Thoughts on insulating a solid brick house in a cold climate

Hi everyone!
I’ve purchased an old brick house near Ottawa, Ontario (closing in September) to fix up for my mother with eyes open about the associated energy costs and upgrades factored in. I’m now trying to solidify my plans for the house, and wanted to get some input on insulating the exterior solid brick walls.
I’ve spent the last few days reviewing all the information available here and on other sites regarding options to insulate homes like this and have somewhat of a plan, but I want to be sure it’s reasonable. Obviously there is a wide variety of opinions on this topic… and best practice and views appear to have shifted over the past 10 years.
So here’s what I have:
The back part of the house is the original ca 1860’s stone cabin on a continuous stone foundation. This now contains the kitchen on the bottom floor. The upper floor has been turned into an attic by sealing off the door and laying fiberglass bats on the floor.
I’m not really going to touch the stone portion for now other than to air seal the gaps into the upper floor and perhaps increase the floor insulation. However, I intend to try to bring those upper floors back into the building envelope in the next year or two as usable bedrooms, so I don’t want to invest too much into it as the energy savings in a year wouldn’t pay off upgrading the floor covering to R30-R50 for a season.
I’m not going to touch the exterior walls yet on the stone section insulation-wise. I’ll need to do some minor repainting on the outside.
The front part of the house is a ca 1890’s brick house which needs some minor repointing in spots. The exterior walls are either 2 or 3 wythe solid brick (haven’t been able to measure to confirm). From inspection, it looks like the brick was originally furred out, then lathe and plaster. On most walls, it appears that they were later (1950’s?) covered in wood paneling, which was in turn wallpapered once or twice, then painted several times.
The ceiling was originally plaster, but that also was strapped, then questionable ceiling tiles put up.
Exterior Walls:
So… my first step in this house is to ideally strip everything back to the plaster and assess it’s condition and whether it is worth saving behind everything that has gone on since. However, my assumption is that it probably will be in rough shape in which case if I am redoing all the walls, I may as well insulate them ‘properly’, or at least as far as is reasonable without introducing durability concerns with the brick.
So, a few thoughts:
#1. I want the brick to dry both inward and outward as it’s quite exposed to rain. Humidity in the house can be managed, especially in colder weather to promote inward drying.
#2. I want to ensure the interior surface of the brick stays above condensation temps 95% of the time. Occasional condensation in mid-winter is OK as long as it can dry. I don’t want moisture in the ends of my floor joists that are lodged in the brick unless it has an escape plan.
Based on those principles, I have this rough plan in mind for the exterior walls:
1. furring on the brick providing a 1″ air gap to redistribute moisture.
2. 1″ EPS
3. 2×4 Studwall w/ 24″ centers against the EPS
4. Cavity fill the studwall with R-14 fiberglass
5. Drywall with acrylic paint
One concern – the original main level parlor has a very elegant original plaster ceiling we want to preserve, so I have no plans to touch the exterior walls in that room. Extra heat loss in that room may well be a price we have to pay, although I could possibly insulate the joist cavities from above.
I also wonder about using something like Intello: (https://foursevenfive.com/product/intello-plus/), however the only real examples I can see of it in use are from the company selling it.
Attic:
The attic appears to have no ventilation whatsoever, with what appears to be some sort of corroded polystyrene spray foam with thin fiberglass batts laying on top. As best as I can tell, more thin fiberglass was shoved down between the rafters all the way to the soffit from above in the sloped ceiling.
My plan here is along these lines:
1. Remove existing insulation
2. Air seal all openings to attic.
3. Beef up the rafters to buy a few more inches of insulation space. Maybe aim for 12″ altogether
4. Cut vents in the soffit, Install Accuvent or a similar product.
5. Install ridge vent on the existing steel roof
6. Put a vapor retarder / barrier below the rafters, then drywall and paint
7. Fill with loose fill cellulose, 10″ in sloped ceiling, to R-50 depth in attic.
Any feedback? I’m worried about insulation and dealing with moisture that may someday make it into the cellulose in the sloped roof from anything from a popped roofing nail to condensation from somewhere else. The hopefully ‘dry’ attic is attached to a ‘wet’ supporting brick wall that will potentially be releasing vapor into the attic unless I can seal it perfectly.
Basement:
There is a full-height basement with a dirt floor and stone walls. I’m at a loss as to what to do here. My understanding is that you can’t realistically insulate a stone basement as it depends on the air in the basement to dry the moisture the stone is wicking out of the soil around it.
The basement is dry and shows no sign of any moisture issues, leaking or flooding ever. It’s been mostly repointed at some point not too long ago.
How do I handle this cold damp basement under the house I am trying to improve?
The bottom line:
In addition to all the above, my goal is to air seal the doors and windows as effectively as possible in conjunction with the attic insulation to reduce the stack effect as much as possible (given that there will still be some air penetration through the brick no matter what I do).
I’d appreciate any advice or feedback as to how best to handle this house. The renovation budget is available to do it ‘right’ since. We need to touch almost every wall anyways, so it’s the right time to insulate it well.
GBA Detail Library
A collection of one thousand construction details organized by climate and house part
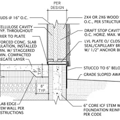
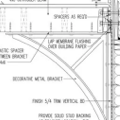
Replies
In Ottawa (comparable to US climate zone 6A) you'll need more than 1" of EPS for dew point control on R14 fiberglass using acrylic latex paint as the interior side vapor retarder (= Class III vapor retardency) . But 2" of EPS (R7.8-R8.4) will get you there.
The IRC spells out R7.5 minimum for dew point control on a 2x4 insulated wall in zone 6:
https://up.codes/viewer/general/int_residential_code_2015/chapter/7/wall-covering#R702.7.1
Most stone (other than limestone) doesn't wick moisture up the wall nearly as much as poured concrete. Granite doesn't wick much moisture at all. Insulating the interior side of most stone foundations isn't much of an issue. Using an inch or two of closed cell polyurethane provides a good air & moisture seal, and that would allow you to install a non-structural batt insulated wall to the interior side of the foam. (Set up the studwalls first, with at least an inch gap between the stud edge and stone, let the stud edges be the depth guide for the foam installer.) If the stone walls are reasonably flat it can be done with dimple-mat and 2" rigid EPS- just be sure it's air tight enough that room air won't convect through the exterior side of the foam. If there are wood beams inset into pockets in the foundation wall, give it a bit of clearance- don't insulate right up to the beam. Most of the time it would be fine to put an inch of spray polyurethane right up to the beam, but not with rigid foam.
Before installing the wall insulation, install ground vapor retarder that extends over the entire floor and up the walls at least a foot, sealed to the wall (or dimple-mat, if a dimple mat is used) ) with duct mastic.
Actually, there's no way to keep the interior surface of the BRICK above condensation temperature >95% of the time unless the brick is insulated from the EXTERIOR.
Insulating it from the interior makes the brick run colder, but as long as there isn't humid indoor air reaching the brick in winter it's not a problem- the brick dries to the exterior. When the temperature of the brick falls below the dew point of the outdoor air in summer (which it will at times, overnight) it will take on moisture as adsorb, and release it when heated by the sun, and the humidity in the channel between the brick & foam can be insanely high for a few hours, but the vapor retardency of a couple inches of EPS is enough to keep that from becoming a problem for the studwall (unless there is a true vapor barrier keeping it from drying toward the interior.).
With 2" of foam and R14 cavity fill the temperature of the interior surface of the foam won't be above the dew point of the interior air anything like 95% of the time either. But in your climate a ratio of R8 / R14 is enough that temperature of the interior side of the foam will be above the dew point of the interior air at least more than half the time over the 12 coldest weeks of winter, and that's enough to keep damaging amounts of moisture accumulation from building up in the fiberglass & studs, whereas a ratio of R4 / R14 is not.
If that's too much wall thickness to deal with, installing furring between the brick and 4" of continuous rigid polyiso, with another set of 1x furring through-screwed to the brick furring onto which the wallboard is installed gets you comparable "whole-wall" performance to the 2x4/R14 + 2" (R8) EPS solution. If you can find a source of reclaimed/used roofing polyiso it's not particularly expensive either. But the monolithic slab o' foam solution complicates wiring & electrical box installation, which is pretty easy in a 2x4 wall.
[deleted double post]
> I want the brick to dry both inward and outward... I want to ensure the interior surface of the brick stays above condensation temps 95% of the time.
With minimal R value from the brick inside face to outside, this is going to be controlled by how well outside air flows behind the brick and back to the exterior. Ie, vent away moisture, don't just redistribute it in a closed cavity.
Siga Wigluv is speced to air seal EPS.
Thanks for the thoughts, Dana!
> Insulating it from the interior makes the brick run colder, but as long as there isn't humid indoor air reaching the brick in winter it's not a problem- the brick dries to the exterior.
So the implication here is that we have to be strict with any air leaks around the wall assembly into the airspace next to the brick. This is a point of concern for me at one point in the house - around the main level parlor room.
This room has a plastered / molded ceiling that I don't want to disturb beyond getting conservation work done to repair some minor damage. As it has a centered feature, I don't want to make the exterior walls thicker as it will throw off the spacing of it all.
So, if I am not touching these portions of the exterior walls, it means that I will need to air seal the space behind my 'enhanced' insulated rooms from the 'mostly uninsulated' room. Any suggestions as to the best way to manage this?
On another note - is there any case for opening the top of this insulated gap into the attic (provided the attic is air-sealed from the rest of the house)? That would allow excess moisture to hopefully escape up and out the ridge vents.
Another question this raises - with this much insulation (~R14 + R8 - losses to thermal bridging etc.), would this cool the brick enough that freeze / thaw effects start becoming problematic?
Others have recommended maxing out at ~R8 to ensure enough heat still passes through the brick to keep freeze/thaw to a minimum.
Freeze/thaw is only a problem when there is active wetting going on. In winter the outdoor air is pretty dry. The bricks will accumulate moisture where the indoor air leaks out a high rate, or from defrost/melt water from windows that drips into the interior side of the brick.
The exterior view pictures show pretty decent eave & rake overhangs that would limit wetting of the exterior from snow melting off the roof, and no glaring signs of bulk water mis-management below windows. This one doesn't look TOO risky to me.
How are the 2nd story floor joists supported by the brick? Is it a ledger-board bolted to the brick, pockets inset into the innermost wythe, metal joist hangers, something else?
I don't know about the second floor joists yet - that detail is not exposed anywhere in the house, and I won't be even thinking about beginning any demolition until the second week of September.
Given the date of the house (estimated 1890's-1900s), I would guess that it's probably pockets in the innermost wythe, but that's just an assumption at this point.
Brian,
Most of your questions are answered by articles on GBA.
For information on your solid brick walls, consult this article: Insulating Old Brick Buildings.
For information on insulating your basement walls, consult this article: How to Insulate a Basement Wall.
As Dana Dorsett correctly pointed out, you have a few misapprehensions when it comes to insulating an old brick wall. You wrote that you "want the brick to dry both inward and outward," but that's only possible if you leave the walls uninsulated. You wrote that you "want to ensure the interior surface of the brick stays above condensation temps 95% of the time," but that's only possible if you decide to install exterior insulation.
Here are the facts: (1) The best approach with this type of wall is to install exterior insulation. (2) If you insulate on the interior, you increase the risk of freeze/thaw damage to the bricks. Read the article for more information. (3) If you decide to insulate on the interior, the preferred insulation is closed-cell spray foam, not EPS.
Dana Dorsett is also correct that there is a standard way to insulate stone-and-mortar basement walls: Insulate on the interior with closed-cell spray foam.
Hi Martin,
Your article on insulating brick buildings was actually one of the first items I read on the subject! However, it's also one of the reasons I posted this article as I've read conflicting opinions that spray foam traps moisture within the brick do to it's low permeance. As I've learned more in the past few day or two, that's looking like a non-issue.
My second concern with spray foam on a substrate like brick or stone is that it's a non-reversible change as it's almost impossible to completely remove from the substrate at a later date. In this project, I am trying to find a balance between energy efficiency and conserving the historical features of this house.
Brian,
Insulating an older brick building on the interior is risky, especially in a cold climate, as my article notes. According to my research, my article provides the best available advice on the topic.
If you want, you can certainly ignore the advice provided in the article -- but I don't recommend that path.
Martin,
At this point I am not ignoring anything, just trying to learn all I can so I can make the right decision for this building.
I do appreciate all you've written on this topic over time!
Brian,
My advice is:
(1) It's better to insulate this type of wall on the exterior than on the interior.
(2) If you want to consider insulating on the interior, assess the quality of the bricks (with professional help, if necessary).
(3) Assess the exposure of the walls to wind-driven rain and wetting from the roof.
(4) If the assessments made in steps (2) and (3) suggest that interior insulation won't risk freeze/thaw damage to the bricks, insulate on the interior with a moderately thick layer of closed-cell spray foam.
Thanks, Martin.
How large of a sample is needed for brick quality assessment? There are no 'loose' bricks that can be retrieved - I would have to remove any from the fabric of the building.
Do you have any recommendations regarding an Ottawa area professional I can retain to assess the other exposure issues? Presumably it has to be someone local as an on-site inspection would be necessary.
I really am interested in doing this right, albeit from an interior approach rather than exterior!
Brian,
As I noted in the article, I advise you to contact the Building Science Corp. in Westford, Mass.
Building Science Corp.
70 Main St.
Westford, MA 01886
978-589-5100
Many of the consultants at BSC have Canadian roots -- I'm sure that they have contacts in Ottawa. They will advise you.
Hi Brian. Sorry to revive an old thread, but I am looking for advise similar to you (insulating a brick house) and I am also located in Ottawa. If you had success in finding someone local to advise on the energy needs of your project, could you please provide me with their contact information, either here or with a PM?
Thanks!
David