High-R Wall Design in a Wildfire Zone?

I am in the process of designing a high-R wall for my future home build in Nederland, Colorado. The property is located at 8600 ft. in climate zone 6/7 and in a high wildfire danger zone. My priorities are a tight building envelope with high-R walls and more environmentally friendly materials that also resist fire, but I’m also trying to get the most bang for the buck on those materials. I’ve read various articles on this site and others, and they’ve been very helpful, but I’d love some input on my design. Here’s what I’ve come up with:
I’m leaning toward a 2×6 frame, rather than a double-stud wall, to preserve square footage. The frame would be filled with 3.5 pcf dense-packed cellulose, sandwiched between 5/8” gypsum and 5/8” plywood. Studs would be 24” oc with California corners to maximize the cellulose fill. The exterior insulation would be 4” of ~6 pcf density mineral wool (Rockboard, CavityRock, VersaBoard, CurtainWall, etc.). I’d go with corrugated metal and fiber cement siding, attached to the exterior with plywood-ripped furring strips. Note: I’m leaning away from rigid foams for the exterior insulation because a number of them either don’t perform well in fires or in the cold, have thermal drift over 5-10 years, or are rough on the environment. That said, exterior mineral wool doesn’t look nearly as cost effective as something like recycled rigid foam.
A few questions that I’m hoping folks can help me with:
1) Exterior insulation: Does my thinking on exterior mineral wool here make sense compared to other options? (I just saw Peter Yost’s post on Kooltherm, a potentially promising product …)
2) House wrap/barriers: I’ve read a number of GBA articles on house wrap and air/vapor barriers, but I’m not clear on exactly how all of the principles translate into materials and placement. Nederland has low humidity, but it snows a decent amount, is fairly windy, and there are a large number of heating days. For the wall design described above, and in this climate, what kind of wrap/barrier should I use and where would it go?
3) Closed-cell spray foam: Given that the mineral wool exterior insulation would allow drying to the outside, could I add 2” of closed-cell spray foam to the inside of my plywood sheathing (and then fill with cellulose) to increase the R-value of the wall? If so, where would I then put my house wrap/barrier?
4) Flaws/tips: Any other flaws in the design or tips for improvement?
Thanks,
Will
GBA Detail Library
A collection of one thousand construction details organized by climate and house part
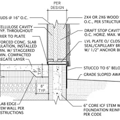
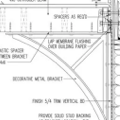
Replies
Will,
Q. "Does my thinking on exterior mineral wool here make sense compared to other options?"
A. If fire safety is high on your list, your thinking makes sense.
Q. "House wrap/barriers: I’ve read a number of GBA articles on house wrap and air/vapor barriers, but I’m not clear on exactly how all of the principles translate into materials and placement. For the wall design described above, and in this climate, what kind of wrap/barrier should I use and where would it go?"
A. Building codes require an interior vapor retarder; in your case, that might mean vapor-retarder paint or a "smart" vapor retarder like MemBrain. Your water-resistive barrier (WRB -- usually housewrap, but there are other options) would be installed either between the plywood sheathing and the exterior mineral wool, or between the exterior mineral wool and the furring strips. The main factor that drives the decision on WRB location is the the integration of the WRB with your window flashing -- and that depends on whether your windows are innies or outies. For more information, see Where Does the Housewrap Go?
Q. "Given that the mineral wool exterior insulation would allow drying to the outside, could I add 2 inches of closed-cell spray foam to the inside of my plywood sheathing (and then fill with cellulose) to increase the R-value of the wall?"
A. I suppose, although the switch would only add about R-5 to your wall assembly.
Q. "If so, where would I then put my housewrap?"
A. Adding closed-cell spray foam doesn't change the location of your WRB.
Will,
I built not far from you in Boulder, in town. The neighborhood association Architectural Control Committee mandated cedar siding and cedar shake roofs for appearance. Cedar is a great firestarter material. A neighbor’s kid was playing with matches and gasoline in their garage, and as you can imagine, things got out of control. Their home quickly went up in a spectacular blaze, totaling the house and their Benz. Fortunately, no one was hurt and the fire was contained to just one home. Afterwards the city banned cedar shake roofs, and we were required to use asphalt shingles. I’ve also seen embers flying out of chimneys in the same neighborhood.
Seems like you have already chosen good fire-resistant materials like metal, fiber-cement siding, non-combustible rigid mineral wool continuous insulation, and 5/8” drywall. Closed cell spray foam would improve the R-value of the wall cavities a little, but a potential fire hazard, except protected being mid-wall. Any wall or attic venting needs to screened to be resistant to airborne embers. Using asphalt shingles? Might want to avoid roof trusses, more vulnerable to structural failure in a fire. Might want to avoid vinyl in windows, fiberglass frames might be best, or maybe have fire-resistant, mineral-wool insulated exterior window shutters? Fire-resistant landscaping may be as important as the structure itself.
These references could provide some good ideas:
Nat’l Fire Protection Association: Prepare your home for wildfires:
https://www.nfpa.org/-/media/Files/Firewise/Fact-sheets/FirewiseHowToPrepareYourHomeForWildfires.pdf
U.C.: Landscaping Tips to Help Defend Your Home from Wildfires:
http://firecenter.berkeley.edu/docs/CeMasterGardener8322.pdf
Fire Engineering Construction Concerns: Trusses
http://www.fireengineering.com/content/dam/fe/online-articles/documents/2013/20130227havel_trusses.pdf
A friend of mine in N California has his own private fire hydrants and emergency water supply, which I believe is required in his area. However, he and his wife disagree on whether they would flee or stay in place in the event of a wildfire reaching their property. Being trapped trying to escape on roads is a threat too. Good to have a plan for what you would do in the event of a large wildfire in your area.
You can refer to the San Diego County Urban Wildland interface info https://www.sandiegocounty.gov/content/dam/sdc/pds/docs/pds664.pdf California has a wild land interface code that could be referenced also.
I would be concerned about the exterior insulation with the wood furring strip and possible gaps where embers could get in & ignite the plywood strips. The metal siding also needs its gaps filled to prevent ember intrusion. Also check out the attic & other vents that are made to stop ember intrusion, as required in California.
It seems you are working on a 2x6 wall plus 4" exterior insulation, seems like a double stud wall might be easier.
For extra protection gypsum exterior sheathing could be placed over the exterior of the building to get an actual fire rate wall assembly.
You can also address thermal bridging with interior side insulation - leaving just gypsum sheathing and siding on the exterior.
Martin, Robert, and Tim, thanks for the comments and resources.
Martin - I appreciate the barrier explanation. Even though the spray foam would only add about R5, would it add more value as an air barrier compared to the same 2” of cellulose? And I think innie windows are a better bet for a tighter envelope.
Robert - Thanks for the tips. I’m in Boulder County, which takes things a step further than Boulder City and has very strict wildfire mitigation regulations. I will have to integrate an interior sprinkler system (hopefully without too much impact on the tightness of my building envelope), my neighbors and I are putting in a hydrant in our cul de sac, I’m going with a standing seam metal roof, I’m looking at Alpen high-R fiberglass windows, and the county mandates a 30ft tree clearing around the house with additional thinning out to about 100 ft. While not bulletproof, hopefully most of these things would go a long way towards saving the structure.
Tim - Thanks for the additional tips on keeping embers out and upping the fire resistance. I’m building <2000 sq ft so i want to preserve square footage with a 2x6 over double stud wall design.
Does anyone have any thoughts on Kooltherm vs exterior mineral wool? I know that Kooltherm performs better than other rigid foams in fire but I expect not as well as mineral wool. I wasn’t able to find info on its performance in the cold or it’s thermal drift. Is that data out there? And how does the cost compare to mineral wool?
Thanks,
Will
Jon - Do you mind explaining a bit more? Are you saying ditch the exterior mineral wool and increase the wall depth/go with a double stud design? I’d like to avoid a 12+” thick wall and it’s impact on square footage. That said, if it costs me the same to increase my square footage for a double stud wall as it would to do exterior mineral wool, then that might be a trade off worth making.
Will
Will,
Other considerations aside, the difference in depth of your two wall options are pretty close. A double stud wall at around 12" and a 2"x6" wall with 4' of exterior insulation = 10". You aren't getting much more floor space with the mineral wool.
Will,
In other words, increase the footprint of your foundation if you decide to build a double-stud wall, and you don't lose that interior space. (Suggest keeping foundation dimensions a multiple of 2' or 4' so ply and studs align with less cutting, which you probably know already.)
Yes, you can omit exterior insulation. Exterior gypsum sheathing (no plywood) combined with double studs, continuous rigid foam on the interior side or strips of polyiso rigid foam on the interior side studs addresses thermal bridging without flammable exterior furring (Tim's point). Strips are hard to beat on material cost and R value/inch.
If you do go with exterior insulation, the exterior furring strips could probably be treated to be more fire resistant.
Malcolm and Robert - I've been having the 2x6 vs double-stud debate for months myself (it seems like an enduring one on this site and others). If I were to build a roughly 80'x25' rectangular structure, a 12" double-stud would increase my foundation by 5%, and with the additional lumber, I think it would be more costly than a 2x6 wall with exterior insulation because the exterior insulation doesn't require foundation underneath it, correct? Some or all of the double-stud lumber cost would be offset by the cost of the exterior insulation, and the labor might be a wash if I can find a contractor with exterior insulation experience, but the double-stud foundation would cost me more. Is it just preference at this point (2x6 with exterior insulation vs. double-stud) or would one of these designs actually be more cost effective with my cold climate and wildfire concerns?
Jon - Thanks for the explanation. I'm intrigued by that design. Where would the strips of rigid foam go? Between the outer wall studs and the gypsum?
Below is an explanation. It's not clear to me what the maximum foam thickness is.
https://www.finehomebuilding.com/2014/11/26/breaking-the-thermal-bridge
Mr. Welch,
Seems like everyone has covered things pretty well already. Avoiding some obviously poor choices for exterior finishes can help, but the sad developing reality is the insurance companies are writing fewer and fewer policies in many areas of Colorado (and other states) due to the rather large losses to fires. Despite a code sprinkler system, you might want to check in on this issue now before committing to any decisions on siting or materials choices. Some insurers do not recognize metal roofs as fireproof due to experiences they have had with (I think) California homes. There are different methods of detailing metal standing seam roofs, some of which create many potential ember catching pockets. It is all a bit involved to get into here.
Tim R already noted that your furring strips over mineral wool needs careful detailing for possible ember control as much as for rodent and insect access. Not designing a complicated multi-plane roof with lots of gables will go a long way to avoiding ember traps regardless of roof materials. High winds associated with fire fronts can attain enough speed and force to buckle some 16' wide garage doors which can make exterior wall choices moot. If possible design for multiple smaller garage doors. Flame walls being fed by large vegetation in close proximity to the house can project enough infrared energy through windows to ignite curtains or vinyl shades. The extended vegetation setbacks and general fuel reduction thinning out to 100' or more relate to this effect. Tool sheds or wood piles pose similar risk if too close to the main house. Adding gas or barbecue propane tanks (or matches) just speeds things up. Speaking of propane tanks, if you are going to have an above ground tank, be sure to aim the axis of the tank away from the house. The ends are supposed to blow off if extreme over pressure occurs. No sense blasting the house with shrapnel. Of course once the windows have been blown out, there won't be much to do anyway.
I would be very concerned with wind loading if not in a very protected spot. My house grumbles in some of the 50+ mph gusts we get and my framing is rather tank like. The idea of 24" framing may become more theory than reality once you have windows and doors placed. A plan with lots free wall area might yield some gains against thermal bridging, but with exterior insulation I suspect the difference might pencil out to be quite trivial. Additionally, finding a builder familiar with the application of advanced framing might be an issue. You might also want to price 5/8" ply over 1/2" versus the relatively few framing bits saved. My own experience with 6" of exterior insulation over very chunky 2x6 framing has given me interior surfaces that are remarkably free of temperature variation. Someday I will get hold of a FLIR camera and confirm this.
You mentioned not wanting a 12" wall, but if you are framing 2x6 with 4" of mineral board, you will be almost there by the time siding and trims on two sides are done. Martin is right about the flashing for window openings be critical relative to WRB. Take the time to read as many threads or articles on the innie-outie battles as you can stand. Now is the time to settle issues like window swing, fixed, tilt-turn, flanged, flangeless, egress requirements, solar gain, etc. Not doing the homework now can lead to very expensive ad hoc actions later. I have not worked with the mineral board and will probably go with recycled foam from repurposedMATERIALS in Denver for my next project. Long screws will be at play with either foam or mineral board with the thermal losses they create. Some feel the mineral squishes enough to make siding a bit problematic because the furring will tighten down unevenly. The furring spacing on 24" framing also may not comply with siding requirements so again consider 16" framing. Polyiso won't melt like EPS and I did use it in the garage under the fire rock. I would have used it on the whole house if a timely source had existed and I could convince the contractor it would be easier to deal with. I ended up with EPS above grade and recycled XPS below. I will be looking closely at ThermalBuck for my next build.
For my own high R build, I went with a full wrap of Henry Blueskin (as the primary) house wrap/weather barrier. Brackets hold Quad lock Retro on the house, a 1/4" gap exists from the block to the Blueskin. Functionally I have two drain planes as there is an additional layer of 1.5" low density foam used under the stucco coating, adhered by applying a cement/glue with a notched trowel that creates a series of vertical drain gaps between the two layers. After shaping the outer foam layer, a first coat of a hard base coat and mesh was applied followed by the finish coat of synthetic which provides color and texture. Because the gaps are sealed at the tops by a large metal cap, I believe they provide a small insulation value and do not exchange freely with exterior air. Martin would hopefully see this detail as the micro gap version of the infamous under vented roof detail and not yell at me for believing there is no air movement. Due to the heavy "outsulation" layer, the sheathing and interior framing elements are not supposed to ever get much below 52F if I remember the notes correctly. Framing is 2x6 on 16" centers, 1/2 plywood sheathing, R19 batts covered with 5/8 drywall. All of which is intended to allow moisture variations over the seasons to dry inward. Since the environment here is quite dry like your area, I have reasonable faith in my scheme. Some day I will cut some holes in the walls and install moisture and temperature sensors to prove this, but meantime, my better half has other things for me to do.
I went with Alpen fiberglass framed triple glazed. I have been very, very pleased with the performance thermally and the interior appearance. As windows can only reduce whole wall performance, choosing the best you can afford makes sense. The paint outside has been a bit underwhelming, but the sun here is brutal on all surfaces. I avoided PVC window choices based on prior experience and thermal expansion properties. If you must go with PVC windows, do not get a dark color, as that aggravates the thermal stress. I have had aluminum clad windows that I did not like due to the way the cladding caused thermal issues. That's another whole discussion if you like. The roof is all unvented R58. Overall, the house performs at about 1.5 BTU per sq. ft. per degree day which (if I have done the math right) is pretty fair I think.
If a wild fire arrives, my whole house may turn into a giant smore. Hopefully, I will never find out. We have done the extensive trimming advised and more. Water is very hard to come by here and basically the fire department will only save lives not property if the big one comes. If the power goes down, no water in a very short time. You mention a personal hydrant, what will keep the pressure going if a fire starts or arrives nearby? Will you have back up power and water to supply the interior sprinkler? Sorry to sound like such a Cassandra, but best to plan for everything to fail when needed.
In the time it has taken to type, this I see more entries have arrived. I am not sure about gypsum sheathing in your context, I would again stress finding an engineer use to mountain wind loads. The double stud wall idea does get discussed a lot. Check into threads about finding adequate packing for such walls and long term stability of the packing. ZIP R osb sheathing has tables for racking resistance available to your engineer which even in a double stud wall needs to be accounted for. I feel the foam break on the exterior side of any stud wall is better use of materials than inside.The idea of interior strips is not helpful at reducing bridging of the cold inward until too late. The sheathing and framing will get much colder further in than with outsulation or ZIP R and move your condensation point into your wall. We might get away with it in Colorado's low humidity, but it is still a less than optimal way to get where you want to go. It also seems very labor intensive and fussy.
A depressing fun fact about thick walls is how assessors determine your square footage. They measure the outside of the house. Some will accept the sheathing side dimensions as the compromise for exterior insulated houses. The lost footage is less this way. Whatever the choice, be sure to think through the intersect of roof and wall so you don't box yourself in with an insulation nightmare. Energy heels on trusses can be whatever you decide and the eave details determined before everyone is standing around asking what you want to do.
One last thing to pile on with. Do you have city sewer by any chance? If not, be aware that the septic rules and soil property tables have changed a lot. Best to get an engineer out to look at what options you have before setting your heart on a house site. In our area, rocks and more rocks are the general rule. Finding enough room to fit house and septic on suitable soil might impact your choices. Hope all this helps.
Jon - Thanks for the article link, looking forward to reading.
Roger - Thanks for the detailed response. Lots of info for me to unpack and some that's above my current knowledge level. I've been researching wall designs but not yet up to speed on roof designs.
I'll definitely be checking in on insurance issues before making decisions on materials--thanks for the heads up on that and the tip on garage doors.
Our property will be tapping into town water and sewer and the hydrant will be on the town main (rare for a mountain property but fortunate for us). We'll also be on gas from the utility company rather than propane, so no shrapnel concerns, thankfully.
Glad to hear about your positive experience with Alpen fiberglass windows. They have good specs and are local, so they're currently top of my window list. If I go with a 2x6 wall design, then I'd have them as "innies." Do you have any concerns about the middle pane film/membrane or did you opt for 3 actual glass panes?
Wind is a big concern. We'll be buffered by a slope to the west and some tree buffer, but houses have to be engineered to withstand 175 mph wind loads, so this will likely have an impact on design and materials.
I had looked into Zip System R-sheathing, but I have concerns about the polyiso cold performance and that their thickest board is 2.5", rated at R-12.6. Below freezing, I would expect this to be more like R-11 or lower, which wouldn't equal 50% of my insulation outside of the envelope and possibly lead to moisture accumulation (although it's a fairly dry climate). I guess I could stack this on top of another rigid foam product to increase the R-value, no?
And I'm absolutely in favor of redundancy and over-engineering for fire protection, so your "worst-case" suggestions are definitely welcome.
Will,
Increasing the thickness of your walls by 6" does mean you need to build extra floor area to be left with the same interior space, but an 80'x25' rectangular foundation only becomes an 81'x26' one. That's just 2' more wall, which isn't much.
I don't think the cost of materials and labour would turn out to be a wash. 4" of exterior mineral wool, fasteners and furring will probably be close to the price of your whole framing package, not just the lumber for the second 2"x4" exterior wall.
I'm not trying to push you in one or the other direction, but 4" of exterior insulation is a lot more complex than adding thicker framing.
Adding furring strips (sometimes called a Bonfiglioli wall) is a very effective strategy, but to make it cost effective you need to do it as a DIY project. The labour component is too high to get a contractor involved.
Good luck with your build!
Malcolm - I appreciate the feedback and cost-related info. This community is helping me to see things with fresh eyes and from different angles, which far outweigh my limited experience. All good stuff!
Mineral wool batts for interior insulation would also add fire protection compared to the blown-in cellulose, wouldn't they?
Irene,
Yes mineral wool batts are made from slag waste and are non-combustible. Cellulose is made from newsprint, and would be very combustible except for its chemical treatment. WHen dense packed inside a wall, there's little to no oxygen to support cellulose burning. So dense-packed considered fire safe.
Mineral wool batts have other advantages, including being easy to install by owner-builders, having a higher R-value (R=4.2/inch claimed for Roxul ComfortBatts) than cellulose, and good soundproofing (but so is dense packed cellulose). Disadvantages include extra labor cutting them to fit snugly around pipes and other obstructions and more expensive than fiberglass. Personally I'd choose them but most builders prefer to have subcontractors install dense-packed cellulose.
On metal roofs, To get a class A rating fire rating you need an underlayment of either a gypsum Dense Deck or roll type of fiberglass Versashield. The metal roof it self is not fire rated it needs an assembly rating to get the class A rating.
Tim's comment is worth remembering in all sorts of other contexts. Fire ratings are for complete building assemblies, not materials. The same is true of STC (sound attenuation) ratings.