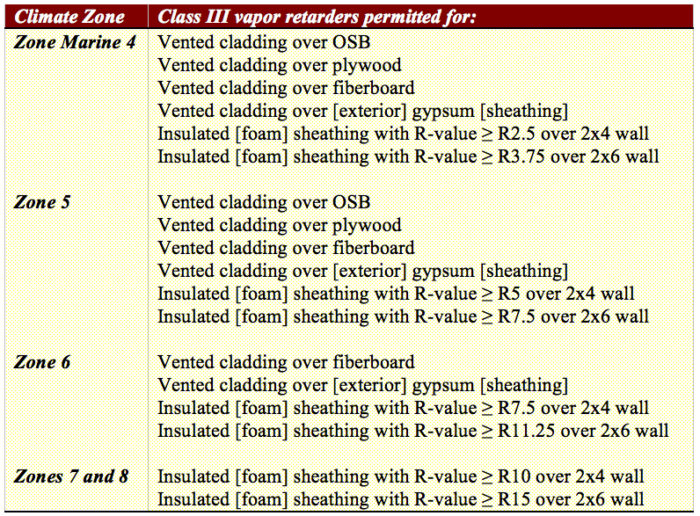
Image Credit: Martin Holladay / IECC
UPDATED on May 15, 2015
Although building science has evolved rapidly over the last 40 years, one theme has remained constant: builders are still confused about vapor barriers.
Any energy expert who fields questions from builders will tell you that, year after year, the same questions keep coming up: Does this wall need a vapor barrier? Will foam sheathing trap moisture in my wall? How do I convince my local building inspector that my walls don’t need interior poly?
To begin a discussion of vapor retarders and vapor barriers, I’ll answer a few of these persistent questions. Since I plan to return to this topic in a future blog, I invite readers to submit further questions.
Q. Why would I want a vapor retarder in my wall or ceiling?
A. Vapor retarders help slow the diffusion of water vapor through a building assembly. During the winter, a vapor retarder on the interior of a wall will slow down the transfer of water vapor from the humid interior of the home into the cool stud bays. During the summer, a vapor retarder on the exterior of a wall will slow down the transfer of water vapor from damp siding towards the cool stud bays.
However, a vapor retarder is a double-edged sword: while under some circumstances it can have the beneficial effect of helping to keep a wall or ceiling dry, under other circumstances it can have the undesirable effect of preventing a damp wall or ceiling from drying out.
Q. How often does water vapor diffusion through walls and ceilings cause problems?
A. Very rarely. In many cases, in fact, an interior vapor retarder does more harm than good. The main mechanisms by which moisture enters a wall are from the exterior (usually due to flashing defects that admit wind-driven rain)…
Weekly Newsletter
Get building science and energy efficiency advice, plus special offers, in your inbox.
This article is only available to GBA Prime Members
Sign up for a free trial and get instant access to this article as well as GBA’s complete library of premium articles and construction details.
Start Free TrialAlready a member? Log in
99 Comments
More confusion
Martin
Thanks for the informative blog. I just wanted to point out that in many places, especially northern climates, that the poly barriers are detailed and sealed because they are not only doing the job of "vapor barrier" but as the primary "air barrier" as well. It is by far the most common method used around here. Almost no one actually calls it an "air barrier" though...almost always referred to as " vapor barrier" which I believe adds to the confusion...
Good point.
You're right Garth. It's amazing to me that this confusion still exists. As far as I can tell, the Building Code of Canada actualy does a reasonable job of differentiating between the two.
Poly air barriers
Garth,
You're right, of course: in Saskatchewan, builders have used a layer of polyethylene as an air barrier since the late 1970s. The tried-and-true air barrier method involved carefully sealing the seams with Tremco acoustical sealant. The method works well in cold climates.
There are only two unfortunate aspects to this tale:
1. Saskatchewan builders mistakenly referred to this air barrier as a "vapor barrier," which only added to builders' misunderstandings of the poly's primary purpose.
2. The method was adopted in warmer climates where interior polyethylene is inappropriate.
Two more unfortunate aspects
Martin
Add these to the unfortunate aspects
3. Poly actually makes a poor air barrier because it is easily damaged and flexes to much (pumping)
4. Most new homes up here also use AC and have stucco on the exterior....more trouble???
Thanks Dr. Joe
For the shoutout to North Carolina!
Martin - good article - you did not discuss the foam sheathing much which is also a vapor barrier - getting conflicting opinions on this site. In a mixed-humid climate - they have always told us no VB - allow the wall to dry in both directions - now most seem to recommend foam exterior sheathing - seems like we are breaking our own rules. I assume it is ok during the summer - will stop the vapor drive from the exterior. During the winter - vapor is moving from inside to outside so the foam will keep us above our dewpoint. Does this pretty much have us covered - is there anything else we should be thinking about? If we are going to install foam on the exterior - how can we calculate the dew point to make sure it is think enough? Do you think 1/2" is enough in NC or do we need to go up to 1"?
For future articles, would like some information on roof vapor retarders/barriers - seems like most of the new "high performance felts" are vapor barriers - having a hard time understanding when we can use them - vented vs. unvented attic, etc. Thanks.
Foam sheathing permeance
Danny,
Your statement that foam sheathing is a vapor barrier is only true for foil-faced polyisocyanurate. At typical thicknesses, EPS and XPS are vapor retarders. One inch of EPS has a permeance that ranges from 2.0 to 5.8 perms, while one inch of XPS has a permeance that ranges from 0.4 to 1.2 perm. In general, permeance decreases as foam density increases — and, of course, as thickness increases.
If you are building in North Carolina, it's important to consider the possible effects of inward solar vapor drive. By limiting this phenomenon, foam sheathing is your friend, not your enemy. And, as you correctly point out, foam sheathing reduces the chance of winter condensation in wall cavities.
In climate zones 3 and 4 — the climate zones of North Carolina — the likelihood of problems arising from winter condensation in walls is quite low, especially if your wall includes an air barrier. Although 1/2-inch-thick foam sheathing won't get you into trouble in your climate, it also won't provide much of a thermal benefit. To reduce thermal bridging through studs, I would think you would want your foam sheathing to be 1" thick or thicker.
Chart question
Martin
When using the values on the chart that you provided, is it assumed that the cavity in the wall is insulated or not? I'm guessing yes, but would appreciate confirmation.
Yes, assume that the cavities are insulated
Garth,
As you surmised, the chart assumes that the wall's stud bays are insulated.
What about removing the high RH?
I appreciate all that's been said, and agree that a very effective air barrier is what's required in northern climes, to minimize moisture laden air into cold wall cavities. But the real culprit is moisture / high RH. Homeowners need to recognize that it's their responsibilty to keep RH low and stable in winter. Using bath fans, kitchen exhaust and HRV's / ERVs and whatever else to keep RH in the 30% - 40% range, AND a great air barrier should minimize or eliminate all threats to wet walls and roof assemblies. 30%RH in a 68F house is pretty comfortable, not dry feeling. It's the builders /renovators responsibility to provide the mechanicals and the A/B, and the homeowners responsibility to maintain them. The vapor barrier idea has shown it's only in the the right place half the year.
Don't forget basements and crawl spaces
Kevin,
You're right. But don't forget the contribution of basements and crawl spaces to indoor humidity levels. If these spaces are designed and built to stay dry, the indoor air during the winter is likely to be dry as well. If these spaces are poorly detailed and built, they can contribute tremendous quantities of moisture to the indoor air.
Thanks
Thanks Martin - very helpful. I think the DOW SIS has a perm rating of .3 so thought that was a vapor barrier (anything under 1 perm?)
Vapor barriers and vapor retarders
Danny,
Depending on your definition, anything under 1 perm is usually called a vapor retarder, while the term "vapor barrier" is usually reserved for Class I retarders (under 0.1 perm). At 0.3 perm, Dow Structural Insulated Sheathing is a Class II retarder.
The decimal demon gets me again
Under 0.1 not 1.0 - got it. Well - that's good news for me and solves another one of my confusion mysteries. Thanks Martin.
Kraft Paper
I will be insulating the interior of my basement walls with foam board, then building a 2x4 stud wall over it. I know the fiberglass insulation I put in that assembly needs to have no vapor barrier to allow the wall to dry inward, but I am having a difficult time finding the proper material - kraft paper faced batts and rolls is the norm. (When I can find it the cost is two or more times that of faced insulation). What are your thoughts on my attempting to destroy the barrier by making numerous cuts with a razor knife after installation?
Unfaced fiberglass batts
Greg,
I'm surprised that you are having difficulty finding unfaced fiberglass batts.
If faced fiberglass batts are cheaper, simply peel the kraft facing off the fiberglass and discard the kraft facing.
Even better: determine the desired R-value of the wall -- in northern climate zones the minimum code requirement now calls for R-15 basement wall insulation -- and buy enough rigid foam (for example, 3 inches of XPS) to meet your needs. Keep your stud bays empty except for electrical wiring.
yup, it's confusing all right
Martin,
So much of the vapor barrier discussion seems like medieval Scholasticism (“How many angels can dance on the head of a pin?”), which sought to integrate a theology with a natural philosophy, and failed at both. This discussion mixes two very different matters: performance outcomes and prescriptive requirements. There is no assurance whatsoever that prescriptive compliance delivers performance. It occurred to me this weekend that putting in a vapor barrier to prevent “condensation” is much like taking off your shoes at the airport to prevent “terrorism”. (Yes, I removed my shoes.)
Everyone wants good performance. No problem there. Prescriptive requirements are intended as shortcuts to good performance, and they facilitate commerce. They should be allowed to remain in effect only if: 1) their subject is critically important, 2) they are necessary, 3) they are sufficient, and 4) if the link between the prescription and the performance outcome is continually policed. In my opinion, all four are open to question. That said, we might imagine a future in which the building code sections that address the vapor barrier would all go blank. I bet most readers would be able to design excellent buildings that perform well and are quite durable, without using the word “vapor barrier” at any point in the process.
Performance benefits clients and the public. Prescriptions benefit practitioners. Once the benefits of compliance with a prescription (to the practitioner) outweigh the benefits of performance (to the client), an ethical line is crossed.
Thanks for your perspective
Bill,
As you remember — you were there — I attended several of Joe and Betsy's "vapor barrier summits" a few years back, as they were drumming up support for their proposed code changes.
Here's the dilemma: many of the experts that Joe and Betsy assembled were trying to fix something that was broken (vapor retarder requirements in the building code). The experts weren't really starting with a blank slate -- weren't really answering basic questions like, "Do we need to discuss vapor diffusion in the code at all?" or "What's a building code for?"
Ultimately these code changes were political, not technical or scientific. (I know that you don't think the word "science" should ever be applied to building detail recommendations.) The questions were, "What are the worst aspects of this code that need to be changed first?", followed by, "What's politically possible?"
Your posting here is very philosophical, so I'm going to tug at your balloon string and bring you back down to earth. Answer me this: What aspects of the current IRC or IECC can get builders into trouble? How can adhering to prescriptive requirements still lead to screw ups?
prescription
Martin,
You recall correctly—I have been in support of Joe Lstiburek’s efforts to tweak the prescriptive requirement so that it at least permitted good performance outcomes, even if it didn’t force them. Joe, incidentally, doesn't support taking the next step which I suggest above, of calling the prescriptive measure itself into question. It is primarily in retrofit insulation where a prescriptive requirement for a vapor barrier becomes a horror (and where Joe might well agree). Retrofit really should be done with performance analysis and estimates. Face it, we're prescription junkies.
vapor barriers
did I miss anyone talking about vapor barrier primer paint? I like it because it eliminates a step in the builiding envelope contruction, is an unbroken barrier and is inexpensive- I use it as the pre texture primer step.
It keeps the moisture on the surface of the rock, not allowing it to stop at insulation or plastic.
You might have missed it...
Dave,
In the answer to the question about building codes, I wrote, "This [code] definition [of a vapor retarder] includes such materials as polyethylene sheeting, aluminum foil, kraft paper facing, and vapor-retarding paint."
You're right, paint works fine. Benjamin Moor Moorcraft SuperSpec Latex vapor retarder primer 260 is one brand. Most vapor-retarding paints produce a dried film with a permeance of about 0.45 to 0.90 perm.
By the way, don't worry about whether or not your vapor retarder is "unbroken" -- a vapor retarder that covers only 90% of a surface (in other words, with 10% defects) is still 90% effective.
Your understanding of the function of a vapor retarder isn't quite accurate. Vapor-retarding paint doesn't "keep the moisture on the surface of the rock, not allowing it to stop at insulation or plastic." All it does is slow down the rate of diffusion. But that's all you need. There is no moisture "on the surface of the rock." However, the moisture content of the drywall will reflect the indoor relative humidity. Since "the surface of the rock" should always be at the indoor temperature, there shouldn't be any concerns about high moisture or condensation on that surface anyway.
Like kraft paper, vapor-retarding paint will allow moisture to diffuse through the drywall. If it encounters a cold impermeable surface inside the wall, the moisture could still condense. However, as the article points out, not much moisture moves by diffusion anyway, so the entire discussion is moot. All we really need to worry about are air leaks.
Brick Buildings
Martin,
Most of the information that I have found addresses wall assemblies for wood buildings but how, if at all, would your recommendations change if you are dealing with a brick building? I am doing a retrofit of a brick row home in Philadelphia, pretty representative of your typical Mid-Atlantic and North-East row home, and am currently thinking of insulating the walls with 2" exterior XPS (tape all seams and add a rain screen and cladding on the exterior, we can only extend the facade 4") and then 5" interior cellulose (frame with 2"x4" studs 1" off of the wall, covered by drywall on the inside and re-framing and installing new high-performance windows and doors) then 8" exterior ISO on the roof and 8" of cellulose in the basement ceiling. We are getting some pushback by architects and tradespeople that don't like the idea of sandwiching the brick but if we are removing interior moisture through a ducted ERV and properly seal and caulk the exterior, do you see any problems with this approach? Do you have any alternative recommendations?
Regards,
Mark Hutchinson
It sounds like your approach will work
Mark,
It sounds like your approach can work, but there are many details that could potentially trip you up if they are not executed well. Exterior flashing details and rainscreeen details must be carefully thought out, as well as potential thermal bridging at the wall / roof intersection.
I strongly advise you to read "Insulating Residential Masonry Buildings In Cold Climates" by Chris Benedict (in the the current edition of Home Energy magazine, March / April 2010). You may also want to consult with Chris Benedict.
interior poly and "old-house" smell
An interior poly seems to prevent the diffusion of smells already existing in the wood structure.
When renovating an old home (gypsum board replacement) should I use poly? Is there another method to prevent the diffusion of smells? House is in zone 4 border with 3 (Southern PA).
My dilemma is that If I also use an outside insulating sheathing I may create a vapor trap inside the wall resulting in the wall not being able to dry in any direction.
Response to Adrian
Adrian,
As far as I know, if you create an airtight barrier, you won't smell anything on the other side of the barrier.
Interior polyethylene is not recommended in your climate. I suggest you install your new drywall using the Airtight Drywall Approach (ADA).
If your home has a forced-air heat distribution system (a furnace), you might consider installing a central-fan-integrated supply ventilation system. Such a ventilation system will slightly pressurize your house, reducing the likelihood that smelly air from your wall cavities will ever reach your nose.
Vapor Woes
I can't decide what I need for a vapor barrier in my walls. Conflicting information is everywhere. I am re insulating my older home from the inside (2x4 walls, R13 craft faced batts).
I am in zone 4, close to zone 5 (Baltimore). I don't cool my house more than 79F in the summer if I use the AC at all.
Coming from Canada, I am tempted to use polyethylene on the interior. Is this a bad idea?
Response to Miles
Miles,
Yes, it's a bad idea. If you (or a future resident) runs an air conditioner, moisture can condense on the outside of the polyethylene and rot your walls.
1. I advise you to consider installing a more effective insulation than fiberglass; for example, cellulose.
2. Whatever insulation you choose, install your drywall following the Airtight Drywall Approach (ADA). This requires gaskets or caulk between the drywall and the bottom plates, as well as between the drywall and the top plates. All electrical boxes should be carefully air sealed.
If I have airtight walls,
If I have airtight walls, won't the moisture condense on the cold side, regardless of whether it is plastic, drywall, foam, or other? Since there is no vapor barrier on the exterior of the house, shouldn't the moisture evaporate to the outside?
Response to Miles
Miles,
You wrote, "If I have airtight walls, won't the moisture condense on the cold side?" What makes you think that airtight construction promotes condensation? The opposite is true. Leaky walls promote condensation, since exfiltrating air carries moisture that can condense on cold sheathing. The solution to this problem is air sealing.
In the article on this page, I wrote, "The main mechanisms by which moisture enters a wall are from the exterior (usually due to flashing defects that admit wind-driven rain) and via air leaks that carry “piggy-backing” moisture that condenses in a wall cavity. Vapor diffusion is a relatively insignificant cause of moisture problems in walls."
You are worried about vapor diffusion, but your worry is unnecessary. Vapor diffusion from the interior toward the exterior is not a problem -- especially in your climate. Air leakage is, so try to address air leakage.
If any moisture does accumulate in your wall (and it shouldn't), it will dry readily -- to the exterior in winter and to the interior in summer.
Thanks Martin. I must admit
Thanks Martin. I must admit that this is a rather confusing issue. If I understand correctly, condensation on the exterior side of air conditioned drywall is less of an issue that we've been lead to believe. If that's true then it makes sense that simply reducing or eliminating air movement through the walls would be beneficial.
Condensation on cold drywall
Miles,
It's impossible for moisture to condense against cold drywall, as you fear, since drywall is hygroscopic. If drywall gets damp during the summer because of inward solar vapor drive, the drywall will dry readily to the interior.
While it's impossible for condensation to form on cold drywall, it is possible for condensation to form on cold polyethylene. Hence the rule: Never install interior polyethylene or vinyl wallpaper in an air-conditioned house.
To learn more about summertime condensation in air-conditioned homes, read When Sunshine Drives Moisture Into Walls.
All the talk is about walls but I assume this holds for ceilings
I have to agree with Miles, every time I think I understand the issue of vapor barriers I read more that makes me question what I read before. We are on border of zone 4and 5. While all the conversation keeps mentioning walls, sheathing, rigid insulation, rain shields, etc. I assume the message is the same for ceilings. My project is a masonry load bearing structure with masonry veneer and a wood truss roof structure. We are proposing to use a spray vapor barrier on the outside face of the block then 3 inches of rigid (c.i.) to avoid moisture hitting dew point in wall, air space and then brick veneer. At the ceiling, I was going to put polyethylene behind drywall covered with 15" of blown in cellulose. To deal with ceiling to wall issue we were going to use peel and stick vapor barrier (ice and water shield) to top of wall over wood plate and on to bottom of trusses then stick poly to it. Sounds like I should pull the poly out and avoid the peel and stick. Right?
Response to Blue Fan
Blue Fan,
If MI means Michigan, I'm not sure how you can be between Climate Zones 4 and 5. According to the DOE Climate Zone map, Michigan is divided into two climates zones: zone 6 to the north and zone 5 to the south.
In Michigan, you don't need ceiling poly, although the poly is unlikely to cause any problems if your attic is well ventilated. One problem with ceiling poly is that it can hold a lot of water in the event of a roof leak. You would probably be fine with vapor-retarding ceiling paint. Of course, your ceiling drywall should be installed in an airtight manner -- no can lights allowed!
You don't need a complicated vapor barrier connection (liek peel-and-stick) between the rigid foam on your wall and your ceiling -- but you DO need insulation over the top of your block wall. You need to be sure you have a continuous thermal barrier connecting the top of your wall foam with your cellulose layer in the attic. I think this might be a good place for spray polyurethane foam -- perhaps a HandiPack or two.
Mixing Barrier Free Walls with Barrier Inclusive Walls
Hello Martin.
I appreciated this timely discussion as I am faced with a rather unique project right now that needs some vapor barrier solutions. We are building a 4000 square foot, traditional Japanese timber frame (that part already done - see http://www.harvesthaven.com for pictures) with light straw/clay walls a la Econest system and conventionally framed gables and roof right now in Southern Alberta, Canada.
We have found straw clay walls to be brilliant because they are completely breathable and the clay coating on each strand of straw protects the straw from moisture as well as giving the wall incredible moisture storage and capillary action when needed and resolves so many problems talked about in this forum. They are hard to build for gables though and the same system can't be used for roofs. So..., we need to come up with a congruent wall system for the gables and roof using conventional insulation products. The gable walls will match the straw clay walls at 1 foot thickness and the roof is being built upwards from a 2x6 T&G decking on top of the timber beams. In the wall, we are planning to use Rock Wool Batt at about R40 value and a heavy poly air barrier with acoustic sealant on the interior side (as per Canadian Code) which will be dry walled on the interior and sheeted with 1/2" plywood on the outside which will then receive a lime plaster. I am worried about inward solar vapor drive though, especially with a lime plaster stucco on the outside. There is no one around here that even considers this however. What are your thoughts? I could leave a sizeable air gap/ventilation gap on the exterior of the wall being I have 1 foot to work with.
Regarding the roof, we are looking at insulating with Icynene open cell insulation (like the breath-ability of the product - thoughts please!) at about R30-40 value. This will be sprayed directly onto either a poly eth air barrier (or "vapour barrier" as even the building inspector calls it) or peel and stick membrane that will be applied directly to the T&G decking, filling in between the 2x10 sleeper rafters part way up and then there will be a 4+ inch air gap left on top of that with cross ventilation between the cavities facilitated by the 2x4 strapping on top of the sleeper rafters on top of which 22 gauge standing seam roofing will be applied. The roof will be ridge vented and we are searching for a breathable yet water shedding membrane to be applied under the metal roof to keep condensation and/or perish the thought, a roof leak, from going into the open cell insulation below. What are your thoughts on this system? We have huge temperature swings here in the winter and summer. We can go from -30 degrees C to +10 degrees C in one day here in the winter and almost have the same variance in the summer.
The building has in-floor hot water radiant heat and an HRV unit but no air conditioning.
Any thoughts or advice would be GREATLY appreciated.
Thanks,
Mark Benson
Response to Mark Benson
Mark,
Inward solar vapor drive shouldn't lead to problems if there is no air conditioning. However, your house will outlast the current residents, and air conditioning might be added in the future. In your climate, I don't think interior poly on the walls will lead to problems, but the climate is changing. You would be safer with MemBrain instead of interior poly.
Your roof sounds fine.
Straw/clay and Conventional Mix
Thanks for the comments and consideration Miles.
After posting, my brain was turning. While there is no air conditioning, speaking from the experience of our straw/clay home we built last year, it stays almost air-conditioned cool in the summer on its own and thus my concern about inward solar vapour drive. In contemplating the 1 foot wall cavity available in the gables, my brother and I came up with a plan to vent the conventional wall cavity in through a hip roof that joins the building at the junction of the straw/clay top plate and where the conventional insulation starts, which will vent up and into the soffit and ridge venting on the roof, ... just in case.
In reading all your dialogue, if I may say, it seems that straw/clay construction (where the walls are more simple) solves all the problems discussed! I guess the centuries of anecdotal examples of such structures surviving mold free in a variety of climates bears witness of that as well. For anyone out there interested in knowing more about that option, you can look at our farm's website where we are slowly recording the building process and what we are learning at http://www.harvesthaven.com.
Thanks again,
Mark
Vapor Retarder?
Hi Martin,
I'm about ready to re insulate and am convinced by your article that no vapor barrier should be present however, what about craft faced insulation? Is there any real harm there? The ADA guide says even polyethylene vapor barrier can be used on exterior walls.
Response to Miles latest question
Miles,
1. You can use kraft-faced fiberglass insulation if you want. The kraft facing won't cause any problems.
2. Interior polyethylene should never be used in an air-conditioned home.
Thanks Martin ^_^. This site
Thanks Martin ^_^. This site has been invaluable.
vapor barrier
We are renovating an existing room, installing new windows, have taken out the old fiberglass insulation because of previous moisture and mold issues. We are thinking of using ROXUL insulation. The room is over a crawl space, there is whole house AC and an April Air dehumidifer in the basement. The house is in Eastern Long Island in New York which can be a damp enviornment. The exterior is board and batten with plywood sheathing and 2x4 studs. Do you think a vapor barrier is needed and or is a good idea on the interior over the studs in use with the ROXUL?
Thanks
Response to Marge
Marge,
Vapor-retarder paint is all you need. Don't install interior polyethylene. If your building inspector insists on a vapor retarder that comes in a roll, use MemBrain.
If possible, install the drywall following the Airtight Drywall Approach to limit the flow of interior air into your stud cavities.
New house in South Carolina
I am building a new house in SC and am curious about vapor barriers. Most of the discussion above seemed to focus on northern zones. Our external sheathing is OSB, tyvec, and Hardieplank. The attic has ridge vents. If I understand the threads correctly, it sounds like I should not use vapor retardants/barriers on the inside, but it would be ok (and probably advisable) to use the ADA. Any good refs to the ADA? Thanks.
Response to Jim
Jim,
You are correct that in your climate, ordinary latex paint applied to your drywall is enough of a vapor retarder to meet your needs. You should certainly not install any polyethylene on the interior of your walls.
It's always advisable to minimize air leakage in your home, and the Airthight Drywall Approach (ADA) is one way to do that. Here are some links to get you started:
http://www.finehomebuilding.com/how-to/departments/energy-smart-details/airtight-drywall.aspx?ac=fp
http://web.archive.org/web/20071010050059/http://www.southface.org/web/resources&services/publications/factsheets/24ada_drywal.pdf
http://www.energysavers.gov/your_home/insulation_airsealing/index.cfm/mytopic=11310
tyvec and external sheathing
Martin,
Thanks for the links. I learned a lot from the gov site. From inside the house, I can see that the external 7/16" sheathing has horizontal gaps of 1/16-1/4" between the sheets. These gaps are covered with a continuous layer of tyvec on the exterior. Do I need to caulk these gaps to establish an airtight wall, or does the tyvec accomplish that?
Response to Jim
Jim,
Q. "Do I need to caulk these gaps to establish an airtight wall?"
A. No, you don't need to caulk the gaps.
Q. "Does the Tyvek establish an airtight wall?"
A. No, just because you have Tyvek doesn't mean you have an airtight wall.
If you want to establish an air barrier at your exterior sheathing, it's best to tape the seams between your OSB or plywood panels. This work has to be done from the exterior, at the time of construction, before housewrap or siding are installed. Read more here:
Airtight Wall and Roof Sheathing
One Air Barrier or Two?
Although some builders have experimented with trying to use Tyvek as an air barrier, the results are not as good as when the air barrier is created at the sheathing level.
Foam in Michigan
I am curently building a 3300 sq ft home in Michigan. I put 2 inches of Extruded on the outside, then tyvek, then an air space, then face brick. My question is what type of insulation should I use on the inside, and do I need a vapor barrier. Any help would be appreciated.
Response to Wally
Wally,
Your R-10 foam insulation may or may not be enough to keep your sheathing above the dew point; it depends on whether you are in Zone 5 or 6, and whether you have 2x4 or 2x6 walls. As long as you don't have 2x6 walls in Zone 6, you should be OK. See Calculating the Minimum Thickness of Rigid Foam Sheathing for more information.
I would recommend that you install dense-packed cellulose, not fiberglass batts, in your stud bays. Cellulose does a better job of filling gaps and odd-shaped cavities than fiberglass batts, and does a better job of reducing air leakage rates.
No, you don't want a vapor barrier. All you need is a vapor retarder.
Stuck in indecisiveness mode
I have a old home (1923) in Portland, OR with a basement that was finished by a previous owner. The basement doesn't have the complete footprint of the main floor. Under one of my main floor bedrooms there is an unvented crawlspace which until last week has not been insulated. I used unfaced fiberglass bats (R-30) in between the joists. I am now wondering if I should lay a layer of vapor barrier (i.e. 6 mil plastic) on the floor of the crawlspace to further insulate. How about a vapor barrier over the concrete walls of the crawlspace (i believe the walls are technically called the footing or the foundation of the house)? The bedroom always felt cool and damp to me so i thought it would be a good idea. Would using a faced insulation draped over the walls be a better idea for controlling moisture?
Response to Ken
Ken,
The best way to detail a crawl space is to close all vents permanently, to install a vapor barrier on the dirt floor, and to insulate the crawl space walls. This creates a sealed conditioned crawl space. You can read more here:
https://www.greenbuildingadvisor.com/green-basics/crawl-spaces
However, you have chosen to insulate between the joists, so it's a little late. I hope you installed a rigid material under the joists (plywood, OSB, or rigid foam) to protect the fiberglass batts.
Yes, you should certainly install a layer of 6-mil plastic on the floor of your crawl space. This poly won't help insulate, but it will reduce the evaporation of moisture into your crawl space.
If you choose to insulate your crawl space walls, don't use fiberglass batts. Use rigid foam (XPS, EPS, or polyisocyanurate).
Thanks Martin for the reply.
Thanks Martin for the reply. Im curious what purpose the "rigid material under the joists" serve? And when you say "under the joists", you mean between the floor boards and the fiberglass bats correct in which case, yes it would be too late as the insulation is hung, but not a huge job to take it down and re-do since its only a 13'x8' area.
What means is available to hang rigid foam to concrete walls?
This website has been a great find! Thanks for all your help.
Second response to Ken
Ken,
If you installed fiberglass batts between the floor joists that form the ceiling of your crawl space, then the batts are exposed on the bottom. Over time, some of the batts will fall out or hang down; some will begin to get damp and grow mold; and others will be damaged by rodents.
Home inspectors see such conditions all the time in existing crawl spaces.
If you install a layer of plywood, OSB, or foil-faced rigid foam across the underside of the floor joists, you will protect the fiberglass batts and make it less likely that they will fall down.
If you decide to install rigid foam on the walls of your crawl space, the foam can be attached to concrete walls with foam-compatible adhesive. It can also be attached with concrete fasteners like Tapcons.
Seattle wall assembly
I'm working on a project in the Seattle area, and the wall assembly is as follows: 5/8" drywall, Certainteed Membrain VR, 5.5" R-21 unfaced fiberglass batts, 7/16" OSB Zip System, 1' rigid xps, 1/2" air cavity and cladding. Do we need the membrain or will latex paint suffice? Also, would cellulose insulation be a better choice due to its hygroscopic capacity, etc? There will be HRVs, and it's possible that some units will opt for mini split heating/cooling systems. Is 1" rigid enough? Is 2" the "right" amount?
Response to Green Builder
Green Builder,
Many of your questions are answered in an other article: Calculating the Minimum Thickness of Rigid Foam Sheathing.
You are in Climate Zone Marine 4. Since you have 2x6 walls, your foam sheathing should have a minimum R-value of R-3.75. Since you are using XPS, with an R-value of 5, you are fine.
You don't need MemBrain; your interior paint will suffice.
Dense-packed cellulose will perform better than fiberglass batts, because it does a much better job of filling odd-sized cavities.
Vapor Barriers
I amin the Philadelphia area. I have been ripping apart residential dwellings over the past 30 plus years. Moisture seems to form from obvious condensation and do damage toward the exterior of the building and this is evidence of condensation. I have seen less of a problem on open wall cavities where on these older homes, an almost complete permeance was available and especially toward the exterior. These buildings usually have clapboard and the exterior vents much more than the interior plaster walls. I agree this is rare but it does happen and usually an interior humidity problem is evident.
I have seen many homes where the newer paints are being used, moisture is migrating through to the outside to condense on the high quality paint that forms a seal around the building. Water bags are the result. In the same communities and with the same construction I have seen the same type of home stained with no issues. The stain leaves the venting properties of the wall intact. I have also seen the use of spacers under the clapboard installed before the painting and with no issues. I have opened up walls to find the evidence of condensation on or near the exterior of the building. The "water bags" are very common in this area.
All of these situations and all of these examples (and I have hundreds) lead me to believe that in this climate, a barrier should be present on the interior of the building. I also believe the so-called "permeable" housewraps act as functional vapor barriers on the exterior of the building in this climate (when it is cold).
When the moisture migrates past the interior in the winter and into the walls or attic, mold can be found being fed by the moisture.
Sprayed polyurethane foam in cold climates
Hi, I live somewhere when it gets very cold and dry in the winter (normal for January is approximately -10 C). and hot and humid in summers. So the vapor can goes both ways. My foundations are not damp proofed actually. What do you think of a material that has 0.3-0.5 perm on the interior side? Can it cause capillarity and potential damages to the sill plate if there is not a capillarity barrier betweed the foundation and the sill plate? Thank you.
Not enough information, Philippe
Philippe,
Knowing the permeance of a material is not enough information to determine whether its use is appropriate for installation on the interior side of a foundation. So please tell us:
1. What type of foundation is it? Stone and mortar? Brick and mortar? Poured concrete?
2. Is it a crawl space or basement?
3. What is this material? Is it an insulation? A vapor retarder? Wallpaper?
The problem of sill rot due to capillary action is a different problem than determining the best permeance for finish materials installed on the interior side of your foundation wall.
Concrete and 2x6 exterior wall.
I have a basement that I am finishing. The bottom portion of the wall(below grade) is concrete with a 2x6 wall9above grade) on top of it. The 2x6 wall is filled with insulation and covered with poly. I have covered the concrete with XPS and built a full 2x4 wall in front of that. I will be putting unfaced batts in the 2x4 studded wall. Should I remove the poly from the 2x6 portion and then make sure that insulation also fills the void that is created between the 2x6 and 2x4 walls. I know that I want fiberglass in front of the XPS but don't know what to do above the concrete. Please advise. I should mention that I am in zone 6, North Dakota.
Response to Gregory Erickson
Gregory,
Q. "Should I remove the poly from the 2x6 portion and then make sure that insulation also fills the void that is created between the 2x6 and 2x4 walls?"
A. Yes.
Q. "I know that I want fiberglass in front of the XPS."
A. I usually advise people to avoid the use of fiberglass below grade. In general, it's almost always better to add a thicker layer of XPS (or another type of rigid foam) and to skip the fiberglass completely.
In your case, since the wall is already built, it's probably OK to proceed as you have planned.
Will I need a vapor retarder
That is what I will do. When the wall is finished should I use a vapor retarding paint of will a normal paint and primer suffice? Thank you!!!!
Paint question
Gregory,
In your climate, which is quite cold, it's probably best to use vapor-retarder paint. Be sure to pay attention to air sealing when installing your drywall, especially around electrical boxes. Air tightness is even more important than the vapor-retarder paint.
air sealing
Thank you Martin!
What extra methods do I have to do when hanging the drywall to make it as air sealed as possible.?
Airtight drywall
Gregory,
Follow the Airtight Drywall Approach. You can Google those three words for more information, or you can read an article I read on the topic. Here's the link:
http://www.finehomebuilding.com/how-to/departments/energy-smart-details/airtight-drywall.aspx?ac=fp
West coast marine climate vapor barrier in crawl space
The walls in my crawl space are 2 feet of concrete block below and just a bit above grade, with two feet of wood framed wall above. There is a concrete floor and the area is considered part of the house. The exterior is painted cedar over 'tar paper' and then plywood. I have caulked the interior around the frame and siding, and insulated with Roxul bats. The house is on Vancouver Island: maritime cool wet winters, warm summers. Do I need to use a vapor barrier (polyethylene) and/or air retarder? Which or both? (I found after reading this article and others that I wasn't sure of what would be best.)
Also, has anyone used double sided tape to apply polyethylene vapor barrier to wood framing? I don't like the petrochemical smell of acoustical sealant and since it does not dry, adds to indoor pollution (unless covered with gyproc, which I don't plan to use in a crawl space).
Response to L. Buser
L Buser,
You don't want to install an interior polyethylene vapor barrier, for the reasons mentioned in this article. Instead, use vapor retarder paint or a smart retarder like MemBrain.
You always need at least one air barrier. In your case, I recommend that you follow the Airtight Drywall Approach. For more information, see:
Airtigtht Drywall
Questions and Answers About Air Barriers
Is it the same for a concrete block wall?
Thanks for your reply to my earlier question.
My basement has a 3.5-foot high concrete block wall, with a standard framed wall above. The concrete block is currently finished with 2x4 framing, fiberglass insulation and poly vapor barrier covered with gyproc, which I know is not what is recommended but that is how we bought the house. I want to change it to solid foam insulation as recommended, with slats or 2x3 and gyproc.
Since concrete blocks are more porous than poured concrete, and since there are the indented spaces along the mortar joints , would those pose any problem with using solid foam, taped and sealed? My concern is the highly porous nature of concrete blocks and the air gaps. The exterior has black sealant and good drainage.
Also would using the metal fasteners possibly crack the concrete blocks or mortar joints and should I avoid using those and just use adhesive?
Thanks.
Response to L. Buser
L. Buser,
Q. "Since concrete blocks are more porous than poured concrete, and since there are the indented spaces along the mortar joints, would those pose any problem with using solid foam, taped and sealed?"
A. No. Just be sure that each piece of rigid foam has a strong bead of adhesive around its perimeter, to provide an air seal. In addition, you should tape the joints of the rigid foam with a high-quality tape. The easiest type of foam to tape is foil-faced polyiso.
Q. "Would using the metal fasteners possibly crack the concrete blocks or mortar joints and should I avoid using those and just use adhesive?"
A. As far as I know, you can use Tapcon fasteners on concrete block walls. These require pre-drilling. But frankly, I've never used Tapcons on concrete blocks; so if I were you, I would verify this information with your fastener supplier.
If you want to use adhesive only, you can. However, be prepared with a pile of plywood scraps, 2x4s and braces to provide pressure for several hours after the foam is installed.
Vapor barrier in garage recording studio
Hello--this is a wonderful forum--thank you!
I have what I think is an unusual situation, and I hope that I haven't made an error that I can't recover from.
Here is a quick description of my building: it is a garage that I 'm converting to a recording studio, and one of the unusual aspects of the construction is that it is a "room within a room" design, meaning that there is an entire building structure built inside the outer shell of the building, with a 2" gap separating them. The outer and inner shells do not touch anywhere, and the reason for this is that the sound isolation is much more effective that way.
The outer shell has cedar siding, 15# siding felt, yellow Dens Glas sheathing over the 1910 era 1x8 sheathing, and then finally 5/8" drywall attached to the inside, between the studs. All of this additional sheathing is necessary to give the structure more mass, and make it less prone to transferring noise. Between the studs of the outer shell is R13 fiberglass unfaced insulation.
The inner shell is unusual in that it is framed inside-out. in other words, the drywall is facing the outside of the building, while the studs are facing inside. It is built this way to save space in the narrow room, as necessary acoustical treatments can be installed between the studs, making the room "sound" better without sacrificing interior space. The walls are built on the floor and then tipped into place.
The vaulted ceilings of the two shells are built as follows: The outer shell ceiling has two layers of 5/8" drywall covering r-21 fiberglass unfaced insulation. The roof framing is scissors trusses, and there are soffit vents running the length of the building, along with a ridge vent. The inner shell ceiling has two layers of 5/8" drywall over r-19 unfaced fiberglass insulation with a poly vapor barrier.
So finally, here's my question: as you can see, this construction method in unusual, and I got confused about where the vapor barrier for the walls should go. I built the inner shell without a VB behind the drywall and I have no way of getting it in there now. After reading this forum, I'm not even sure if I should have it. Would it make sense to paint the entire inner wall, framing, drywall, and all, with a Vapor barrier paint? I should mention that all the seams, holes, etc, have been caulked prodigiously with acoustical caulk. The inner space, while sealed extremely well, will have an air intake with an in-line fan and silencer along with an exhaust vent with a silencer at the opposite end of the room, high on the wall. This system moves fresh air into the room quite efficiently, and is necessary, since the construction is so air-tight. I will also have a mini-split heat pump in this space that will be used for heating and ac. I'm in Seattle, so ac doesn't get used a lot, but with a room full of hot, sweaty musicians, it will.
Thank you in advance for reading this lengthy post. I hope you don't tell me I have to tear walls down!!
Response to Mark Nelson
Mark,
Your post was long, and it took a while to glean the important information. As I was reading it, I was thinking, "What's the climate?" You finally told me, near the end: Seattle.
As you probably know, airtight details matter more than vapor barriers. It appears that you have paid close attention to air sealing, so that's good.
You don't need any polyethylene vapor barriers in your climate. Polyethylene vapor barriers can cause problems, especially in buildings that are air conditioned. As far as I can tell, you installed a polyethylene vapor barrier in your roof assembly, but not your wall assembly.
Was that polyethylene vapor barrier a good idea? Probably not. Will it cause any problems? Probably not (especially because you have ventilation from your soffits to your ridge vent).
You didn't mention whether you installed any baffles to create an air barrier above the unfaced fiberglass batts in your roof assembly. (These baffles would separate the insulation from the ventilation channels.) Such baffles would have been a good idea.
Now that everything is built, I wouldn't worry about anything. My guess is that everything will be fine.
Response to Martin Holladay
Hi--
Thanks so much for your response. Yeah, I know it was long--sorry about that--I just thought there was a lot of information I needed to impart to give an accurate picture of my unusual construction.
To answer your question about baffles, since the roof has scissors trusses, the only area where there would be danger of blockage of the vents would be right near the soffits at the bottom of the roofline. I installed chicken wire (not very elegant, but effective) to ensure that the insulation didn't block the vents, so I'm confident that the air will move freely.
I wish I had learned about this site before I installed the vapor barrier in the ceiling of the inner shell, but I guess there's not much I can do about it now, short of tearing out a double layer of drywall. My reasoning with putting the barrier in the ceiling of the inner shell was that any moisture that got through the inner shell would also have to get through the outer shell above it before it was vented through the ridge vent above that. I thought with the vb and the fresh air circulation through the inner room I could keep moisture from collecting between the two shells. That was my reasoning, anyway.
Anyway, unless you have any additional opinions about this, I guess I'll stop losing sleep over it.
Thank you, Martin, I really appreciate your input!
And one last question for Martin...
I have one section of the inner ceiling shell that I have not yet covered, which is about 45 square feet out of 250 square feet of total roof area. I'm assuming I should just leave the VB off of this section, unless there's are reason I should install it since the rest of the inner shell does have a VB. any thoughts on this?
Thank you!
Response to Mark Nelson
Mark,
Don't install any polyethylene.
Response to Martin Holladay
Ok--I will steer clear of the poly from here on out. Thank you for the advice.
help
I have been researching like mad to find an answer to my specific room problem. I just added a small bathroom to a house in Iowa that was built in the late 80's. Plastic vapor barrier was installed before drywall in outside walls and ceilings when the house was built new. My question is this: Would it be better to omit the vapor barrier in the remodel, especially the ceiling of the new bathroom so as to keep water from permeating the ceiling sheetrock, getting stuck between the sheetrock and vapor barrier and staying wet forever? This house has a vented attic space. Is the above blog/article suggesting that vapor barriers in my climate are now not preferable? I am dying to know the answer.
Response to Andrew Gross
Andrew,
Q. "Would it be better to omit the vapor barrier in the remodel?"
A. Yes. There is no need for interior polyethylene in your climate. Of course, it is vitally important that you pay attention to airtightness when you build the addition.
Q. "... especially the ceiling of the new bathroom so as to keep water from permeating the ceiling sheetrock, getting stuck between the sheetrock and vapor barrier and staying wet forever?"
A. Moisture can't get "stuck" between your ceiling drywall and the polyethylene. During the winter, your indoor environment will be different from the outdoor environment. The interior will be warm and humid, while the exterior air will be cold and dry. That's normal. The moisture contained in the interior air should stay put. As long as you pay attention to airtightness when you build your ceiling, there won't be any air leaks through the ceiling that can carry moisture. The amount of moisture that moves through the ceiling by diffusion won't be enough to worry about, as long as you have an adequate layer of insulation, installed carefully. If the insulation is air-permeable (like fiberglass), you'll need ventilation above the insulation layer. If the insulation isn't air-permeable (for example, spray polyurethane foam), then you won't need any ventilation above the insulation layer.
thanks
Thanks for the above thoughtful response. You stated that I need to "pay attention to airtightness when you build your ceiling..." I have a bath fan and 4 IC can lights in this bathroom remodel. Are you suggesting I do something to seal those???
Also, I have already applied two coats of vapor retarding paint/primer to the ceiling of this bathroom just as additional info.
Thanks again. I feel like I am finally on a path to get this bathroom done. I have already installed the plastic vapor barrier and the drywall is finished. Based on your comment above, I plan to remove it from the attic side. I only installed it because that's how it had been done before (construction in the late 80's).
I just need to know if I need to do anything with the bath fan and can lights.
Thanks!
Thanks again!
more info
Martin,
Did you have any thoughts on my last post in response to your reply to me?
Thanks!
Response to Andrew Gross
Andrew,
Most green builders who pay attention to airtightness avoid the use of recessed can lights in an insulated ceilings. These fixtures are notoriously leaky; they take up room in the ceiling assembly that should be filled with insulation; and they create "hot spots" which accelerate the stack effect and ice damming problems.
You have two choices:
1. You can remove the can lights now, before it's too late, and repair the holes in your drywall ceiling. Then install surface-mounted fixtures instead.
2. You can learn to live with the recessed can lights, and their energy penalty, and you can do your best to repair the damage from the attic side. If you go this route, you should encapsulate each can light in an airtight box made of drywall or rigid foam. These boxes must have all seams carefully sealed with high-quality tape or canned spray foam. Each box needs to be sealed to the drywall from above. The boxes need to be large enough to provide several inches of air between the box and the recessed can. Then pile insulation on top of the boxes.
Carefully seal the crack between the drywall and the exhaust fan housing with high-quality caulk.
Insulation in Zone 5
I am located at the northern end of NJ. Zone 5 according to the map.
For a upstairs add-a-level project (new 2nd floor and attic), is the following flash and batt ok?
3 in of closed cell spray foam in attic, 1inch of closed cell spray foam in walls, with fiberglass batting
Additional information:
* wood construction
* standard shingles
* standard siding - though a question is, do we still need rigid foam board on the outside with the closed cell foam on the inside?
* this would result in an unvented & insulated attic space. The floor of the attic would be left uninsulated so that it is within the rest of the building envelope.
I have a constructor lined up but I am concerned because the insulator would not provide any sort of guarantee. I couldn't figure out what the dew point would be.
Alternative is to go with standard vented attic with fiberglass in the floor of the attic. Tried and true and crappy...
Thank you!
Response to Harry Shoe
Harry,
Your plan will work. According to the building code, the type of unvented roof assembly that you are planning to install will only work (in your climate zone) if you have a minimum of R-20 of foam above your air-permeable insulation. Three inches of closed cell spray foam will give you an R-value of close to R-20, so you'll be OK.
As far as I know, most states impose guarantees on the work that contractors perform in homes. Even if your contractor says that he can't provide a guarantee, state law probably requires him to do so.
For more information on this type of insulated roof assembly, see Creating a Conditioned Attic.
Is polyethylene vapour retarder needed in northwest coast home?
Lots of interesting comments here. Thanks folks. I have a stick frame old house (over 100 years old) with wood shakes and siding. The walls are in great shape after over a century of no vapour barrier and no insulation. We are renovating. We have installed fibreglass insulation in the exterior walls. Given our moist (living close to the ocean) and temperate climate (never gets very hot or very cold) and not needing air conditioning, With lots of cooking and showers, we have condensation inside the double glazed windows during the winter. Is it healthy for our house to have polyethylene on over the insulation installed over the fibreglass insulation on the interior side of the wall? I'm wondering about rot and mold in the walls.
Response to C. Calderwood
Q. "We have condensation inside the double-glazed windows during the winter. Is it healthy for our house to have polyethylene on over the insulation installed over the fibreglass insulation on the interior side of the wall?"
A. The condensation on the interior side of your windows during the winter is a symptom of a problem. The solution has nothing to do with polyethylene in your walls.
Your interior relative humidity is too high. That's why you are seeing condensation. You need to lower the indoor relative humidity. The easiest way to do this during the winter is to increase your ventilation rate. If your home doesn't have an HRV, you can begin by running one or two of your bathroom exhaust fans for 24 hours a day until the condensation goes away. Then you can ventilate for fewer hours.
Once you've done that, it's time to find out why you have so much indoor moisture. The usual culprits include a wet basement or crawl space, too many houseplants, wet hobbies (like having many fish tanks), storing firewood indoors, drying clothes on indoor racks, taking lots of showers, and doing lots of cooking.
Some of these issues can be addressed by fixing problems (especially a wet basement or crawl space). Others involve habits that you may not want to change. If you are unwilling to reduce the indoor moisture load, you need to increase your ventilation rate.
High indoor humidity can definitely cause moisture problems in your walls, so you will be doing your house a favor by getting your interior RH under control. In your climate, I do not recommend the use of interior polyethylene, for all of the reasons stated in the article on this page.
Healthy Home Humidity
Hi, We have a humidistat connected to our ventilation. We can set the percent of humidity we want to try to maintain. What percent humidity is healthy for a wood frame house with fibre glass insulation in the exterior walls and painted wood exterior siding?
Response to C Calderwood
C Calderwood,
It makes sense to aim for 20% to 40% relative humidity during the winter, and 60% during the summer. Remember:
1. You can't use ventilation to lower the indoor relative humidity during the summer. Ventilation only works for that purpose during the winter.
2. Many humidistats and humidity meters are poorly calibrated. If you still have condensation on your windows, your indoor RH is still too high, no matter what your meter says.
3. You still need to identify the source of the moisture in your house and rectify the underlying problem.
Bathroom in Sunny South Carolina Vapor Barrier
Great information! I live in South Carolina. I am re-doing my bathroom tile. I have Kraft faced insulation on the exterior inside wall, and am going to put up Hardie backer board over it.
There is a lot of conflicting information on the Internet. Most tiling forums suggest putting up a vapor barrier behind cement board, with the requirement to slit the Kraft faced insulation. Reading this posting I get the idea I should not put plastic 6 mil up on the wall.
No plastic vapor barrier? And if I may ask, why is it so encouraged to do so if it is the wrong thing to do. Would I have the same problem if I used a product like RedGuard instead of plastic?
Thank you!
Response to Tom Juchum
Tom,
There are two issues here. If the wall tiles are part of a shower surround or tub surround, it makes sense to ensure that the installation is waterproof. A variety of products are available for this purpose.
If the wall is not part of a shower surround or tub surround, ordinary wall construction advice applies. In all climates, it makes sense for a wall to include an air barrier. In South Carolina, walls should never include an interior vapor barrier (polyethylene), for the reasons explained in this article.
Exterior foam shower vapor
Hey Martin....I'm getting ready to put up hardi backer on the shower walls but am confused about what to do with a vapor barrier behind it. Two of the walls are exterior which has a few inches of exterior ISO. Any advice on what to do for a vapor barrier behind the tile walls? Thanks
Response to Stan Smith
Stan,
You posted your question in two locations. I have posted my answer on the other page where you posted the same question:
https://www.greenbuildingadvisor.com/community/forum/general-questions/45686/vapor-barrier-showers-exterior-foam#comment-107521
Utterly confused
The wall I'm planning to build looks like this: Aluminium siding, 2" EPS, plywood, 2x4 frame with Roxul batts, drywall, non-vinyl wallpaper.
I've not yet decided it will be air-conditioned. (60% it does)
What air/moisture retarder/barrier you advise where in the wall?
I'm living in zone 5A near the border of zone 4.
Response to Tony Tibbar
Tony,
I assume that we are talking about a new house that has not yet been framed. Right? If that's what you are designing, you may want to read this article: How to Design a Wall.
In your case, the easiest location for the air barrier is at the plywood sheathing. If you tape the seams of the plywood sheathing with a high-quality tape like Siga Wigluv, and seal all air leaks at penetrations (windows, plumbing penetrations, and wiring penetrations), then the plywood will be a high-quality air barrier.
Your water-resistive barrier (WRB) can either be installed between the plywood and the EPS, or it can be installed between the EPS and the siding. This article explains more: Where Does the Housewrap Go?
It's even possible to use EPS as a WRB, but I don't recommend that approach.
Your EPS is a vapor retarder, so you don't have to worry about inward solar vapor drive. If you live somewhere where there is a building inspector who wants you to install an interior vapor retarder, you should install a layer of vapor-retarder paint on your drywall.
For more information on the building science principles underlying walls with exterior rigid foam, see Calculating the Minimum Thickness of Rigid Foam Sheathing.
Fiberglass Wall Batt Kraft Paper on Exterior Side in North GA
I just heard of a home builder installing the batt insulation with the kraft paper on the exterior side. Now, even in "Hotlanta", there is more cooling degree days than heating degree days. However, depending on the year and lifestyle, it is often a toss-up as to whether there are more cooling days than heating days.
So given this climate situation, if this home is reasonably well sealed (passes the blower door test as required by Georgia), if the home builder placed the batt insulation on the "cold in winter side", what would be the down-side? The home already has drywall and the home builder is not willing to remove and replace according to the prescription.
No down side at all. @ Tom Gotschall
Asphalted kraft facers are "smart" vapor retarders, and become substantially vapor open when there is enough moisture in the cavity to become a mold issue. Asphalted kraft runs about a half-perm when bone dry, but over 5 perms under high humidity (more vapor open than standard latex interior paint.) If they were FOIL facers there is a potential condensation problem during peak cooling season, but with kraft there is no issue.
If it has plywood or OSB sheathing, the sheathing is itself a smart vapor retarder, limiting the rate at which outdoor moisture can get in via vapor diffusion.
Unlike cooler climates kraft facers offer almost no resilience upgrade (on either side of the assembly) in Atlanta's climate. Facers only make it harder to inspect the installation quality.
[edited to add]
I just remembered Allison Bailes' blog on this very topic a few years back:
https://www.greenbuildingadvisor.com/blogs/dept/building-science/should-paper-facing-batt-insulation-face-inside-or-outside
Response to Tom Gotschall (Comment #89)
Tom,
Dana Dorsett is correct. That said, builders should remember that they are required by building codes to install materials according to manufacturer's instructions. If the manufacturer of the kraft-faced batts requires that the insulation be installed with the kraft facing on the "warm-in-winter" side, then that's the way that the batts have to be installed -- or the builder is at risk of a contract dispute that could land him in court.
In this case, it makes no sense to make any changes. But builders should be aware of the risks of violating manufacturers' instructions.
This whole vapor retarder based on Climate Zone assumes that is a simple question. Maybe it is, and I am just dense. I am considering building in the San Bernardino mountains of SoCal, which seems to be listed as Zone 3 Mixed/Dry yet it gets sometimes 2 or 3 feet of snow on the ground so it seems like I should be following advice for a colder climate -- maybe zone 4 or 5.
At any rate, I am enamored of Joe Lstirbeck's "Perfect Wall" which has a full vapor barrier like peel & stick Grace adhered to plywood or OSB sheathing, then all insulation outside that held in place by battens and siding attached to battens over a rainscreen. The stud cavities are left open, uninsulated, and possibly even omitting drywall for an industrial or loft style interior. It seems like this should be fine for any climate -- outside vapor drying to the outside and inside vapor drying to the inside. After reading you article and all these other questions and answers I don't know what to think anymore.
1) Is there something wrong with this approach ? I was figuring on R30 Rock Wool batts on the exterior then Tyvek or two layers of roofing felt, 1/2" rainscreen gap created with spacers under the siding fasteners, then fiber cement siding.
2) I had thought Rock Wool Comfort Batts (as opposed to Comfort Board) would not slump or lose shape if they got wet like fiberglass batts would. So why are Comfort Batts not used on exteriors when Comfort Boards are 3x as expensive for the same R value ?
3) If this is OK without drywall, does it change if some walls or future owner decides to add drywall ?
Dreamer,
Q. "At any rate, I am enamored of Joe Lstirbeck's Perfect Wall, which has a full vapor barrier like peel & stick Grace adhered to plywood or OSB sheathing, then all insulation outside that held in place by battens and siding attached to battens over a rainscreen. ... It seems like this should be fine for any climate."
A. It is. This approach is called the PERSIST approach. For more information, see this article: "Getting Insulation Out of Your Walls and Ceilings."
Q. "Is there something wrong with this approach?"
A. No. The main disadvantage is the high cost.
Q. "So why are Comfort Batts not used on exteriors when Comfort Boards are 3x as expensive for the same R-value?"
A. If you want to install a continuous layer of mineral wool on the exterior side of your wall sheathing, density matters. Squishy insulation makes installation of the furring strips difficult. That's why most builders who want to install a continuous layer of exterior insulation choose rigid foam, not mineral wool. For more information on the best density of mineral wool insulation installed on the exterior side of wall sheathing, see this article: "Installing Mineral Wool Insulation Over Exterior Wall Sheathing."
Q. "If this is OK without drywall, does it change if some walls or future owner decides to add drywall?"
A. You local building inspector would need to approve any plan to skip the drywall. In some cases (for example, if you have an attached garage), the drywall improves the wall's fire rating (and is therefore necessary). If you obtain approval to omit drywall, adding drywall later won't cause problems.
Thanks Martin, that sounds promising.
I had previously read your linked article on Rockwool exterior insulation and one reason I liked the mineral wool approach was that I dislike foam, its dimensional stability and insect problems as well as cost and r-value loss at cold temps. The cost issue is serious and that is why I'd prefer to use the less dense but much less expensive batts, as long as they won't slump if they get a little wet.
Presently, per square foot, foam is $0.09/R, Rockwool Board $0.21/R, and Rockwool batts only $0.045/R where I live. Considering an R30 wall, the incentive to use batts is obvious.
The article dismisses the use of squash blocks as unnecessary with the denser material but doesn't address the advantages of squash blocks -- the ability to use the cheaper batts and the lower cost of squash blocks and short screws compared to very long and pricey screws. I shudder at the thought of how many holes I'd punch in the peel & stick missing the studs aiming 10" screws through insulation already in place. Especially since I hope to make drywall optional so those holes wouldn't be hidden. I was thinking of securing the 2x4 battens to the sill plate and rafters and then just two or three 6" lengths of 2x2 squash blocks along the length of the batten -- pocket hole screwed inboard and outboard. Then thread the batts through into place and allow the batts to expand tight around the squash block. Maybe I shouldn't refer to them as "battens" as they are more like the outboard chord of a truss wall -- except they are not load bearing and there is structural sheathing and VB between the inner chord (2x6 studs) and outer rather than a complete truss outboard of the sheathing.
This has gotten off topic of vapor retarder/barrier placement, but I do wonder about all the fastener holes people are punching in WRB and vapor retarders so it seems like minimizing those with a separate containment for exterior RW batt insulation should be talked about more.
Regards, Kirk
Kirk,
I think you are embarking on a difficult approach. I've given you my advice -- but you seem to want to try something different. Good luck.
It would be interesting to hear more about the use of squash blocks to get low cost, very high perm exterior insulation. How many are needed? At what point is insulation not considered "continuous" (on a code or building science basis)?
An assembly that will avoid cool climate sheathing rot even better than PERSIST is to not have any exterior sheathing. Maybe (some speculation here) something like:
interior side plywood sealed to be airtight
MemBrain
low cost batts between 8" plates and staggered studs
WRB (eg taped Typar)
diagonal steel or wood strapping (allowed? Does the interior plywood count for anything?)
fiber cement siding
Be careful (some climates) - with AC, everything reverses and PERSIST causes cool sheathing.
Taking his cue from Thorsten Chlupp, Lucas Durand, (who used to post frequently here on GBA) did something similar. Here is a link to his project: http://ourhouseuponmoosehill.blogspot.com/p/details.html
Good point - plywood gussets have a similar function (support exterior siding) but seem far more appropriate than blocks for thick exterior insulation.
Thanks for that link, Jon.
I have seen several articles about structural sheathing being on the interior side of the studwall instead of outside. It seems to provide the structural strength against wracking well enough, but this places all of the wall framing and sheathing plywood outside the WRB and vapor retarder. I much prefer the PERSIST or REMOTE approach that keep all the structural elements of the framing on the warm side of a WRB and VB. Having only the weight of the siding carried by furring would be a relatively light load easily supported by a 2x4 furring strip resting on the sill plate. Using squares of plywood to tie the furring back to the studs through the sheathing and VB could be done several ways -- pocket holes in the plywood squares, or galvanized angle brackets -- and might provide more support than 2x2 or 2x4 blocks as the "rungs" in what is really a ladder truss wall like in your link. This would seem more cost effective and structurally sound than long screws securing furring to the studwall through thick rigid foam.
Kirk
Log in or become a member to post a comment.
Sign up Log in