Cape needs insulation retrofit (with ventilation)

Hi all,
New owner of a 1 1/2 level cape here. Finished upstairs. Zone 5. I’m experienced with home renovations and DIY, but new to Capes.
Trying to bring upstairs environmentals in line with lower level conditioned home temps year round without running the mechanicals 24 /7.
No insulation to speak of. No ventilation. No vapor barrier. Planning to make the attic “outside space”.
I’ve blocked all of the underfloor joist bays, sealed all chases and penetrations, insulated the kneewall hatches very well, etc. This has helped a lot.
Next steps:
Add 60/40 – soffit / ridge venting to a 1:150 target
Add as much cellulose insulation possible on the attic floors (target R40)
Add baffles from the soffits with wind wash protection.
Add as much cellulose (netted) or fiberglass batts (faced) on the backsides of the kneewalls with an air (not vapor) barrier on the backside (target R 15).
This is pretty close to what I’m dealing with: http://www.doityourself.com/forum/attachments/insulation-radiant-vapor-barriers/13395d1370215535-insulate-knee-wall-cape-cod-20130602_134155.jpg
Here’s where I’m trying to go:
http://www.energysmartohio.com/uploads/content/HalfStoryAFTER_600.gif
or
Outstanding concerns:
I’m having trouble determining the best way to insulate the sloped 45 degree walls WHILE maintaining airflow over the insulation.
I’m aware that I should be trying to maintain about 2″ of space above the insulation.. but this is a retrofit, so my options are few.
I feel like I have a few options for the 60″ long sloped walls from the top of the kneewall to the flat ceiling:
1) install faced fiberglass insulation that fits in the 2 x 6 cavity with 2″ of room to spare above.
2) install Rigid foam against that fits between the rafters in the 2 x 6 cavity (directly against the sheetrock).
3) construct my own “baffles” for the sloped walls from rigid 3/4 foam, furr them off the underside of the deck by 2″ for airflow and dense pack cellulose below the foam and above the sheetrock.
Any advice or opinions would be greatly appreciated.. as I am struggling with what direction to take here..
Thanks!
GBA Detail Library
A collection of one thousand construction details organized by climate and house part
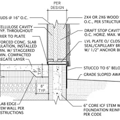
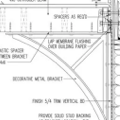
Replies
Ohio,
Ideally, you will sister some framing to your existing rafters (or fur them down) so that you have enough room for R-38 insulation.
Closed-cell spray foam will give you the highest R-value per inch. (It's possible to install spray foam in ventilated rafter bays; the ventilation channels will lower your risk of sheathing rot.)
Another possibility is to create ventilation channels with EPS rigid foam; then fill the rafter bays with air-permeable insulation like cellulose, fiberglass, or mineral wool; and to install a continuous layer of rigid foam on the interior side of the rafters to address thermal bridging and to improve the assembly's R-value.
For more information on your options, see How to Build an Insulated Cathedral Ceiling.
Thanks Martin,
Unfortunately the upstairs is in far too nice shape to go ripping out the drywall so I'll probably not reach R38 overhead . I had been thinking about doing spray in foam on the sheetrock side and just having them leave an air gap.. I'm just afraid that foam's inability to absorb any moisture could be trouble in any horizontal application (especially since I don't have a vapor barrier).
Regarding your second suggestion.. I hadn't thought of that.. I'm attaching a drawing.. let me know if I got this right..
In this scenario.. how much room do I need to leave between the 2 EPS sheets to allow the insulation contractors to fill will cellulose for example..
Also, installing furring strips up into the rafter bay in any secure fashion is going to be a real PITA.. is there any problem with gluing something to the top face of the sheet to "fur it back" and letting the insulation contractors dense fill underneath it so the sheet "floats up" to the roof deck? See second attachment..
Thanks!
Ohio,
First of all, if you choose to install closed-cell spray foam, you don't need a vapor barrier. Closed-cell spray foam is already a vapor retarder.
This discussion is probably moot, however, if you are unwilling to remove the finish ceiling. For a conscientious installation of spray foam, your spray foam contractor will need good access to the rafter bays. That means you'll need to remove the existing drywall or plaster on the sloped ceiling.
Second, you misunderstood my suggestion. I suggested that you include a continuous layer of rigid foam on the interior side of the rafters; I didn't suggest that you cut the rigid foam into thin strips and insert them between the rafters. (Your approach doesn't address thermal bridging through the rafters.)
Attempts to insulate rafter bays by inserting thin strips of rigid foam between the rafters don't have a good track record. For more information on the problems associated with this method, see Cut-and-Cobble Insulation.
It's doubtful that 3/4" EPS is sufficiently stiff to dense-pack against an a 22" wide rafter bay (or even a 14" wide rafter bay- it'll bow out and likely crack in at least a few places. To do it with 3/4" goods it would need to be supported mid-bay with a strip of furring (or better yet, 2" EPS) to keep the ventilation gap open.
If you're not going to demo the sloped ceiling, how do you propose to even get the EPS in there, and seal it tightly enough to the rafters to prevent the cellulose from getting into the vent gap during installation?
If instead of ridge venting you add gable vents to the mini-attic above the head-banger sloped ceiling you'll do OK with a slow-rise pour in the sloped ceilings, forget the ventilation gap. A half-pound open-cell pour would perform nearly as well as a 2lb closed cell pour from a thermal point of view, but paint the sloped ceiling with "vapor barrier latex" if you go that route to make it a class-II vapor retarder at about 0.5 perms. A 5.5" a 2lb pour would be about 0.2 perms- more vapor-tight than vapor barrier latex, but is a "solution-problem", with an extremely slow drying rate. In a zone 5 climate 0.5 perms is fine for protecting the roof deck from wintertime moisture drives, but has more than 2x the drying rate of a closed cell pour.
The alternative to a half-pound pour would be to dense-pack that section with 3.5lb cellulose and apply v.b. latex to the sloped ceiling. A cellulose solution runs lower risk of blowout (the pressure is limited by the blower settings), and probably cheaper too. It has the additional protective advantage of being able to buffer much of the wintertime moisture loading in the insulation itself, sharing the load with the roof deck, reducing the peak moisture levels in the roof deck. (Almost every time I've looked at half-pound pour solutions I've ended up going with dense packed cellulose, primarily for cost & risk reasons. YMMV.)
Another problem with the proposed EPS + cellulose solutions even IF it were buildable is that you'd get at most ~R14 in there, which in a zone 5 climate is a recipe for ice dam formation (even with the vented roof deck.) With cellulose or a half-pound pour you'd be at about R20, which while not great, is quite a bit better. Code only demands 1" of air gap for vented roof decks, which would get you to the R17 range- still not great, but measurably better than R14.
With plank roof sheathing and dark shingles the mold/rot risk of going unvented, insulating the roof deck is pretty low in zone 5. In capes and bungalows with 6" rafters and kneewalls it's usually the right way to go.
Then, when it's time to re-roof, in a zone 5 climate adding enough rigid insulation above the roof deck that it comprises at least 40% of the total R further reduces the risk at the roof deck by raising it's average wintertime temperature to above the typical wintertime indoor-air dew point. eg: If the cavity fill is R20, you'd need at least R13.3 on the exterior. The total center cavity R would be R33.3, and R13.3/R33.3= 40%. To do that with some margin in an a relatively thin layer, 1.5" of polyiso (R9) against the roof deck with 1.5" of EPS (R6.3) on top of the isos gives you R15.3 for the foam layer. Using EPS on the exterior layer means you would not have to de-rate the polyiso for it's abysmal low-temperature performance relative to it's rated-R. Despite the slightly lower rated-R of EPS + iso stackup relative to 3" of polyiso, it will in fact outperform 3" of polyiso during the cold winter months that matter, but 3" of polyiso (even derated) would be still get you above R13.3 for wintertime performance. And since you would be thermally breaking the rafters, even R33.3 done this way performs about as well as R38 between 2x12 rafters (BETTER than 5.5" of R7/inch closed cell foam between 2x6 rafters), and R35 will do better still.
Hi Martin,
Thanks for sharing that info and for clarifying. I definitely don't want condensation problems that can come with the application of rigid insulation in cathedral ceilings such as those in the "Cut and Cobble" scenario.
I've been following the Lstiburek school of thought.... It seems like diligent sealing, doing as much insulation as possible and maintaining airflow above it - and then not worrying about it - are the rules of thumb.
Source: https://www.greenbuildingadvisor.com/blogs/dept/building-science/lstiburek-s-rules-venting-roofs
It seems my choices for insulating the slopes are limited to whatever I can evenly apply directly over the back side sheetrock (faced fiberglass or spray foam) I'll have to live with thermal bridging until I reroof it seems.
Believe it or not - I do have pretty good access to that area from below, so spray foam application ex. R17 as I think Dana may be suggesting (with a min 1" gap for air) would be possible if the contractor has a wand that would reach the 4-5 feet into that cavity to be able to apply it correctly. I can also take the ridge out to get them overhead access if needed.
Dana, I actually have a contractor proposing to dense pack and the slopes with cellulose and just use gable vents to provide "cross flow" ventilation in the kneewall attics... but that just doesn't sit well with me. I realize that I'd be running less than optimal R value with either a faced bat or spray in solution.. but keep in mind.. right now I have nothing in there, so my assumption is that any insulation is better than what I have now...
I like the idea of using a paint based vapor barrier.. I had no idea that product existed.
So If I understand correctly.. it sounds like applying spray foam directly above the sheetrock with at least a 1" overhead air space really sounds like the best (though I understand not perfectly ideal) option for my situation...
Pardon my ignorance on the subject Dana but the 1/2 lb pour you're referring to is open cell correct?
And thanks again for all of the figures and suggestions, I realize my constraints don't make it easy.
"So If I understand correctly.. it sounds like applying spray foam directly above the sheetrock with at least a 1" overhead air space really sounds like the best (though I understand not perfectly ideal) option for my situation."
I'm not sure how you could possibly make it a vented assembly with ANY type of spray foam without pulling down the ceilings ( or ripping up the roof deck.)
Half-pound pours are indeed open cell foam, but in a slow-rise formulation that can be injected via a small hole rather than sprayed. Like the sprayed versions it has a very high expansion ratio, but since it takes several minutes (as opposed ot a couple of seconds) to fully expand it flows and fills the available space. Since there is open space for it to expand up into the mini-attic above, the risk of blow-out is extremely low. When used for filling stud bays (which have top & bottom plates, it's a closed box) it's possible to over-pressurize and pushing out the walls if you squirt in too much. It's a more expensive way to go than cellulose, but it makes a fairly tight air seal.
If you REALLY insist on a vented assembly it's time to bite the bullet and gut the slope ceilings and do it right. Half-measures and hacks have risks. With closed cell foam you could use even half-inch EPS as the backstop for the vent on which you'd be able to spray about 2-2.5" of foam. With closed cell you'd not be able to make it perfectly flush with the stud edges, since the material is too hard to trim flush if you overfill (unlike open cell foam, which would be trimmable.) But if you open it up and sprayed the roof deck with 2" of closed cell you could then put R15 rock wool or sprayed cellulose in the remaining 3.5" you'd have about R25-27 in there. The 2" closed cell foam itself would be a 0.6 perm vapor retarder on it's own, which is perfect for protecting the roof deck, and at about 50/50 the foam/fiber ratio would be high enough to completely mitigate condensation issues without use of interior side vapor retarders of any type.
In fact, 2" of closed cell foam on the roof deck is sufficient protection for even R49:
http://www.buildingscience.com/documents/bareports/ba-1001-moisture-safe-unvented-wood-roof-systems