2,600. The minimum is 553. Our bills since January have been:
JAN $220
FEB $158
MAR $120
APR $116
MAY $81
JUN $173
JUL $229
AUG $186
AVERAGE = $160 PER MONTH
I think our average bill is a bit lower than what you had thought it would be. The Icynene must be working!
We do use Duke Energy and I called them today. We've been billed at a higher rate than we should since they didn't know we had an EnergyStar rated home. So we'll now benefit from the slightly reduced rate."
Dave
This house is a "Florida" style home with a 8/12 pitch roof and 25" ceilings at the main entry.
Affiliations
John,
Since Martin was so focused on Scott and I and our affiliations, would it be possible for you and Martin to provide a history of your professional accomplishments/certifications and any industry lobbying group each of you may be affiliated with?
Still no qualifications
Todd,
As I explained when Scott asked me the same question, I have no qualifications. If you want to compare who has more professional certifications, I am happy and eager to concede immediately. You win.
I have never joined any industry groups or engaged in lobbying. I am a journalist.
About my friends
Todd,
You wrote, "I know many of Martin's friends at EECC." Who are they? I guess I should tell you to say hi to them, but I don't know who they are. What does EECC stand for?
Wall energy rating
Martin, I thought you might dismiss a real study that shows the actual performance of fibrous insulation wall assemblies. Should we not consider more recent test's like this one will determine the performance of the assembly rather than just the component rvalue?
Martin the Journalist
Martin, Martin Martin - you actually wrote about this....do we really need to review your less than honest version of what actually occurred at the 2008 ICC meeting in Minneapolis?
"At the 2008 Minneapolis hearings, a more sweeping code change proposal — the so-called Thirty Percent Solution — was defeated after vigorous opposition from representatives from the National Association of Home Builders (NAHB), Icynene Incorporated, and Pilkington Glass. The Thirty Percent Solution was supported by a wide coalition of organizations, including the U.S. Department of Energy, the U.S. Conference of Mayors, the National Association of State Energy Officials and the Energy Efficient Codes Coalition."
I would assume you where aware of the Energy Efficient Coalition, or EECC since you included them in your article....LOL!
Facts from this meeting you failed to report are numerous. Martin, you should apply at the NY Times before they go bankrupt from their ever decreasing readership, you'll fit right in!
Do you REALLY want to go there, Martin?
Sorry - Correction EECC
I meant the Energy Efficient Codes Coalition, EECC.
http://thirtypercentsolution.com/
I wasn't in Minneapolis
Todd,
Like many journalists, I report on news events that I don't participate in. Although I interviewed people who were there, I was not at the meeting in Minneapolis, nor do I have (as far as I know) friends at the EECC.
I'm not sure what your point is, Todd. You're taking up a tremendous amount of time and space, and throwing a variety of left-field accusations at me that I'm doing my best to respond to. If you have information about the meeting in Minneapolis that you want to share, or any information that contradicts my reporting, feel free to share your facts. Otherwise, some of your suggestions — for example, suggestions that I should be fired, or that my qualifications need to be defended, or that I have the wrong friends — are less helpful than sticking to facts.
Upgrade cost from R20 to R38 $
Todd,
I am merely an Architect from North Texas with lots of questions.
I do not belong to any Lobby Groups.
My only brush with fame was having my personal home published in Fine Homebuilding Magazine(Annual Issue).
I sincerely appreciate your feedback.
I do not have Rem/Rate software but I assumed that was what you were using.
If you are curious why I asked about window area and HERS index... it is because I am trying to get an idea if the home that you were modeling was a "just barely code home" or near Energy Star level.
I really wish we could post attachments here at GBA because I would like to see all of the parameters from your example home.
Since you called it a 2-1/2 story home I assume that there is not much roof area compared to floor area?
What was the roof area?
Total wall area?
First floor area?
Is this a home that has been built or just an example?
8.5% window area does sound very frugal on the window area.
The Energy Star Reference House is 18% window area.
I would never suggest that anyone build a leaky (0.55 ACH Nat) house with fiberglass insulation.
I am curious what the upgrade $ charge would be in your example house to increase the Icynene from R20 to R38?
I wasn't in Minneapolis
Martin,
I will post my final comments soon. You are correct I'm not a journalist and as you can tell from my writing skills, I never will be! LOL.
I do believe this website provides a tremendous service and over the past weeks I have read a number of your past articles. I believe that you believe you are doing the right thing when you bring up these issues to the forefront and I agree they do. However, I also believe you need to take MUCH more care in your articles to better represent all the facts and present other positions that may not be 100% in line with your views of the world, this is what a journalist does. If a lay person reads many of your articles, your bias is apparent. For example, in the Minneapolis meeting you would be surprised that Icynene, a member of the ABC in fact joined in the proposal of the DOE. This fact was clearly not resented in your article. There were 7 proposals submitted to the ICC technical staff and the EECC version was not approved, the DOE/ABC proposal was and not because the members were at the bar or sleeping, it was because the merits of the proposal. BTW, some of EECC's proposals elements were identical to the DOE/ABC.
What I am is a person who is very concerned when someone writes about a topic with clear bias or does not fully represent all the facts.
Getting back to your article, the facts presented from the REM/Design I provided and Viktor iniatally presented, clearly shows increasing R-value does NOT provide a measurable savings for the homwowner. $2 a month difference is not worth the time of day or advances the debate. Would you agree?
Upgrade costs
John, I know you would like for me to spend more time on this, but my friend hopefully you know I'm really trying to stay focused on Martin's article. The REM/Design clearly illustrates the premise of Martin's article was incorrect. Option 1 and Option 2 - R-20 vs. R-38 foam clearly illustrates this point with only a $2 a month savings. This also illustrates that if you used an R-30 foam in your home in a vaulted assembly, you wasted your money. I'm sure you could have found a much better way to spend that money other than a $1-$2 monthly savings. If I increase the window to wall ratio, the savings or lack thereof would be the same, if we only consider insulation R-value...I'm sure you can see this! Option 1 and 2 are identical with the only difference being R-value in the vaulted assembly. If you do not believe me, please purchase REM/Design and run your own analysis. Given that you are an architect this tool will allow you to model you to model your designs for your clients, a service I know they would see value in. We have done this numerous times for builders, homeowners and architects as they decide where to best spend their "energy saving dollars". John, you could have purchased a number of licenses of REM/Design and REM/ Rate with the money you spent or wasted on R-30 foam for your home! Now you have to agree that was funny! LOL!
Square feet of roof area and cost to upgrade?
Todd,
What was your example roof square footage and how much would you charge a builder to upgrade the roof deck foam from R20 to R38?
I stand by my reporting
Todd,
My reporting on the 2008 IECC meeting in Minneapolis was accurate. According to Bill Fay, the executive director of the Energy Efficient Codes Coalition, "Icynene didn't support any pro-energy-efficiency proposal at all in Minneapolis. Gabe Farkas from Icynene was there. He not only spoke against the Thirty Percent Solution — our proposed package — he also stood up and said the whole concept of a package was wrong. Later, when the elements of the package were voted on individually, Icynene didn't support a single one of the 21 components of the package — in fact they spoke against most of them."
Your description of the ABC joining in support of a DOE proposal did not occur in Minneapolis in 2008. That was an entirely different meeting — in late October 2009 in Baltimore. While Icynene's belated decision to stop lobbying against a more stringent energy code is to be applauded, there's no need to erase the historical record and give them credit for good behavior in Minneapolis.
I stand by my reporting
It appears there are different facts from different people.
Cost to upgrade
John, not sure the relevance of your question as the facts of the REm/Deign I sent proves that Martin's artilce is off base. The option 1 vs, option two proves it make no sense to upgrade to R38 or R30 in this applciation. Foam can range from .26-.36 per board ft at 1" for open cell and .90-1.10 per board ft for closed. There are also many hybrid foams....i.e. Icynene MDR-200 r-vale per inch at 5.0 and is water blown.
Is Icynene an insulation or a cult?
Just how much BS (that's not building science) can the foam fetishists dish out?
For those who insist on credentials: I have been a pioneer in super-insulated design and construction for 30 years, have earned national efficiency awards for my homes, and teach and consult on building science and hygro-thermal engineering.
So let me address some of the nonsense:
1) Loose-fill attic cellulose settling is a non-issue, since the FTC R-value rule requires advertised R-values to be for settled density (just as rigid foam board must be rated at aged R-value).
2) Attic cellulose settles to about 1.4 pcf, depending on depth. Dense pack in closed cavities is at a minimum of 3 pcf which offers R3.8/inch, so any slight increase in attic density over time actually increases the R/inch value.
3) As another avid reader of building science and lab and field study reports, I've seen nothing to even suggest that an R-20 foam attic can perform anywhere near an R-38 fiber-insulated attic with equivalent air sealing (which, by the way, would violate all laws of physics). Post the links, rather than simply asserting the impossible (or the deliberately distorted, such as comparing foam to the worst fiberglass installations).
4) It appears endemic to Icynene and other foam propagandists that they have no grasp of basic math (I also teach Math for Builders). The above-claimed 2% improvement of R-38 over R-20 (which has already been addressed) is either utter ignorance or complete fraudulence. I lean toward the latter, since this is typical of the Icynene product propaganda showing alleged diminishing returns for increased R-value.
Not only is R-38 a 47.4% improvement (or reduction in conductive thermal transfer) square foot for square foot, but R-38 in a flat ceiling that significantly interrupts thermal bridging through the ceiling framing is 166% more thermally efficient than R-20 foam sprayed between 2x8 rafters 16" oc on a 12:12 roof (common here in New England) which has 140% of the surface area of the flat ceiling.
In other words, all other things being equal (good air control layer, e.g.) the R-20 unvented roof has 2.66 times the heat loss of the R-38 flat ceiling.
Additionally, in cold country there would be ice dam problems with the unvented under-insulated "hot roof", unwanted radiant heat gain in summer, decreased life of composition roofing materials, and the potential for dramatically diminished durability in the event (inevitable at some time in the life of the house) of a roof leak.
What's particularly irksome is that the foam propagandists on this thread not only display a stunning ignorance of building science and basic math, but attack those that do as uninformed and wrong-headed.
A cult backed by the facts
Our company has won numerous awards from the GBC for our work and education on energy efficient design. In 2007 three homes that won awards from the GBC in Charlotte for sustainability and energy efficiency and we were involved in all three and yes ALL three used R20 foam in the deck.
If someone can tell my how to post or send the complete REM/Design files presented, you can then see for yourself with all things equal, besides R-value the sample house with R-38 (option 2) only had a $2 a month savings. At this point, Randy you can direct your questions to the engineers of this program.
Randy, I would read the link Scott attached....being the academic you are I'm hopeful you can explain the results as no one else has been able to.
Lastly, see the 8 year old field study by the DOE I posted and explain that while your at it...
"Additionally, in cold country there would be ice dam problems with the unvented under-insulated "hot roof", unwanted radiant heat gain in summer, decreased life of composition roofing materials, and the potential for dramatically diminished durability in the event (inevitable at some time in the life of the house) of a roof leak."
A properly installed unvented attic has proven to eliminate ice damming in colder climates, since you are in New England you may want to talk to Dr. Joe and visit Anderson Insulation in Boston to walk you through a few homes. Dr. Joe and his staff as well as others have research papers that you should educate yourself on before making comments like the above. These papers are backed-up by field studies vs. classroom theories. The shingle question is also one Dr. Joe can answer for you, and yes give CertainTeed a call while your at it. The data provided from the DOE study in Florida also provides useful data. Dr. Craig Dewitt of Clemson University has also written several papers on the "so called shingle issue" raised by the non believers, and no he is not a member of the cult. As far as the roof leak question, water will come directly through open cell foams, this has been proven in ICC approved lab testing.
Randy, come to the dark side!
Yes... I made a mistake
Scott/Todd,
Yes..... I feel foolish for upgrading the foam on my personal home beyond code minimum.
It was NOT a wise choice of funds.
But I am learning.....
Next time .. I will invest my money in a good (non-foam) air control layer and then probably double the code minimum R-value.
I think we all can learn something from the Vermont guys.....
I think that David Butler made some good comments as well.
Options
John,
I do not disagree with you at all. If you have a ranch home in Austin with no R-8 HAVC duct exposed to the 130+ degree summer attic temps and effective detail on the air barrier assembly you can have achieve reasonable performance. However, I would use foam to seal the top plates for each room below from the attic.
Vermont boyz
John,
There is no doudt there are a lot of great ideas out there! One item many people seen to miss is the cost to provide the "air control layer" in the field and make this a very reptable process. If we all were to pay attention to the detail that you, Martin and many others talk about we can make great strides in home performacne. The reality is however, we cannot build a "porche" in the field with the labor costs builders and homeowners are willing to pay and make this a repeatable process. Foam, installed correctly and trust me it's not as hard as has been descibed on this site, inherently solves many of these problems. So, going back to one of initial posts the "cost" of compliance" vs. makes foam very repeatable and very cost effective.
While I know Martin and others have addressed the "air control layer" on this site in great detail the facts in the field are very different from their view of the world. It appears that many on this site will do what ever they can to not use foam...that is frankly unfortunate.....as the facts show otherwise.
I'm a fan of spray foam
If anyone cares, I'm a fan of spray foam. It's a great way to improve the airtightness of building assemblies.
Given my usual caveat -- try to exceed minimum code R-value requirements for the best performance -- I have often recommended spray foam and will continue to do so.
I'm a fan of spray foam
Martin, I'm a fan of cellulose....and my caveat is given the detail and costs required to get cellulose to perform in a repeatable manner in the field, across all climate zones, in all assemblies is not worth all of the other issues associated with this product i.e. having to leave a wet blown wall uncovered for days (up to 30 days according to NAIMA) to properly dry....my opinion for what it is worth is the R-value debate is not worthy.
Many technologies will come onto the market in the near future and if our building codes solely focus on the myth of R-value as a path to home performance our population will not be well served!
I know cellulsoe has inproved over the years, but just last week we actially had to "chissle" the settled cellulsoe out of a home as over the years the wetting of the material caused it to become almost "brick" hard.
Is Icynene an insulation or a cult?
Robert, the facts are clear, increasing component rvalues does not equal actual reduction in energy consumption. REM/Rate, REM/Design and Energy Gauge do not provide the us with accurate predictable energy consumption for a home to be built or even after it is built. Because the only measure we have to predict the energy consumption is mostly based on steady state rvalues. With an unvented attic assembly i.e. foam roof deck we are not able to model or predict the benefits of enclosing the attic. This assembly provides three main benefits in the South that are not available with vented attics.
1. The HVAC is now in semi-conditioned space where the temperature in the attic is always < than 85 degrees compared to 135+ for the vented attic. Please remember we all do not build or live in the NE. This benefits the HVAC up to 20% (according to DOE and others) by decreasing the TAR (temperature at register). Why is this benefit not considered or measured ? Just because our tools do not take this into consideration does not mean the benefits are not there.
2. Current modeling tools do not take into consideration the added insulation value of the free insulation (air space between the roof deck and the interior ceiling air barrier) that is automatically provided when using a foam unvented roof deck assembly. Again, we know the air is an insulator but yet our current modeling tools DO NOT give us credit for something we know exists.
3. Lastly, know should not assume air barrier details and sealing technical are completed correctly because it is almost always not done correctly. The folks weighing in on this subject seem to think everyone builds the same way in which they do. Again, this is not the case in the real world.
Again it drives you crazy why a foam home insulated with less rvalue across the envelop performs better than a home of typical construction insulated with fibrous materials. Just so you don't go crazy I will give you the answer.
YOU MUST consider all of the forces at work, it is not all about the rvalue.
Structural Sheathing Air Control Layer
Scott,
Thank you for changing the tone of this discussion.
I think there is an air control strategy currently practiced in the Northeast that could work well in almost all climates.
Builders are achieving Passivhaus airtightness levels (0.6 ACH50) by using structural sheathing as the Air Control Layer.
I think this strategy can be easily learned and REPEATED by folks with conventional construction skills.
Isn't More Better?
Martin, wow, lots of posts here with many interesting points of view.
If I follow your statement that R-38 is 47% better than R-20 and technical, yes it is, then why not use R-72. After all, R-72 is 47% better than R-38. Or better yet, shouldn't we use R-135 because that is 47% better that R-72.
Where does it end? Honestly, if your point is that we should use R-38 over R-20 because it is 47% better then it applies to even higher R-values.
From what I've read here, it seems to me that the big difference of the two sides is the starting point. Martin, your starting point is R-20 in the roof and that does give you 47% better performance for that one assembly. But does that really tell the whole story? Where is the starting point? R-20 blocks 95% of heat flow. R-38 blocks 97.4%. How do we measure this difference?
For most of my customers, heat loads and BTU's are meaningless. But they sure do understand $$$. Energy auditors typically use software that calculates payback for any energy upgrade. Think of an EEM. Let's not forget that the Mortgage industry started much of the standards for energy efficiency. Thus, unless we equate our energy efficient recommendations to real dollars, it's useless to the consumer.
Most people are more interested in a value rather than pure energy efficiency. How should we define "value?" In this case, it's the acceptable payback period. Some may think 7 to 15 years. Others 20 or even 30 years. Heck, my mortgage is 30 years. The payback for upgrading from R-20 to R-38 with Icynene LD-R-50 is over 50 years. When this long of a payback period is considered, wouldn't you agree, Icynene LD-C-50 installed on the underside of a roof deck at R-20 is in most cases a better value than R-38? And without any doubt, it's a better value than R-72 or R-135?
Of course we have to consider cost
Kevin,
You're right: upgrading from R-20 Icynene to R-38 Icynene is expensive. That's a marketing problem for Icynene -- and it's a major reason why many builders prefer to install R-38 cellulose. Compared to R-38 cellulose, R-38 Icynene just can't compete.
Icynene's solution to the high cost of their product is to advocate R-20 ceilings and roofs. Well, that's one approach. The only problem is that the homeowner isn't getting R-38 anymore.
Listen, a strong argument can be made in much of the country (although perhaps not in North Carolina) to justify R-60 insulation for new construction. But the prescriptive code in NC calls for R-38 ceilings. I'm sure plenty of NC builders manage to meet the prescriptive code easily with cellulose insulation, just as builders in Vermont do routinely.
If Icynene is having trouble competing, it's due to the high cost of their product -- not to the fact that homeowners wouldn't benefit from R-38.
But you're right -- if you're selling a very expensive insulation product, it's hard to convince homeowners to install code-minimum levels of insulation. In fact it may not be cost-effective -- which is why cellulose begins to look like a much better deal.
Lipstick on cellulose
Kevin and Scott.
All good stuff. I really thought we were getting somewhere with Martin. But I think based on Martin's latest post, we've taken a number of steps back.
MARTIN, you are obviously a big fan of cellulose and I of any product that actually works, not just when it's installed but for the life of that structure. This is very timely in that I just met a client today that installed 2 feet of cellulose in his attic in 2005, new construction. He marked the depth on the wall and NOW, low and behold the cellulose has settled more than 8". I would post the pics if I could.
Now Martin, based on all your experience and after reading all of those studies what R-value do we have now?
Did anyone but me notice that Martin has never addressed the issues pointed out by NAIMA and that I have raised about his favorite product?
I do not care are, how much lipstick your put on a pig, it's still a pig!
Thermal Imaging
Martin,
When you visit North Carolina, I will take you to a few homes that installed cellulose and with our thermal camera you can see for yourself the settling issue of cellulose.....a picture is worth a thousand words. I hope you then post these images on your site!
Air barrier
John,
I installed 1/2" foam board on the exterior of my home built in 2008 and based on the HERS score and my energy bills it was a big waste of money vs similarly sized homes where we only installed foam.
As Scott has said repeatedly, I know it's hard for Martin and others to understand how the r-value argument does not hold up in the real world vs the academic one Martin lives in. Martin as you have said on numerous occasions of those who disagree with you, you are in fact the person misleading your readers and the public. The facts prove this no matter now much lipstick you put on it.
I think you missed my point
R-20 with 1/2lb foam is not code minimum. It's much better than code under the performance method. If a foam insulation contractor is installing under the perscriptive method then he is making a huge mistake. I am an Icynene dealer. have been for 11 years. I was the first to use the performance method. I showed the crew at Icynene how I did it. so I guess you can blame me.
If I understand you correctly, you are implying that R-38 of cellulose performs the same as R-38 of foam. The problem is that I just don't see the numbers to support that finding. Before becoming an Icynene dealer, I was a builder. I used wet spray cellulose and blown. I ran into moisture issues and problems with attacheing drywall to rafters that had been netted and dense packed. I got into the foam business because no one would come to spray my homes.
Well, to get to the point, I have found through a decade of field work and testing that I can take any home that uses cellulose and redesign it with foam getting 20-30% lower energy bills with lower R-values. I've never installed Icynene by the perscriptive code...not once in 11 years. My company has insulated the parts of the US Capital building and many many multi-million dollar homes. One recently was 37,000SF. Owner of the redskins, former head of fannie mae. The point is that these people have the money to afford anything they want. These projects also have engineers designing the HVAC systems. And yes, we only installed 5.5" of Icynene to the underside of the roof deck.
Here is my take on it. It's not about the perscriptive codes it's about maximizing perfomance while maintaining a value. You can take out my R-20 Icynene and replace it with the same cost in cellulose, maybe that will be R-120 or something like that, but the R-20 Icynene will still have the lower bills. you may be spectical of my claim but it's true.
About 10 years ago we sprayed a home for a customer and we installed R-15 under his roof deck. Well, he had a geo-thermal HP. In the winter during cold spells, his resistant heat came on. the HVAC contractor came out with an thermal camera and quit honestly said that not only it wasn't enough insulation but that our install was less that quality. First off, I knew he didn't know what he was talking about and second, he didn't know how to us a thermal camera, lol. but either way I know I would get the last laugh. I sent my crew out and sprayed another 4" of foam bringing the R-value up to R-30 and all of this at my own expense. The next winter guess what happened? The exact same thing. Resistant heat came on like clock work. The problem ended up being the ground loop size and the ground temps were driven down to the point of not being able to get enough heat from the ground. That HVAC company never made it right. But that customer is now a builder and we do all his work. We actually have about 30 homes with only R-15 in the roof. Not my first choice but those builders were on a budget. We don't offer that package anymore but it did work well. I hope you are not pulling your hair out too much from hearing that.
Bottom line...
You can't compare a product that works to a product that doesn't.
Kevin, you've gone too far
Kevin, I appreciate your comment on pg 2 of this blog, and if you've read my comments, you know I support the performance approach (prescriptive codes are a rather blunt enforcement mechanism), and you know I have no philosophical issue with specifying less than "code" for roofs over encapsulated attics. But I take exception to your claim that you can take any home that uses cellulose and reduce energy bills by 20% to 30% by using foam at lower R-values. Presumably that claim would extend to fiberglass insulated homes as well?
I can give you several examples of fiberglass or combination fiberglass/cellulose insulated homes in CZ3 that use less than 1.5 kWh/sf for heating/cooling (all electric), which works out to approximately 1/3rd of total energy use. These are actual, and not modeled costs. Two of these homes belong(ed) to me.
Unless spray foam can reduce hot water, lighting and miscellaneous loads, I'm not sure how you can trim 20% to 30% off the energy bill when the HVAC only makes up one third. Certainly not with less than code R-values. Perhaps you meant that you can save 20% to 30% of *HVAC* energy?
This sort of loose and careless claim is what gives the home performance industry a black eye. If you really meant what you said, then you're simply ignoring that similar performance can be achieved with less expensive techniques.
In particular, the homes I referred to earlier typically have advanced framing, standard R19 fiberglass batts done right, continuous exterior foam (EIFS), vented attics with R38 (all ducts inside), engineered overhangs, and conventional air sealing . Granted, this approach entails an additional hassle factor the builder, but once the crews get over the initial learning curve, the incremental cost is less than foam. Foam is easier, but not necessarily the most cost effective approach.
More Disinformation
Scott,
Nobody argues that, if you make the design error of installing HVAC in an attic, there is an energy benefit of insulating the roof deck. But there is no energy benefit from the air space in an attic, since it's not a dead space but full of convective currents.
And nobody assumes that conventionally-built housing has good air barrier detailing. The only way that an Icynene house looks good is compared (as everyone in the industry does) to the worst case: fiberglass insulation and poor detailing. Just as the "diminishing return" argument that's repeated ad nauseum and ad absurdum is based on an uninsulated house as a baseline.
it's also not at all difficult to model the effects of quality detailing. I use my own spreadsheets and they offer accurate predictions of real energy consumption. Of course it's not just about R-value. It's also about hygric performance, and indoor air quality, and toxicity of materials, and environmental impacts, and the local and broader economic and cultural ramifications for the occupants, their community and the world at large.
On all those levels, petrochemical foams fail miserably. And even on a simple hygrothermal performance basis, it can't compete with natural materials.
Todd's Lipstick-Enhanced Pig
The only "pig" in this trough is NAIMA and the Icynene industry, both of which have consistently relied on deliberately misleading and often factually incorrect statements, charts, graphs and claims, including attacks against more environmentally and cost-effective solutions to thermal and hygric issues.
What the performance method shows
Kevin,
You wrote, "R-20 with 1/2 lb foam is ... much better than code under the performance method." You're exhibiting a misunderstanding of the performance method. The performance method does not change the credit given to a certain thickness of insulation. Under the performance method, R-20 insulation is still R-20 insulation.
All the performance method allows one to do is come up with a whole-house heating and cooling budget based on the totality of information entered on the house in question: its presumed infiltration rate, the number and size and orientation of the windows, and the U-factors of the walls and ceiling.
For example, if a house has few windows and the windows have good specs, it's easier to get away with R-20 ceiling insulation than in a house with many windows with worse specs.
Todd, I'm sorry to hear that you have cellulose installers in N.C. who either fail to anticipate settling or who deliberately mislead customers. I have seen such cases in Vermont (although the settling was to a level about 2 or 3 inches below specs, not 8 inches). The remedy is to call back the cellulose contractor and insist that more cellulose be installed to comply with specs. I did this once on a school insulation job.
Reputable cellulose dealers in Vermont know all about settling. There are charts on every bag of cellulose that show the recommended installed thickness to achieve the desired settled thickness. After a few callbacks, rookie cellulose installers realize their reputation is on the line, and they usually get religion.
Eventually, I hope the cellulose installers in N.C. will learn the same lessons. As I'm sure you know, there are examples of installers who fail to comply with specs with every insulation type. Plenty of spray foam installers have been called back to sites where the installed spray foam thickness did not match minimum specs.
Read the study Martin
R-20 insulation is not R-20 insulation Martin. You fail put any amount of time in trying to understand the thermal dynamics of various materials, not just foam. For example, there is a new technology invented in RTP (Research Triangle Park) NC that has been proven to perform better than spray foam with less R-value. Martin, in the world you, Robert and John live in new technology would not be allowed, that is really sad! If you are truly a "Green Advisor" open your eyes and get off this 50 year+ old test that has been proven time and time again to be false using a mean temp of 75 degrees. Martin, it really does not take much money to run a true test....just take spray foam, cellulose and fiberglass and place a heat lamp under them and then inform all of us in a time lapse every ten minutes the heat flow through these materials AND read the Canadian study Scott posted and then get back with us. If you truly are a journalist you say you are I would assume this would peak your interest....that is unless you REALLY do not want to know the facts!
NASA
Tell me Martin, being the investigative journalist you are. What does NASA us to insulate our space craft, cellulose, fiberglass...I think not! Let us know what R-value and material they use and if they use cellulose or fiberglass now much cabin space would be left for the crew members?
On R-value and space vehicles
Todd,
R-20 is indeed R-20, because the R-value of insulation is defined by law (the federal R-value Rule). Of course, as many of us have repeated again and again, R-value is not the only metric to consider when designing a house -- it's just one datum.
The heat-lamp test beloved of radiant barrier manufacturers -- a side-by-side test performed in a glass terrarium at many trade-show booths -- does not represent typical heat flow through building assemblies, since it exaggerates radiant effects. However, good software like REM/Rate or PHPP does a good job of modeling heat flow through building assemblies.
I'm happy to concede that closed-cell spray polyurethane foam is a great insulation for NASA to use on spacecraft, where weight is a primary concern. Cellulose would be ridiculous on a space vehicle.
However, my home does not need to escape gravity and reach orbit. It's staying put, so the weight of cellulose in my attic won't be a problem.
You have introduced the "Buckminster Fuller fallacy" into this discussion. Buckminster was in love with geodesic domes because of their light weight. Eventually, however, someone pointed out that it really doesn't matter how much a house weighs. Adobe homes make perfect sense in some climates, but I wouldn't want to try to launch one into space.
better than code
no, sorry Martin. I'm not misunderstanding the performance code. R-20 with lower air infiltration performs better that prescriptive R-values with prescriptive air infiltration. The problem is that the code and energy calculation software enters air infiltration as if it magically appears. But we all know that's not how it happens.
I can see that no matter what, you are refusing to see this in a real world view. Bottom line is that the R-value stated on non-air barrier insulation is a LIE!!! It's one of the biggest scams in the building business. The metrics is wrong. How can a company sell a product knowing it's not being installed to perform the same as it does in a laboratory?
Stop thinking in R and start thinking in $.
About lies
Kevin,
No, I'm sorry: you're wrong about R-value. It's simply untrue that the "bottom line is that the R-value stated on non-air barrier insulation is a LIE."
R-value labels are closely regulated by the Federal R-Value Rule. While I have investigated and reported occasional violations of the R-value rule — typical offenders are distributors of radiant barrier products, bubble-wrap insulation, and "insulating" paint — these offenses are not typical of national insulation manufacturers.
You can rest assured that the R-values shown on the labels of fiberglass batts from major manufacturers are accurate and fully comply with the R-value Rule.
Of course, any builder who ignores the need for air sealing is likely to be unhappy with the thermal performance of the home's insulation. It's also clear that spray polyurethane foam does an excellent job of air sealing — at least in the framing bays where it is installed. (Other areas -- for example, between bottom plates and subfloors -- must still be addressed with other products.)
Many, many builders have achieved remarkably low air infiltration rates -- including 0.6 ach50, the Passivhaus standard -- without any spray polyurethane foam.
Passivhaus standard
In Martin's world whatever works in Vermont works everywhere. The concept Martin speaks of was developed in Germany, which is typically a cooler climate than that of the NE US.
One of the homes we were involved with and won an award from the GBC is a passive house. Since 2007 we have worked directly with the homeowner to document the actual energy costs. What the homeowner has identified is the highest energy costs are from Mid December thru early March - quite a contrast from what the passive proponents would expect. As the homeowner has said "what a big waste of money"!
Again all of you who follow this blog must understand the narrow view of Martin's world, one that is only based on what he reads and chooses to follow. If Martin was a journalist vs. an activist of those he follows he would present information very differently; in Robert's world I guess this would be called Martin's cult. If you read many of the posts you will easily see Martin rarely "really" answers a direct question and rarely responds directly to a questions when it is not in his favor. As I have said time and time again, this is NOT the actions of a journalist.
Martin, you say in past posts that REM/Design is a great tool for modeling. Please send me an e-mail; since you found my website I'm sure you can find our e-email address on it. I will then send you the REM files you can post them on your site for all to see. We can then have a debate on the results of those REM files and your misleading article that R38 somehow saves the world from those evil foam people.
My e-mail address
Todd,
Feel free to contact me:
martin [at] greenbuildingadvisor [dot] com
E-mail sent
OK Martin, you now have the REM files... I look forward to your r-value debate based on their contents....I assume you still to view REM/Design as a reliable tool that does not exaggerate the views of those evil foam people.
Reviewing the REM/Rate reports
Todd,
Thanks for sharing the REM/Rate reports. After reviewing them, this is what I noticed:
-- The rater assumed that fiberglass-insulated homes have an air infiltration rate of 0.55 ACT(nat), while the Icynene-insulated homes have an air infiltration rate of only 0.10 ACH(nat). While it is certainly true that many fiberglass-insulated homes are that leaky, such sloppy construction practices are not recommended, and many fiberglass-insulated homes achieve better air sealing results.
These differences in air infiltration rates account for the bulk of the reported differences in heating and cooling loads.
-- The reports show that a house with R-20 Icynene in the ceiling has heating bills that are 11.6% higher than a house with R-38 Icynene in the ceiling. While the difference in heating bills in the mild N.C. climate -- especially now, when fuel costs are low -- is only $53 a year, the burden of higher fuel costs for an R-20 insulated ceiling will be much higher in colder climates and when fuel costs rise.
The clear savings in heating bills resulting from an increase in the ceiling insulation from R-20 to R-38 explain why code officials have set the prescriptive requirements at R-38 in N.C. Obviously, an 11.6% increase in heating bills is significant when considering the fuel that will be consumed by millions of new homes that will be built over the next few years. Let's hope that few builders are tempted to downgrade to R-20.
Review of REM/Design - not REM/Rate files
I was hopeful Martin would use this information to provide his readers with all the facts. But once again, he has disappointed. I think this is the example of what many of us have been saying for a long time. If anyone were to read many of Martin’s postings and past articles and then investigate the issue themselves, you will find on numerous occasions where Martin either twists the facts or misrepresents the facts. Well he has done it again!
Most professionals know the REM/Design does not truly consider the performance of the unvented attic, but that is not the real debate here. Either way, I choose to show real numbers vs. Martin's choice to pick out pieces of data that only shows a narrow view of the facts in Martin’s world. The topic of Martin’s article was R20 – R38 foam insulation in an unvented attic and how Icynene was hurting the industry and homeowners by not promoting prescriptive R-values.
A small view into what we have established through all of the terrific input is:
1) Martin initially said the use of R-20 was “unlawful” his words not mine and then said that it was in compliance with the NC ECC code use performance path compliance.
2) Martin told us that Carrboro was in climate zone 3 and there are 3 climate zones in NC, again false.
3) Martin John and maybe Robert are fans of cellulose, but none of them have ever published the well known issues, as identified by NAIMA with this product...I wonder why? Martin, what is the water absorption rate of cellulose and how does this affect its performance over time...Please answer the questions.
4) Martin has informed us that he is a journalist with no industry credentials.
5) Martin, without the full contents of Viktor’s letter came to a conclusion that Icynene was saying it was in compliance with prescriptive requirements. We all know now the full contents of Viktor’s letter and Martin’s characterization of Viktor’s letter/intent was false. To Martin’s defense he referenced what was posted by Sophie. But a non-journalist, like me was easily able to get the full letter, a task I would have thought a journalist would have investigated.....
6) Martin references a phone conversation with Ed Reeves of Icynene. Now based on all of the other factual mistakes uncovered, how can Martin’s readers really believe his version of that conversation....?
7) We have established that Martin believes REM/Design is a great modeling tool....I assume he has a copy and uses it on a regular basis?
8) I think what we have tried to explain to Martin is that homeowners do not care about R-value or the misleading percentages that explain them or that the test for R-value is inherently flawed. What they do want to know is what will it cost them to operate their home and what is the payback on any investment. Martin, a really good topic for your next article!
9) I provided to Martin three REM files for him to hopefully post for all to see. Once again Martin did not disappoint. He represented only a small fraction of what is illustrated in this analysis. Is anyone surprised?
Three REM/Design configurations were sent to Martin:
- R20 – R38 foam homes (unvented) with the only changing variable r-value. ACH etc all stayed the same. This is the exact configuration Sophie posted.
Conclusion: The operating cost difference between the R20 and R38 foam house for the full year on a monthly basis is $4 or 2.4%. Martin only wants to show half of the story or a percentage he likes...I wonder why?
Let’s forget about foam for just a minute and focus solely on the position of Martin, John and Robert....this gets good! The next REM/Design paints a very sobering picture! Remember, Martin said himself REM/Design was a good tool for this analysis.
- R30 fiber home (vented attic) compared to a R42 fiber home (vented attic). Again the only changing variable was R-value and in this case as Martin likes to say (A 40% INCREASE)!!!!
Conclusion: The comparison from a R30 fiber to R42 fiber home; adding 12 more R or a 40% increase shows the difference in operating costs on a monthly basis of $2 or .7%. Martin did not mention this? I wonder why as this is at the heart of his article! What is really funny is the EECC and all of its supporters are spending all of this lobbying money and time to increase r-values for the cost of 1 cup of coffee each month. Now you talk about misleading!
- R38 fiber home (vented) compared to a R42 fiber home (vented). Again the only changing variable was R-value and in this case as Martin likes to say (A 10% INCREASE)!!!!
Conclusion: The comparison from a R38 fiber to R42 fiber home; adding 4 more R or a 10% increase shows the difference in operating costs on a monthly basis of less than $1 or .2%. Martin did not mention this? I wonder why?
I guess the summary of the posts is that once gain Martin failed to provide information that was not in line with his narrative or thought process. Wonder why? Martin if you are to be believable PLEASE post the REM files for all to see......
Image #2
Image #3
Repeated accusations already addressed
Todd,
Repeating false accusations that I have already addressed does not bolster your case.
1) I never said that R-20 was unlawful. A simple review of my writing shows that.
2) I have consistently written that N.C. has two climate zones on the IECC climate map and that Carrboro is in climate zone 4. If you have any evidence to contradict those facts, please present it.
3) I am happy to concede that cellulose, like Icynene, is able to absorb and hold water.
4) You are correct that I am a journalist with no industry credentials.
5) Todd, I have already thanked you for making the full text of Viktor Ginic's letter available, since I was only able to reprint the portion shared by Sohpie Piesse at the time my blog was written. I will take this opportunity to thank you for a second time.
6) I can assure you that my report of my conversation with Ed Reeves was accurate. Mr. Reeves has not contacted me to contradict my report.
7) Yes, I believe that REM/Rate does a good job of modeling energy use.
8) "I think what we have tried to explain to Martin is that homeowners do not care about R-value or the misleading percentages that explain them or that the test for R-value is inherently flawed. What they do want to know is what will it cost them to operate their home and what is the payback on any investment." You are right that many homeowners don't care about R-value. It's also true that not all homeowners care about their energy bills. Homeowners are all over the map on these issues.
9) You have criticized me for not loading all three photos as I was in the process of loading them. It's hard to share photos on this site, and I apologize for the low resolution of the images. All three are now loaded.
Post to a URL
Thanks Martin for the attempt to post ths REM files. However, the posts are unreadable. Can you create a link to a URL that allows the full .PDF's to be viewed by your readrers?
Links
Todd,
http://picasaweb.google.com/101225087026240837992/REMRateReports#
http://picasaweb.google.com/101225087026240837992/REMRateReports2#
http://picasaweb.google.com/101225087026240837992/REMRateReports3#
WOW
Did anyone notice that Martin did not address the essence of the discussion on this post i.e. R30 vs. R42 (40% improvement) and the savings to the homeowner....I did!
I need to run now but will address the rest of Martin's response once I return.
Martin, you can easily post the .pdf's I sent to your site and then provide a URL for all to review them. If you do not know now to do this, I would contact your webmaster for help, that is if you want your readers to see all the facts.
Martin wrote:
Todd,
Martin wrote:
Todd,
Repeating false accusations that I have already addressed does not bolster your case.
1) I never said that R-20 was unlawful. A simple review of my writing shows that.
Your words from your past post: “In other words from your post, it's significantly worse than the minimum ceiling allowed by law.”
Martin, it’s clear to me and from any finder of fact that you mean this to be unlawful or illegal if anything other than R-38 is installed in climate zone 4.
2) I have consistently written that N.C. has two climate zones on the IECC climate map and that Carrboro is in climate zone 4. If you have any evidence to contradict those facts, please present it.
Martin, on my post of March 7th that I copied directly from your article you wrote this: "In Climate Zone 3 — an area that includes architect Sophie Piesse’s home town of Carrboro, North Carolina — the minimum prescriptive requirement for ceiling insulation is R-38.”
It’s nice to see that you have now corrected your original article. If you go to page 10 of the 2006 IECC or 2009 NC ECC you will find a map; on that map you will notice several counties located the northwest portion of NC in climate Zone 5. Therefore my math shows 3 climate zones for NC not 2 as you state.
3) I am happy to concede that cellulose, like Icynene, is able to absorb and hold water.
Martin, based on ICC approved testing what is the water absorption rate of Icynene compared to Cellulose? Answer the question please....
4) You are correct that I am a journalist with no industry credentials.
OK and we have established that you are a “journalist”. Do you have a Journalism degree from an accredited University, if that is what you claim you are?
5) Todd, I have already thanked you for making the full text of Viktor Gina’s letter available, since I was only able to reprint the portion shared by Sophie Piece at the time my blog was written. I will take this opportunity to thank you for a second time.
You are welcome for correcting your misrepresentation of Icynene’s position.
6) I can assure you that my report of my conversation with Ed Reeves was accurate. Mr. Reeves has not contacted me to contradict my report.
I wonder why? Maybe he has better things to do with his time. I think his boss, Paul Duffy wrote a very eloquent response to your misleading article!
7) Yes, I believe that REM/Rate does a good job of modeling energy use.
Cool, we’re getting somewhere!
8) "I think what we have tried to explain to Martin is that homeowners do not care about R-value or the misleading percentages that explain them or that the test for R-value is inherently flawed. What they do want to know is what will it cost them to operate their home and what is the payback on any investment." You are right that many homeowners don't care about R-value. It's also true that not all homeowners care about their energy bills. Homeowners are all over the map on these issues.
WOW, now Martin is taking on consumers; they do not know what they want so “Martin” will tell then what they need.....Sounds like a familiar position from "progressive" minded people... I believe consumers are the best gauge of reality, not Martin and his friends...don’t you?
9) You have criticized me for not loading all three photos as I was in the process of loading them. It's hard to share photos on this site, and I apologize for the low resolution of the images. All three are now loaded.
Great and thank you! We can now have a debate on “known” data points and not misleading percentages. Martin what is 100% of 1
IRC '09
Martin, you wrote:
Feb 5, 2010
7:18 AM EST John, you're right
by Martin Holladay, GBA Advisor
John,
If you or I were writing the code, of course we could do a better job. The clearest way to establish air-sealing requirements is to include a threshold -- so many cfm @50 Pa, or so many ACH @ 50 pa, or a similar threshold. But — heavens forbid! — such a logical approach would require builders to conduct a blower-door test. That's a requirement in Sweden, but here in the U.S., we're evidently suspicious of such a crazy idea.
I hope that (and I am sure that one of the 277 posts pointed out) you are aware that a blower door test is an alternative compliance path for air sealing/ insulation visual inspection in IRC '09? As far as enforcement, I would expect that as the comfort level with, and the attention given to the latest changes, that enforcement will become more uniform. I do not think the duty of improving the quality of housing should fall to enforcement officers or the ICC, though. That's like saying that highway safety is the resposnibility of police speed checks. Sorry if this issue was covered, but I did not read all 277 posts before responding.
Thanks for your comments
T.C. Feick,
Thanks for your comments. (And I don't blame you for not wanting to wade through 277 posted comments.) My blogs have several times referred to the 2009 IRC and IECC code changes, most recently here:
https://www.greenbuildingadvisor.com/blogs/dept/musings/forget-vapor-diffusion-stop-air-leaks
As I wrote in that blog, the inclusion of required blower-door testing for some new homes is definitely a step in the right direction.
I agree with you that the burden of improving housing quality should not fall only on the shoulders of code officials. But as energy codes continue to get more stringent, many of us involved with residential construction can't help noticing that many energy code requirements have never been consistently enforced.
One can only conclude that our society much choose to either (a) devise methods to improve code compliance and enforcement, or (b) come up with a different mechanism — something other than the building code — to improve the energy performance of new homes. Because the system we've got now isn't working.
enforcement is a joke (in many areas)
T.C. Feick wrote:
> That's like saying that highway safety is the resposnibility of police speed checks.
T.C., with all due respect, your analogy doesn't hold water. If a city were to make only a token effort to enforce traffic laws, and this resulted in a ridiculously high accident rate, egregious speeding, reckless driving and DUI's, I think it would be fair to hold the politicians and police responsible.
When it comes to the energy efficiency of homes, enforcement *is* the problem. Building codes and enforcement thereof drives mass market construction practice, especially with respect to energy and safety codes. In situations like energy efficiency, where defects are not apparent to the buyer, most builders only do what they must to pass inspection.
Fortunately, a growing number of builders see the marketing benefit of building efficient structures. The problem is that many 'green' builders make poor choices, opting for high visibility check-offs such as high-SEER HVAC equipment, while continuing to ignore key provisions of the energy code (infiltration and duct installation practice come to mind).
The bottom line: many jurisdictions simply don't have the political will to take energy code enforcement seriously. Builder and developers will continue to see to that.
Why Icynene recommends less
I want to get back to the starting of this long topic. Icynene has been recommending less insulation. One motivation for this that has not been brought up so far (from what I can tell) is that Icynene has installation problems when it is applied in thick cavities. I recently had a Icynene project that essentially failed IR inspections due to voids in the foam that seem to have been created when the foam pulled away from itself during the installation. We were filling 11 7/8 inch I-Joists in a cathedral ceiling. It was a huge mess, and a failure from an energy and durability perspective (despite looking perfect during a visual inspection). It seems that the product has problems actually achieving higher r-values in ceilings. Perhaps this is why they want to spray thinner?
Removing air barrier to meet Fire Code
Can someone explain why you remove the paper from insulation down 16" from top plate on an exterior wall for FIRE CODE. I can understand the (steal beam) reasoning...somewhat ...but how can you remove some of your air barrier and say sheetrock will be the air barrier?
Removing paper from insulation
Anonymous,
1. I have never heard of a building official requesting that the kraft paper facing be removed from insulation. The code requires the kraft paper facing on insulation to be protected by a thermal barrier (1/2-inch drywall, generally).
2. Kraft paper facing on insulation is NOT an air barrier.
Response to "Why Icynene Recommends Less"
Anonymous,
Thanks for sharing your story. Interesting information.
Competition
What Icynene is trying to say is competition does it, we aren't going under because we have to stick to it. I know 4 other manufacturers that suggest the same thing DEMILEC, AIR TIGHT, LAPOLLA, CERTAINTEED, and JOHNS MANVILLE. Competition is a b@#ch. We all have to keep our head above water. 99% of people almost faint when you tell them the price on 5.5". Could you imagine double!! I have plenty of references who can tell you how much I have saved by putting 5.5" of ANY open cell spray polyurethane foam. ANY BRAND! I am an advocate for foam when installed CORRECTLY @ 3.5" in vertical walls and 5.5" on all slopes it WILL out perform any fiberglass or paper product out there.
Response to Juls
Juls,
Thanks for your frank assessment of the situation.
"Competition is a b@#ch. ... 99% of people almost faint when you tell them the price on 5.5 inches. Could you imagine double!!"
That certainly sums up the current situation nicely.
Retrofit Options
1st, I am not the same Todd. But have read through all 6 pages / 286 posts :).
I am a homeowner and have read many articles etc about R-value, Air infiltration etc. My head keeps spinning on this subject. I know I can spend tons of $$ and seal up the home boost R-value etc. But as other have said, Todd included, there is a point of diminishing returns I would think. Allot of this post has been about building new homes and insulation but the other side is what is the best options/ best practices of those that have older homes and maximize energy efficiency, comfort and payback.
I have been remodeling my house slowly room by room over the past 11 years I have owned it. Over this time the suggestions/rules kept changing. I have a split level home built in 1969. I actually had an energy company come out to do a blower door test, since I am an interested homeowner that wants to make my home more comfortable and lower my expenses.
I have read about thermal bridging and using rigid foam on the exterior or double walls, spray foam, cellulose, bringing hvac into the conditioned space, hot roofs, vented roofs, etc. Many things that would make the home tight(er) would require modification on the exterior and budget wise I am not going there yet. Need to finish the inside first. I have read about Icynene (Open Cell) as well as cellulose or closed cell and not sure what direction I should go. I will have walls open in about 1/3 of Sq footage to re-insulate. Maybe up to 2/3 of the living area/garage if I choose to go that far now. My A/C and duct work is installed in my attic. Heat is in basement.
Response to Todd S.
Todd,
Thanks for sharing your story. You didn't really include any questions.
You wrote, "I have read about Icynene (open-cell) as well as cellulose or closed-cell and not sure what direction I should go."
If you are asking which of the three options to choose, it's up to you.
Open-cell foam and cellulose have about the same R-value per inch. Cellulose is the "greener" choice because it is made from recycled newsprint.
Closed-cell foam has about twice the R-value per inch of the other two products you mention, so it makes sense if your stud bays have limited depth, as yours probably do. But closed-cell foam is expensive, and some green builders try to avoid it because it is made from petrochemicals.
Response to Martin
I guess I am trying to ascertain what would be the best option for insulation and stop air infiltration in my retrofit situation. Particulars:
1) Not planning on re-siding yet. Maybe another year.
2) Sheathing is Celotex (I think that's what is called)
3) Only siding that will be removed is for the new windows, in the area of the remodel. Flashing & tyvek around the windows for now to tpae and tie into later when I re-side. . I may cutback the celotex around the window framing and use 1/2 plywood like I did for other windows.
I am gutting 1/3 of the living space. Possibly it will be up to 2/3's depending on budget. Given the above and not touching the exterior at this time, thus can't wrap & tape the house with Tyvek as an air barrier, what would be the best choice then for air sealing from the inside. I ask because I thought open cell, like Icynene or even cellulose could collect water vapor.
As I mentioned above, my air handler for the house A/C is in the attic. Actually its in the upper attic and the duct work comes down into the lower attic above the section I will be remodeling. I know its optimum to have the duct work and air handler inside the conditioned space. But don't know if this could be accomplished. Not much room to frame it in somehow and leave room for insulation. Or is a hot roof possible and a good idea for a retrofit. What would be the best way to accomplish.
Second response to Todd
Todd,
Properly installed, neither open-cell foam nor cellulose will collect moisture. My insulation advice remains unchanged: it's up to you.
If your number-one goal is air sealing, then either open-cell foam or closed-cell foam will result in lower air leakage rates than cellulose.
The best way to address having an air handler in the attic is to move the insulation to the sloped rafters and bring the attic into the conditioned space. If you don't want to do that, move the air handler and ductwork.
Follow-up to Martin
In the case of cellulose or Icynene do you need to use a vapor barrier (i Am in NJ). I know you said that neither will collect moisture if installed properly. I assume that means that the cavities are sealed so that there is no air movement. Thus preventing moisture through the wall through conduction or convection.
As far as the attic goes, if I move the insulation to the rafters then I assume the are talking hot roof. Would it then be open cell or closed cell foam in this application. I thought I read it should only be closed cell. To prevent potential rotting of the roof deck. But looking for verification. The pitch is not high. I have to check this and the rafter height, which is probably 2x6's. Need to make sure that I can get enough R value this route. Also would have to seal up the ridge vent. As far as moving HVAC and ductwork, I don't see that as a viable option. Only other thought would be to somehow frame it in and sheet rock the walls to sort of bring it into the conditioned space but not sure there is adequate space to do that.
Third response to Todd
Todd,
Q. "In the case of cellulose or Icynene do you need to use a vapor barrier (I am in NJ)?"
A. Most building codes require an interior vapor retarder (not a vapor barrier). Open-cell foam qualifies as a vapor retarder. If you install cellulose, vapor-retarder paint (on your drywall) should work fine. For more information on vapor retarders, see Vapor Retarders and Vapor Barriers.
Q. "If I move the insulation to the rafters then I assume the are talking hot roof. Would it then be open-cell or closed-cell foam in this application?"
A. For answers to all of your questions about insulating a sloped roof, see Creating a Conditioned Attic.
What a load of *&$%
I want to start by saying that I install spray foam, cellulose, and Tripolymer injection foam. I also perform energy audits for new home owners and I am a professional witness for legal matters. I hear this line of BS from local spray foam contractors all the time. I visited two home this past summer that were told it was OK to use 5” of open cell spray foam in the overhangs and 8” in the attics. They both moved in and when winter came they had freezing floors over their garages. They also had very high energy bills. I agree that the air sealing function of spray foam products has its benefits, but don’t make the mistake of thinking that you can get away with a lower R values. My two customers that are I the process of suing the insulation contractor and builder have a different opinion on the topic and with a professional witness like myself at their side you are going to find yourself in deep trouble.
I would also like to point out that contractors that are only installing R30 spray foam in your attic are not focusing on your best interests. They are also not focused on helping the environment. R30 is a decent R value for today’s energy cost, but as fuel prices increase you are going to need R values that are much higher. If you want to insulate your attic the right way you should consider a good air sealing package and minimum of R50 cellulose or blown fiberglass. Needless to say cellulose would be the better product to use. It has a lower embodied energy and manages moisture better than fiberglass.
If you want to see a scary video of spray foam being used in attics go to “YouTube” and search for “NFPA Fire Test Video Short”. The video shows a comparison between cellulose, fiberglass, and open cell spray foam. I will let the video speak for itself.
Ray Evangelista
Performance vs. Prescriptive
Wow, all i read about here is R-value and "the code". Does anyone even care that there are different ways to pass the energy efficiency portion of "the code"? That is called the performance method. Basically if you show, with an approved method, that your system is equal or better than model energy code then you pass. This means using a blower door to quantify the tightness then plugging that number into REM-rate or REM-design software to determine actual energy consumption. Do this a couple times and you will see leakage rate has a much larger effect on BTU's then R-value.
I am an Icynene dealer and a mechanical engineer. I continuously educate myself and enjoy reading these blogs. Thank you for adding to the discussion.
Response to Stuart Fern
Stuart,
To prove compliance with the performance path option of an energy code, a builder must submit documentation using a program like REM/Rate. If the REM/Rate calculation shows compliance, then the local building official will sign off on the design.
When Icynene was called to task for promulgating Viktor Ginic's letter, the company eventually responded that Ginic was referring to performance path compliance methods, not prescriptive path compliance methods. However, this explanation strains credulity, since following the performance path requires no such letter or documentation beyond the required REM/Rate calculations. In other words, if you are following the performance path, you already HAVE documentation, and the Icynene letter would be redundant and unnecessary.
Some Icynene dealers, and some builders, were using Ginic's letter for the purpose of convincing code officials to allow them to skimp using the prescriptive path. But now that the issue has been made public, I accept the fact that Icynene has backed away from that tactic and has publicly disavowed it.
R-25.2 in my attic is better than the R-30 Batts
Two winters ago, I had 6" of Demilac Ago Balance sprayed in the attic of my Flagstaff (winter lows down to -20, summer temps as high as 96) 1977 ranch style home, replacing the R30 batts placed in between the bottom chord of the trusses. I had also removed all exterior wall drywall and fixed the poorly installed batt insulation and glued and sealed 1" foil faced isocene before screwing and glueing the new drywall on. All of the new Pella triple panes were properly installed and sealed.
My energy costs dropped 15%, not an amount that will pay for the new insulation for several years, if ever, but, the bedrooms are now useable spaces. Now that the kids are grown and moved out (for good, we hope) we can use the two spare bedrooms for and office for me and a studio for my wife. It used to be that winters rendered the rooms so cold, you could see your breath. Our kids had complained for years about the situation. Proper tightening and insulating is well worth the extra costs.
As a builder of passive solar sustainable straw bale homes for the past near 20 years, I have always followed the principles of the passivhaus. The first rule of good passive solar design is tightness, followed by insulation. Those two principles, as taught by Johnny Wiess of Solar Energy International, works well for any location, even those that do not have good access to the sun. For most of the past years I have followed the Oakridge National Labs recommendation of R-50 attics for our climate, but when I use the expanding foam, I drop back on this since the tightness compensates for insulation value.
I based my decision to under-insulate on the attached chart, which shows the drop off in benefit with more inches of insulation.
Response to Ed Dunn
Ed,
I certainly agree that efforts to improve a home's airtightness are important and cost-effective. Good for you for improving your home's performance.
Unfortunately, the bar graphs in the pdf document that you link to are misleading, as I have stated in earlier comments. Any bar graph that compares a proposed installation of spray foam with 0 inches of insulation or 1 inch of insulation is absolutely ridiculous, since those installations are illegal. Instead, the bar graph should compare proposed spray foam insulation thicknesses with the minimum code requirements.
Thought they did?
Martin, Graphs 2.1 to 2.2 DO compare isocene to fiberglass. What am I missing here? Also, charts 1.1 and 1.2 show that there is little gain with added foam thickness. It seems to be working on my house as advertised.
As my house is not a solar home (shaded) and my highest monthly natural gas bill is now down below 80 CCF (from about 100 before re-insulating), proof is in the pudding? Once I chop down those trees and put in the trombe` walls, gas consumption should go even lower.
Response to Ed Dunn
Ed,
The bar graphs in Figures 1.1 and 1.2 are deceptive because they include illegal options like 0 inches of insulation, 1 inch of insulation, and 2 inches of insulation. These illegal options lead the uninformed reader to conclude that they represent conventional options when in fact they are irrelevant.
The line graphs that compare the perfromance of Icynene with fiberglass are deceptive because they assume that the builder of the house with fiberglass insulation made no attempt at air tightening -- which, as my blog explained, is routine but illegal.
Of course if you compare the performance of Icynene to a house that is 7 times leakier, the Icynene house will look good!
Icynene isn't so wrong after all!
I know this is an old thread but I need to chime in. The problem is, that with the advent of these wonderful spray foams, both Demilec and Icynene, the performance is SO superior that the argument that a house is insulated against the elements based on an R value becomes a nonsequitur. And, truly, I can vouch for the superior performance as owner of an Energy Star home in which only 6 inches of Demilec were sprayed between the rafters of my attic. The attic is 70 degrees on a 90 degree day, that is absolutely superior! The problem with R Value is the science behind its creation. It is a measurement in which the heat transfer was measured in an environment without average wind speed. I say do away with the R Value system entirely and replace it with something that makes sense in the real world! Every leak alters the thermal barrier. We are not talking apples and oranges folks, in the real world all of these elements need to be looked at together. Just my two cents and thanks! I am a double green certified Realtor and VP of an Energy Star custom builder in North Carolina. Yes, we achieved our 69 HERS score with only 6 inches of spray foam insulation in the attic and the code inspector understood the analysis; it was a bit of a fight but we got it done :)
Attic Temperature
Meg, the reason that the attic is 70 is because it is conditioned....not because the spray foam is magical ...and concerning the HERS index....I scored a HERS index of 51 on my home partly because I exceeded minimum code R-value
To put a point on a couple of things
I agree wholeheartedly with Martin that Icynene should not be condoning an installation that does not meet the letter of the law. I also agree with Dan, that it is easy to overspend on insulation using today's assumptions for materials cost and energy cost in an LCCA, but that was not the focus of the original article. A market rate house built by a builder who cares not for energy efficiency is a poor performer. Icynene's recommended installation may well perform better. That also was not the focus of the article. It is Ethics vs Economics. I will use foam where it makes sense. Where air sealing is easy to achieve elsewhere in the assembly, I will continue to use cellulose. Martin's article, as I saw it, was an exposure of a flawed and unethical marketing technique. An explanation on the requirements of IRC ch 11 may be needed for some, since the article references those paths of compliance. Martin's expressed focus on the air sealing requirements, and the lack of enforcement, is a much larger problem than Icynene's marketing. Flaws in air sealing exist in almost all of our built environment. The codes are moving to a performance test of air sealing through mandatory blower door test. I see that as a great move, although it will take years to be the norm in most jurisdictions outside some major urban areas in progressive states, code-wise. Spray foam in all of its forms is a fraction of the market at present. Good discussion! Thanks Martin and commenters.
R rating "system"
I really don't blame the Icynene people for responding to Martin's somewhat snarky article about their analysis of the most efficient use of the product. Anyone else would do the same, and we all know that any structure must be addressed as an entire system , when attempting to evaluate the energy efficiency of the building.
To simply say that you need R-whatever , placed throughout the entire structure, regardless of the type of insulation , is simplistic, dogmatic, and frankly wasteful.
Kevin O'Kelly's argument about the redundant effects of simply piling R-Value on top of R-Value is a good one.
Anyone in the building trades for a while can see that simple R -values are really value-less , in predicting the overall HVAC energy consumption of a structure. I would like to see DOE start using a more responsible system of measuring heat movement, utilizing all three forms of heat energy migration. Maybe they could call it the H Factor. Anything would be better than the present R rating system, concocted by the manufacturers of Fiberglass.
Response to Mark Winslow
Mark,
You wrote that "the present R rating system [was] concocted by the manufacturers of fiberglass."
You are wrong. R-value was first defined by Everett Shuman, the director of Penn State’s Building Research Institute, in 1945. It was not developed by the fiberglass industry. For more information on this topic, see Understanding R-Value.
You wrote, "I would like to see DOE start using a more responsible system of measuring heat movement, utilizing all three forms of heat energy migration." Actually, R-value already measures all three heat flow mechanisms -- conduction, convection, and radiation. Again, see my article, "Understanding R-Value," for further discussion of this topic.
Concerning your proposal to develop "a more responsible system of measuring heat movement" that might be called "H Factor," building scientist Joseph Lstiburek is already working on that project. (I sometimes jocularly refer to his new metric as the "Joe factor.") For more information on the Joe factor, see A Bold Attempt to Slay R-Value and Air Leakage Degrades the Thermal Performance of Walls.
I disagree strongly with your contention that "R-values are really valueless in predicting the overall HVAC energy consumption of a structure." Any energy modeler will tell you that knowing the R-value of a wall assembly, roof assembly, or floor assembly is absolutely essential to understanding or predicting energy consumption for space heating or space cooling. It is one essential factor -- but not the only factor.
response
OK, I can see that you are an intellectually dishonest poster , so I will not continue this.
You are very skilled at misquoting , or re-defining someone's statements , and then attacking the false argument. I never said that R-values are meaningless, I said simple rvalues (re: alone) are meaningless, and you yourself admit in the last sentence that it is not the only factor, which is exactly what I was meaning.
Upon reading the other posts here, I can see you doing this on a regular basis, defending an article which was intemperate, and frankly should never have been posted, because it is obtuse in nature.
BTW- your OWN ARTICLE that you cite, contradicts the statements you make here, so I am really wondering why I am wasting my time. Have fun.
Response to Mark Winslow
Mark,
As you can imagine, I stand by my story and my recent remarks. My quotes are all accurate, and, as you can imagine, I don't quite agree with your assessment of my writing as "intellectually dishonest" and "obtuse."
However, if you and I agree that R-values are necessary but insufficient information for evaluating the performance of a house or building, then that's great. I always like to emphasize points of agreement.
H-Factor
In no way am I supporting the use of R-20 (of any form of insulation) in a roof assembly. I do however see problems with the R-value system. Until Joe Listiburek completes the "H" rating system- consumers (and many professionals) will continue to be misled by R-value numbers.
The insulation's rated R-value is frequently misunderstood as the "whole wall" performance. Whole wall performance is affected by; air leakage, convection patterns in the insulation, difficult spaces left unfilled by insulation, thermal bridging, wind washing and so on. I doubt this is news to anyone reading this.
In real world applications different types of insulation with the same R-value perform differently because they affect the each of these variables differently. Again, no news here, but as soon as you try to explain this to a consumer they look at you like you are selling snake oil.
All other factor being equal (air sealing, R-value, thermal bridging) spray foam does typically outperform loose insulation products with the same “R-value”. It’s difficult to imagine a real world application where spray foam doesn’t fill the cavity better, and reduce convection/wind washing/ air infiltration when compared to fiberglass.
How much of a difference does it make to go from batts to spray foam? It depends on the other variables.
1. Is the spray foam installed”over” the rafters to reduce thermal bridging?
2. Is there ridged foam above the sheathing to control thermal bridging?
3. How well air sealed is the building? In a perfectly air sealed building the performance level of batts would probably come close to that of spray foam. In a very leaking building an R-5 of spray foam might outperform the R-38 fiberglass.
R-value numbers get even more confusing when comparing things like SIPs or ICFs to stick build assemblies and fiberglass batts. The consumer is left very confused and opts for the low bid with the fiberglass batt insulation of the “right” R-value.
Full disclosure: I like working with SIPs, soy based spray foam, AND cellulose. In my opinion no system or insulation is perfect and all of them can be valid choices in the right circumstances.
Imagine a truss roof with insulation in the attic floor and the attic is vented. Is there anyone who would argue that R-38 batts would perform as well as R-38 spray foam? So how do we educate the public on the difference?
Response to David Jones
David,
Q. "How do we educate the public on the difference?"
A. GBA has attempted to educate the public on these issues, and continues to do so. Here are some links to relevant articles:
Understanding R-Value
A Bold Attempt to Slay R-Value
Air Leakage Degrades the Thermal Performance of Walls
Installing Fiberglass Right
Air Leaks or Thermal Loss: What’s Worse?
education vs. communication
GBA does a great job of exploring these issue in depth for readers who already have some kind of understanding of the subject. If a reader has found GBA they probably already have a fairly high level of understanding or are in the process of putting in the effort to get there.
The vast majority of the public has no clue about these things. Yes, they could read GBA, but for someone starting out on the path of understanding building science issues it would be huge undertaking.
My question of how to do we "educate" the public was misleading since there are sources like GBA for people willing to put in the effort to truly educate themselves. My question was intended to refer to those who just starting down this path, or who want to do the right thing but don't want to make the kind of effort required to understand these issues. (There are over 300 posts on this one subject alone and not all the comments agree.
Most people want these issues to be condensed to a few numbers or sentences. I talk to hundreds of people a year about energy. Almost all of them have heard of R-value. Almost none of them understand or want to understand R-value at the level discussed here. The problem as I see it is that the insulation R-value does not equal performance (its only one factor in performance), but the public believes it does.
Whole wall R-value numbers sound good in theory, but they are to easily confused with the insulation R-value. I look forward to the "H" factor system. We need a more comprehensive way to quantify performance for people not willing or able to understand these issues in depth.
Icynene
I recently had the perimeter above ground wall cavities of my walk-out basement filled with this open-cell foam. The contract says it would be insulated to R-19 but they filled the 3 1/2 stud cavity and by their materials this is 3.7 per inch R rating. In response to my inquiry after the fact they sent me a letter from 2003 that says in performance this meets Michigan building requirements (did in 2003 perhaps or is this the same logic in the above discusison--it performs better than the company rating in practice.)
And now, what can I do? possible to add Polyiso over this to meet at least R20 or have it removed? and start over? or?
Advise much appreciated.
Response to Phylis Floyd
Phylis,
The insulation company is clearly in violation of the contract. The stud bays are insulated to about R-13, while thermal bridging through the studs brings the whole-wall R-value considerably below R-13. There is no possible way to argue that this is an R-19 wall.
Step One is to negotiate with the insulation company to see if they can agree to a solution. A negotiated settlement is better for all parties than taking the company to court.
Possible solutions include:
(a) Removing the existing insulation and replacing it with closed-cell spray foam.
(b) Installing a continuous layer of rigid foam on one side of the wall to boost the wall's R-value.
Good luck.
Log in or become a member to post a comment.
Sign up Log in