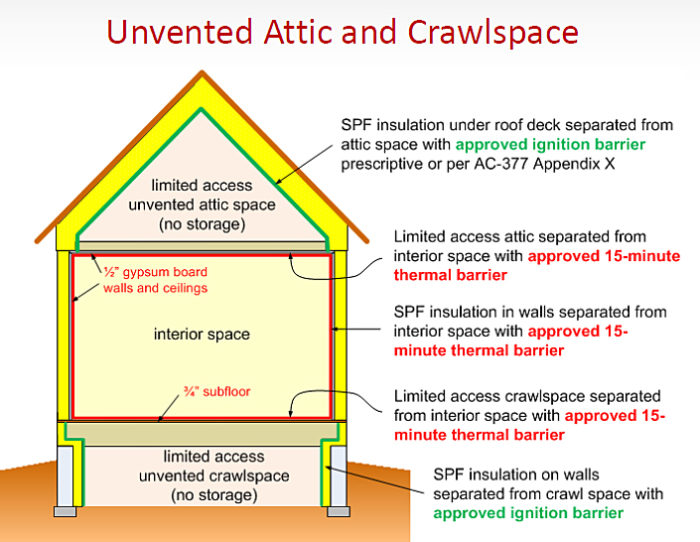
[Image Credit: Image #1: Rick Duncan / Spray Polyurethane Foam Alliance]
UPDATED on February 6, 2021 with new information on the use of mineral wool insulation as a thermal barrier.
Do building codes require spray foam insulation to be protected with a layer of drywall or a comparable barrier for fire safety? There is no simple answer to the question, for several reasons. The first reason is that the code is complicated.
The second reason is that the code is poorly written.
The third reason is that the code is subject to interpretation by local code officials.
And the fourth reason is that even when the code clearly requires spray foam to be protected with a thermal barrier or an ignition barrier, many code officials don’t bother to enforce the code.
Unprotected spray foam can be a fire hazard
Exposed spray foam can be hazardous. According to a guide for spray foam installers, “Thermal Barriers and Ignition Barriers for the Spray Polyurethane Foam Industry,” “When exposed to fire sources, such as trash fires, welding arcs, cutting torches, or red-hot metal, unprotected SPF [spray polyurethane foam] can ignite and may result in a flash fire.”
If a house that includes spray foam ever burns down, lawyers will want to know whether the spray foam was installed according to code — so builders who don’t pay attention to ignition barriers are taking on liability.
Distinguishing an ignition barrier from a thermal barrier
Before delving into this issue, we need to learn some code jargon.
The building code has two different terms to describe barriers to protect insulation from catching fire. The first term is “thermal barrier.” (The ill-chosen phrase is code-speak. Most builders and scientists use the term “thermal barrier” to refer to insulation; unfortunately, code writers use words in a way that differs from most speakers of English. So for the purposes of…
Weekly Newsletter
Get building science and energy efficiency advice, plus special offers, in your inbox.
This article is only available to GBA Prime Members
Sign up for a free trial and get instant access to this article as well as GBA’s complete library of premium articles and construction details.
Start Free TrialAlready a member? Log in
29 Comments
Our Code
Very interesting blog Martin.
"If a house that includes spray foam ever burns down, lawyers will want to know whether the spray foam was installed according to code — so builders who don’t pay attention to ignition barriers issue are taking on liability."
I know you are addressing the majority of your readers when you refer to "the code", but our codes in Canada place the responsibility for ensuring that their structures meet code on the owner, not the builder. Something worth knowing when you put your faith in your architect or contractor.
Response to Malcolm Taylor
Malcolm,
I'm not a lawyer, so I can't claim any special knowledge about U.S. liability laws.
However, in many cases, the plaintiff's lawyer throws a wide net, alleging that almost everyone is somehow liable -- and in the end, the lawyer hopes to snare someone with deep pockets (either a wealthy individual or an insurance company).
Metal SIPs
Would the metal that encloses metal SIPs serve as an thermal barrier? Though it would require the use of conduit for electrical runs, I've wondered if anyone merely finishes these surfaces on the inside without drywall. I know that it has been done on the outside.
Martin, I haven't seen spray
Martin, I haven't seen spray foam companies coating spray foam for fire such as an unvented roof in an attic with limited access hatch. Codes call for access hatches. Which code to break? I know of both being broken.
And without reading thru again... what about spray foam on attic floor? Cover with ___" of cellulose and then legal, how many inches?
Response to Jeff Carroll (Comment #3)
Jeff,
Q. "Would the metal that encloses metal SIPs serve as an thermal barrier?"
A. It isn't a prescriptive thermal barrier, but it may have been approved as an equivalent thermal barrier if the manufacturer of the SIP contracted for the necessary testing. Contact the manufacturer of the SIP and ask whether the required testing has been performed.
Response to A.J. Builder (Comment #4)
A. J.,
You wrote, "I haven't seen spray foam companies coating spray foam for fire such as an unvented roof in an attic with limited access hatch."
It doesn't surprise me to learn that the code isn't being enforced in your area. In spite of the lack of code enforcement, however, builders are still required to follow the code. If a homeowner wants to challenge a builder for building a house that doesn't meet code, the fact that the local inspector didn't catch the code violation won't get the builder off the hook.
Q. "Codes call for access hatches. Which code to break?"
A. I advise you not to break the code. If you are required to include an access hatch, you are also required to protect spray foam insulation with an ignition barrier or a thermal barrier.
Q. "What about spray foam on attic floor? Cover with X inches of cellulose, and then legal? How many inches?"
A. Cellulose can be used as an ignition barrier; for more information, see Cellulose Fire Blocking and Ignition Barrier Capabilities. Curiously, that document does not state the minimum number of inches required for cellulose to comply with ignition barrier requirements. According to Dana Dorsett, the answer is 3 inches. I suggest that you confirm that thickness with the manufacturer of the cellulose product you are using before adopting this approach.
I've seen quite a bit of spray foam
I've inspected some homes that have had spray foam installed and it would seem that the GC's are unaware of the thermal barrier requirements. The spray foam companies don't bother to tell them when they bid the job. In this area there are many homes that want the rustic look of tongue and groove knotty pine and the contractors want to install it without the required thermal barrier.
The SPF contractors don't tell the GC about the barrier because the cost of the foam plus the thermal barrier makes that option more expensive than fiberglass and tongue and groove.
The contractors scream when they find out because they never included sheetrock in their bids.
There was a great write up in a Canadian publication titled "Polyurethane spray foam, solid gasoline" that was pretty scary.
There are only several jurisdictions rigorously enforcing this part of the code, or that's what I hear from the contractors.
Building codes that are
Building codes that are unclear suck.
Storage
I just have to point out that there's an elephant in the room in terms of ignition barriers. Can anyone honestly think of a single accessible space in house that will not eventually be used for storage? The only deterrent I've seen is a crawlspace so disgusting no one would think of going in it. Attics are always game, no floor, no problem.
Response to Andy Kosick
Andy,
Some building inspectors may agree with you, so it certainly makes sense for builders to discuss this issue with the local building department.
Builders of energy-efficient homes who want to discourage homeowners' attempts to use unconditioned attics for storage sometimes omit a conventional access hatch. Instead, access to the attic is via a small exterior door on the gable end of the house; this type of access door can only be reached with an extension ladder.
This method reduces, but does not eliminate, the chance that homeowners will use this type of attic for storage.
.
tongue-and-groove ceiling
The code directly addressed tongue-and-groove wood ceilings and spray foam in section R316.5.2: "The thermal barrier specified in section R316.4 is not required when foam plastic in a roof assembly or under a roof covering is installed in accordance with the code and the manufacturer's installation instructions and is separated from the interior of the building by by tongue-and-groove wood planks or wood structural panel sheathing in accordance with Section R803, not less than 15/32 thick bonded with exterior glue and identified as exposure 1..."
I really don't know what kind of fire testing, etc, this came from, but it is pretty clear that foam behind tongue-and-groove is OK by code without a thermal barrier. Not clear whether an ignition barrier is required instead, but I have interpreted that to mean that a cathedral ceiling with tongue-and-groove would not need it, while an unvented attic with limited access over a tongue-and-groove ceiling still would.
Response to Leigha Dickens
Leigha,
Thanks for pointing out the provisions of section R316.5.2. I have edited the article to include a reference to this code section.
Response to Leigha and Martin
Hi Martin and Leigha,
As far as tongue-and-groove wood planks go - would you interpret the code provisions to apply to walls as well as ceilings?
I am thinking of having my interior basement walls insulated with spray foam (they are bare concrete right now). I am planning to build some interior stud walls first so that after the insulation I can create some finished space. I want to know if I have at least the *option* not to use drywall but to instead use tongue-and-groove boards. (or anything else - what else might meet the criteria?)
From my understanding, one way to have that option would be to have the installers also apply intumescent paint (so I would not need an additional "thermal barrier"). But that paint is costly and I would be interested to know if I can proceed without it.
Thanks for your insights.
Response to Susie Derkins
Susie,
The exception provided by Section R316.5.2 of the code clearly applies to roof assemblies, not walls.
But there are countless examples of muddy language in the code, and the final arbiter is always your local code inspector. My interpretation is irrelevant to your dilemma; the only person who can answer your question is your local inspector.
thermal barrier on a building base
Hi Martin,
In a building base which is not meant to be as a crawling space, nor for storage, but is insulated with SPF, do I need to use a thermal or an ignition barrier?
thanks,
Response to Luis Rivera
Luis,
I don't know what you mean by a "building base." Do you mean a basement?
If it is accessible, you probably need a thermal barrier. If it is hard to access and not used for storage, you may be able to get away with an ignition barrier. If you have any doubts, just ask your local building inspector (the local authority from your building department).
Thermal/igniton barrier
No, is not accesible, nor a basement... is the base for an electrical substation control building. For what yuo say, probably I don't need to use the barrier, but I'll check with the code official.
Thanks!
See page 37 of this BASF presentation
http://www.duluthenergydesign.com/Content/Documents/GeneralInfo/PresentationMaterials/2014/Day3/omanbr-safspr.pdf
Check foam products ICC-ES Report for tested and accepted alternatives
Update on 3/4-inch plywood as a Thermal Barrier
I was recently looking at this topic in more detail for a project--it appears that one of the amendments to the 2015 I-Code now explicitly allows 3/4" (okay, 23/32") wood structural panel as an interior thermal barrier. See page 180 in this writeup of the accepted revisions in the 2015 I-Codes: http://www.ecodes.biz/ecodes_support/free_resources/Pennsylvania/PDFs/2015_IRC_Revision_History%20.pdf (screenshot of the page below).
Response to Kohta Ueno
Kohta,
Thanks very much for sharing the information. I have edited my article to include a reference to your comment.
Need to Rock the Lid?
Hi All,
I'm trying to add drywall as a thermal barrier in a basement. A previous homeowner seems to have used a diy spray foam kit on the walls and the foam is currently exposed. I'm happy to sheetrock and fire tape the walls, but for various reasons I'd rather not sheetrock the ceiling. Of course, this will not close off the spray foam completely because of the open joist bays. The only other option I can think of to seal those gaps is to add a dorky little drywall rectangle in each bay to seal it off. Is there a smarter solution or are those my two options?
Thanks in Advance,
First Time Long Time
Hi Nelson,
While it's likely you may have already found a solution (I'm late to this thread party), we have had success with using Roxul in these situations. In fact, the code inspector in this case recommended it. Of course, as Martin and others have said, best to check with your local official.
Best,
Ben
Sorry to bump an old thread. I could post this question in the Q&A forum, but it seems appropriate here...
This article concentrates on the thermal barrier requirements for spray foam specifically. Are the requirements the same for other types of solid foam insulation that are exposed to the interior of the house?
For example, I am considering using a pre-cast concrete foundation wall system for my new house which is available with integrated interior XPS insulation (the foam is actually used as a form when the wall section is cast) and would be exposed on the interior of the basement. Would that exposed insulation also be required to be protected with an approved thermal barrier? If so, it forces me to finish the interior of the basement (at least to the extent of installing a thermal barrier) when building the house instead of waiting until my finances recover as I was planning.
Thanks,
Jim
Jim,
The relevant code section (as explained in the article) is Section R316.4 of the 2009 International Residential Code (or comparable sections in later versions of the code).
The code refers to "foam plastic," which is code-speak for "cured spray foam or rigid foam (including XPS, EPS, and polyiso)."
Q. "This article concentrates on the thermal barrier requirements for spray foam specifically. Are the requirements the same for other types of solid foam insulation that are exposed to the interior of the house?"
A. Yes.
Q. "I am considering using a pre-cast concrete foundation wall system for my new house which is available with integrated interior XPS insulation (the foam is actually used as a form when the wall section is cast) and would be exposed on the interior of the basement. Would that exposed insulation also be required to be protected with an approved thermal barrier?"
A. Yes.
Thanks, as always, for another helpful article, Martin. Quick question:
I'm planning to install 3/4" tongue-and-groove boards directly over closed cell spray foam in my un-ventilate cathedral ceiling. My understanding is that those boards will serve as a sufficient thermal barrier, but I've read elsewhere that I'd need to install the 3/4" boards *on top of* 1/2" gypsum board. Can you please clarify? Is there any reason in addition to fire safety that I'd want both boards and sheetrock between me and the spray foam?
User 7493744,
As to whether or not you need gypsum drywall as a thermal barrier, that ruling needs to come from your local code enforcement official (who is the only person whose opinion matters). My ruling is irrelevant.
If you were installing a fluffy insulation like fiberglass batts, an airtight interior layer (for example, gypsum drywall with taped seams) would be essential. If you are insulating with spray foam, which is an air barrier, the interior side air barrier becomes unnecessary.
I had open cell foam sprayed in the rim joist area of an unfinished basement. It was applied much thicker than the allowable 3 1/2" thickness, so it needs a thermal barrier. The inspector has said he is okay with either 1/2" drywall or an intumescent paint (even though, as I read this article, an intumescent paint is only acceptable in a crawl space or non-storage attic.)
I recall reading in the past of the health hazards posed by flame retardants. Is exposure to DC-315 intumescent coatings something to be concerned about if it is sprayed in a storage/utility space? It would certainly be much easier than trying to cut and cobble drywall around all the joists.
Timothy,
Q. "Is exposure to DC-315 intumescent coatings something to be concerned about if it is sprayed in a storage/utility space?"
A. I have no idea. I'm not a fan of intumescent coatings -- mostly because the performance of these coatings in a fire is somewhat suspect compared to the protection provided by 1/2 inch drywall. I haven't heard of any health problems associated with intumescent coatings -- but I haven't researched the issue.
Thanks, Martin, for your response. It probably would take me less time to install the drywall than to research potential toxicity of the intumescent coating. Plus, it sounds like a better thermal barrier.
Log in or become a member to post a comment.
Sign up Log in