Will my insulation plan work?

I am in the course of remodeling an 1860s balloon-framed farmhouse in NE Pennsylvania. I am currently reinsulating the attic. It originally had only R-19 fiberglass insulation in it which had discolored due to numerous air penetrations.
I was able to score salvaged 1.5″ felt-covered polyiso board (came from a torn-down factory) for very cheap and have purchased a closed-cell spray foam kit. My plan was to put about an inch of spray foam between the floor joists directly on the drywall then use unfaced fiberglass to fill the remaining void and then put the polyiso on and tape the seams with foiled tape.
My worry now is that any moisture may get trapped in the fiberglass and cause problems. Should i put the polyiso down first then spray foam then fiberglass? I only have 2×6 floor joists to work with. Any advice would be greatly appreciated.
PS. This is a great site, lots of good info.
Thanks again
Ben
GBA Detail Library
A collection of one thousand construction details organized by climate and house part
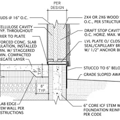
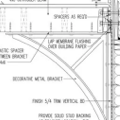
Replies
Ben,
The answer to your question depends on how successful you are at addressing all of your ceiling's air leaks.
Sealing the air leaks is by far the most important part of this job, so it's worth taking the time to do a meticulous job.
There is no easy way to integrate the used polyiso with this project. You can use the polyiso, but installing it will be fussy and time-consuming. The easiest (and in many ways best) approach to improving your attic would be to use spray foam from a two-component spray foam kit to address the air leaks, and then to install a deep layer of cellulose insulation.
If you want to use the polyiso, I would cut it into strips and install it between the joists, against the drywall. Seal the perimeter of each piece in place with spray foam. (As I said, this is fussy, time-consuming work.) Then install the fiberglass batts on top.
Remember -- cellulose would be better than fiberglass batts.
I do have a 2 part spray foam kit but you suggest not putting the iso sheets on top of the foam and fiberglass? Would enough cold air penetrate the iso and contact any heat loss coming up through the spray foam and fiberglass which will cause moisture issues?
Ben,
You live in climate zone 5 of climate zone 6. If you want to combine rigid foam insulation and fluffy insulation, with the rigid foam on the exterior side of the fluffy insulation, building codes require that the rigid foam be thick enough to prevent condensation problems. In your climate zone, that means that the rigid foam would need a minimum R-value of R-20 or R-25. (For more information on this topic, see How to Build an Insulated Cathedral Ceiling.)
Your polyiso has an R-value of only about R-9 or R-10.
There are a few caveats to this analysis: the code requirements are for cathedral ceilings, not insulation installed on attic floors, because contractors don't normally use your suggested method on an attic floor. So the code doesn't directly address your situation.
Here's the bottom line: you might get away with your suggested approach if your air sealing is impeccable. That level of air sealing might require a blower door to assist you.
If your ceiling has air leaks, you might get moisture accumulation on the underside of the rigid foam.
Ben,
By sealing the attic floor properly and meticulously, as Martin mentioned, you theoretically eliminate heat loss through air leakage, which means you eliminate moisture transport by air, which as we know is a much larger concern than moisture transport by diffusion. If the air sealing is done well, then your moisture concerns should be minimal. You might want to do a blower door test to find the small leaks, and perform a pressure diagnostics test to determine how connected your attic is to outdoors.
You seem to imply that you're plan is to insulate the attic floor with a layer of spray foam, rather than seal key areas (perimeter, attic floor penetrations, top plates, etc.) This approach should be fine, but likely more costly from a material standpoint. Be mindful that your approach means that any electrical wiring along the floor will be sealed in, and you should take caution around any recessed lighting that may be present. Cellulose, as Martin mentioned, is generally the preferred practice. It is a great way to add R-value quickly and for relatively cheap.
Thanks for all the information Mike and Martin. My main reason for using the spray foam (and you are right its costly) and the ISO board is due my limited floor joyce size (2x6) and my desire to add osb or plywood on as much of the attic space as I can to use for storage. With three kids i have alot of stuff to store and old houses are always limited on storage space. My house overall is poorly insulated. I have single pane windows, (27 total) single pane doors (6 total) with new storm doors. I hope to get storms put on the windows this year.I only have about r-13 in the walls so insulating my attic to anyhting above R-35 will probably not give me any signifigant gains. I will take my time and seal all top plates, vent stacks and pentrations carefully luckily i only have a couple recessed lights to deal with. Another factor contributing to the heat loss was an unsealed chaseway where a chimey was at one time, that alone was a huge contribtor to my heat loss. I have a very open floor plan and heat with wood so sometimes the drafty condistions help to not heat me out of the house but when it gets below 0 its gets chilly. I expect to see pretty substantial gains in efficiency and a drop in my wood consumption. I ordered enough spray foam to seal the rim joyce in the basement as well.
Thanks again
If buying storm windows, it's worth the up-front freight to go with a Low-E hard coat glass, and even though it's more expensive, it'll pay back QUICKER than clear glass storms. Harvey has the tightest storm windows in the industry, and has a low-E option:
http://www.harveybp.com/upload/products/literature/Harvey_Storm_Products_Brochure.pdf
But the Larson Gold series with low-E glazing sold through box stores don't suck either:
http://www.larsondoors.com/inc/pdf/larson_windows_brochure.pdf
If you can stack two layers of that 1.5" iso you'll have sufficient R-value to avoid condensation in the fiberglass layer even with minor air leakage. But you'll do even better if you use cellulose as the cavity fill (far more air-retardent than fiberglass too. At 1.5" (~R8-9 for old roofing iso) you don't have enough cold-side R for dew point control, with an inch of closed cell plus 4.5" of fluff (~R20), but if you double-layer the iso you're good to go at R16-18.
Even though that's below the IRC prescriptive value, it's the ratio that counts, and the IRC precriptive values presume R49 for climate zones 5 & 6, and you'll be in the mid-30s. Taping the seams, or even a layer of housewrap as an air barrier between the layers as both a slip surface and air barrier ensures that any nail holes or other air leaks in the lower layer of iso doesn't leak air and condense on the second layer.