Exterior 1920’s block/brick wall that must be insulated — but HOW?

I have a headache that have been researching as I need an affordable fix to be completed by the end of this summer.
Here is the deal: the 27’x70′ wall in a zone 5A (on top of a mountain to boot) you see in the attached pictures used to be the interior wall of a building that has been torn down. I now own both lots, our building does not use this wall for support, but it is used as an exterior wall. The metal plates you see are tying this wall into our steel I-beams and presents a good bit of thermal bridging.
The wall is constructed with one wythe of red brick (can be seen on the interior of my building and looks real nice) and one wythe clay-type dual-cell block. The problem with this is I have no good way to add furring strips to the building as the dual-cell block is very brittle.
On the first floor I have removed a 2×6 partition that was installed about 5′ from the wall to open up that section and to keep the wall warm, but at a cost. On the second floor there is a 2×4 R-7 kraft-faced fiberglass insulation. When we receive an east wind (not often), water does penetrate though with wall.
What I want to do is insulate the exterior wall to keep it warm and dry as I would like to use it as a heat sink; I also need to protect it, and further tie it into my building.
Here are my thought.
1.Closed Cell Spray foam, 3-4 inches, and paint the foam to protect it from UV. Down side is the cost ($20G) and the foam is not that protected from anything.
2. Figure out how to attach a framing system to the steel plates with most of the weight being supported at the bottom of the wall and use 2-4″ of ridgid foam board covered by metal siding.
3. Use a metal-clad 4″ (R-16.68) foam panel that anchors and has its weight supported at the bottom of the concrete footer and tie it into the steel plates along the side of the building at a cost of about $20G installed. http://www.permatherm.net/structural_insulated_panels/structural_insulated_panels.html
4. I haven’t checked into it, but tear the wall down and rebuild — but I must admit, I love the look of the brick on the inside of the wall.
Problem is I don’t have much money to do this but I have to correct this wall. Please let me know your thoughts as I’m all ears.
Thanks!
GBA Detail Library
A collection of one thousand construction details organized by climate and house part
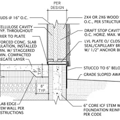
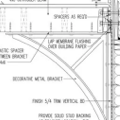
Replies
If you're hell-bent on keeping the exposed brick on the interior your best bet is going to be some version of Option 2. Bolt a steel angle to the foundation and balloon frame 2 x 6 metal stud to the top of the wall tied through at story height, insulate and metal clad exterior including careful parapet flashing over the top. Is that a structural pier or a chimney half-way along? If the latter perhaps you could cut it off to simplify the process.
If on the other hand you can bear to give up the interior exposed brick then forget option 4, just frame a well-insulated wall on the interior. It will certainly give you more bang for the buck in thermal improvement than any other option. You can remove this if at some future date you can build a functional structure on the adjacent lot to re-internalize the wall - perhaps a glazed sunspace? What is the wall's orientation?
The first issue is whether this existing wall is structurally adequate, regardless of the energy performance. It looks like it may have originally been an exterior wall but that doesn't mean it works or hasn't degraded over time, especially when you say water penetrates the wall with a good wind. There is no sense spending a lot of money adding a new wall and insulation if the old one is about to fall down. Metal studs will work but have such a high thermal bridging that the effective R-value ends up quite low. Assuming the wall is structurally adequate, 3"+ of rigid foam adhered and anchored would probably give you the best performance and keep the masonry on the interior as a thermal mass. Tapcon type anchors and washers can be used to hold the foam in place then a stucco coating (Dryvit type system or similar). Anchoring loads are very low so the condition of the existing is not as critical and if greater strengthis required, parge the outside surface of the masonry with a structural bond coat before adding the rigid insulation. Not sure what all that will cost where you are but it should give you a decent wall.
Corian: There will be no thermal bridge if the insulation is installed on the outside of the metal studs as John proposes in his original post.
Spray foam vs. cladding: I guess this is partly an esthetic issue. I've yet to see an exterior foam job that is anything but a kludgy mess, but that's just from my personal experience - perhaps there's a good way to do it. More importantly, it's also a lifecycle issue - the metal studs, foam board and metal cladding are all easily removable and re-usable if circumstances change, and the brick behind will be in great shape. The only future life for all that spray foam and dryvit is the landfill, along with the brick from which it is now inseparable. A triumph of present convenience over sustainability: not so green IMHO.
In any case I agree it's important to ensure the wall is structurally sound before doing anything.
You guys are are quick... The wall faces to the east which is when I get water penetration with a strong east wind, but that only happens here a few times a year. Prior to securing the wall to our building it was free standing, it stood on its own and now the metal square plates have it secured to our building. Since securing it to our building I have seen zero movement or degradation with the exception of water freezing on the outer area of the wall. There are a few preexisting cracks in the thicker end sections that I intend to use injected epoxy to correct. I hesitate to tear the wall down as I don't know how they secured the 2x4 walls on the second floor. My tenants would be a little us set if I give them an open sun room. I have no idea if they nailed those walls to the brick or not and the guys that build the new section in the 70's have all passed away. The middle column is indeed a chimney and I am wondering how much support that gives to the wall. I have entertained the idea of inspecting the chimney to see if I can put it back in use some day. From a cost and reutilization aspect ballooning metal studs only attached to the metal plates and at the bottom has merits. Around my area guy only prefer to use wood but they will use what ever is required. The roof of my building has Duro-last on it, that material will be easy to extend the flashing. Great roof to as it has fixed all the leaks and have has zero problems since it has been install 5 year ago. Please keep posting ideas and what not as very curious.
John,
There are plenty of ways to fix this problem, but they all take money. It won't do any good for any of us to suggest solutions if the answer is always the same -- "I can't afford to fix it."
Here's my recommendations:
1. Hire an engineer to assess the structural integrity of the wall.
2. Assuming the wall is sound, hire an EIFS contractor to cover the exterior with rigid foam and synthetic stucco.