Insulate knee walls

Situation: Currently have knee walls with no insulation behind them or the cathedral portion of the ceiling. The rafters are 2×6’s. Ventilation is provided from vents installed between the exposed rafter tails. Blown in insulation is currently blocking off the top of the cathedral portion. I live in zone 5.
There was some haphazardly blown in insulation that had fallen from the top which looks like sheep’s wool but has fiberglass in it which I pulled out(about 6 contractor sized trash bags). There was ice damming and some mildew on the roof deck. I plan to clean this with a mixture of hydrogen peroxide and vinegar to make peracetic acid.
My Idea:
Cut and remove some of the flooring. Through this access install bat insulation under knee wall and foam to seal.
Install soffit baffles and place batting under floor boards towards the exterior wall. This batting will go up against the soffit baffles and also be foamed to seal.
There are 22″ between rafters and knee wall joists so I will cut 2″ xps into 21″ strips 8′ long.
Tricky part:
put 1″ blocking on roof deck at corner of each rafter bay from knee wall side and attic side to ensure ventilation gap is maintained.
From the attic feed down one strip of xps and then another strip of xps under it. Hope and pray any protruding nails are not a huge obstacle.
Install baffles at the top of the attic, place batting under for reinforcement and foam to seal.
Go into the knee wall and attach a piece of rubber hose onto the end of a great stuff spout, maybe even attach some heavier gauge wire to the rubber hose to make it easier to guide. Guide it up to the top of the cathedral portion and fill the gaps on either side of the xps.
Apply two layers of xps to the knee wall as well and put back blown in insulation until the R-19 under the floor boards is brought up to R-49.
The one knee wall I’m looking at I will leave an access door because there is a stack pipe and bath vent and I’d like to keep access there. The other three I will glue xps to the back of drywall and cover the edges of the xps in caulk to air seal my once opening.
The cathedral portion should be R-49 but the inspector said he’d be okay with me doing this and doesn’t expect me to rip out all the dry wall and sister beams to the 2×6’s to give enough space to bring it up to R-49.
This would cost me ~$584 to do all 4.
Or I could have it done with foam in an unvented style. Block off the bottom of the cathedral portion and have that filled with the stuff they put in your walls and then have the knee wall portion sprayed. Foam alone would cost me ~$1354 at $1 a board foot and an estimated 64.5 sqft per each knee wall area and 5.25″ of foam. This would actually exceed code because unvented attic assemblies in zone 5 only require R-20 but this would be ~R31
What do you all think? XPS or foam or something else?
GBA Detail Library
A collection of one thousand construction details organized by climate and house part
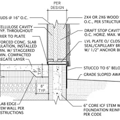
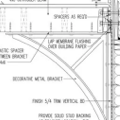
Replies
First, the likelihood of being able to pull that off with can-foam without screwing it up seems remote.
Second, XPS is about as un-green as it gets in the foam insulation world due to the copious quantities of extreme global-warming potential (GWP) HFC blowing agents used (often a mix, the primary component of which is HFC134a, at a GWP about 1400x that of CO2.) If you used EPS instead it would have similar thermal characteristic and would be cheaper (if thicker) to achieve the same rated R, and since it's blown with pentane @ ~7x CO2 you'll have done less than 1% of the climate damage as an XPS approach.
Third: In climate zone 5 at in an unvented approach you can get away with a flash'n'-batt approach using just 2" of closed cell spray foam on the roof deck and R15 rock wool or HD fiberglass between the rafter. It's the foam-R to fiber-R that counts- at R49 with this approach you would need R20 of closed cell on th roof deck which would be OK with up to R39 of interior fiber. But with R12 you have to keep the R to the interior down to R23ish. Make sure that the fiber is a full fill- a compression fit for any air-barrier covering you put under the rafters. With as little as 3" of rock wool you will have met code for a thermal barrier against ignition on the foam, and you could just stop there, using housewrap or something as an interior side air barrier (just nothing more vapor tight than 0.5 perms).
If you wanted a thermal break on the rafters you could add up to 2" of EPS without it being too vapor-tight or creating condensation issues at the spray-foam/fiber boundary, but that would require half-inch gypsum (or OSB or plywood) on the interior side as a thermal barrier for the EPS. With 2" of EPS, 2" of ccSPF and R15 of rock wool you'd be at about R35 center cavity, but performing better than R38 in joists due to the R8 of thermal break you get over the rafters.
It would also considerably outperform the 5.25" of ccSPF solution, which DOESN'T thermally break the rafters. Installing 5.25" of closed cell foam between would also be at least as bad as XPS, since it's blown with HFC245fa at about 1000x CO2 GWP. (With the exceptions being Aloha-Energy's water blown 1.8lbs closed cell foam or Icynene's 2lb and 2.2lb semi-open cell water blown foams.)
There is no recent version of the IRC that prescribes R20 for cathedralized ceilings, but there are state & local codes that do. In locations that would require R39 between attic floor joists R30 cathedralized ceilings are sometimes allowed. R20 can be grandfathered in or waived by the inspector, but SFAIK there is no location in climate zone 5 that expressly allows R20 cathedral ceilings in new construction.IRC 2012 prescribes R49 ceilings for zone 5:
http://publicecodes.cyberregs.com/icod/irc/2012/icod_irc_2012_11_sec002.htm
Maybe I'm confusing the R-20 requirement for condensation control: http://publicecodes.cyberregs.com/icod/irc/2012/icod_irc_2012_8_sec006.htm
I'm trying to do this green, efficient, and without ripping out the existing drywall or making the rooms smaller. The roof is only a few years old so ripping it off is out of the question. I'm a vet an a college student so money is tight too.
With that in mind, what is really my best option? 2" of ccSPF, 2" of EPS, I'd only have 1.25" of space left. I also don't know how to get 2" of ccSPF on there without ripping out all the interior drywall.
Jim,
It's hard to make a recommendation without a site visit. But in many cases, it's impossible to do a good job of retrofitting insulation in a sloped roof assembly without first removing the ceiling.
For more information on this topic, see How to Build an Insulated Cathedral Ceiling.