Roofing underlayments

In a truss framed cathedral ceiling with R-60 cellulose and continuous vent channels from soffit to ridge, how important is the permeability of the roof membrane with a charcoal colored asphalt shingle roof?
Location; Western Massachusetts – Climate Zone 5, 7928 HDD
GBA Detail Library
A collection of one thousand construction details organized by climate and house part
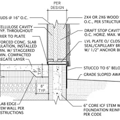
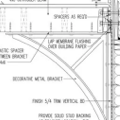
Replies
Not only is high vapor permeability not necessary in the underlayment on a well-vented roof, it may be counterproductive with a dark-colored asphalt roofing which will absorb solar radiant heat which could drive rooftop moisture through a permeable membrane.
Having said that, however, I would warn against using an impermeable membrane, like Ice & Water Shield which completely prevents outward drying. Some drying potential in both directions is always preferable to limited drying potential. #15 felt still makes an excellent roof underlayment. With a well-ventilated and well-insulated roof, ice dams and consequent leakage should not be a concern.
Is there anything new vis a vis venting around skylights? We used to cut notches in the top of the rafters (when the rafters were over sized to accommodate 12" of insulation). I can't do that because my rafters are not over sized and the roof is already sheathed. I will be adding a 2x4s perpendicular to and underneath the rafters, so there will be 14" of cellulose insulation.
My roofer is pushing a wider rolled material that will not curl or tear such as Typar RoofWrap 30. It comes in 41 1/2" x 10 square rolls at 0.54 perms (ASTM E96A).
Thanks, Robert.
Jon,
Everyone wants to use the latest high-tech stuff. That's the magic of marketing. The polymeric roof underlayments are an advantage and perhaps worth the price if the membrane will be left exposed before roofing is installed.
Felt works best if installed as the roofing goes on, so it doesn't have a chance to curl or wrinkle or get ripped off by the wind. This also has the advantage of staging the roof once and saves money both on materials and labor.
#15 felt is still the best WRB and has similar advantages as a roofing underlayment. But the pricey stuff makes scheduling easier and can be easier for the roofer to install (though they have to invest in a cap nail gun). Though I haven't yet seen it, I expect that the plastic nail caps required for the high-tech underlayments will telegraph through regular 3-tab shingles (as opposed to architectural shingles).
Thanks, Robert - I appreciate your input.
I am in agreement with felt and installing shingles soon there after, but that is not the case here. The underlayment will sit for almost a month before roofing, so the polymeric seems the best choice. Cap fasteners are specified for the roof underlayment and weather resistant barrier at the sidewalls, which the contractor has already invested in.
Robert-
I understand 15# felt (and 30# felt) being a perfectly fine WRB/roofing underlayment when the finished roofing is intended to be the primary waterproofing layer, i.e. composition shingles. What about the cases when you are dealing with materials such as clay and concrete tile. These materials allow more moisture through and the job of waterproofing falls more to the underlayment, and indeed at very low roof slopes the tile roofing is considered "decorative". Now you have a finished roof material that will last a very long time and the need for an underlayment that will last just as long. The typical solution to this has been the application of an SBS type underlayment creating very limited to no drying potential to the exterior. With an unvented roof assembly this is a dangerous combination, and yet the question is how to maintain vapor permeabilty and long term durability with this type of roof finish/assembly. Is there any other material that makes sense than the new high tech stuff, some of which boasts a 50 yr warranty? Thanks for your thoughts.......this is a real world scenario that is playing out in climate zone 2....
Graham,
The best type of roofing underlayment for the roofs you describe is one of the new breathable (high-permeance) synthetic roofing underlayments. Options include GAF Materials Deck-Armor, Cosella-Dörken Delta-Maxx Titan, VaproShield SlopeShield, Cosella-Dörken Vent S, Nemco Industries RoofAquaGuard BREA, and Cosella-Dörken Delta-Foxx.
For more information, see Synthetic Roofing Underlayments.
Back again........well the owner has basically said I am wasting my time worrying about trying to maintain a "vapor open" roof assembly. He doesn't feel that moisture entering the assembly is a significant possibility as a result of condensation in his climate zone 2. I have stressed that it is prudent to allow the assembly to dry to one side or the other as a "fail safe" but it appears he wants to use closed cell foam with a vapor impermeable underlayment below the clay barrel tile. Is it time to have him sign a waiver of liability????????
Graham,
All manufacturers of vapor-impermeable synthetic roofing underlayments -- in other words, the vast majority of all synthetic roofing underlayments -- only allow their products to be installed over a ventilated roof assembly.
If a contractor chooses to install a material (underlayment) in violation of the manufacturer's installation requirements, then (a) the installation has no warranty from the manufacturer, and (b) the installation violates the building code, since the code requires all materials to be installed according to manufacturers' recommendations.