Martin Holladay: some vapor barrier questions for Martin

Martin, First, let me thank you for some excellent discussion on a number of salient building issues.
I’ve read as much of your discussion on vapor barrier location as possible, but I remain puzzled by 3 comments that continue to resurface:
1) You believe that polyethylene film is not to be used as a vapor barrier: I could not disagree more; after 10 years of work in Minnesota, I’ve seen what can happen when VB’s are left out. All of the expert seminars at the AIA Convention insist that VB’s are essential in cold climates. After viewing their photos of buildings turned icicle, I must agree.
2) Some of your readers have implied that an exterior VB location is correct. This position is only correct in the lower Southern states where humidity outside the building is the culprit. Any northern or cold climate should have VB’s at the interior side of studs. Since the dewpoint in any wall system is within the system, moisture-laden air from the interior will drop when it hits that point. Thus any VB not to the interior is inviting moisture to condense in the assembly.
3) Some of your readers have referred to “moisture barriers” (Tyvek) as “vapor or air barriers”. This is not correct. Tyvek allows vapor and some air transmission. For this reason it can, and should, be placed on the exterior side of the sheathing without creating the dreaded “double vapor barrier”.
Thanks for the discussion,
Stephen Thompson, AIA
GBA Detail Library
A collection of one thousand construction details organized by climate and house part
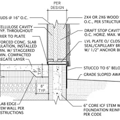
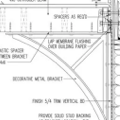
Replies
I'll back up Martin on his recommendations. First a clarification, vapor barrier is more accurately referred to as a vapor diffusion retarder, but we can call them barriers for the sake of this discussion
Poly vapor barriers can be very problematic. They are a disaster in warm humid climates, and even in cold climates, if there is any air conditioning being used, there is a big opportunity for vapor drive to the interior where it will condense inside the wall cavity. Vapor barriers in extreme cold climates can serve a purpose if they are installed without any gaps or perforations - if there are, moisture laden air will flow right through any gaps, minimizing its effectiveness.
In most warm climates, there is enough cold weather that walls dry to the exterior in the winter, so an exterior barrier is also problematic.
In general, if you do an excellent job of air sealing, the need for a vapor barrier is minimal, except possibly in extreme cold where no air conditioning is being used.
Regarding housewraps (Tyvek), they are weather barriers, and while manufacturers claim they are air barriers, it is very difficult to install them so that they actually minimize airflow through a wall assembly. Some are effective weather barriers, but the nails used to install them can allow bulk water to flow through. If you use another method for air sealing, felt or tarpaper is a good substitute in many applications.
Stephen,
Read the following and see if you have a new take on Poly vapour barriers versus TESTED air barriers, and properly spec'd vapour permeable materials.
http://www.civil.uwaterloo.ca/beg/Downloads/ASHRAE%20Thermal8%20Vapor%20Barriers.pdf
I'll let Martin defend himself, but I must say a couple things.
I think you really need to go back and review some building science 101. Who are these "experts" at the AIA conference? ALL legitimate and respected building scientists do NOT recommend a vapor barrier/class I vapor retarder anywhere but the most extreme cold climates. Homes in the lower 48-- Airtight Drywall Approach and a class III vapor retarder (latex paint) is all you need.
The key to a durable wall assembly is air sealing, not vapor barriers.
And builders can successfully use a low perm, vapor-blocking, exterior foam sheathing in cold climates if the foam is thick enough. As long as the condensing surfaces are above the dew point, you won't have condensation in walls.
AND Tyvek CAN be an air barrier if taped and sealed properly. It's difficult, but possible.
I don't argue that Tyvek is explained as a "moisture barrier" but I'm sure people are referring to a Weather Resistant Barrier. I'm confident that most building pros know that Tyvek allows vapor to diffuse through it.
Wow, I got beat out by 2 posters. You boys are quick!
Glad I could generate such enthusiastic discussion! Hey, I can learn!
Be advised that both the Canadian Building Council and the U.S. Department of Energy (not to mention many of the experts you can GOOGLE) continue to recommend VB's on the interior side of studs in cold climates. Either they need to update their literature or you guys need to write a definitive manual.
Thanks again,
Stephen Thompson, AIA
Glad I could generate such enthusiastic discussion! Hey, I can learn!
Be advised that both the Canadian Building Council and the U.S. Department of Energy (not to mention many of the experts you can GOOGLE) continue to recommend VB's on the interior side of studs in cold climates. Either they need to update their literature or you guys need to write a definitive manual.
Thanks again,
Stephen Thompson, AIA
Stephen, as everyone else points out, It's all about the air barrier.
In my opinion, the National Building Code of Canada does quite a good job in distiguishing between vapour retarders and air barriers.
My experience has been however, that despite having clear guidance on distinguishing between the two, every building professional I've had the pleasure of dealing with has somehow had it drilled into them that they are something like the same thing...
My best guess is that the building industry in Canada has built so many homes for so long that use a poly "VB" as a vapour retarder and air barrier, they have somehow become synonymous with each other.
The reality is you can get a lot more in terms of energy performance and durability if you understand the role of each as a seperate entity within a wall system and make design choices that use sometimes different materials to optimum effect - ie: ADA for an air barrier and vapour retarding paint as a vapour retarder as Brett suggested above.
Maybe the strangest aspect of the "VB" dogma in Canada is that it assumes one solution for all 3,851,807 square miles of the country? Hmmm...
Lucas
Well said...too many confuse vapour barrier and air barrier. Best to treat the two as separate.
Stephen
I suggest you go the the Building Science Corp website and do some research.
If you think poly vapor barriers are so important than what do you recommend for insulation and air sealing. Do you recommend fiberglass batts. What about air sealing.
Joe L of BSC talks about how much moisture an air leak can carry past a small tear in a poly vb. Once the moisture in in there is has a hard time getting out. Have you noticed how poly is installed in 99%+ of homes? Lots of tears and penetrations.
Poly is rarely installed to the level of being an air barrier as well as a vapor barrier, If its not an air barrier than it is not really a vapor barrier. Except in the most extreme climate a vapor retarded is all that is needed. Painted drywall is a vapor retarder. Add dense pack or spray foam insulation and you don't have the air flow carrying moisture into the wall. Take it farther with advanced air sealing and it gets better.
Stephen,
I'm coming late to this discussion, but you've addressed your comments to me, so I'll chime in.
You wrote, "You believe that polyethylene film is not to be used as a vapor barrier: I could not disagree more."
Well, interior polyethylene CAN work in Minnesota (and Vermont, and much of Canada), as long as
1. Your building isn't air conditioned, and
2. You don't have any foam sheathing.
Even in those situations, though, poly isn't a great idea. Building codes in the U.S. have never required interior poly -- only a 1 perm vapor retarder, which means that vapor-retarder paint has always satisfied the code.
To read a clear example of catastrophic failures caused in part by interior poly, see When Sunshine Drives Moisture Into Walls.
You also wrote, "Some of your readers have implied that an exterior VB location is correct." If you are referring to the use of exterior foam sheathing, this is now standard practice in commercial construction in cold climates, and has become extremely common in residential building in many areas, including Vermont. If you haven't learned the basics of designing a wall with exterior foam sheathing -- which is entirely code-compliant, by the way -- you should probably read Calculating the Minimum Thickness of Rigid Foam Sheathing.
Concerning your final point -- "Tyvek allows ... some air transmission" -- you are mistaken, and I'm sure the engineers at DuPont will be ready to do battle with you. When Tyvek hit the market in the 1980s, it was introduced as an air barrier. You can't blow air through it, and it meets the technical definition of an air barrier. Some builders (including me) question whether Tyvek (even when taped) is durable enough to be a home's primary air barrier, but that discussion is a separate one from the material's physical properties.
I'll side with Stephen, a poly VB in MN is the way to go. The warm side poly got bad press about 10 years back with the stucco fiasco, this was a detail failure in the stucco application. Solar driven moisture should not be happening in a properly designed wall. I have built new ( all with warm side poly) and remodeled many homes in MN with poly vapor barriers and have never once seen moisture damage or moisture accumulation in walls.
Bad building practices promote building failures, improper flashing details leading to bulk water intrusion are a main culprit. ADA will not save buildings from moisture damage if the exterior drainage plane is inadequate.
I recently replaced windows in a 1968 vintage 2 story in Minneapolis, the drywall on the exterior walls was foil-backed. This is one of the earlier low perm air barriers I have come across. Aside from some filtering of air through the fiberglass batt insulation around the electrical outlets, the walls were pristine. This house has fiberboard sheathing with lap siding and is drying to the cold side.
Doug,
My experience in my own home is similar to yours. It's a 1980 house with a poly vapor barrier -- I built it -- and when I have had an opportunity to open the walls, everything looks fine.
Of course, my climate is between 8000 and 9000 HDD, and I don't have air conditioning. People further south, and people with air conditioning, haven't all been so lucky.
Martin,
I agree with you, a low perm, warm side air barrier is only suitable for cold, dry climates. The triangle from Minnesota to Utah to Idaho would be were I would use warm side poly in new construction. In Minneapolis we do use AC but only on occasion in late June, with July and August being the warm period. This is in contrast to a heating season of 7 solid months.
I am in favor of promoting good building practices with specific climatic conditions as a guide. What I don't like to see is a one size fits all, homogenization of building details across the US. Hands on, in the field experience in MN says a warm side, low perm air barrier works, be it plaster or polyethylene.
I believe that poly, used as a vapor barrier, works just fine in our climate (Zone 7). But it is almost always used as the air barrier as well. It works OK if properly detailed but it is a disaster when it comes to renovating. It is virtually impossible to repair a poly air barrier after cutting into or opening up an exterior wall.
Martin,
Thanks for your response and those of your readers. I'm trying to digest the plethora of information and commentary regarding Vapor Barriers or retarders. At your suggestion I took the time to read your "When Sunshine Drives Moisture into Walls". Still it's difficult to blame an interior poly application for a brick veneer wall installed without a suitable cavity. Poor moisture barrier construction is the problem, in my opinion. We know we should create a minimum 2" air cavity behind a brick veneer; this eliminates grout bridging and allows the brick to dry out. Combined with brick vents that reduce positive pressure on the exterior of the wall and 2" XPS over the sheathing, the cavity should never allow water to enter the interior assembly. I usually install Tyvek between the XPS and the sheathing for good measure.
...And so, I stubbornly question if this discussion isn't more about solid moisture barriers preventing water and water vapor from entering assemblies from the outside as opposed to air-conditioned poly properly positioned in a poorly designed moisture barrier assembly? Your patience please. It's difficult to teach old dogs new tricks.
Stephen,
Your analysis shows a confusion between diffusion effects, water penetration effects, and air leakage effects.
You wrote, "We know we should create a minimum 2" air cavity behind a brick veneer; this eliminates grout bridging and allows the brick to dry out. ... I usually install Tyvek ... for good measure."
Inward solar vapor drive is a diffusion phenomenon that really has little to do with water penetration. It can occur in spite of the air gap (although the air gap will certainly reduce inward solar vapor drive) and in spite of Tyvek (which doesn't have a significant effect on diffusion). A layer of XPS is effective at stopping inward solar vapor drive.
Your concern about interior poly is misplaced, because wintertime moisture migration into wall cavities is mostly an air leakage phenomenon; diffusion plays only a very minor role. You need an interior air barrier, not a vapor diffusion barrier, to address the problem of wintertime moisture migration into wall cavities. In your original post, you mentioned "icicles." Ice accumulation in wall cavities is not a result of diffusion.
[This comment by William Rose was sent to me by e-mail, because he was having trouble posting it.]
Architects are pretty much the last remaining defenders of the vapor barrier. Why is that? I try to explain it using the ideas of performance and prescription. The client, and the public, want performance. Prescriptions (standards, codes, etc...) are invented as shortcuts to performance, and they facilitate commerce. Two problems: 1) prescriptions never get better over time, and 2) institutions accrue around them drawing profit and protection.
The vapor barrier is a prescription. It has outlived its usefulness. It detracts from performance at least as often as it provides benefit, all somewhat climate-dependent of course, and mostly it has no impact on performance. Buildings don’t need poly vapor barriers, architects need vapor barriers. My colleague Larry Elkin calls them “liability barriers.”
The AIA Code of Ethics makes no mention of building performance. It obliges the architect to comply with all applicable codes and standards. It lives in a make-believe world where all prescriptions (developed in the US by volunteer effort) are good, and cover the architect’s butt no matter how poorly the building performs (ok, overstatement). Architects often defend no-longer-defensible prescriptions precisely because they, the architects, are hardly equipped to deliver performance in contravention to outdated prescriptions. And they participate only rarely in the standard-making process, by my experience.
There’s a peer-reviewed ASTM paper that makes this same argument: Rose, W. “Insulation draws water,” Journal of Testing and Evaluation, 39:1. January 2011. There’s a performance approach to making vapor barrier design decisions: ASHRAE Standard 160, “Criteria for moisture design analysis in buildings.”
Bill Rose
I like his (Rose) analysis of codes, architects, liability, and the building process. Pretty accurate, in my opinion. For most items I never look to building codes to tell me how to build, I look for the best methods and processes and then as almost an afterthought I make sure they comply with codes. And if they don’t comply and I think the code is wrong, I will fight for a variance. Sometimes I get it, sometimes I don’t.
Where would I find these papers he refers to.
Allan
Allan,
A little Googling is all it takes to find out how you can obtain the documents Bill Rose referred to:
Insulation Draws Water
Criteria for Moisture-Control Design Analysis in Buildings
Thanks Martin. Have you read either of these publications, if so would you recommend them to builders.
Allan,
I haven't read them.
Allan - if you haven't read Rose's Water in Buildings you should. I confess to understanding maybe 2/3 of it (in fact, I'm due for a re-read) but it's shaped my and many other peoples' thinking.
Carl said, " In general, if you do an excellent job of air sealing, the need for a vapor barrier is minimal, except possibly in extreme cold where no air conditioning is being used." Correct me if I am wrong, but I think Carl's statement is misleading. Vapor can travel with air movement, but can also travel without it, for example, an air tight plastered straw bale wall still has vapor moving through it. I agree that vapor barriers are not essential in most areas of the country.
Matthew,
The only reason to have a vapor barrier is to address vapor diffusion. If you want to address air leakage, you want an air barrier, not a vapor barrier.
Carl's point is that diffusion-related problems are very rare. Most moisture problems in walls are caused by wind-driven rain; a secondary set of problems (far fewer) are caused by condensation of interior moisture piggybacking on exfiltrating air. Neither of these problems has anything to do with vapor diffusion.
Dan (#22)
I have seen several references here to the book by Rose, but have not read it.
Martin, I believe vapor diffusion, and the materials that inhibit the process are a HUGE part of what goes wrong in buildings, such as the case with EIFS, poly vapor barriers, and double vapor barriers. Air sealing will not solve vapor problems necessarily in my mind. These problems did not exist before the invention of vapor impermeable building materials and tighter construction practices, which should serve as proof that vapor can be a problem without air leakage. IMHO....
Matthew,
You wrote, "I believe vapor diffusion, and the materials that inhibit the process are a HUGE part of what goes wrong in buildings." You may believe that if you want, but this really isn't a question of belief. Vapor diffusion is a physical process that can be measured, and as such it falls into the realm of physics rather than belief.
Building scientists who have measured diffusion effects all agree that it's very hard to come up with a scenario where wintertime diffusion alone is responsible for water accumulation in walls, unless the interior has a very high humidity level (as would be seen in a swimming pool or greenhouse) or in a very cold climate (more than 9000 HDD). When wall damage can be traced to interior moisture migrating into wall cavities, the culprit is almost always air leakage.
You wrote, "These problems did not exist before the invention of vapor impermeable building materials." Matthew, that sentence surprised me -- I thought at first that you were writing a defense of the polyethylene vapor barrier. Instead it turns out that you are harkening back to the good old days when walls always stayed dry.
It's true, of course, that walls in old, uninsulated homes were generally free of moisture problems. But this was mainly due to two factors: they leaked air like a sieve (and were therefore remarkably well ventilated), and they saw a lot of heat flow from the interior to the exterior, baking them dry (because they were uninsulated). I really don't think that these facts are very useful when it comes to guiding designers of superinsulated homes.