PWF insulation with double wall – where to put the vapour barrier?

I have a log house that sits on a permanent wood foundation of 2×6 on 12″ centers with R12 fiberglass insulation and interior vapor barrier. I’m in zone 7 or Canadian zone 2. To complicate things further I’m off grid with just solar. For heat we use wood and I’ve just installed a propane furnace to a) move air and b) heat the basement. There’s also a pellet stove in the basement, but expensive and energy intensive. We haven’t fully experimented with the furnace for heating the basement, but should do ok as want to put two bedrooms down there. Without any heat it would get down to 1 or 2 degrees C or 34F this last winter which wasn’t a very cold one, looks like pretty much over now as not a day below zero in the forecast.
So, won’t get into it but the previous owner messed up backfilling as he didn’t have a floor in and broke the footing at the corners and pushed in the walls about 6 inches in the center. I put a 2×4 PT floor in and dug up and redid the weeping tile, exterior poly and grading. Straightened one end wall by pushing it back out and put a secondary wall under the joists support walls. The walls were substantially out of line, but I feel confident now with the integrity of the building. The secondary 2×6 wall now leaves the opportunity to stuff in more insulation. Also at the top I have a space between the secondary wall and foundation to put in a batt. Here would be the current setup –> poly, plywood, R12 in foundation studs, vapor barrier, R20 in space between walls in top 4 feet, R20 in secondary wall, then drywall.
I wanted to put that extra R20 between the two walls in as well so that there would be extra insulation on the above ground portion of the foundation. I pictured that the footing and ground around the basement might freeze deeper since the cold air would sink and with the extra insulation in the secondary wall there would not be enough heat to keep the footing above freezing temps. This insulation though then sits against the VB where the previous plan just had it as a dead air gap.
I haven’t put in this setup except in about 8 feet of wall in hopes of getting some colder temps and experimenting with condensation (note I checked the rim joist area as no VB and there was no condensation even though that was there all winter) . The winter is done for that now and in the couple cold days I had since I got that section installed it was fine. Problem is I’m not sure how’d it do when all done and through a long winter of -30C, -20F at night. The extra insulation is definitely needed to minimize the use of the furnace and electricity from my battery bank and seems like being able to do this would be a huge bonus as there is really no other way to heat this space.
Now here’s the question, what should I do about the interior VB? Currently it’s taped and acoustical sealed to the top plate of the foundation wall. My thought is to leave it there and put the insulation in. The two interior batts of R20 would be able to then dry to the inside and any moisture in the outer sandwiched portion could dry through the exterior plywood that is about 2 1/2 feet above ground. I have also toyed with the idea of poking a bunch of holes in the VB to at least give it some permeability . Also considered scraping the VB all together. The issue I worry about is then having to run a dehumidifier in the summer which is seriously power hungry and not a good match for being off-grid. I’m thinking in a way that leaving the VB and R12 insulation in the exterior portion is equivalent to the new idea for putting 2″ of rigid foamboard on a concrete foundation and then framing in a R12 wall. Also I figured that with the drywall air sealing further that the chance of much condensation happening are slim as not much air flow especially after i reseal the exterior plywood joints this summer. Though it worries me that condensation could happen and then drip down the wall onto the floor to sit on top of the poly that lines the basement floor.
I attached a picture for details. Note I have foam board in half the basement in the bottom half of the exterior wall but only R5 as there was no insulation there and I had scraps leftover from use as an air barrier behind the tongue and groove ceiling in the upstairs.
Need some ideas here with the VB as stuck on this step and need to finish it properly as spring is about to hit and exterior projects take precedence. Thanks in advance!
GBA Detail Library
A collection of one thousand construction details organized by climate and house part
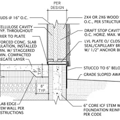
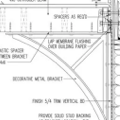
Replies
Derek,
There are a lot of issues here. In general, I'm not a fan of interior polyethylene, except on above-grade walls in very cold climates (the Prairie provinces, northern Ontario and northern Quebec, the Yukon, and interior Alaska).
Below grade? You don't want polyethylene on your walls.
The best way to insulate a wood foundation is on the exterior (with rigid foam or mineral wool). But I bet you don't want to hear that.
Derek,
Another series of questions swirl around your plan to operate a furnace in a Canadian off-grid home. In December and January, these appliances will quickly lower the voltage of your batteries -- so I imagine that you will be running your generator for more hours than you like.
Ok, so there's one side left to dig up this spring. I could put rigid on the outside of that portion, but the rest I'm not digging up again. That leaves me to slash the VB on the inside and stuff full of fiberglass (I already have it). I did surround the house with two feet of salvaged EPS that was about two inches that I laid flat figured it'd be some R value to stop the frost going down by the house.
I'm thinking that for the above grade portion I could put on some EPS and then cover with vinyl siding style board and batten though my partner would like rock veneer.
What will slashing the VB do for humidity levels in the basement? It'll allow the fiberglass to dry to the inside if wet, any other advantages of slashing it? Other than humidity, disadvantages?
In regards to the furnace it is more for the ecm fan that I installed it. I put air return vents close to the cathedral ceiling in the loft to bring that air down to the basement. Even if need to use the furnace from almost zero I can heat the basement to a pleasant temperature in about half an hour. Might lead to a bit more generator use, but I think it'll work. Only other option is a boiler unit, but figured since the ducting was already there would try the furnace first.
Regards to climate zone I'm North of Thunder Bay in Northern Ontario. Had condensation issues this fall with insulation in the gable area before I got VB on it. Pulled it back to find lots of condensation and mold growth since was freeze, thawing at that time.